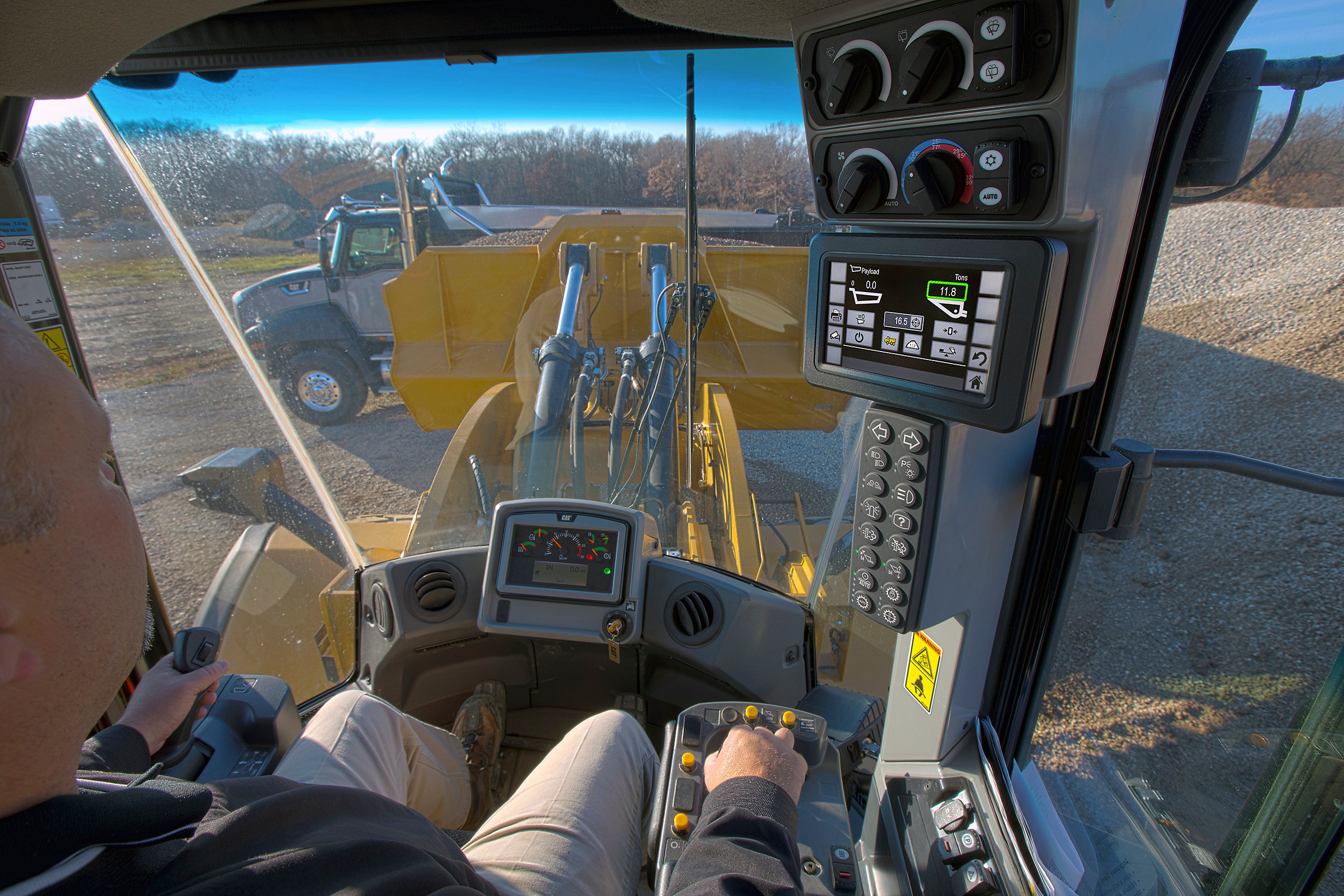
Loading, like hauling, has to be properly carried out as any hold-ups at this stage can be costly. And there is no shortage of equipment and tools to make sure that the task can be completed quickly and efficiently.
New wheeled loaders and excavators, including hybrid machines, have been showcased recently, while systems to help with load-out have also been introduced.
“This industry-first integrated on-the-go payload system for excavators weighs loads as the boom swings, with no interruption in the loading cycle.
Advanced weighing features enable the operator to make quick, time-saving load adjustments at final pass, before loading the truck,” says the company, which has introduced its new M Series compact wheeled loaders, 906M, 907M and 908M, featuring Caterpillar’s optimised Z-bar loader linkage, and which have electronically controlled hydrostatic drive systems that meets US EPA Tier 4 Final / EU Stage IIIB emissions standards.
Also new are the Cat 950M and 962M wheeled loaders, which use Cat C7.1 ACERT engines that meet Stage IV emissions standards, and which are said to feature more power than their K-Series predecessors and up to a 10% gain in fuel efficiency. They also have the Cat Production Measurement system.
