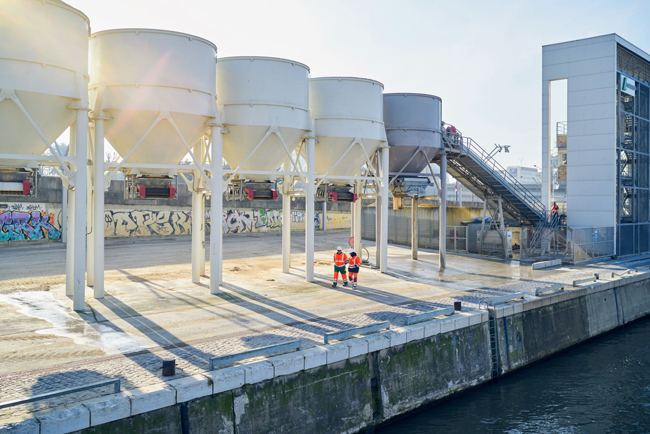
French aggregates demand has grown significantly in the last two years, fuelled partly by high-profile infrastructure projects. Guy Woodford reports
The Grand Paris Express (GPE) project is the largest transport infrastructure project in Europe and represents a total investment of about €38.5bn. It is designed to meet the growing city’s needs for an improved transport infrastructure and prepare Paris for the 2024 Olympic Games.
LafargeHolcim says it will be using barges on the Seine to sustainably manage excavated earth equal to six times the weight of the Burj Khalifa in Dubai, the tallest building in the world. The company plans to work on the GPE project over the next 15 years.
To meet the project’s challenging schedule, LafargeHolcim has added mobile ready-mixed concrete plants to its existing Parisian ready-mix concrete network, enabling an average production of 300m³/hour for the GPE. In addition, the company will remove and treat at least three million tonnes of earth from the construction site, then use the excavated material to re-landscape its nearby quarries.
For the transport of both aggregates coming from nearby quarries situated in the Seine valley and the excavated earth, LafargeHolcim will use barges on the Seine river. The company says this solution is more efficient and sustainable than road transportation as two barges can handle the load of 220 trucks. It adds that the solution will also meet the challenge of transporting large amounts of material through an urban area with over seven million inhabitants.
The GPE is one of several infrastructure megaprojects aiding recovery of French aggregates demand. Others include EuropaCity, a €3.03bn 800,000m² cultural, recreational and retail development in the Triangle de Gonesse in Ile-de-France, north of Paris, due to be completed in 2024, and the latest €893mn works in La Défense, Paris’s central business district, which includes modernisation, refurbishment and greener landscaping schemes.
Nouredine Arkhouch,
According to the latest available
François Wintergerst, director, Sales and Service operations for
Like aggregates demand, cement consumption in France is also rising. It rose 2.5% in 2018 to 18.6 million tonnes, despite just 0.2% growth in the first half and a fall in the housing construction market. This does represent a slowdown from 2017, which recorded a 4.5% increase in cement consumption. Cement imports in 2018 remained stable at 15% of sales. In 2019, cement consumption is expected to remain stable due to the growth in public works and the tertiary real estate market. There are 29 cement works in France with 5,000 employees and LafargeHolcim leads the market with eight cement plants.
The French earthmoving equipment market – the third biggest in Europe - increased by more than 3% last year - the best year since the market crash of 2008.
Heavy earthmoving equipment is up 8.6% to 5,100 machines, according to data compiled by CISMA, a member of France’s Federation of Mechanical Engineering Industries (FIM).
However, the increase is much lower for compact equipment, just 2% over the 2017 figure in 2018. Sales reached 17,250 machines in France, Europe’s third-largest market for such equipment.
For crawler excavators, the market remained stable in 2018 compared to 2017.
Mini excavators, which account for 73% of the total crawler excavator market, posted a slight decline of 2%. The decrease is explained by a 15% decline in sales to renters. Nonetheless, the mini excavator market is close to historical record levels.
