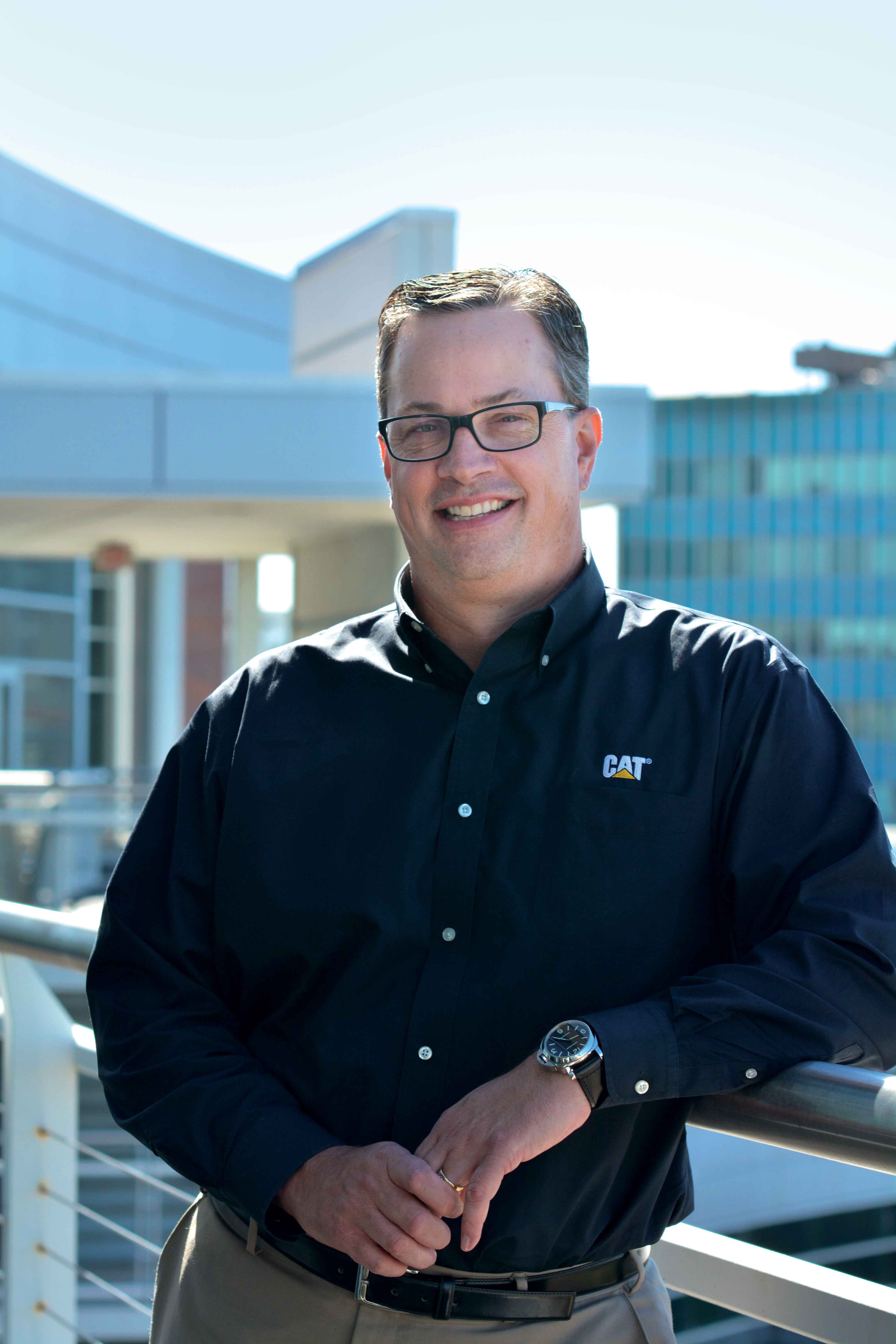
Caterpillar is a forward-looking company and is investing heavily in future technologies that will benefit its customers - Mike Woof & Guy Woodford were among leading construction and quarrying magazine editors who spoke to senior figures implementing the US industry giant’s tech vision.
At an exclusive roundtable event at bauma 2016 in Munich, Germany, senior executives from
At a further exclusive roundtable discussion with journalists, George Taylor, VP Marketing & Digital Division, Tom Pellette, Caterpillar Group President, and Karl Weiss gave an insight into how Caterpillar is keen to work with innovative tech companies and deliver exciting new possibilities such as the 3D printing of spare machine parts, and the use of augmented reality for machine repairs and engineer training.
Fuel efficiency and powertrain alternatives are crucial for the future of construction, while the issue of emissions will remain a priority for some time to come. Caterpillar has invested a great deal in research and development to reduce emissions and also develop alternative powertrains, issues that figured prominently in the discussions. Weiss said, “We have an electric drive dozer but it is propelled by diesel. We don’t have at this point a full electric drive machine. I think for underground equipment that is the future but we don’t have the battery power we’d need as yet. We continue to push the envelope but it’s not there yet.”
Fellin said that when Tier 4 was discussed, engineers said it would increase fuel consumption but in fact, the latest engines deliver fuel savings. He added, “We’ve taken a step now and we’ll take major steps in the future.”
