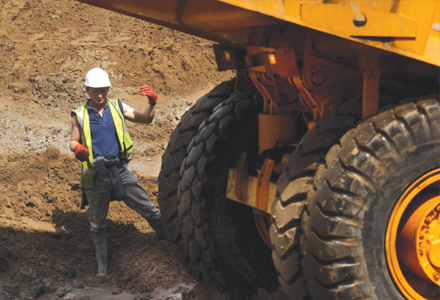
Reducing human interaction with machinery through greater automation is helping to deliver improved safety for quarry operators
Long gone are the days of breaking, loading and hauling rock by hand in quarries and as a result the safety of quarry workers has improved significantly. In recent years the safety has improved exponentially as greater automation has further distanced workers from the machines.
Over the last decade safety in quarries has been steadily improved and many have cited the implementation of initiatives and improved reporting for the gains. But how much have advances in machine design played in the improvement?
The main causes of accidents in quarries are commonly identified as being caused by slips, trips or falls; transport; or manual handling or musculoskeletal injuries.
While safety initiatives have helped reduce the risk of slips, trips and falls and improved quarry design and signage have reduce the accidents involving transport, automation of some operations has had a big impact on minimising manual handling or musculoskeletal injuries. This is because many of these injuries occur when operators need to interact with machinery, mostly for maintenance but also during daily operations.
Productivity benefits Many automation projects are driven partly by the potential to improve productivity and efficiency but also deliver clear safety benefits.
Quarries increasingly now have a central control room for the control of static crushing, screening and blending operations as well as for concrete and asphalt mixing. This allows operators to remain in a controlled environment but have a clear view of the whole plant with easy access to information on any problems. Once an issue has been identified, it is usually very easy to isolate the part of the plant where the breakdown has occurred to allow inspection without potential for machinery to restarted inadvertently.
On mobile crushing and screening equipment, many quarries now use remote controls operation and units can also be linked so if there is a problem with one, the others in the series also shut down.
Automation on construction equipment is also improving health and safety of operators with simple functions like auto-dig reducing fatigue on repetitive operations. Equipment often features cut-out systems if a maintenance panel is removed to prevent injuries, while others prevent booms are arms from being lifted or moved on steeply sloping ground or if overloaded to reduce risk of overturning.
Some quarries are opting for conveyor systems to reduce the interaction of man with machine. Here also, automation of conveyor systems is reducing accident risk with automatic shut down when there is a failure and simplified systems for component replacement.
Modern management systems are allowing all of these automation advances to be brought together and integrated into one facility. This is allowing greater communication between different operations in the quarry and improvement management as a result.
While automation has helped to minimise the interaction of operator with machines, it is unlikely that quarries will see the complete automation now being trialled in some underground mining operations. According to one mining automation specialist, quarry sites are considered to have too many variable factors and too wider an environment for the technology to be directly transferrable.
Nonetheless, it is likely that further advances in technology and wireless communication will bring news steps in automation leading to additional safety benefits.