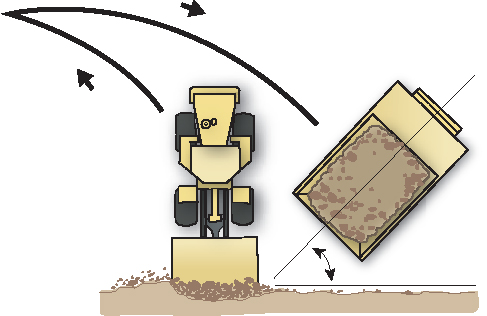
Rapidly rising fuel prices across Europe over the last decade look set to continue, driving increased demand for new fuel efficient equipment. Claire Symes takes a look at Caterpillar's latest development
It is estimated that around 40% of hauling costs within a quarry come from the cost of fuelling equipment to carry out the work. Without investment in more fuel efficient equipment, this cost is set to rise in the long term as fuel costs in Europe continue to soar.
Most equipment manufacturers have reduced fuel consumption over the last few years by adding new Stage IIIA compliant engines to their machines. But
Initial testing suggested that the system offers fuel savings of at least 15%, which could represent savings of around €20,000 a year compared to a standard machine.
According to Cat, both its quarry and general construction customers want to lower owning and operating costs but they also want flexibility in choosing how this is delivered.
"Rising fuel prices are a major concern, especially for European operators of big machines that can burn between 40 and 100 litres per hour," said Caterpillar large wheeled loader product specialist Bertrand Graeppi-Dulac. "We developed the system to meet demand from customers to help them maintain their operating margins.
"We started with working on a system for the 988H because this size of machine is mostly used for V-type loading of trucks in a quarry and can spend up to 40% of its operating time idling, which can burn more fuel than necessary." The software-based solution has three modes - full power, balanced power or max fuel savings - which can be selected by the operator from an in-cab switch.
Full power mode is the same as the machine's previous configuration, where the wheeled loader operates at 2120rpm. According to Graeppi-Dulac, this setting is best used when the operator's main focus is production, rather than fuel savings.
In balanced power, the machine still operates at 2120rpm during digging operations, but in between pump flow is lowered and the engine power is automatically reduced to 1800rpm. Like balanced power mode, the max fuel savings option still maintains 2120rpm of power and full pump flow for digging, but reduces power to 1700rpm outside of the digging cycle.
According to Cat, the system allows fuel saving to be made throughout the cycle by automating the power application depending on demand.
"When the machine drives forward at around 2mph and the arm is lowered ready to drive into the stock pile or working face, the software automatically senses that the machine is about to enter a loading cycle and switches to 2120rpm if in either of the fuel saving modes," said Graeppi-Dulac. "But once the arm is lifted, the software switches back to the previous mode because the additional power is not needed for the loading cycle." Cat's own testing of the system suggested that fuel savings of at least 15% were possible but field testing showed that even greater savings could be made. Field tested of the system was carried out in a limestone quarry in Madgeburg, Germany, where the 988H wheeled loader was used mainly for truck loading.
In full power mode, the 988H used on average 68.1litres/hour of fuel. But when balanced power was selected the fuel consumption dropped to 53litres/hour, a reduction of 22%. In max fuel saving mode it was 33% more fuel efficient than in a standard machine with a consumption rate of 45.4litres/hour.
"Using the system does not impact on the amount of material moved in each cycle but may add around three seconds to the cycle time, which is unlikely to have a significant impact on the overall production rate," said Graeppi-Dulac.
The new fuel management system is now standard equipment on all new 988H wheeled loaders and a retro fit kit is also available for machines manufactured before June 2007.
"Demand for the retro fit kit has been high," said Graeppi-Dulac. "It takes about a day to fit and, for most operators, the system will pay for itself in reduced fuel costs in as little as 15 days."