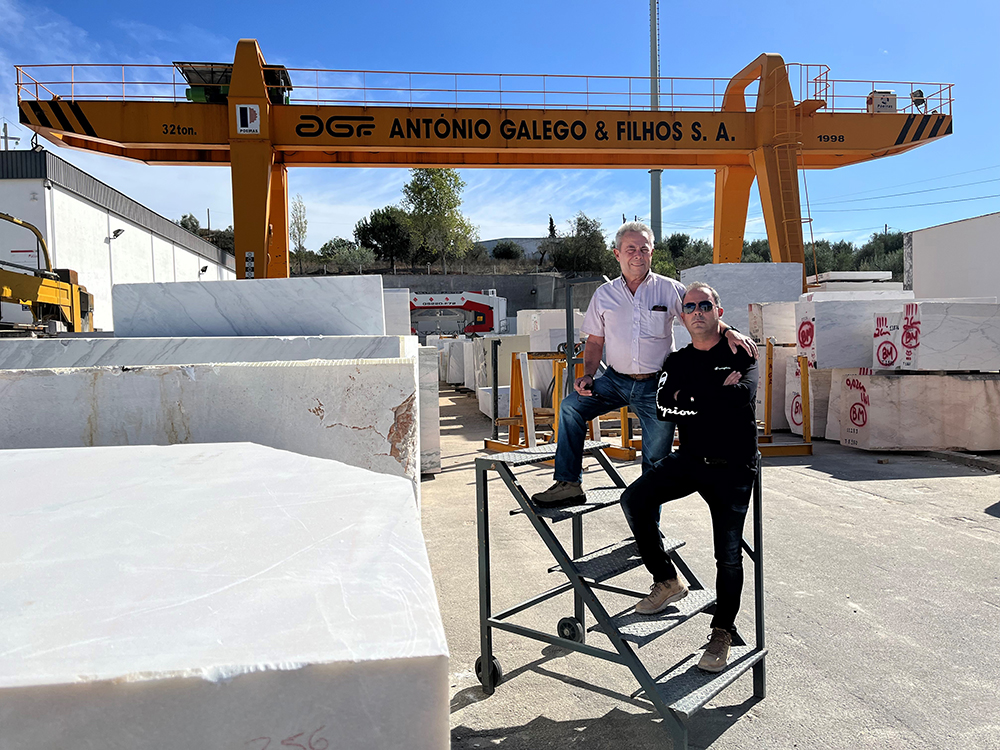
A next-generation Cat 980BH (Block Handler) is the new star of the show at one of António Galego & Filhos Mármores’s (AGF) two Portuguese Estremoz marble quarries, just two kilometres from each other in Bencatel, around 14km south-west of Vila Viçosa in southern Portugal.
The state-of-the-art machine removes unwanted waste material in combination with two Cat 730C articulated dump trucks (ADTs), spreads waste material for haul-road maintenance, and creates gravel material ‘beds’ to allow primary marble blocks to fall softly after being diamond-wire-saw cut and excavator-nudged away from the quarry face. The Cat 980BH also removes secondary marble blocks up and out of the quarry to the company’s processing plant, where further cutting and polishing work is done. Additionally, the versatile machine is used to lift raw marble blocks from the yard onto on-highway trucks for export to Indian and Chinese customers.
Fitted with a powerful Cat C13 313kW EU Stage V emissions standard engine, the 30-tonne class Cat 980BH can be fitted with a Performance Series bucket to offer improved material retention while reducing dig times. The robust next-generation 980BH is built for premium efficiency and productivity, with its easy-to-use technologies a standard offering.
