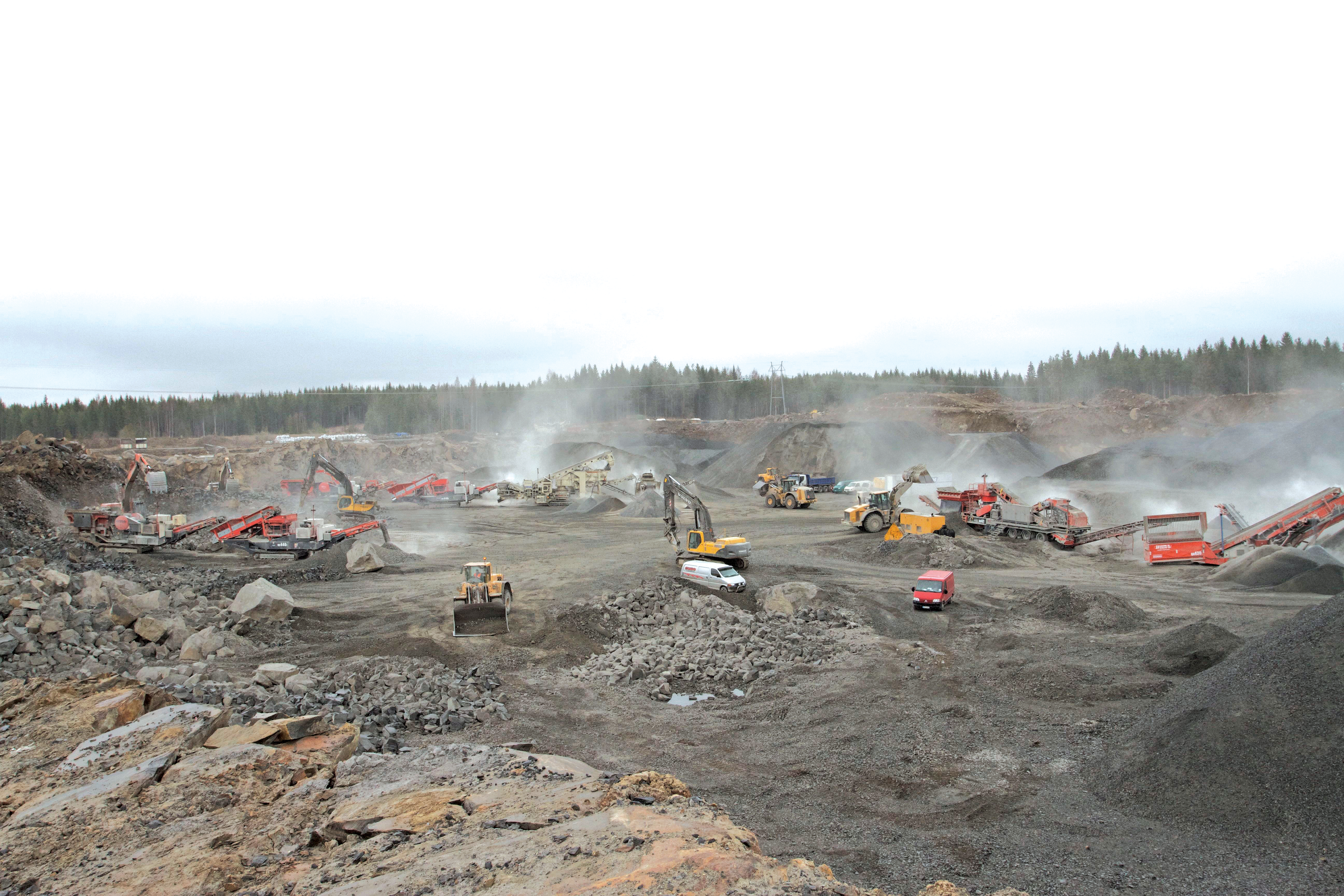
NCC Roads’ Marjamäki aggregate production site located in Lempäälä, Finland, saw a high-powered rock processing operation when two companies, JJ Kaivin ja Kallio and Veljekset Mäkitalo, established their crushing operations side-by-side.
