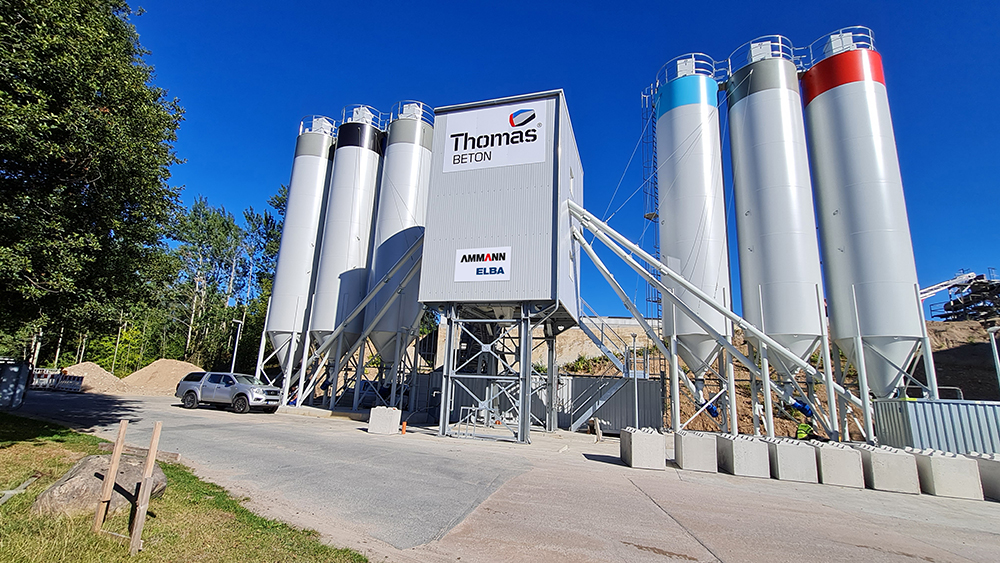
With careful planning, Thomas Beton's concrete plant, based in Lurshchau, Germany, was successfully modernised during ongoing operations. An Ammann Elba CBS 120 SB concrete mixing plant was connected to an on-site aggregate linear bin as the new heart of the plant.
When the first 300m³ of concrete was mixed during the commissioning of the new plant, Rainer Brings, managing director of Thomas Beton, was impressed by the speed of the plant. With the acquisition, he can significantly increase his hourly output compared to that of the old one - up to 120m³/h is now possible.
This increase in output was urgently needed as demand for fresh concrete had increased significantly due to the need for large foundations for regional wind power plants and a nearby precast plant. The old plant had reached the limits of its capacity.
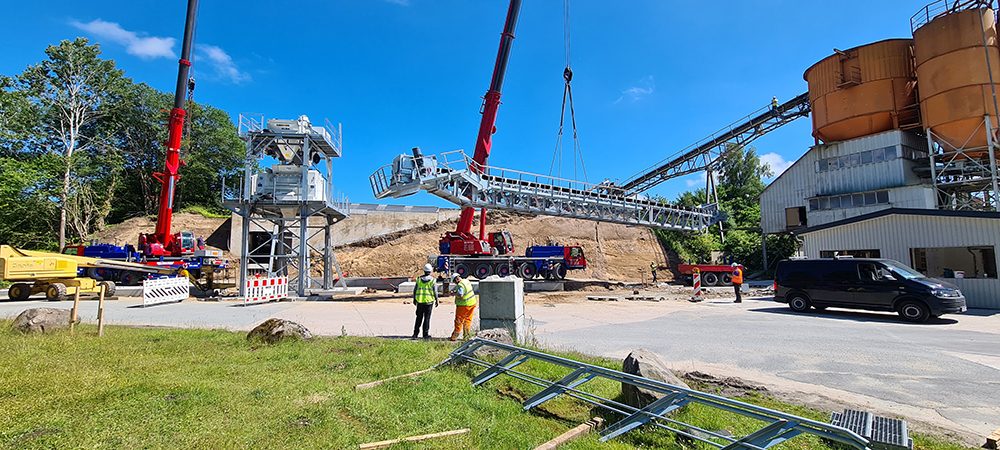
Two challenges had to be mastered during this modernisation. On the one hand, the existing dosing construction had to be technically integrated into the new construction across the height difference of an escarpment. On the other hand, the plant had to continue production during the modification in order to be able to serve the current orders.
