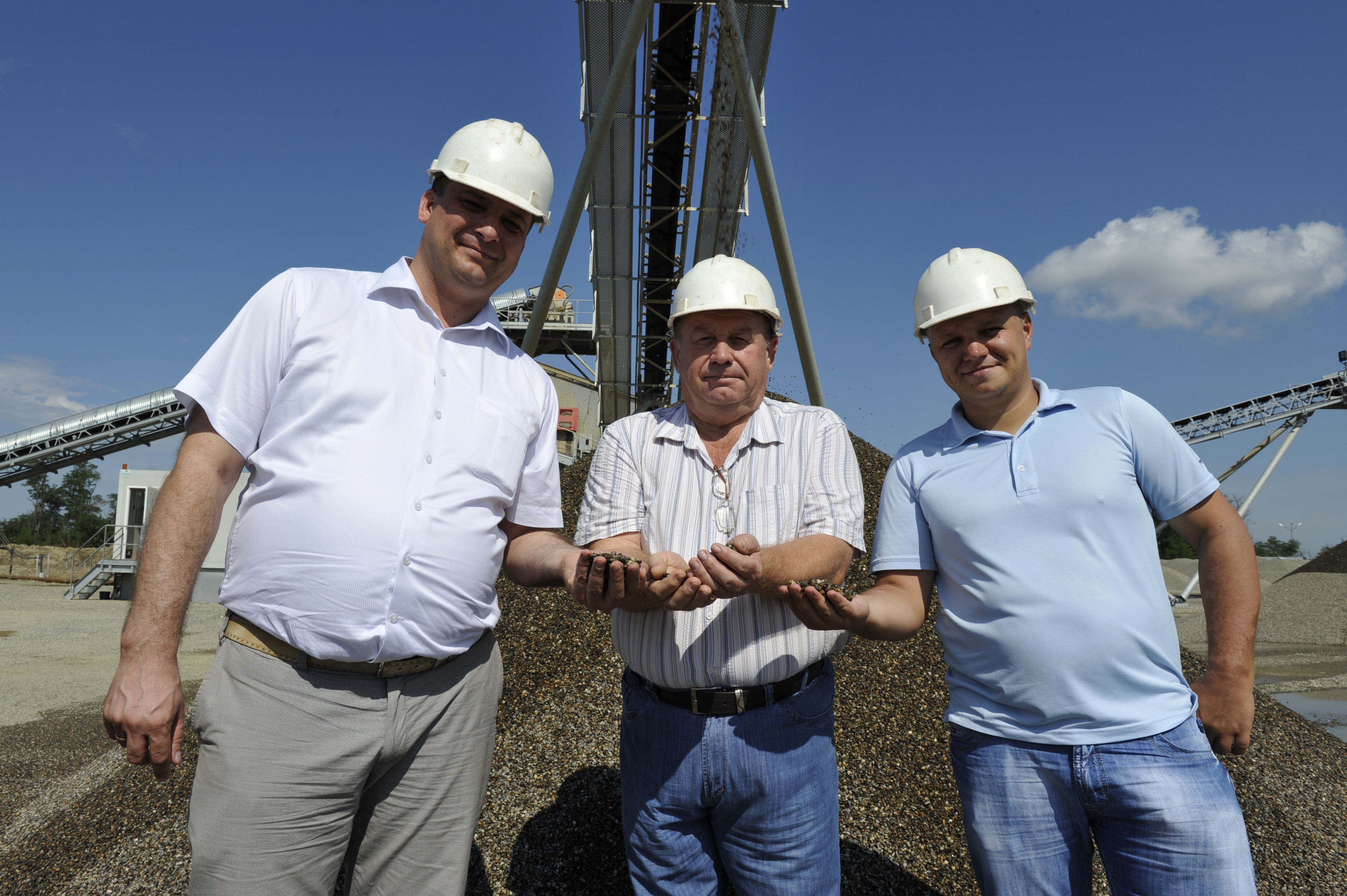
One Russian quarry is working flat out to supply sand and aggregates for infrastructure for the 2014 winter Olympics. Patrick Smith reports
The holiday resort of Sochi is Europe’s longest city and home to what is said to be the continent’s largest construction site.
Much of the year the Russian Black Sea destination has a sub-tropical climate, but temperatures can drop considerably particularly in the nearby mountains.