“Payload data can be viewed at a glance through the in-cab display to assist operators with fast, efficient loading to exact specification, without under or overloading, maximising hauling potential and performance of the entire fleet.”
Data is stored to help managers calculate daily volumes, monitor production, and manage their business, and the Cat Production Measurement is fully integrated into the machine systems and display at the factory.
Indeed, Caterpillar says its M Series medium wheeled loaders have become more efficient by using Cat Production Measurement, which for further operator convenience, works with the machine’s automated loading feature, Aggregate Autodig, to reduce operator inputs and improve productivity during repetitive loading when working in aggregate stockpiles.
Meanwhile,
Trimble says the LR360 can reduce fuel and maintenance costs by avoiding unnecessary idling of loaders and trucks in load-out. It also provides quarries with increased truck visibility to ensure that its trucks are loaded to capacity in the shortest time possible.
“LR360 is first and foremost a tool to improve the accuracy and speed of load-out operations. But it can also reveal hidden improvement opportunities,” says Johan Smet, general manager of Trimble Loadrite. “LR360 enables users to drill into production data to see individual trucks, loaders or even bucket-by-bucket data to identify cost leakage.”
From
It has been designed and constructed at HCM’s wheeled loader factory at Ryugasaki in Japan, where it will initially be sold.
Hitachi says its design engineers have incorporated new TRIAS II technology into the Zaxis-6 range of excavators to meet EU Stage IV emissions regulations. Hydraulic loss is decreased by reducing the amount of hydraulic oil returned to the tank due to cooperative control of the pump and valve. Two solenoid valves have been added to control the pump flow effectively, lowering fuel consumption. An auto shutdown feature also prevents fuel wastage, as well as reducing noise levels, exhaust emissions and CO2.
Inside the cab, the technology within the multifunction LCD monitor enables operators to check the machine’s status and settings at a glance, and the new machine also has Hitachi’s remote monitoring Global e-Service.
Another significant change to the Zaxis-6 range is the implementation of a selective catalytic reduction (SCR) system. The engine output of the 30tonne class ZX300LC-6 has been increased to 186kW compared to 140kW for the ZX290LC-5.
With bucket capacities ranging from 4.5-5.7m³, the loaders are powered by the Scania DC13 six-cylinder engine producing 257kW and 283kW of power respectively at 1,800rpm, and claim up to a 10% reduction in fuel consumption. The engine meets Stage IV emissions regulations without the need of a diesel particulate filter (DPF).
With a net 159kW at 2,050rpm and operating weights between 29,850kg-30,950kg, the PC290LC/NLC-11 is said to “maintain the powerful performance of the previous Komatsu PC290 model.”
“This new excavator does so much more than simply meet EU Stage IV emissions regulations: it offers significant advances in fuel consumption, provides 3G communications, improves operator comfort and includes new safety features,” says Vince Porteous, product manager at Komatsu Europe International.
The 95kW WA200-7, which is driven by a Komatsu SAA4D107E-2 engine and which complies with EU Stage IIIB exhaust emission regulations, weighs approximately 11,800kg.
Komatsu says it will be bringing different sized hybrid excavators to the market in the next “one or two years” with the new models to follow on from last year’s successful launch of the third-generation HB215LC-2 excavator.
A new
The L180H features a 13litre Stage IV final engine, and the machine also has Volvo designed and manufactured driveline components including Optishift with torque converter lock-up and reverse by braking feature, designed to offer fuel savings each shift. Volvo says fuel savings are further enhanced by the Volvo Eco pedal encouraging the operator to run the machine at its optimum rpm in the engine’s torque curve.
The L180H has been equipped with a 5.6m³ straight lipped re-handling bucket; Volvo’s optional ride control and boom suspension system together with
The F Series features four solutions for quarrying, waste handling and contracting, and the models 621F, 721F, 921F and 1121F, with respective bucket payloads of 4.3tonnes, 5.4tonnes, 7.1tonnes and 9.1tonnes and maximum power of 128kW, 145kW, 190kW and 259kW, comply with EU Stage IV/Tier 4 Final with the Hi-eSCR technology developed by
Models up to 20tonnes feature the Proshift five-speed transmission that is said to enable the operator to take better advantage of the outstanding torque. “The lock-up results in fuel savings of up to 2litres per hour and faster cycles compared to conventional transmissions,” says Case Construction Equipment.
“Wheeled loader operators work long hours on a fast and powerful machine, so comfort is a key concern. Case teamed up with top range seat experts Grammer for the F Series’ new premium leather seat, which provides outstanding protection from repetitive shocks and vibrations.”
“This is the first machine to display our new LiuGong DNA. Over the coming months and years you will see machines with the same visual cues as the 856H.”
Powered by a