After the stock had been checked, it was determined in detail which components could be replaced and which could continue to be used. “We now operate 12 Ammann Elba ready-mixed concrete plants of this type in our factories in northern Germany,” says Brings. “When planning the new plant together with Ammann Elba, we were able to make perfect use of the flexibility of the assemblies.”
The modernisation of the site during ongoing operations took only eight weeks. While the old mixing tower continued to do its job, the new ready-mixed concrete mixing plant CBS 120 SB with single-shaft mixer CEM 2660 S was connected to the existing aggregate linear bin as a belt conveyor plant.
The complete locking and dosing technology of the on-site linear bin itself was renewed. A technical masterpiece was the threading of the new 35-metre-long weighing belt into the concrete linear bin. This challenge was successfully solved thanks to the many years of experience of the Ammann Elba dealer Proschwitz GmbH, Trittau, which was also responsible for the overall assembly.
The discharge gates are actuated via compressed air by an integrated screw compressor. The weighed aggregates are finally conveyed directly into the pre-hopper of the mixing plant via a conveyor belt. A sand-moisture measuring device below the dosing gate continuously measures the material moisture.
The cement is stored in six cement silos, each with a capacity of 100 tonnes. High-performance cement screws EZL 80/100 are used for dosing in the generously dimensioned cement weigher.
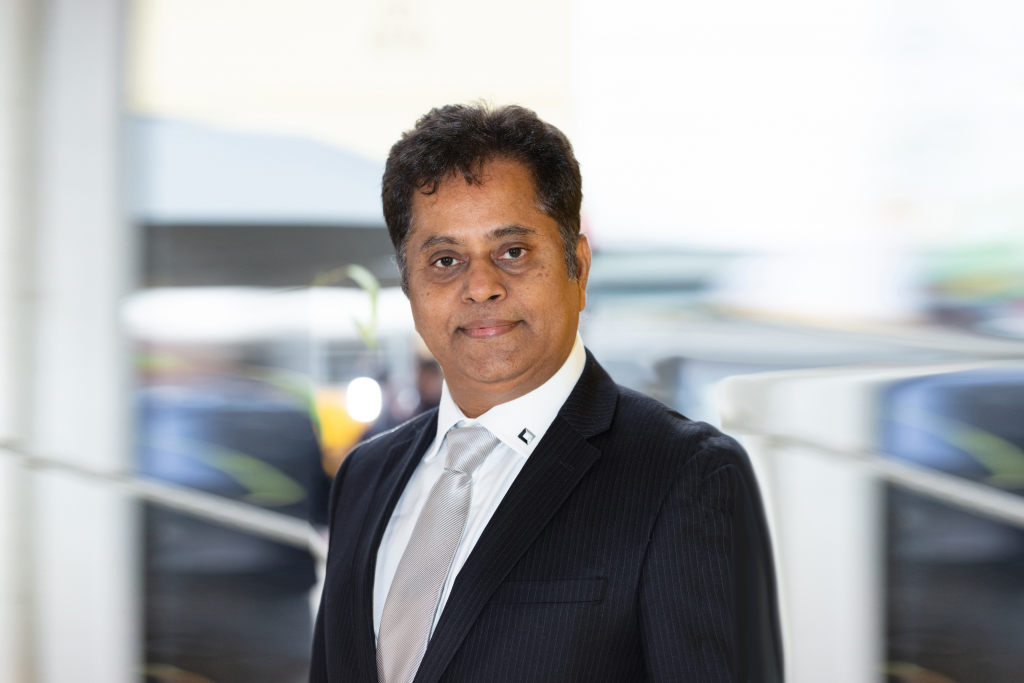
Brings says he is “completely satisfied” with the result and impressed with the uniformity, stability and high quality of the concrete produced by the Ammann plant. A dedusting filter and a mixer cleaning system are integrated into the CBS 120 SB, preventing contamination. The winter cladding LL 60, which encases the entire mixing plant, also protects against temperature fluctuations caused by the weather.
