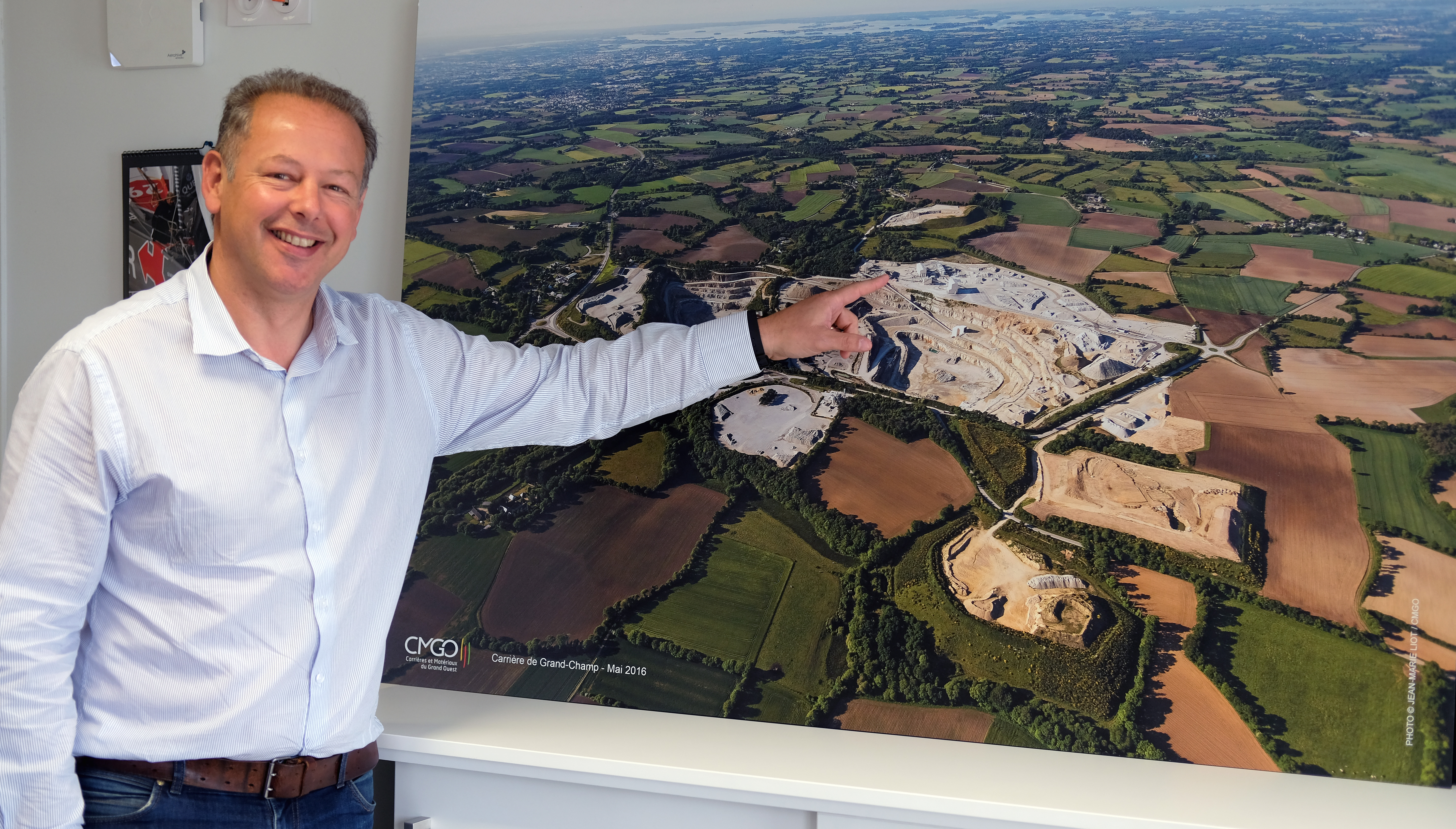
Savvy automation is at the heart of the new complete plant solution designed and installed by Metso for CMGO (Colas) at the French firm’s Grand-Champ quarry near Vannes in Brittany. Guy Woodford went onsite to see the ambitious project in action.
Named CLARA after the granddaughter of the former site manager of CMGO Lotodé quarries, the bespoke
The impressive site’s all-Metso equipment line-up comprises a VF866 feeder, C160 jaw crusher, a HP500 secondary cone crusher, two HP6 tertiary cone crushers, and a number of vibrating screens: CVB2661-3P, CVB2050-3, CVB266, two TS4.3 and three TS5.3 models.