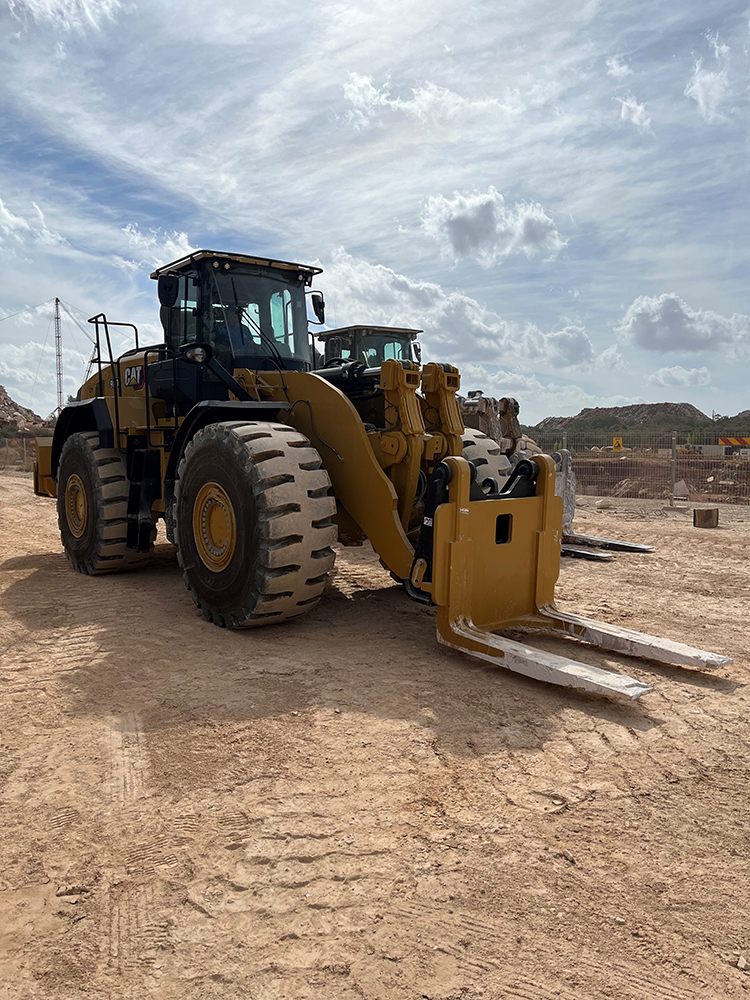
“We can move a 30-tonne marble block easily with the 980BH as it has got even greater lifting capacity than our 980MBH. Our operators tell me that the 980BH operates smoothly, with all four of its tyres always remaining on the ground,” says Marco Galego, co-general manager of AGF with António Galego, his father and co-founder of the third-generation family-owned business.
Since 1996, AGF has purchased 20 Caterpillar machines, with a Cat 980G wheeled loader and Cat 325B crawler excavator, the first two bought models. As well as the 980BH and 980MBH, AGF has a 980KBH in its current machine fleet.
“We are longtime Caterpillar customers,” continues Marco. “We traded in our Cat 980G in 2009 for the next-generation Cat wheeled loader after it had worked 18,000 hours on the same tyres. We trade all our wheeled loaders in after 18,000 hours, and they are always in great resale condition.
“Our Cat 345D [large hydraulic] crawler excavator, bought in 2009 along with a Cat 330D, was my favourite machine - the best Cat machine ever!” says Marco. “It never had a problem, was very powerful and worked really well.”
When asked to describe Cat machines in a word, António says: “Strong,” adding that the servicing of all AGF’s Cat machines has been very good, helped by a strong relationship he and Marco have built up with Caterpillar’s longstanding Portuguese dealer, STET.
Marco explains that he and his father have used Product Link and VisionLink since 2014 to better assess their Cat machine fleet’s performance, with the pair estimating it has halved the fleet’s running cost. They use the technology to identify points in the production cycle where they can reduce machine fuel consumption. They also proactively handle fleet maintenance by getting fault-code information sent directly to their smartphones. Fault-code monitoring is an essential part of machine- condition monitoring and repair, significantly increasing fleet uptime.
Marco and António stress that due to increasing energy and fuel prices, Cat Product Link and VisionLink have become even more invaluable to AGF. The father-and-son team is looking into expanding its data and fleet-monitoring capability by investing in a state-of-the-art Cat Productivity solution.
A €9mn-a-year-turnover business, AGF extracts around 150,000t of marble a year across its two Vila Viçosa quarry sites (Tex - where the Cat 980BH is deployed - and MSB), with 30,000t resulting in final product for sale, leaving an 80% waste ratio. Site operating hours are Monday-Friday 8am-5pm and Saturday 9am-1pm. Tex and MSB are running at capacity, with a further increase in production not feasible.
Marco and António decide which marble blocks are selected for final sale, with the process drawing on their vast industry experience. “No two marble blocks are the same. The way the veins move throughout the block, their brightness, and the background behind them. All this goes into setting the price for what is a unique product,” explains António.