The two companies operate comparable
The
“It takes quite a fortune-teller to accurately forecast the demand for various products for the long high season,” says Sirpa Oksanen, NCC Roads sales manager.
Thus productivity is essential as the crushing season starts in mid-September, and has to be shut down by the end of April.
NCC Roads contracts crushing and blasting operations at the Marjamäki site to
“Both companies provide quality materials. I needn’t worry about poor quality even though I don’t always have time to oversee the operation in person. Of course we maintain quality control, but the guys have active quality control procedures of their own as well. Customers are happy with the product quality. We haven’t had a single complaint about gritting aggregate last winter, for example,” says Oksanen.
Of the aggregate production lines, the Mäkitalo crushing line is laid out in a traditional way as a single chain of units.
“We have three stages, one after the other, and a screen at the end. This way we get a finished product in one go,” explains Mikko Mäkitalo of Veljekset Mäkitalo.
JJ Kaivin ja Kallio has a similar three-stage plant, with the primary and secondary crushers in succession discharging the 0–90mm fraction into a stockpile. From there the fraction is transferred for further processing in a tertiary unit, and then to a screening unit. “This way the front end can always run at full capacity, and any disruption there won’t affect the capacity in the back end because we have buffer storage in between,” says Jarno Virtanen from JJ Kaivin ja Kallio.
“At this site, it’s also an advantage that some 0–90mm fraction goes to the sellable goods stockpile, and this is achieved without any changes. If you’re making traditional fraction, the traditional solution is just fine.”
Veljekset Mäkitalo uses six crushing plants, including a set-up comprising a Sandvik UJ440i jaw crusher in a primary capacity for most of the year, and a Sandvik US440i cone crusher as the secondary unit for about two months. To facilitate a trouble-free production process Mäkitalo places emphasis on preventative maintenance to ensure the crushing fleet is kept in top condition. The frequent turning over of crusher jaws has positively affected the service life, with the swing jaw on the Sandvik UJ440i having processed 450,000tonnes and the fixed one 200,000tonnes of aggregate.
Pekka Jauhiainen, Sandvik Construction sales manager, points out that the average life of a fixed jaw is around 150,000tonnes and that of a swing jaw less than 300,000tonnes, meaning Mäkitalo has increased the service life of the jaws roughly 50% simply by paying attention to them.
The other contractor, JJ Kaivin ja Kallio, also has a long history of using Sandvik equipment, and has enjoyed highly impressive rates of production, especially at the Talvivaara mine. Here it acted as a sub-contractor for Veljekset Mäkitalo, and utilised a Sandvik UJ440i jaw crusher in a primary capacity. Since commissioning in June 2008 it had crushed crushed 4.3 million of tonnes of rock up to 2012.
“We have had good and seamless cooperation with Mäkitalo. If one of the companies has a spare part that the other needs, it will certainly be made available to avoid any downtime,” says Jarno Virtanen. “We cooperate in many other ways as well.”
Mäkitalo agrees that the cooperation between the companies is fruitful.
“This sort of thing will become more common because it’s a good way to speed up the work. It’s a modern approach and takes us in a good direction by benefiting both the customer and us. This way small contractors can achieve better results and cooperation also makes it easier to comply with strict permit terms.
“We think the same way, aiming for high-quality products while respecting the environment and emphasising maintenance.”
The relationship between the two contractors ensures that productivity is maximised, thereby ensuring that NCC Roads and its customer’s needs are fulfilled. Through acting in partnership, by implementing policies of proactive quality control as well as preventative maintenance, and through the use of advanced mobile crushing technology from Sandvik Construction, the required aggregate production has been achieved before the long summer shut down, thereby facilitating a ready supply of high quality construction materials. RSS