The market for excavators of more than six tonnes operating weight continued to improve, with a rise of 4%. Meanwhile, sales of six-12tonne excavators dipped by 1% but sales of crawler excavators over 12tonnes jumped 7% to 2,377 units.
Several yellow iron and crushing and screening plant manufacturers have been investing significantly in their French production sites in recent years. For example, Liebherr-France SAS has invested €5mn in a new state-of-the-art assembly line in Colmar. Based on the principles of lean management, the main task of the new line is to produce the latest generation of Liebherr crawler excavators, which launched on the market worldwide earlier this year as the ‘Generation 8’. The product line consists of the R 922, R 924, R 926, R 930, R 934, R 938 and R 945 models.
With logistical means that are said to be optimally geared to production, the new assembly line achieves average cycle times of 155 minutes per station with an output of five excavators each day. Altogether, the ‘R3’ assembly line has 26 work stations and nine preassembly stations synchronised with the main line.
With a workforce of over 1500 employees and annual production of 2000 machines, Liebherr-France SAS in Colmar is the main production location for earthmoving crawler excavators in the Liebherr Group. The standard production range comprises around 30 crawler excavator models, from the R 914 Compact to the R 980 SME for earthmoving work and for use in mining.
German tracked mobile crushing and screening plant manufacturer
Other major global quarrying plant makers have recently made changes to their French distributor network.
Since 1 April 2019, Bergerat Monnoyeur (BM) has operated as
BM is not only supplying a comprehensive range of Sandvik mobile crushing and screening equipment but will also be providing spare parts and full aftermarket service. This move, says Sandvik MRT, will benefit customers in France by offering consolidated, more localised and customer-focused support in their area.
With over 100 years’ experience in the industry, BM is an established and reputable name with a strong footprint for the supply of heavy equipment in France. With its headquarters in Saint-Denis, BM has six branches and 38 workshops altogether throughout France.
SAMI TP is Metso’s new distributor of mobile crushing and screening products and related wear and spare parts and services for the aggregates market in northern and western France, including Brittany, Normandy and Aquitaine, as well as the Paris area and Grand Est.
A subsidiary of BPM Group, SAMI TP specialises in the sale, rental, financing and repair of construction equipment. With eight main locations and a turnover of €52mn in 2018, SAMI TP is mainly active in the excavation and earthworks industries.
Meanwhile,
Eric Gueguen, Tipmat president, met with Terex president and CEO, John Garrison, at the bauma 2019 exhibition in Munich, Germany (8-14 April) to formerly sign their distribution contract.
French demand for recycled aggregates is also rising, according to Metso France’s Wintergerst, with much of it being channelled into the Grand Paris Express project. “Buildings will need to be demolished before new infrastructure can be installed. Metso is participating in this with its powerful impact crusher installations. able to crush old concrete and separate it to recover the most valuable fractions.”
HCME’s Arkhouch says other projects increasing the use of recycled aggregates include the Mure, Improvmure, Recybeton, and Ecoreb projects. Currently, Arkhouch says annual French recycled aggregates demand is just over 120 million tonnes. “Road construction majors like Colas and Eiffage sort extracted material on site with mobile equipment and use it for the same project.”
Speaking about the growing environment protection-focused working regulations within the French aggregates sector, Metso’s Wintergerst says: “The rules for the working conditions, including noise, dust and safety, in quarry installations are strict and getting stricter. Metso’s equipment and installations are designed based on the best standards. Metso participates and follows closely the work done by the various environmental committees at a French and wider European level. This means we can bring our knowledge to the committees and apply the latest regulations to our own plant designs.”
On the same subject, Davy Guillemard, president of Volvo CE France, adds: “French quarry regulations are becoming increasingly restrictive. For each quarry, the environmental impact is analysed by the French authorities. Lots of things fall within the scope of the environmental quarries’ impact like flora and fauna protection, water protection, water recycling, noise and vibrations reduction, dust, sludge recycling etc. Similarly, the end of quarrying must be integrated from the beginning to anticipate the redevelopment of the site. In France, the average time to obtain the licence to open or extend a quarry is between five and 10 years.”