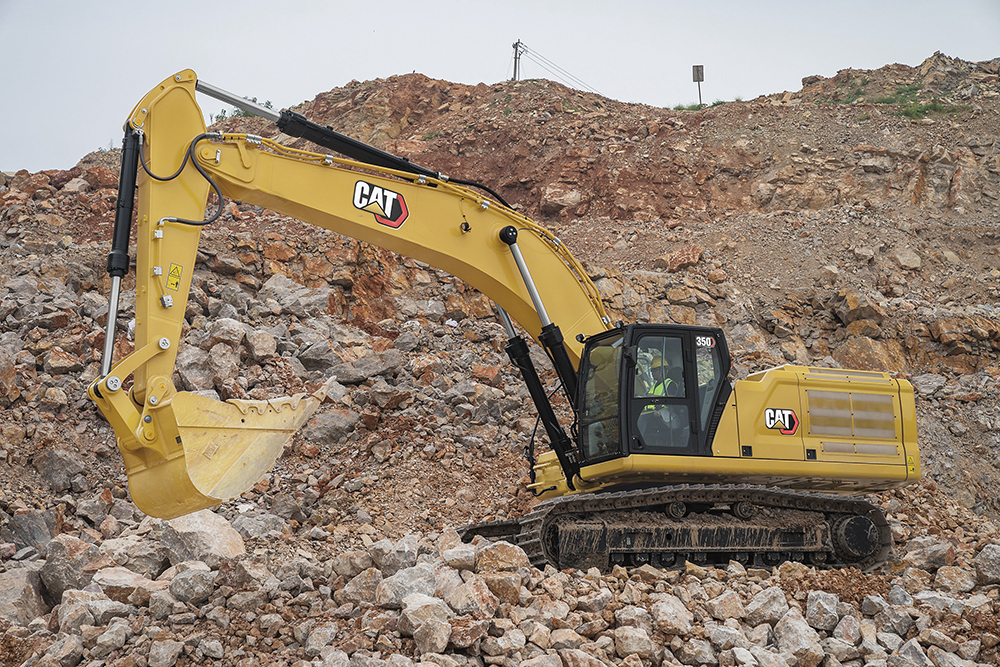
“We have a lot of repeat business and customer relationships going back a long time,” says Marco, who lists the United Arab Emirates, Saudi Arabia, India, the US, China and North Africa among key export markets for AGF’s premium marble products.
“Domestic customers are mainly wholesalers who sell to export customers. We are getting big orders connected to the Line-Neom project, a new city being built in [Tabuk Province, northwestern] Saudi Arabia. It will be five times bigger than New York,” stresses Marco in highlighting the US$5trn, 170km-long city megaproject. “India is another big market for us. Its population is growing fast, and even if just a small percentage of the larger population can afford to buy marble blocks, that’s a lot of people.”
While AGF’s trading remains strong, the number of marble quarry sites in the Portuguese Estremoz marble region has reduced from 120 sites down to around 25 following a market consolidation process which began in 2015. Some of the reduction in marble quarry firms is also linked to tightening health and safety regulations.
Despite a difficult global economic climate, Marco and António say the size of the world’s wealthy marble-block client market is growing, which, along with reduced regional competition, is good for AGF’s long-term future. Marco says that AGF has another 50 years of marble reserves to extract, with the business’s Cat’s 980BH and other Cat loading and hauling machines sure to play a key part in the company’s continued success.
Doosan Infracore, which became Develon on 18th January 2023, has invested significantly in its quarrying-suited medium and heavy excavator and wheeled loader model research and development in recent years. Speaking to Aggregates Business at the bauma exhibition in Munich (24-30 October 2022), Chris Jeong, CEO of formerly Doosan Infracore’s European subsidiary, said: “The last three years have seen us improve our market position across the heavy equipment lines, including medium-to-large excavators where we are now at a 9% market share. We think we can grow further in this area.”
Visitors to bauma 2022 saw the latest developments in Doosan Infracore’s XiteCloud system as the company further expands its business portfolio into the field of construction-site management to complement its existing operations in manufacturing and sales of construction equipment.
“Our quarrying and construction customers are very keen on XiteCloud and the big fleet management capability it gives them, and we are keen to give them the best machines to support it.”
Asked how he sees European construction and quarrying equipment customers' expectations differing from what he saw in his extensive experience working in emerging markets, Jeong replied: "Customers in Europe are very diverse and very specific in their requirements. We always look to be well prepared when we launch new products so that we can meet what customers in Germany require, for example, and the differing requirements of, say, those in the UK and so on."
So how does Jeong see the construction and quarrying equipment in a decade’s time? "I read an article some time ago which said that the construction industry is one of the most conservative industries in the world, but the COVID-19 pandemic brought forward the desire for autonomous machines and technology. Also, to make the [construction or quarry] job site more efficient, connectivity will be key. No single job site has one branded equipment fleet, and customers want full visibility of their job site and its running costs. As not just a manufacturer but also a solution provider, this is something we are very keen on giving to our customers now and in the technology we are working on for the future."
Featuring powerful digging force and strong swing torque, the new fixed-gauge Cat 350 excavator can be equipped with large buckets up to 3.2m³ for claimed class-leading productivity. While productive, the 350 consumes up to 13% less fuel than the Cat 349 to lower costs, reduce CO2 emissions, and operate more sustainably. Three power mode options – Smart, Power, and Eco – match the excavator to the job to further reduce fuel consumption.
“Caterpillar is committed to reducing greenhouse gas emissions while helping our customers meet their climate-related objectives,” said Brian Abbott, Caterpillar’s global product manager for large hydraulic excavators. “The 350 is our latest example of delivering on that commitment.”
