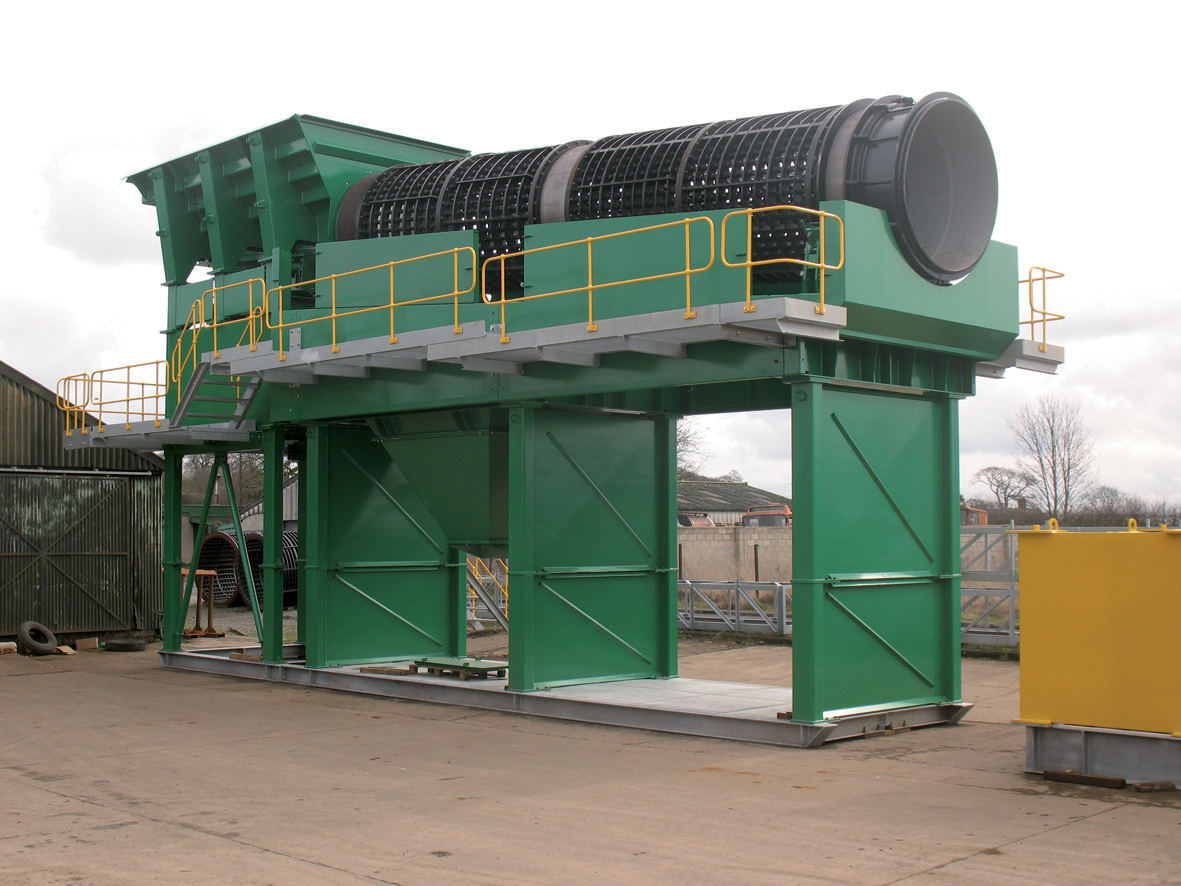
One operator quarrying limestone for cement production had over the years experienced heavy clay contamination with its as-dug material and was forced to separate the contaminated rock containing clays to form a waste tip, which grew to approximately 1.5 million tonnes. The Stelex trommel will be used to clean this waste material to recover the good rock for further processing, thereby increasing the company's efficiency and production levels.
The feed hopper, made of abrasive resistance steel, can accommodate 100tonnes, and a variable speed-reciprocating tray, which is supported on rollers beneath the hopper, feeds material into the barrel at a pre-programmed rate. The 1.8m diameter barrel (made up of four 2m long segments) is manufactured from high grade steel bars welded to form segments, which are bolted together. The apertures are made to suit an individual customer's requirements.
The barrel is carried on six steel rollers, two of which are driven by heavy duty, variable speed, hydraulic motors, which allows the barrel speed to be matched to the optimum feed rate of the material.
The dirt or clays in the feed are discharged through the barrel segments while the clean rock travels down to be graded by the different apertures in the segments. Oversize, which can be lump sizes of 900mm, is discharged off the end of the barrel.
Both supplied machines are mounted off the ground to allow materials to discharge below for removal via loading shovels. One unit is mounted on concrete walls and supplied with a feeder/collecting conveyor and a 56m stockpile conveyor: the other machine is on a pre-built steel skid frame and legs with chutes under the first 4m section for sized product separation onto a stockpile conveyor.