Hybrid technologies provide a path for the future and Weiss said, “We will add more models to our XE line. Going forward we’re looking at electric and hydraulic hybrid technology as well as CVT drives. You will see for some machines electric or hydraulic solutions.” He explained that there will be different solutions for different product categories and that with regard to excavators, “…we strongly feel the hydraulic hybrid is a more cost-effective way to do it.”
Fuel consumption is a major cost factor for customers, accounting for some 30% of the running cost of a machine. Fellin added, “At the end of the day, everyone wants to know how much fuel they’re saving. That’s what counts.” He added that the data produced by the latest machines is also of benefit as firms can track operation and use very closely. “The VisionLink allows us to do that. Customers can take information from any machine in the fleet. The connectivity of the machines on the jobsite is a key.”
Weiss added, “What’s happening now is that our customers are coming to us and saying, ‘How do you help us make more money?’ It’s not just about saving money.”
Reducing engine emissions has been a massive focus for Caterpillar as well as its many rivals. The recent scandal surrounding VW and exhaust emissions reinforced the importance of this area for Caterpillar. Weiss said, “We have used what happened within VW as a strong internal message.” He explained that because VW is a strong brand and a strong company, it was a wake-up call to review internal processes and ensure that Caterpillar would not make the same mistake, “That was the message from the top down at Caterpillar.” He continued, “What’s different from on-highway is that you don’t bring your wheeled loader to a testing station and run the machine.
You have safeguards within the supply chain and there is spot testing. We have a close relationship with the EPA and it audits us on a regular basis.” He added that the firm audits itself internally as well as being covered by the EPA and said, “We do it very openly.”
Machine autonomy is an important future technology and an area where Caterpillar has been a leading player for some time. The firm’s autonomous mining machines are becoming established, with a potential for this technology in quarrying and construction in the future. Weiss said, “You could have an autonomous worksite but you need the building blocks to get there.”
Kelliher said, “It took us about five years to go from the launch to full commercialisation. I predict that in five years we could take autonomous machines from the large mining environment down to quarries.” And he added that the firm has active autonomous machine technologies, not just for mine haul trucks or underground loaders, but also for large dozers and blasthole drills, while truck loading with large rope shovels could also be automated in the future.
Weiss said, “On a typical construction site, it’s not as predictable as a mine site. If it’s a large construction site we see more near-term possibility of having autonomous machines.” But he explained that tasks involving more human interaction such as highway widening jobs are more complex and are less suited. “The complexity of a construction site is that you have several phases. If you’re moving material from here to there the dozer could work all day long without an operator. You could have multiple dozers and soil compactors.”
The proliferation of gaming systems has also been a driver in developing new control systems for machines. Hoefling said that because the younger, less experienced operators are more familiar with modern technology, they even have more experienced operators asking them how to use these new systems. The development process is involved and Weiss said, “We’ll show a product multiple times to a customer to get real time customer input in new technology.”
During the other exclusive Caterpillar roundtable discussion with journalists at bauma 2016, and in response to a question touching on research suggesting that 3D printing of houses may be possible in “one or two years”, George Taylor, Caterpillar VP Marketing & Digital Division, said: “We have seen some technology that 3D prints [house] foundations and have had dialogue with those behind it.
We also have a number of arrangements that are looking at how to really leverage 3D printing. Today, metallics are a big driver of that, with our product line durability. We believe that 3D printing may not move as fast as we’d like it to, but it will be faster than we think. We have a lot of experimentation on this and are looking at it for our aftermarket business. It’s not hard to imagine that one day we would chip a part file to either a customer or dealer, and have that part printed for applications. We have today around 45 production 3D parts that we print.”
At Caterpillar’s bauma 2016 press conference, the company’s Chairman and CEO Doug Oberhelman said how the construction and quarrying equipment sector giant is currently investing US$2 billion a year on digital technology R&D.
Some of this investment is going into how Caterpillar can make best use of virtual and augmented reality technology in the construction and quarrying equipment sectors. Speaking on this subject, George Taylor said, “Augmented reality offers a lot more powerful applications. Having a technician with a pair of [augmented reality] glasses on that help them to more productively repair our machines is a great example of how it could work.
Another example is being able to overlay on a machine gauges that aren’t really on the machine. There’s a variety of different applications we are exploring in that area. “We are also doing some work in marketing and sales, doing walk rounds of a machine virtually with augmented reality technology. This enables you to see inside the machines. It helps you bring the machine to reality for a customer.”
Taylor said Caterpillar had also developed a new technology to support service technicians in the field. “It allows them to put a reader, for example, on top of the engine and a technician back at the main store can instruct them on what to do, and the technician in the field can see this on an iPad.”
Karl Weiss, Caterpillar VP Earthmoving Division, said, “I think there is enormous scope for a large construction contractor to have a full GPS 3D system set up. This could eliminate a lot of waste on a job site. I think this would have the biggest immediate impact, but we know that’s a big step for a lot of our customers. We’re trying to give them smaller steps [such as Cat GRADE with Assist for excavators, and Cat Slope Assist for dozers] to get there.”
Asked about how Caterpillar viewed their competition in the race for new technology to improve customers’ machine productivity and efficiency, Weiss said, “It’s amazing how good our competitors are.
How quick and well they can do things. However, I think our total approach to giving customers the very best alternatives for saving them money, all the way down to the building blocks to get them there, is unique. There are also emerging competitors, from the sensor manufacturers to the start-up who may be able to build a foundation of a building through 3D printing.”