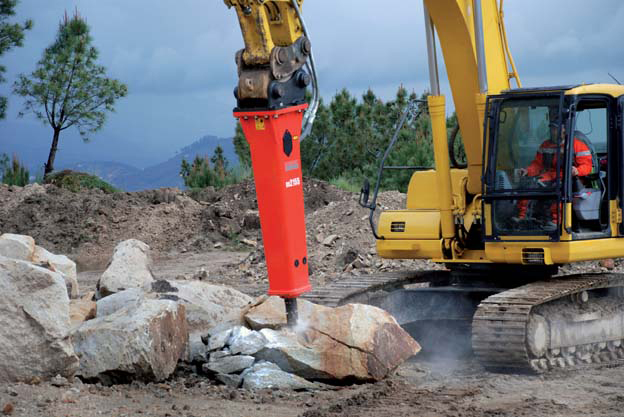
Hydraulic breakers have become a key tool for secondary breaking and, in some quarries, are also gaining ground in primary breaking application
Hydraulic breaking is the technique of choice in Europe when it comes to secondary breaking - drill and blast for this type of work has almost completely disappeared due to the safety issues. But developments in performance and power also now mean that hydraulic breakers offer an alternative method for primary breaking in some circumstances.
"Drill and blast is still the first option for primary applications," said
"There are a number of other options when it comes to blast-free quarrying other than hydraulic breakers. The first is to use surface miners but these are very rare in Europe mostly because they need a large deposit to be economic and many quarries in Europe are too small. The other option is to use a hydraulic excavator fitted with a ripper but the potential of this technique is very dependant on the geology.
"But both these approaches still call for the use of a breaker to cope with more difficult or harder deposits making hydraulic breakers a key tool in European quarries." According to Ahr, breakers can make maximum use of reserves by offering a higher efficiency in extracting the final bits of rock before a consent area is exhausted. The breaker can be used to pick off rock where conventional blasting would not be possible or economic. In the same way, hydraulic breakers can be used effectively for selective extraction in deposits with different grades and avoid mixing to maintain quality.
"In one quarry in Norway there are some intrusions that are almost 100% dolomite but these are interspersed with normal limestone," explained Ahr. "Mixing of these two means that it can only be used for low grade applications such as road construction and is next to worthless, but by using a combination of a ripper and hydraulic breaker, the dolomite can be kept separate and the operation is significantly more profitable."
Technology
With greater reliance being placed on breakers by quarries, there is also a demand to make the attachments more user friendly in terms of use and maintenance, as well as minimising downtime.
Changes in design were mostly as a result of the Outdoor Noise Directive but the need to reduce noise and vibration has also been driven by urban construction. While these improved designs were not conceived with the quarrying market in mind they have benefitted the industry and helped to improve operator comfort and reduce machine wear.
"Breakers now produce around 122dB(A) where as five years ago they were commonly producing 130dB(A)," said Ahr. "Further reductions are difficult as it is the striking of the rock that makes the noise rather than the operation of the breaker." Performance of breaker calls has improved significantly too - most modern designs are now 65 to 80% efficient - and this trend has also been combined with the launch of larger breaker sizes and the combined effect is significantly higher powered units.
"I don't think that there is a market for much larger breakers than our current 10tonne HB 10000 - the focus in the future will be on producing more energy from less weight," said Ahr. "The big challenge is on metallurgy and improving hydraulic and percussive energy delivery." Changes in design have also helped to reduce maintenance - autolube systems have been available for a decade now and these not only help save time but also improve dust protection, so less time is needed to clean the chisel and bushings. According to Ahr, in the future we are likely to see closed guide systems for tools to further reduce maintenance.
Another key development will come from cooperation with carrier manufacturers. "Hydraulic breakers are attachments and to a large extent depend on the developments of the base machine or the hydraulic excavator," said
One area where development is expected is through auto-adjust systems that will enable the carrier machine to detect which breaker has been attached and change the hydraulic flow to match in order to get the best performance from the breaker and also to minimise the potential for over powering. It reduces the potential for human error in the set-up process.
Appropriate technology
Nonetheless, most breaker development is aimed at meeting customer needs. "We see a definite trend or shift towards the emerging markets in terms of market share for hydraulic breaker sales and we think that emerging markets will play a major role in effecting our business in the future," said Ramaswamy. "We therefore plan to develop flexibility in our breaker design so that our breakers can be made suitable for both the developed markets as well as the emerging markets.
"This approach is evident in the new hammer models launched last year which have a basic or standard version for the emerging market and fully loaded version for the developed market. This is made possible by a host of 'retrofit options'. This flexibility also provides customers with the ability to retrofit the hammer after purchase, to ensure that the hammer is always to the latest and most appropriate configuration as application requirements change."
Demand
Sales of hydraulic breakers have dropped with the economic situation and Ahr said that many rental operators are ageing their fleets and focusing on refurbishment, maintenance and repair. However, he said that this may change in the next few months.
Atlas Copco is also working to help its customers and has leased a couple of its HB10000 breakers to customers where it would previously have only considered a sale, as Ahr said that there is demand for the unit but customers are struggling to finance the purchase right now.
Ramaswamy has also noted a change in buying patterns for hydraulic breakers with reduced demand, which he directly links to the current reduced demand for aggregates and cement in Europe. But he added, "With major economies of the world initiatinssg steps to stem the decline, we anticipate that the worst is over and the turn around should happen soon, although when the business climate will improve is anybody's guess."