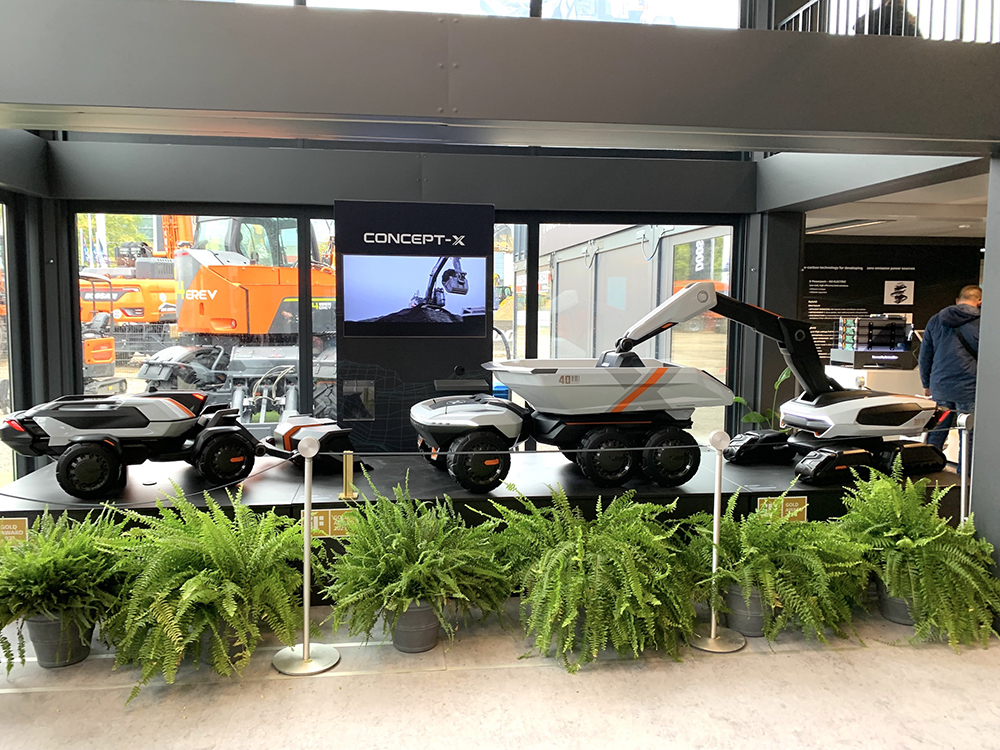
The new 350 excavator’s standard Cat 2D Grade system indicates depth and slope on the monitor with alerts to increase operating efficiency. Grade Assist helps the operator to effortlessly stay on grade with single-lever digging. For truck loading and trenching applications, Swing Assist automatically stops excavator swing at operator-defined set points to consume less fuel. Lift Assist helps to avoid machine tipping by letting the operator know the load is within safe-working-range limits. To safely work around obstructions, 2D E-Fence prevents the excavator from moving outside operator-defined set points.
Cat Payload onboard weighing gives real-time weight estimates to achieve precise load targets and improve efficiency. When combined with VisionLink, Payload offers remote managing of production targets. Alternatively, the monitor’s USB port allows fleet managers to download up to 30 days of work for progress management without an internet connection or VisionLink subscription.
Available in-cab technology upgrades include Cat Grade with Advanced 2D for creating and editing grade designs via a second high-resolution touchscreen monitor and Cat Grade with 3D to create and edit designs on that second monitor plus the ability to see the front linkage’s full range of motion. All Cat Grade systems are compatible with radios and base stations from top third-party technology suppliers.
The Cat C9.3B engine has more than 14 million hours of service to attest to its long-term reliability. Synchronized 1,000-hour oil- and fuel-filter service intervals reduce downtime. The hydraulic oil filter offers a 3,000-hour replacement interval – an increase of 50% over the previous design – and provides improved filtration performance.
The 350 can work up to 4,500m above sea level. It features a standard high-ambient temperature capability of 52˚C (126˚F), cold-start capability at -18˚C (0˚F) with optional cold-start capability at -32C (-25˚F). Automatic hydraulic warm-up in cold temperatures gets the machine to work faster and prolongs the life of machine components. A double-element air intake filter with pre-cleaner features high dust capacity, and the machine’s high-efficiency hydraulic fan offers an optional automatic reverse function to keep cores free from debris.
Product Link collects data automatically and gives fleet managers critical operating information like location, hours, fuel usage, idle time, maintenance alerts, diagnostic codes, and machine health online through web and mobile applications. Maximising machine uptime, remote troubleshoot and remote flash allow dealers to remotely connect with the machine to diagnose fault codes and update operating software. Operators can easily track filter life and maintenance intervals through the touchscreen monitor.