A key part of Metso’s showpiece installation at Grand-Champ quarry is the site’s prototype automated truck loading system developed in collaboration with CMGO. With the system, each truck driver entering the quarry specifies the product/blend range and quantity he wants to deliver to the final customer. The weigh-bridge operator processes this information onto a swipe card which is given to the truck driver. The driver then goes to the truck loading station, guided by ground markings and a big digital display. Arriving at the loading entry gate, the driver stops in front of an interactive terminal and follows the instructions given by the touchscreen, passing his card onto a swipe card reader. While doing this, the trailer is scanned via specific sensors. This allows for the checking of whether the volume of material requested can fit the trailer; and for the measuring of the length, width and height of the trailer to ensure correct material distribution over its length, delivering optimum loading. The loading entry gate then opens and the truck comes into the loading area. The driver is guided by traffic lights and once he stops, the shuttle conveyors load the trailer automatically. After loading is completed, the light goes green and the truck comes out of the truck loading station and goes to the exit weighbridge where the truck is weighed as a final check before leaving the quarry. This further weighing makes sure the truck remains within legal highway weight limits, while also triggering the invoice process.
Another key automation tool within Metso’s process design at the Grand-Champ quarry is VisioRock. It uses cameras, including some on the conveyors belts, and a sophisticated software package to monitor the site’s secondary cone crushers’ performance and relay the information back to the quarry’s central control room, where an operator monitoring the VisioRock cameras and software performance data can quickly act to fix any production problems. VisioRock is set to be installed on Grand-Champ’s tertiary crushers later this year – which will be the first use of the system on a tertiary crusher globally.
Metso says VisioRock allows for five quality controls to be carried out each second, guaranteeing product quality and size before ensiling, and the right final end product mix for the client. It also, crucially, stops oversized material entering a silo, and allows for thorough analysis of screen media, allowing for better scheduling of maintenance.
The plant automation set-up at Grand-Champ quarry, which also includes fully automated regulation of feed to the hopper, has been warmly welcomed by Médéric d’Aubert, sites manager for CMGO Brittany South. “The automated plant is more efficient. The crushing is far more energy-efficient, there’s a lot less downtime and the final product is more consistent in its high quality. The plant is also easier to maintain and improves worker and site safety, as we need less staff onsite.”
So comprehensive is Metso’s automated plant solution, Grand-Champ quarry is only operated by two CMGO employees, significantly reducing wage costs.
Another crucial advantage of the new plant for d’Aubert has been its reduced noise during the quarry’s 12 hours-a-day Monday to Friday operating hours. This is said to have been widely welcomed by the quarry’s neighbours and is key to CMGO being allowed by local authorities to obtain a license to operate at Grand-Champ quarry.
“Local regulation imposes noise and dust level limits. And on this we commissioned a detailed site study by a specific environmental company,” explains Vincent Celsi, sales support manager – aggregates business line at Metso France. “After this, we put a double layer of cladding on the outside of some of the quarry buildings. This modified the sound and the direction of emissions.”
Grand-Champ quarry uses LYSAIR products to supress dust generated during working hours. And adding to its impressive green credentials is the quarry’s closed circuit water treatment facility – enabling 100% water recycling. Furthermore, d’Aubert proudly shows photographs of how each fully quarried section of Grand-Champ is being gradually returned to nature, with a sustainable development programmes in place to protect birds, bees, frogs and other indigenous species. With another 40 years of aggregates reserves at Grand-Champ, such nature-minded operation will, says d’Aubert, “remain a key onsite focus for CMGO”.
During the erection of the complete plant at Grand-Champ, d’Aubert and his team were able to use a temporary Metso material processing plant alongside their existing proven plant. This, he says, was key to avoiding any disruption to day-to-day business. Working only with one partner, Metso, on such a grand project also, d’Aubert believes, helped with its successful delivery. This included 155,000 hours of work without incident during its assembly.
All of the mylonite granite material at Grand-Champ quarry is won initially by blasting, with rock drills used to reduce the material’s size prior to being loaded by excavators and wheeled loaders onto a mixed
The quarry also produces manufactured sand out of -4mm or -2mm fines for use by general construction customers.
This product is stored on the ground via a stacker conveyor belt and is then directly delivered to customers by truck.
A strong focus on plant maintenance is inherent to Metso’s process design in order to drive down overall production costs is apparent during a tour of Grand-Champ quarry.
Having a large wear parts stock onsite, reducing costly downtime, is part of this, but a general reduction in the size of the new plant – one jaw crusher and three cone crushers, compared to the previous one jaw crusher and nine cone crushers – is also greatly helping to reduce maintenance needs. Rubber panels equipped with ceramic pastilles are also being used to monitor the installation’s crusher wear and friction points.
“Our job is to produce without stops at the lowest cost per tonne. We have one or often two replacements of each machine wear part per month onsite,” explains d’Aubert. “This plant is a new production tool so we are learning quickly about how much replacement stock we need. We expect Metso to be as reactive as they can be when we don’t have a part in stock.”
Overall, d’Aubert and his management team at CMGO Brittany South say they are extremely proud of this flagship plant project – CMGO (