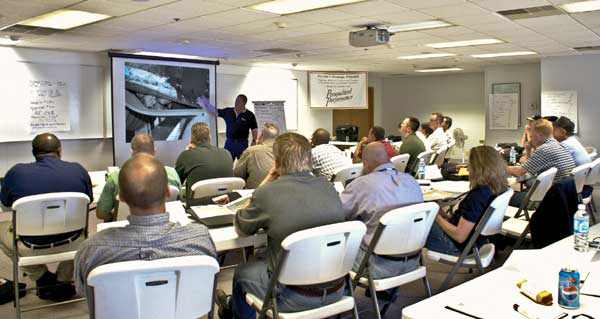
Investment in conveyor systems is helping some quarries to improve productivity and reduce operating costs. Claire Symes reports
With the need for more fixed operating costs, many quarries are turning to conveyors as a hauling option in place of using a fleet of dump trucks. According to the conveyor manufacturers, they can offer a more environmentally friendly and cheaper option in the long term.
Both fixed and mobile conveyor technology has evolved to offer better capacities, greater material retention and lower maintenance demands. This, combined with the ability to forecast operating costs, has convinced a number of quarries to opt for conveyors despite the squeeze on capital investment.
Fixed returns
Hanson needed to transport material over large distances and development of a new reserve at Must Farm meant expansion of the conveyor system was needed. Clay reserves at Must Farm are overlain by 1 to 2m of sand and gravel, which Hanson had consent to extract for aggregates, so needed a conveyor system to transport both feed materials.
Continental's solution involved two separate systems - a 400tonne per hour conveyor for the sand and gravel and a 600tonne per hour system for the clay deposits, which featured sprung rollers to maximise containment. The conveyors also had to cross a railway line using an existing bridge structure and Continental overcame the space constraints here by running the conveyors one above the other. The conveyors also cross local roads before reaching the brick plants and cover a total distance of 4km.
The other issue for Hanson was the limited working time that was consented for Must Farm but the need to supply the brick plants with material 24 hours a day. To resolve this, Continental split the clay supply into two lines so that half could be used for immediate production and the rest stored undercover to create a stockpile for overnight.
Stockpile solutions
While Continental's solution for Hanson's Must Farm development helped the company to transport material over a number of fixed barriers that would have prevented hauling by truck, conveyors can also offer a good solution for stockpiling.
Before the deciding to buy the Telestack system, Alluminsil was using a small tracked stockpiling conveyor to stockpile the material. As there was no radial function on the conveyor, the stockpile capacity was minimal and the material was suffering from segregation, degradation and compaction. Also, the company had to move the whole plant to stockpile the material in specific areas of the site.
According to Telestack, since the purchase of the TS 542 the quarry has identified increased production capacities throughout the site. The material is currently being loaded directly into the screen, which feeds the conveyor. The gypsum material is then being stockpiled in windrows using the automatic radial function of the TS 542. The automatic stockpiling program installed as an optional extra allows the machine to stockpile up to 270 degrees automatically with no intervention.
Alluminsil is able to stockpile up to 79,589tonnes from one source point which Telestack has said saves production time and fuel costs as there is minimal movement needed on site. "This also eliminates the need for operators in this process as it is a fully automatic system," said the company. "The unit also includes a crawler tracked dolly unit c/w integrated diesel engine, this allows the operator to easily move the unit around the site easily depending on the stockpiling requirements." Northern Ireland-based
According to Continental managing director Alistair Forsyth, the growth in demand is partly due to the mobility of the equipment. "All our products containerise which helps keep the shipping cost down - all track products ship without any breakdown which is a significant advantage in the set up of our products," he said.
Maintenance matters
Regular maintenance is a key element in achieving the lower cost potential of conveyors and
Martin has said that its Foundations Workshop series has been teaching bulk-materials handling personnel how to operate and maintain clean and safe belt conveyors for nearly 20 years but the company thinks that more quarries could benefit from a better understanding.
Level one involves a fundamental introduction to belt conveyors, components and safety considerations. This level is designed for newly-hired employees or those with little experience around conveyors. Level two includes an in-depth look at methods to improve the safety, performance and payback of belt conveyors by controlling fugitive material and improving system efficiency. The top level is focused on the improvement of belt conveyor systems, demonstrating the justification for investment in solutions to reduce fugitive material, maximise production and extend component life.
This seminar is developed for engineers and managers responsible for the design and administration of belt conveyor systems.
It is clear that there are conveyor options for almost any quarry - it is just a case of finding the right solution to provide long distance hauling, material transfer or stockpiling. Design improvements and wider availability of training means that the need for maintenance is no longer an issue, the question now is more one of reviewing the investment cost in context with operational costs.