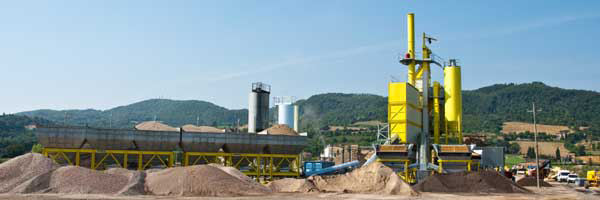
Asphalt plant manufacturers are investing heavily in developing equipment to reduce energy costs and emissions
Energy savings and reduced environmental emissions are two major challenges for industrial designers of any kind of machine and asphalt plants are no exception. Asphalt production calls for great amounts of energy in the form of heat to dry and heat aggregates at the required temperature.
As
At present most asphalt is produced in hot mix plants at around 160°C, a temperature that decreases viscosity and moisture during the manufacturing process, and offers a very durable material, commonly used for high-traffic areas such as busy highways and airports.
According to Ammann-SIM, methods to produce asphalt at low temperatures have been the subject of research for a while, especially methods that do not require drying of the aggregates - the most costly step in terms of energy.
"In the case of the aggregate drying process, we are thinking of the burner-dryer system. With the burner we intend to develop the energy contained in the fuel to generate a combustion reaction. As this is a highly exothermic reaction, it produces heat," said the company.
"Therefore the first step to reduce energy consumption is to obtain this reaction in an efficient way: the generated heat is transferred to the aggregates and this is where the dryer comes into play." The company has been seeking a type of blading that can work efficiently with all kinds of mixes, and it is undertaking research in partnership with the academic world to study heat transfer mechanisms in asphalt mixing plants' dryers.
"The first significant results obtained were used to design the [SIM] RAH 50, a dryer that uses 10-15% less fuel, and employs up to 50% of milled asphalt," said Ammann-SIM "Using the new sophisticated technology leads to lower fuel consumption and a correct and efficient use of milled asphalt. In order to control the thermal exchange, the RAH 50 can vary the rotation speed according to exhaust gas temperatures and the product to be dried." Indeed, Turkish manufacturer
The company says that using the system can boost aggregate output by up to 50%; increase asphalt plant efficiency by 15%, and reduce bitumen consumption by 10-15%.
It is also further proving its new
Asphalt output of 500,000tonnes/year is to increase with the commissioning of a sophisticated new 320tonnes/hour plant, which is twice that of the earlier generation plant installed at the site.
The two asphalt plants are linked to two Challenger systems, and Simge Group is adding the Ratek recycling system to the new asphalt plant to capitalise on the potential for recycled asphalt. Aggregate costs in Turkey are comparatively low but bitumen costs are high, so asphalt recycling is becoming more of an issue in the country.
This prompted E-MAK to develop its Ratek recycling system, which operates in addition to a conventional asphalt plant. Because the Simge Group has its own quarries, it is able to fine tune its technology in the field and will prove the Ratek concept.
Meanwhile, Marini, part of the
"This was in terms of energy saving (both electrical and thermal energy); environmental impact (noise reduction as well as low gas and dust emissions); finished product quality, and maintenance (use of special anti-wear materials and a reduction of electric motors being used)," said Marini. Apart from this, plant components including the dryer drum for virgin and recycled aggregates, bag filter, screen, and mixer were also examined.
The asphalt plant installed in Città di Castello, Perugia area, central Italy, features high-efficiency Siemens electric motors and, thanks to the use of inverters, allows for the control of dryer rotation speed, exhauster fan, screen and mixer.
A report will show the different operational steps and list the data of asphalt produced, such as percentage of RAP [recycled asphalt pavement] used.
UK-based manufacturer
Its new Phoenix StarMix 3000 high level static 240tonnes/hour asphalt mixing plant has a 3,250kg mixer and includes eight cold feed hoppers, facility for RAP introduction, four vertical high efficiency bitumen storage tanks, a fibre additive system and 300tonnes of hot storage capacity under the mixer.
The plant has been commissioned in County Tyrone, Northern Ireland, by
Moroccan company Enterprise Ouarrach, which bought a Phoenix RoadStar 1500 mobile batch plant three years ago for projects near Casablanca, required a larger capacity plant, and in a departure from the more usual fully mobile plants supplied in Morocco in recent years, it selected a Phoenix StarMix 3000 static 240tonnes/hour batch plant to support the continuing infrastructure development and maintenance. The new plant, one of the largest in Morocco, offers high capacity and environmentally compliant installation, and features five cold feed hoppers, a 2.5m diameter dryer, mixing tower with screen bypass facility, bag filter, five horizontal bitumen storage tanks and 200 tonnes of hot storage capacity.
Earlier this year, ÇESAN launched its new easy-to-install mobile asphalt plant with a capacity of 280-300tonnes/hour, and featuring a five-floor screening system, four tonnes of mixer volume, a stone mastic unit and standard road dimensions, allowing easy transportation on all roads across the world.
The Turkish manufacturer also saw one of its 200tonnes/hour plants successfully supplied and commissioned in Nigeria, where its low operating costs and the ability to be operated either semi-automatically or fully automatic by two personnel, made it an ideal choice.
Highways maintenance specialist, FM
Fitted with a multi-fuel burner, a frequency inverter controls burner blower speed to optimise efficiency of the drying process.
The heart of the recycling system is a 2.8m x 12m long uniflow recycling drum, which dries and heats the RAP materials. It is fitted with a 5,000kg twin-shaft paddle mixer and has a hot mixed material storage capacity totaling 600tonnes.RSS