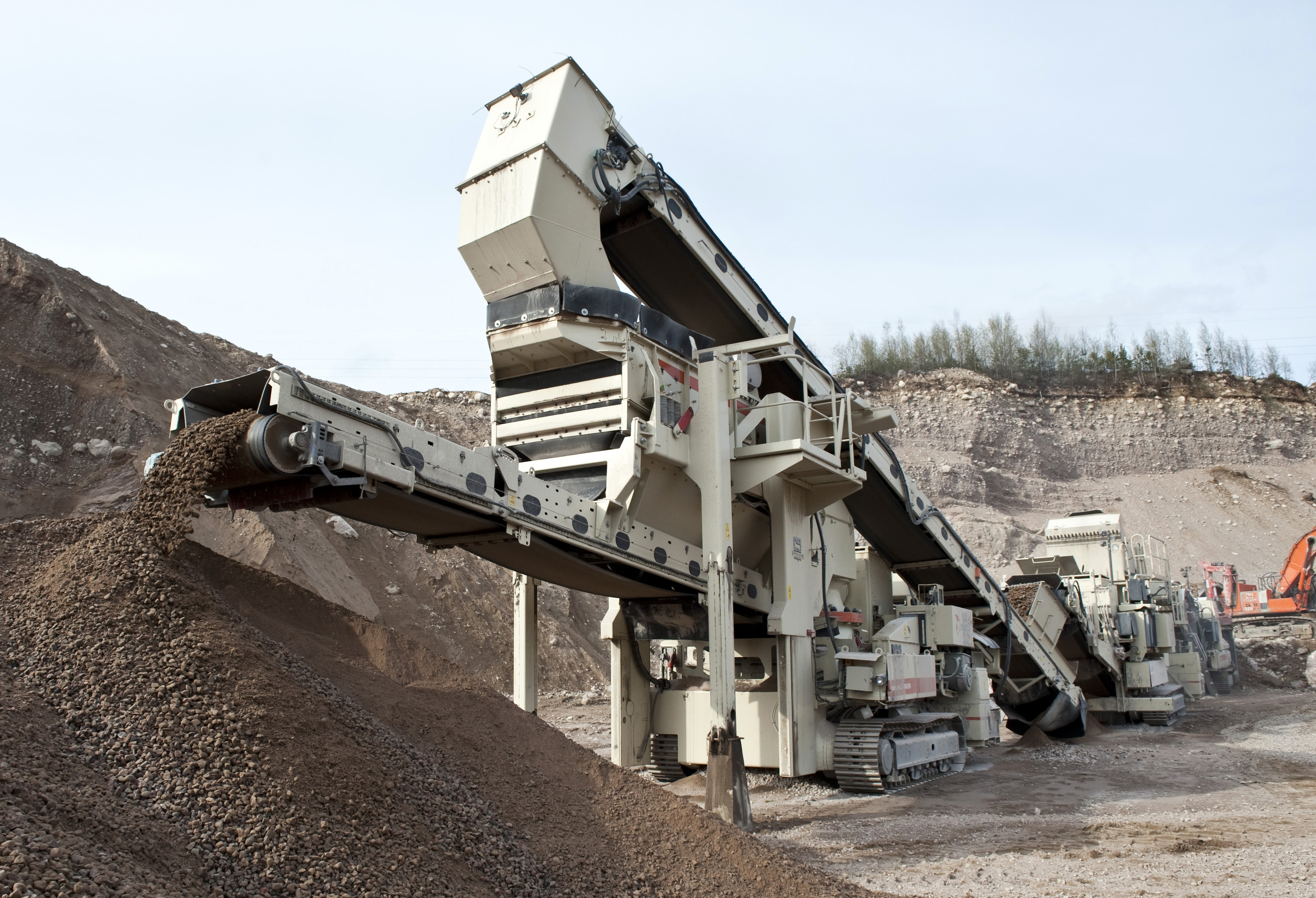
Optimisation software has the potential to significantly improve crushing and screening productivity. Claire Symes reports
With many capital expenditure plans limited or on hold, quarry operators are increasingly looking for alternative approaches to get the most from their existing fleets. When it comes to crushing and screening equipment, the method of choice for enhancing productivity appears to be use of optimisation software.