“From planning to transport and installation, Ammann Elba demonstrated a high level of detailed work,” says Brings. “And since our team knows the Ammann Elba plants very well, we were also able to continue production seamlessly.”
Sakthi Ramamoorthy, CEO of Lintec & Linnhoff Concrete, knows more than most about the concrete industry, having dedicated decades of his career to it. He says spotting the potential for high-quality manufacturing in Asia and harnessing the benefits of automation have helped establish the Eurotec concrete batching plant brand in the global market.
Commenting in a company Q&A session on the most interesting change he’s observed in the industry over his time in the business, Ramamoorthy says: “When I joined the industry back in 1992, automation was just starting. Before that, all the modules had a lever attached to them, and only by moving the lever would you be able to dispense the concrete, but we have come a long way since then. Most plants now are completely automated and increasingly focused on more sustainable operations.”
Ramamoorthy says that Lintec & Linnhoff Concrete recognised these trends early, enabling the company to create product lines that appeal to customers. He adds: “Also, our Lintec containerised designs have been a real advancement for the industry. Ever since the early designs, it’s been something popular with clients. The new plants are sleek, powerful, and eco-friendly.”
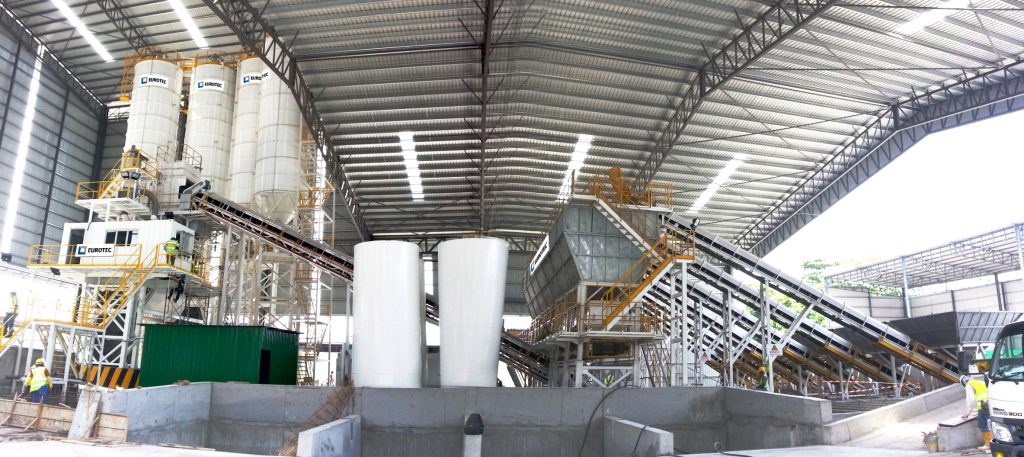
Responding to a question about the success of the Eurotec brand and its future development, Ramamoorthy says: “The cost of importing plants to Asia from Europe has always been high. There was a gap in the market for high-quality plants that could be sourced at economical prices. That’s when we launched the Eurotec brand to fill that gap. Keeping the European design, we manufactured the plants in Asia and achieved high-level cost efficiencies without compromising quality. We launched Eurotec in 2003 and have sold over 400 plants across Southeast Asia, South Asia, the Middle East and Africa.
“I believe we’ll see some interesting innovations in the sector over the next five years. Large concrete batching plants will only be seen on megaprojects, requiring high-level concrete production at the job site. For other applications, we’ll see plants become increasingly mobile and shift to fully electric-powered. This will help the industry boost its sustainability and efficiency. We’re excited to share further details on these trends with our customers in future.”
An ELKOMIX-60 PL precast concrete batching plant and an ELKON ERCYL-10 concrete-recycling plant are providing vital support to a leading Croatian building materials company. The plants are being put to work on ready-mixed, precast and semi-dry concrete production in Drjne, in Croatia’s Koprivnica region. The customer has more than 1,700 employees and is renowned for its quality cement, concrete, aggregates, and bricks.
The ELKOMIX-60 PL plant has an ELKON 1500/1000 1 planetary mixer equipped with a moisture probe to precisely control water content. The set-up also includes 6x20m³ aggregate storage bins made from galvanised steel which are partially buried underground so that aggregate loading can be done without ramps.