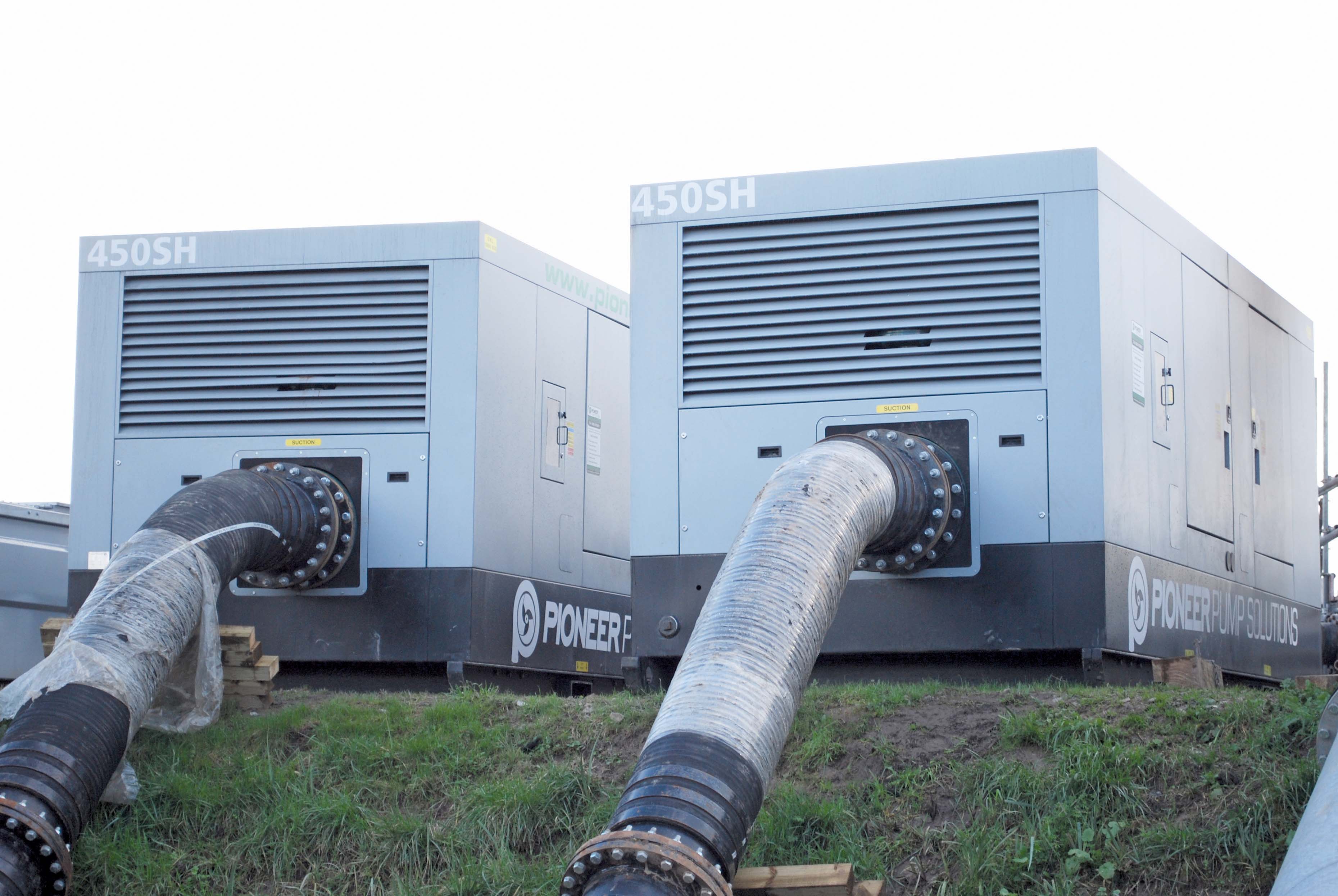
Most mining, quarry and industrial operations worldwide require some form of dewatering system to keep their operations moving. As water becomes even scarcer, the precious resource is often being used, cleaned, and recycled, says Weir Minerals.
Indeed, the company supplied equipment used by Holme Sand and Ballast’s Masters Quarry near Wareham, County Dorset, England, that produces around 200,000tonnes of sand with a small amount of gravel each year for a diverse range of applications.
The company decided to upgrade the quarry’s sand processing plant in order to increase capacity, efficiency and reliability, a task given to a related company, Holme Mineral Processing (HMP), which contracted
Essential challenges at the site are ensuring the cleanliness and purity of the sand and achieving accurate grading of two products: the coarser of the two contains particles between 5mm-500 microns while the finer grade contains 500micron-75micron particles.
The system specified included a Warman SJ submersible pump on floatation unit; electrically-driven centrifugal Warman WGR slurry pumps; Enduron vibrating dewatering screens fitted with silt-return arrangement and including screen underflow pipework, supporting structure and supports; Cavex Hydrocyclone; Enduron Sizing Screen, and T Type Classifier and Dense Medium Separator. To transport the sand slurry between each piece of equipment, heavy-duty
To achieve a marketable product, the lignite content and other unwanted materials have to be reduced to less than 0.5% by weight and Holme specified a maximum lignite content of 0.3% by weight.
The wide range of end products in the Holme range is produced by accurately blending the clean, classified coarse and fine products in different ratios using a bespoke touch screen programmable logic control system designed and installed by Weir Minerals. The feed to the dewatering screen is controlled by Linatex-lined flow-control valves linked to density transmitters in the classification units that can be adjusted depending on feed material being supplied and grading of end products required.
