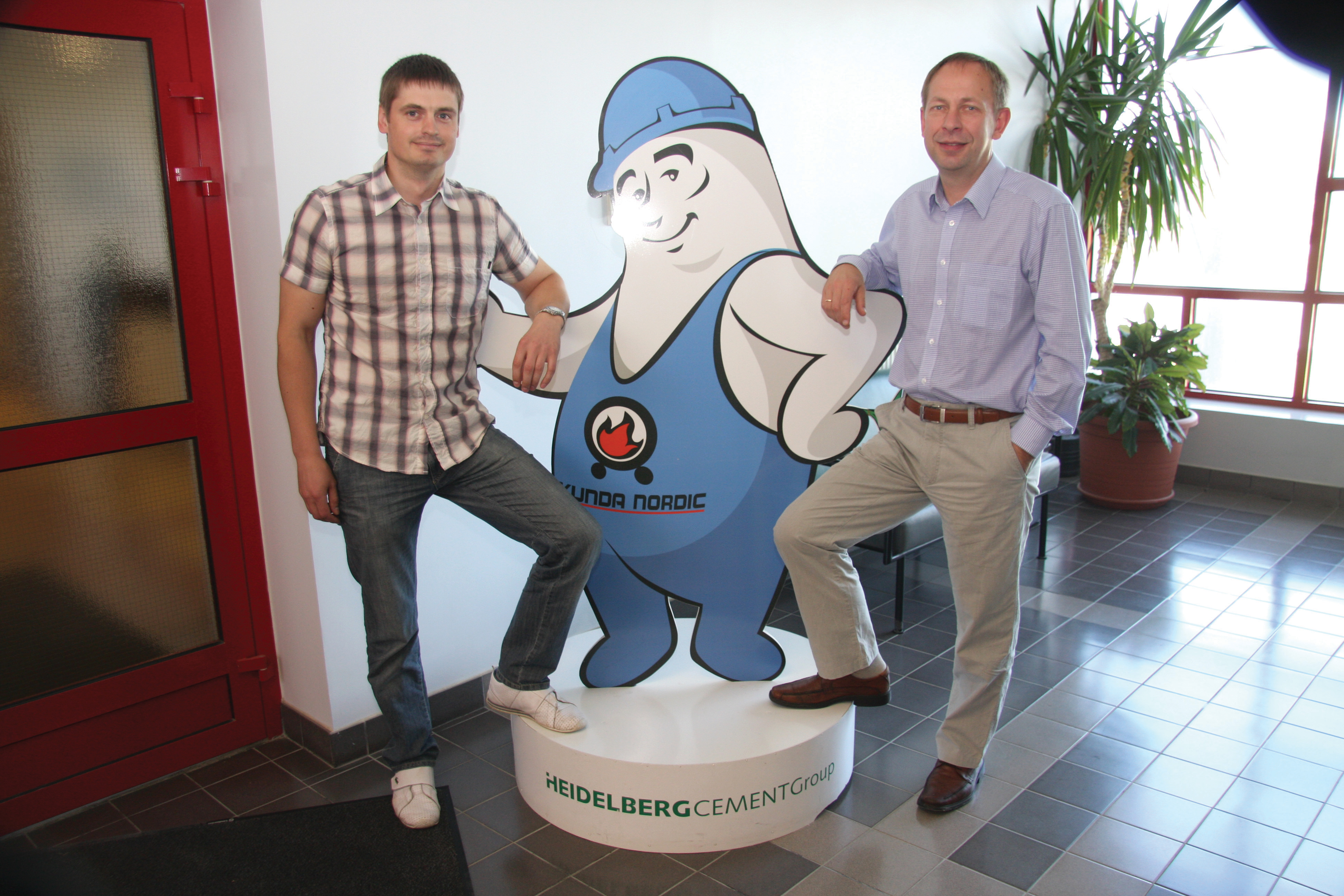
Estonia's biggest quarry also operates the country's only cement plant, as well as a port. ABE visited the Heidelberg site to find out more
Knda Nordic Cement (KNC) is an operation with over 140 years of tradition but despite the age of the quarry, it is still a key player in the Estonian aggregates and cement business. The company's many operations are located in and around the town of Kunda in the North Eastern part of Estonia - in a region that has the most commercially viable limestone reserves in the country.