"Over the years we have seen an increase in demand for optimisation," said
Sandvik was one of the early promoters of computer simulation for plant optimisation when it started to offer the service in the 1970s. According to Svensson, much of the focus then was on capacity. "While this is still important, the focus has changed to production cost and quality he said."
Investment
"We have seen more and more companies investing in
Bedrock's crushing and screening optimisation program is now used in 65 countries so the company is well placed to see the trends.
"Dealers are also investing in AggFlow to help with proposals so that they are talking in the 'same language' as their customers and the manufacturers. This is particularly true on the mobile side of the business," said Teller. "It helps them to remove errors during the specification process and the manufacturer can be sure of delivering what the customer expects and wants."
Metso Minerals has also just released a new version of its optimisation software. "Bruno is a crushing and screening simulation tool that was first released, in its current format, in 1996," said Metso Minerals development engineer Saku Pursio. "The system was developed to help customers to save money. It is expensive to try and finetune in real life but sitting at a desk it is possible to optimise the setup both quickly and cheaply." Version 3.3 of Bruno was released this year and is based around the cost per tonnes for 1000hours of operation. According to Pursio, it is ideal for planning new plant, whether a fixed or mobile system.
"The system concentrates on operating costs - power draw, maintenance, parts," he said. "Some Finnish companies have taken Bruno as the official tool for design and these engineers have certain equipment that they have to work with.
Recent optimisation of mobile plant for a Finnish customer helped to deliver 20% more production just by adjusting settings." In new quarries, operators are using software to optimise the operation to achieve targets and then benchmark the operation and track production.
"In existing quarries, the operators are taking real field data to show what is achievable in optimum conditions and they can also input real plant measurements to help resolve where problems might be occurring," said Bedrock president Bryan Lewis.
"Sometimes the rock is harder or the blast material too large which prevents the 'on paper' figures being achieved but sometimes it is bottlenecks or the equipment not being operated correctly.
"In a situation where the rock in to rock out is achieving 800tonnes per hour but theoretically 1000tonnes per hour should be possible, the operator needs to understand the cause. One site where this process was carried out, checks of the equipment showed that the cone crusher had a cracked adjusting ring.
"The optimisation allows for targeted investment." Lewis added that the program can also help operators to look at the impact of wear on the machine on the processes and look at different scenarios of swapping equipment and conveyors around.Productivity focus
According to Sandvik, productivity should be the pivotal factor in any decision regarding the purchase of a crusher. "This productivity is measured in terms of tonnes of end-product material produced," said the company. "Many get sidetracked by secondary issues, such as hours worked, manganese content or tonnes through the crusher, and there is no denying that these are all important features.
"However, they only play a part in a bigger process, since it is the end-product produced that defines the actual return on investment for capital employed in the purchase of equipment, parts and services. Without this, no revenues can be generated."
Sandvik has said that its experience of the industry - which spans more than 100 years - has shown that wear parts of inadequate quality are often associated with such discrepancies as incorrect profile shapes, dimensions and ovality, all of which have rather expensive implications. These include diminished capacity and reduction, incorrect product graduation, increased circulating load and damage to bearings, bushings and other components. Svensson also believes that optimisation is important to quarries looking to improve production. "A typical example of the results possible is shown in a basalt quarry where we carried out the process in Germany," he said. "The product quality in the asphalt fractions did not meet the tight specifications, but at the same time there was too little of the 11/16 fraction as well as the need to avoid excess dust and sand production.
"The obvious solution would have been to put in an extra crushing stage, however, this is a costly exercise so we made an attempt to fine-tune the existing plant. By intensive simulations we found that with low cost changes to the existing equipment, that it was possible to meet the demands.
Together with the customer, we implemented the changes and also trained the personnel to operate the equipment in a new way. The end result was good - the quality demands were met and it increased production of the very much needed 11/16 product."
Reviewing operations
Teller believes that before the global recession quarry operators were working flat out and not looking at their production so closely, now they are working more intelligently. "This trend is likely to continue," he said. "Bedrock is working with a number of universities so that the next generation of engineers has a clear understanding of the benefits of optimisation. With computerisation, people are more familiar with the Internet and PCs so there is a new generation engineers who are more savvy."
In the meantime, current research and development means that further innovations in optimisation software will soon be available and add more functionality.
"The next generation of optimisation software will allow quarry operators to link the sales price of the material, so operators can look at the implications of producing a specialist material for one customer on the rest of the production," said Lewis. "This is one to two years away."