In order to ensure reliability, maximise the wear life of parts and minimise down-time, the Warman WGR and AH centrifugal slurry pumps supplied with the plant are equipped with the upgraded WRT impeller and throat bush combination, which features an advanced computer modelled hydraulic design to reduce turbulence and wear.
The Cavex Hydrocyclone can be adjusted to classify particles according to their density very accurately, which allows the lower-density lignite particles to be separated from the sand with a high level of effectiveness. Weir Minerals has guaranteed that the units will deliver lignite content in the final washed sand products of less than 0.04%, seven times less than Holme’s requirements.
The additional capacity delivered by the new plant has allowed Holme to increase production at the quarry to over 150tonnes/hour, theoretically giving a maximum sand production capacity of over 300,000tonnes/year if required.
As well as processing sand and gravel quarried at the site, Holme also uses the plant to recycle sand. While this currently accounts for only a small proportion of production, the company is aiming to increase it to around 40% in the years ahead.
“We worked closely with the site team at Holme from initial design and specifications right though to installation and testing to ensure the system would deliver on every goal,” says Ron Blazer, process design manager at Weir Minerals Europe.
Atlas Copco says it has increased its commitment to dewatering solutions by appointing Per Rehn as vice president for business development pumps for the Portable Energy Division, a position created to enable
“Along with compressors, generators and light towers, pumps is one of the pillars of our Portable Energy Division,” says Norbert Paprocki, president of the division.
“The creation of the vice president role to focus exclusively on pumps shows the value we attach to the segment and the opportunities we see for growth in this exciting sector.”
“The recent launch of the PAS diesel driven pumps is just one example of how we intend to lead the industry.”
Indeed, the company’s significant expansion of its dewatering pump solutions includes the introduction of a new range of diesel-driven portable pumps, the 4, 6 and 8 inch (10cm/15.25cm/20.3cm) dry-prime units, PAS 4, PAS 6 and PAS 8.
The company already offers electric, pneumatic and hydraulic submersible pumps, and the new diesel-driven pumps extend its dewatering pump solutions for tough environments or where power is not available.
Atlas Copco says the pumps are best suited for transporting or lifting water with abrasive solids in suspension with applications including dewatering at construction and mine sites, floodwater or stream diversions and sewage bypass for industries and municipals.
The PAS 4, PAS 6 and PAS 8 have an operating flow range of 50-600m³/hour with a maximum head of up to 37m. Their solids handling capacity reaches up to 76mm.
The Atlas Copco PAS come with a skid fuel tank that allows the pumps to run for days without refuelling, while the “straightforward design and basic controller module ensure easy operation.”
Meanwhile,
As flash flooding, tidal surges and storms wreaked havoc across the UK, the British government’s Environment Agency enlisted
Initially three pumps fitted with Volvo Penta’s TAD943VE Tier 3 engines were dispatched to help control flooding in some of the UK’s most affected areas, but the pumps were so quick and efficient at containing urban water damage that Pioneer Pump was asked to send its entire fleet of Volvo Penta-powered units to assist the Environment Agency.
In County Somerset, south-west England, Pioneer Pump mobilised its largest 450mm high-flow pump sets, installed with Volvo Penta’s 16litre TAD1643VE engines. By increasing the engine’s size and capabilities, the number of pumps required could be decreased.
“One pump fitted with a Volvo Penta 16litre engine can move over 3,600m³ of flood water per hour. Bigger engines and bigger pumps require fewer trucks for hauling, which in turn reduces the environmental footprint,” says Simon Ruffles, Pioneer Pump’s managing director, EMEA.
Global water technology company
“With our Field Smart Technology customers can monitor the operation of a pump that is located anywhere in the world,” says Dave Boucher, product manager with Xylem.
“Information about an engine’s and pump’s operating conditions, running temperature, oil level and pump suction for example, can all be relayed via this telemetry system.
“Data is collected at one minute intervals and transmitted to a password-protected website which customers can view on their laptop, tablet or smartphone.”
Smart Technology offers customers additional security as it enables them to turn off and lock a pump located anywhere in the world. A built-in alarm system warns operators of faults in a pump, which means that when an engineer is going to fix the problem they know exactly what equipment to use.
Xylem has also recently shown off its range of
Meanwhile, Selwood has redesigned its new S300 solids handling pump as part of an ongoing strategic pump development programme, which has seen the successful introduction of a new family of high head dewatering pumps from 100mm-200mm.
“We are very excited about launching the S300 high head pump. Selwood has committed to designing and manufacturing a new world class range of high and medium head pumps. The new S300 offers dramatically improved hydraulic efficiency, flow and head with excellent suction characteristics,” says Mark Page, sales and manufacturing director of Selwood.
The high head pump is powered by a Stage III/Tier 4 Interim-compliant
Japanese pump manufacturer,
Tsurumi’s LH4110W pump from its LH-W range and the GSZ-75-4L pump from its GSZ range were released earlier this year. The LH4110W high head submersible pump features the largest pumping head in the Tsurumi Europe range and can pump water up to a maximum head of 218m with a maximum capacity of 2m3/minute, while the GSZ-75-4L submersible dewatering pump features the biggest pumping capacity in Tsurumi Europe’s range with the maximum volume of 17.6m3/minute. It pumps over a delivery head of 38m and has 75kW motor output.