Today the company belongs to a joint venture between
Estonia is characterised by the fact that the granite bedrock is too deep to be exploited commercially. The only viable material is limestone and even then, the number of limestone quarries is quite limited. The deposit located in Kunda is the biggest quarry operation in the country corresponding approximately 10% of the total production in Estonia.
The KNC operated cement plant is the only one in the country. Therefore the company is vital for the economy of Estonia and even more so to the town of Kunda.
KNC's main operations are a limestone quarry, a cement factory and a port. The whole area covers approximately 400ha. Reserve levels are good in Kunda and applications are underway to ensure the site is operational for tens and tens of years to come. The workforce at KNC numbers 220, which clearly demonstrates the scale of the operation.
The recession has hit Estonia as well and resulted in some cutbacks but, according to Meelis Einstein, who is managing director of KNC, the first signs of recovery can been seen and felt.
"The whole world has suffered from the recession, and so is the case with Estonia and KNC. At the lowest, our operations were reduced by half, but fortunately it seems that the worst period is over.
Modernisation
Even during the Soviet times, the operation was regarded as modern - to a certain degree. For instance, the quarry was equipped with Finnish crushing equipment instead of domestic machines, which was very unusual at that time.
The most recent upgrade took place a year ago, when a modern fleet of portable crushing and screening units was purchased from
"The old plant was stationary and was equipped with a jaw crusher and two impact crushers," explained KNC development manager Riho Iskül. "Consequently, the hauling fleet was big and needed a lot of manpower and fuel and was really quite uneconomic. So we analysed the situation and our need for improvement and came up with the plan to turn the quarry into a portable operation. Now we have all of our crushing and screening units on wheels and in spite of the fact that we only move the plant probably once a year, we save a lot in fuel and manpower." In addition to direct savings, the new crushing plant increased the operation's profitability through changing the type of crushers. "Since the impact crushers of the old plant were replaced by one secondary and one tertiary cone crusher, the amount of fines has decreased almost by half.
"This has naturally increased the amount of saleable aggregates," said Iskül. The fines are also used economically - they are transported to the cement factory and used in cement production.
Customers
The quarry produces materials both for the company's own cement plant and for external customers.
"All the crushed limestone is sold to customers - mostly companies in road construction and concrete production. They need good quality material with high cubicity, and that's what we now get from the new plant," explained Iskül. "We produce seven different standard end products and special products upon customer specifications, and because the plant is fully automated, we are now much better equipped to flexibly react to customer requirements than in the past." The annual production of the quarry is approximately 2million tonnes with one third sold to customers and the rest is used in the cement factory. Most of the year the plant operates in 12 hour shifts, seven days a week, but there are off-peak periods with eight hour shifts, five days a week. In December and January the plant is closed for maintenance.
"One of KNC's policies is to subcontract non-core operations. For instance, drilling, blasting and loading are subcontracted to a local subsidiary company that belongs to the Finland-based Lemminkäinen group," said Iskül.
Blasting takes place every second day with around 12,000 and 20,000tonnes of limestone won in each blast.
Water is a particular problem at the site as the bottom level of the quarry is located below both the seawater and groundwater level. Therefore the quarry is equipped with a series of powerful submersible pumps and a set of canals to control the waster masses.
Moving railroad
"The main quarry has two separate operations," explained Iskül. "Two thirds of our limestone is suitable for cement production and this material is blasted to blocks with the maximum size of 1m and loaded to railcars by a wheeled loader. The train then goes directly to the cement plant that is located approximately 5km away from the quarry site. At the plant we have an big old jaw crusher to reduce the material to the right size.
"Altogether we have 7km of railroads in the area and they also serve as an alternative way of transportating material." Around a third of the limestone contains too much magnesium oxide to be suitable for cement production and this is crushed at the site and sold as aggregates to customers working in the construction sector.