This mixture may well have been a factor in the decision that will see Sochi host the XXII Olympic Winter Games in February, 2014; the XI Paralympic Winter Games a few weeks later, and the Russian Formula 1 motor racing grand prix the same year.
An estimated €7 billion is being made available for the Olympic construction works in Sochi, which include the Olympic park and village; the Krasnaya Polyana ski resort about 45km away in the Caucasus Mountains, and a huge road and rail development to take participants from Adler (home to the station and airport) to the resort.
A number of impressive tunnels are being built to take the infrastructure, and more than 300,000m³ of concrete will be used for shotcreting and for solid cladding of these tunnels with
More than 155,000 workers are involved in the construction projects (40,000 in the Olympic park).
And because the Olympic site is classified as a 12-magnitude seismic zone, Olympstry (the state corporation) and Russian regulations require that only the highest quality washed aggregates are used in concrete for construction of vital infrastructure.
Almost 200km away in the city of Maykop, Republic of Adygea, southern Russia, this is music to the ears of the owners of the comparatively new Maykop Nerud Quarry, an almost dust-free operation nestling among picturesque lakes and fruit plantations.
Aggregates and sand from the quarry are transported to Sochi, which is 115km long, to be used on Olympic projects including a 2.5km tunnel complex for road and rail; the Bolshoi Ice Palace and for making prefabricated tunnel linings at the Severstroy plant, which will disappear on completion of its work early in 2012.
Maykop Nerud produces sand and crushed stone of various sizes using mobile crushing and screening plant and a stationary washing complex from
In the first quarter of 2012 more Metso stationary crushing and screening equipment will be commissioned at the quarry and this includes a Nordberg C80 jaw crusher; two Nordberg HP4 cone crushers; two Nordberg CVB2060-4 inclined screens, and Nordberg SF2360 and SF2870 sand traps, which will be added before the stationary washing plant. The contract was signed in June, 2011, and the new equipment will see production rise from 250tonnes/hour to 550tonnes/hour.
In the scorching summer heat when temperatures nudged 50°C, the lake was used by many of Maykop Nerud’s 80 employees to cool down as they swam over the sand-gravel mix that is said to feature properties of granite with excellent hardness (40kN), making it ideal for the production of high quality aggregates.
Retrieving the material is straightforward quarrying technology, with excavators (on this occasion a Volvo EC240BLC, one of a number on site) scooping the mix out of the lake and moving it to stockpiles. Two Volvo L120F wheeled loaders are used to move material around the quarry.
From stockpiles, where the 0-150mm stones are left for 24 hours, the sand-gravel mix is moved the short distance by trucks to a specially-constructed ramp where it is tipped into the three-stage crushing and screening process from Metso, which started operating in October 2010. The Metso washing plant started operations in February, 2011, and is the first of its kind in Russia.
Crushed to 0-20mm, the processed material is transported by conveyors to the washing complex consisting of a feed hopper, conveyors, a four-deck washing screen, a spiral classifier and an automated control system.
From stockpiles, where the 0-150mm stones are left for 24 hours, the sand-gravel mix is moved the short distance by trucks to a specially-constructed ramp where it is tipped into the three-stage crushing and screening process from Metso, which started operating in October 2010. The Metso washing plant started operations in February, 2011, and is the first of its kind in Russia.
Crushed to 0-20mm, the processed material is transported by conveyors to the washing complex consisting of a feed hopper, conveyors, a four-deck washing screen, a spiral classifier and an automated control system.
Topsoil at the rear of the stockpiles is removed and taken to a special site nearby so that further sand and gravel can be garnered, and to date the quarry, along with adjacent quarries, has supplied over 1 million tonnes of inert materials/aggregates to Sochi.
Maykop Nerud was established just over four years ago by Stanislav Steblyansky and Alexey Poddubny, deputy general directors, along with another shareholder. Alexander Kozhanov is general director of Maykop Nerud.
The necessary documentation to open the quarry took some two and a half years to complete. An initial move that has proved a great asset was the acquisition of a railway yard near the existing quarry, and it is from here that one or two trains containing 3,000-6,000tonnes of crushed stone and building sand is transported daily to the Olympic site. With the drive from Maykop to Sochi over mountainous roads, some in urgent need of repair, taking around six hours in a modern car, the use of trucks is out.
