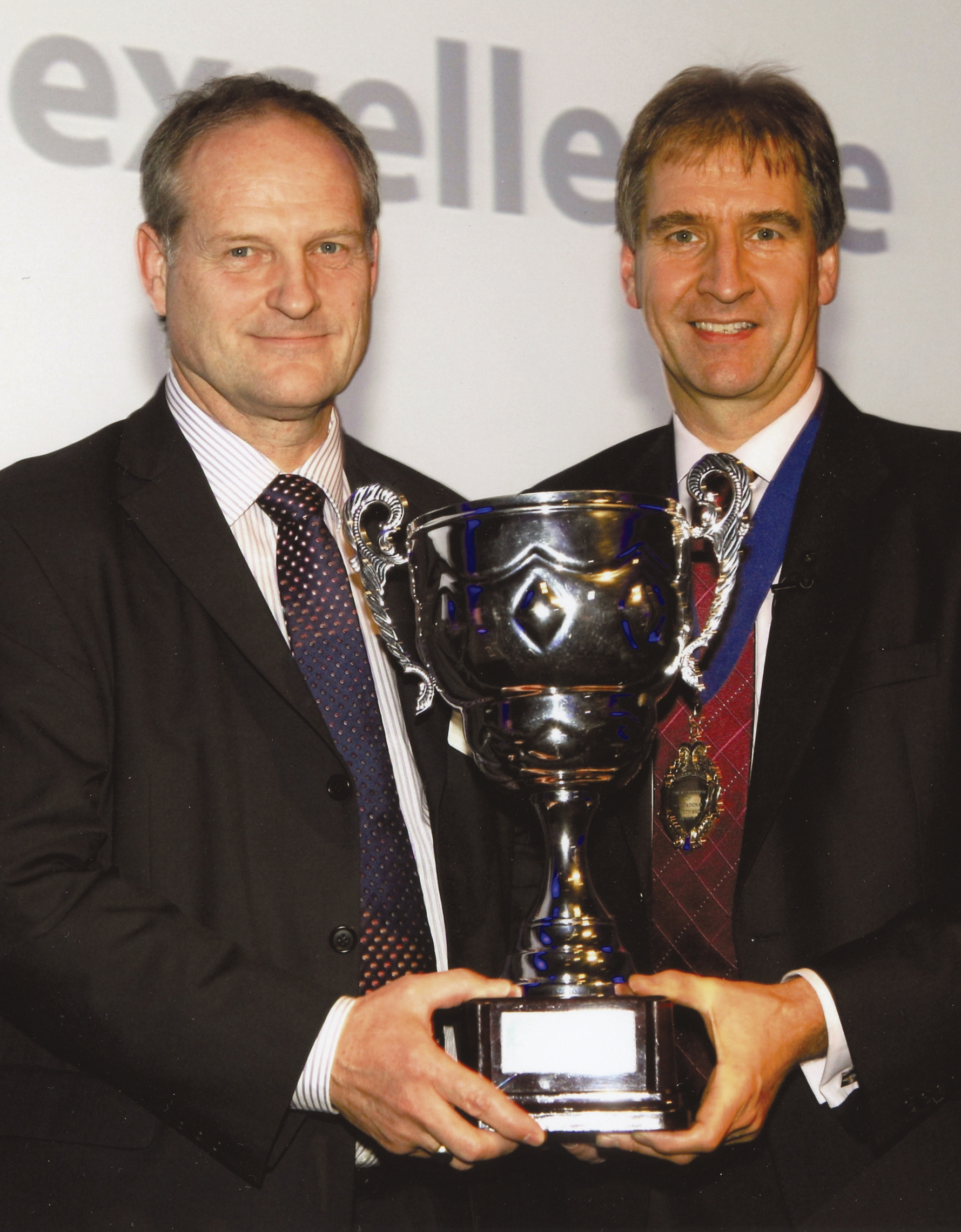
Raising the Bar, an initiative at the John Wainwright quarry, aims to create a sustained and vibrant safety culture as Patrick Smith reports
Anew safety initiative called Raising the Bar has been introduced by an award-winning company at its quarry.
Late last year at the
At its Moons Hill Quarry in County Somerset, south-west England, the company quarries basalt, and has been supplying premium aggregates to the construction industry since 1891.
Raising the Bar aims to get every member of the workforce up to speed with health and safety and keep the accident rate on a downward trend by creating a sustained and vibrant safety culture at Wainwright, and helping every member of the workforce to make safety a personal priority.
The company says it will do this by challenging current work practices to ensure safety first; ensuring a robust approach to non-compliance; Visible Felt Leadership (VFL), where managers lead by their own actions; raising the profile of the Works Safety Committee, and ensuring Wainwright has a fully competent workforce.
Another part of the scheme is The Scoop, a company health and safety newsletter published twice a year and distributed to everyone who works at Wainwright. It raises awareness among the workforce about health and safety standards; highlights initiatives to keep accident levels low and contains an array of interesting stories, helping to motivate staff to maintain the highest possible safety standards.
“Wainwright is a participant in the Health and Safety Executive’s (HSE) ‘Target Zero’ initiative,” says safety, health and environment manager Wayne McKeown. “This is intended to decrease injuries in the quarrying industry by 15% each year.
“The Scoop is a means of keeping Wainwright’s team in touch with the latest safety news, and helping to raise awareness of every aspect of the Raising the Bar initiative.”
Wainwright also offers Institute of Occupational Safety and Health (IOSH) accredited training courses across its workforce to ensure that staff members receive the right health and safety training for their role in the business.
The safety credentials of Wainwright’s safety management team are now subject to independent verification, following the company’s enrolment in the Institute of Quarrying’s (IoQ) Corporate Professional Competence (CPC) scheme. It is the ninth company in the sector to sign up for it, being awarded a CPC in July, 2011 following an extensive audit of the safety qualifications of its management team.
Wainwright has also been participating in an HSE-fronted initiative looking at the long-term effects of silica dust on the health of the workforce. It was asked to represent the
The initiative aims to raise awareness of the risks associated with silica dust, and to develop a policy that the HSE can present to the industry’s workforce.
Alongside this, Wainwright has taken the opportunity to review its own silica-dust controls. The basalt quarried at Moons Hill contains almost 60% silica, making this an especially pertinent issue for the company.
To improve its onsite controls, Wainwright has commissioned dust-mask face-fit testing and dust-mask training; improved the quality of the respiratory protective equipment issued to its workforce, and improved standards of housekeeping.
Over the years, Wainwright has also invested in a DustFoam Suppression System, fixed-plant hoover systems, air conditioning and water suppression systems.
As part of the Raising the Bar initiative, Wainwright has introduced six-monthly Safety Review meetings for its site contractors, and these are designed to ensure that all contractors understand the safety requirements of the Moons Hill site.
“Generally, everyone has safety issues,” says Peter Barkwill, Wainwright’s managing director. “So we need to work together to make sure we’re doing everything right. There are contractors working in every area of our business, including maintenance, crushing, cleaning and overburden removal, and we have a duty to help them operate as safely as possible.
“The Contractor Safety Review meetings ensure that we communicate effectively with every contracting business we use, and that our supply chain partners operate to the same exacting standards that we apply.”
In a bid to further improve its health and safety credentials, Wainwright is now working towards the Occupational Health and Safety Management System 18001 (OHSAS 18001) accreditation, the British Standard for the management of health and safety, which it hopes to achieve by the end of 2012.