"Once in a while the railroad is moved closer to the face. Moving the tracks is not a cheap operation but our calculations prove that the rail transport is much more economical than the use of a hauling and loading fleet," he continued.
KNC's policy also is that the transportation of aggregates to customers is primarily down by the customers' own truck fleets. "We have several stockpiles on site and the customers come here to be loaded by a subcontracted wheeled loader," said Iskül.
Oil shale
A particular geological character of Northeast Estonia is the oil shale - the Estonian translation is 'burning stone' - which for so many years was the most important domestic source of energy. Today oil shale is still extracted and used in the country and KNC is no exception to this.
KNC owns an oil shale deposit in its area that is used to power the cement plant. Oil shale is easy to exploit and is extracted by an excavator equipped with a ripping device, which is then swapped for a standard bucket to allow the material to be loaded into haul trucks.
We extract it because it can be used in generating power in our cement plant. Our oil shale corresponds one third of the energy required to heat the plant," explained Iskül. "As far as we know, we are the world's oldest cement plant using oil shale as fuel." KNC has indeed four different quarry operations altogether. In addition to the three already mentioned, KNC also has a clay quarry that is used to supply further raw materials for the cement production. The quarrying there takes place approximately once a week and the operation is subcontracted.
Streamlined
KNC is very careful in trying to make the quarry operations as cost-effective as possible and also feasible. The mining department - the company function responsible for the quarries - contains only 14 people, out of which 12 people work in the main quarry and two at the oil shale operation.
"The obvious reason for this is of course the use of subcontractors, wherever possible," said Iskül. "The most recent reason for considerable cost savings was the modernisation of the main quarry. Our main aim was to minimise the need for transport and that's exactly what we have done. The railroad is an essential factor in reducing wheeled transport and is a significant factor in saving fuel."
Secure future
The limestone quarry in the present form has another 15 years of operational activity, however, KNC has already taken steps to secure the operation beyond that. In the vicinity there is a 172ha sized deposit where the exploration process began already five years ago. There are limestone reserves of 27million m³, which will last for another 50 years and the application for these reserves was presented to the Estonian ministry of environment in May this year.
"Our operations have been an essential part of the nearby communities for a very long time," said Iskül. "Naturally we are aware of our impacts to the people and to the environment but restoring old quarries is an important sustainability task for us. One oil shale deposit has already been filled by overburden and top soil and planted by trees that it will turn into a forest. The main quarry on the other hand still has years of active life but afterwards it will be turned into a lake."
Cement leader
KNC is the only domestic producer of cement in the country and is sold to domestic clients and the rest goes to export into Latvia, Finland and Russia.
The plant also produces clinker for export and in 2009, KNC's clinker was exported to Russia, West Africa and Brazil. From the peak sales in 2007 the figures have decreased by almost half but as stated earlier, the return of business is already on its way.
The history of cement production in Kunda started in 1870 when the operation was founded by John Girard de Souçanton - the owner of the Kunda Manor. Since then there have been a lot of developments - mostly for the better - however, the last decades of the Soviet era resulted in significant pollution problems. In 1992 the company was privatised with the name of Kunda Nordic Cement Ltd and in 1999 was acquired by Heidelberg Cement Group. Today Heidelberg is the majority owner with a 75% shreaholding, while CRH holds the remaining 25%.
"While our cement plant by most standards is a modern operation, there is still quite a lot to do to turn it into an ultra-modern plant. The process is based on the wet method and we do have plans to modernise over the next few years to the dry method, which is more energy efficient. We did have already a tentative plan for the change but due to the recession we have had to postpone it for the time being," said Einstein.
Integrated business
Since the cement plant is located just a few kilometres from the coast of The Gulf of Finland, the town of Kunda already had a port facility at the time when the cement plant was established in 1870. But in 1911, the port became a part of the company and has been a vital element for its export business.
However, in recent years the port also has become an element of Heidelberg-related imports, as well helping to meet demand for hard rock aggregates in Estonia. As a result, KNC has recently started a new business to import crushed granite aggregates from Heidelberg operations in Norway and markets them to domestic customers.
"We are quite a diversified company with different types of operations. However, all our operations are linked together one way or the other," Einstein concluded.