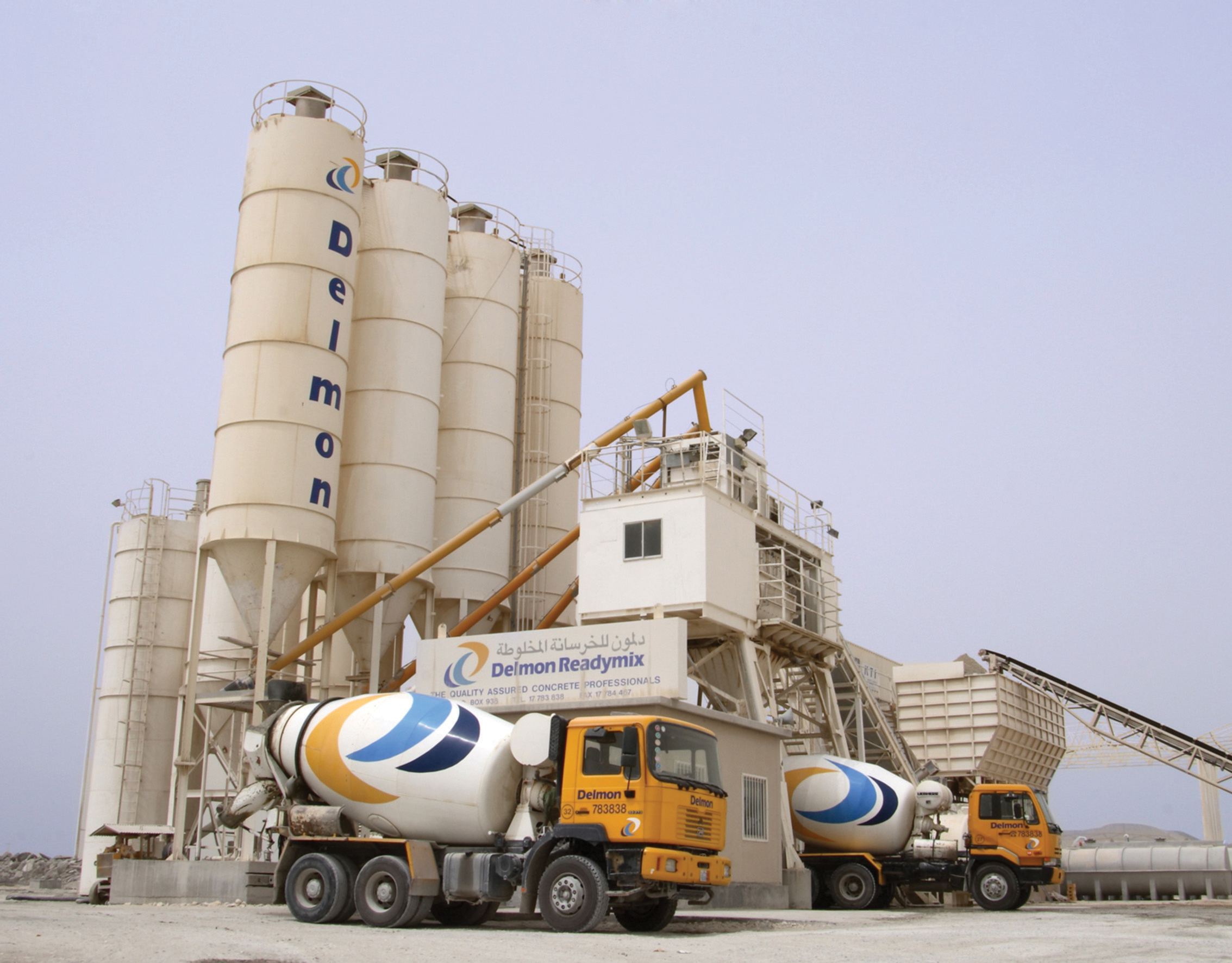
Delivery of high quality concrete depends on close control of the measuring and mixing process and recent work at Bahrain-based Delmon Readymix's plant demonstrates
Meeting the design parameters of ready mixed concrete both at the point of dispatch and delivery is essential but this important target is not always achieved. Bahrain-based
Delmon's plants experience variations in the aggregate moisture that are unique to its location and climate. While the moisture of their marine sand usually delivers free water into the load, on many occasions the limestone aggregate is dry enough to absorb free water out of the mix just to achieve its saturated surface dry (SSD) condition. This wide variation in moisture had necessitated the creation of several compensatory processes at the batch plants, the first of which was that the batch operator would manually adjust the water in the mix design before the load if the aggregates were thought to be dry, and secondly, the truck would make a required trip to the slump stand for final adjustment.
Command recommended the installation of its Precision Water System (PWS) and upgrading the spectrum batching system to its CommandBatch program to improve the quality and consistency of its ready mixed concrete products.
Delmon's new system is equipped with four Command Alkon moisture probes, providing moisture measurement for all aggregate up to 20mm. The first benefit of the PWS to be realised was the ease of calibration of the moisture probes. Delmon general manager Jon Mottram said, "The new system is very simple, all you have to do is hit the bake out button on the probe calibration screen, capture the material under the weigh bin, [have] the lab staff do a moisture test, then re-enter the figures into PWS at any time later and away you go. You need to repeat the bake outs to get the final calibration curve, but this builds up over time and gets better with the more calibrations done. It is very simple."
The plant at Delmon requires two or more batches to make the full truck load. "With PWS you get changes in the aggregate moisture immediately adjusting the final water addition to the batch," Mottram explained. "No waiting for adjustment to be done on the second batch. This capability ensures every part of the load is produced correctly.
"We now have more accurate slumps at the plant with +15mm achieved repeatedly, requiring less use of the slump station. The batcher no longer adds water manually to correct the slump. PWS allows the absorption of the aggregates to be taken into account when batching the concrete, so, when using very dry material which will absorb moisture, the system automatically adds water to the mix which gives the correct slump of the concrete and the correct yield. We are achieving a tighter envelope on slumps at the job; the customer gets better consistency between loads, we get happier customers with fewer complaints ensuring our company keeps an edge over the competition."
One unexpected benefit of it has been the ability to rely on it to alert the producer to other aspects of the material quality process. For example, Delmon has discovered that material issues (dust content, grading changes) are flagged up much earlier than in the past. If the grading of materials goes out of specification the water demand changes and the batcher has to trim the total water requirement. This problem is more easily spotted as an issue now and action can be taken much earlier.