Indeed, initially the company bought products from another company and delivered it by railway to customers. However, as the customer base grew, including entering into contracts with major construction companies in Sochi, it became apparent that the company would have to buy crushing and screening equipment to improve its business further.
“In the initial stages of preparation for the requirements of the equipment we had planned to purchase a mobile washing plant, but Metso’s engineers convinced us of the advantages of stationary washing and screening equipment. Today, with the complex working 24/7 at full capacity, it is easy to see that we made the right choice,” says Alexey Poddubny.
At present, Maykop Nerud is producing some 40,000tonnes of material a month (15,000tonnes of sand, 15,000tonnes of 10-20mm aggregates and 10,000tonnes of 5-10mm aggregates) but it sells some 140,000tonnes, including material from other companies. But when the new Metso equipment is installed the quarry’s output will increase to 140,000tonnes a month.
“Maykop is the only producer of very good quality sand and nobody in the area can produce the same quality sand. For the Olympic construction work there are very strict rules regarding the quality of the sand. This is why they want to buy from Maykop,” says Stanislav Steblyansky, who points out that Maykop sand is being used for the special road for the Formula 1 event in Sochi.
FACT FILE: RUSSIA
Location:
City of Maykop, Republic of Adygea, southern Russia
Raw material:
Hard rock sand-gravel mix, hardness40kN
Capacity:
250tonnes/hour, with increase up to 550tonnes/hour in 2012
Resources:
Over 10 million m³
End products:
Washed building sand 0–5mm and crushed aggregates 5–10mm, 10–20mm, 5–20mm, 20–40mm“One of the most important things at Maykop is that we have Metso spare and wear parts at the plant. This is important because otherwise there would be some distance to travel if anything breaks down.
“We can use the spares for our own purposes but parts can also be delivered to other Metso customers as required. This is a special agreement between Metso and Maykop.”
And with everything produced at the quarry going to Sochi for the Olympic construction it is essential machinery keeps running. In Sochi, Stanislav Steblyansky is on hand to see products from his company’s quarry on site at Tunnel Complex No 1 and at the Severstroy plant.
Tunnel Complex No 1 is part of the route from Adler in Sochi to the Alpika Service Alpine Resort, which will include six railway tunnels with a total length of 10.5km, three motorway tunnels totalling 7.5km and service tunnels between the rail/road tunnels totalling 9.1km.
The 2.5km rail tunnel at Complex No 1 has a cross section of 74m² while the two-lane road tunnel has a cross section of 134m². Maykop Nerud has supplied more than 150,000tonnes of 0-5mm washed sand and aggregates in fractions of 5-10mm, 5-20mm and 10-20mm for shotcreting and for the concrete lining of the tunnels, which are being constructed by UGSK.
Crushing
1 x Lokotrack LT106 jaw plant
1 x Lokotrack LT
200HP cone plant
Screening
1 x Lokotrack ST3.5 mobile screen
1 x Nordberg CVB 2060-4 inclined screen
Washing
Metso stationary washing complex
including 1 x Nordberg SF2870 sand trap
WHEELED LOADERs
2 x Volvo L120F
Excavators
2 x Volvo EC240BLC
HAULING
Various vehicles
Equipment to be installed with commissioning in the second quarter of 2012
Crushing
1 Nordberg C80 jaw crusher
2 x Nordberg HP4 cone crushers
Screening
2 x Nordberg CVB2060-4 inclined
screens
Washing
Metso complex including
1 x Nordberg SF2360 sand trap
1 x Nordberg SF2870 sand trapAcross the city, Taisa Shyryaeva, quality manager in the laboratory at Severstroy, and her team check samples of the concrete (made using sand and aggregates from Maykop Nerud) that is being transformed into prefabricated tunnel linings. Stanislav Steblyansky is checking his sand and aggregates that have arrived at the plant’s railway sidings from Maykop Nerud.
At present Severstroy is producing the concrete elements for 23km of various tunnels, and at its height was producing elements from 72 specially-built Herrenknecht forms in 24 hours.
However, with closure of the plant in February or March 2012, three years after opening, the operation will be moved to near Moscow where, among other projects, it will make elements for the Moscow Metro.
Maykop Nerud will also be looking for further growth, and can look to an estimated 10 million m³ of sand and gravel, or 20 years of reserves, left in the quarry. After quarrying is completed the area will be turned into an artificial lake for recreation and fishing.