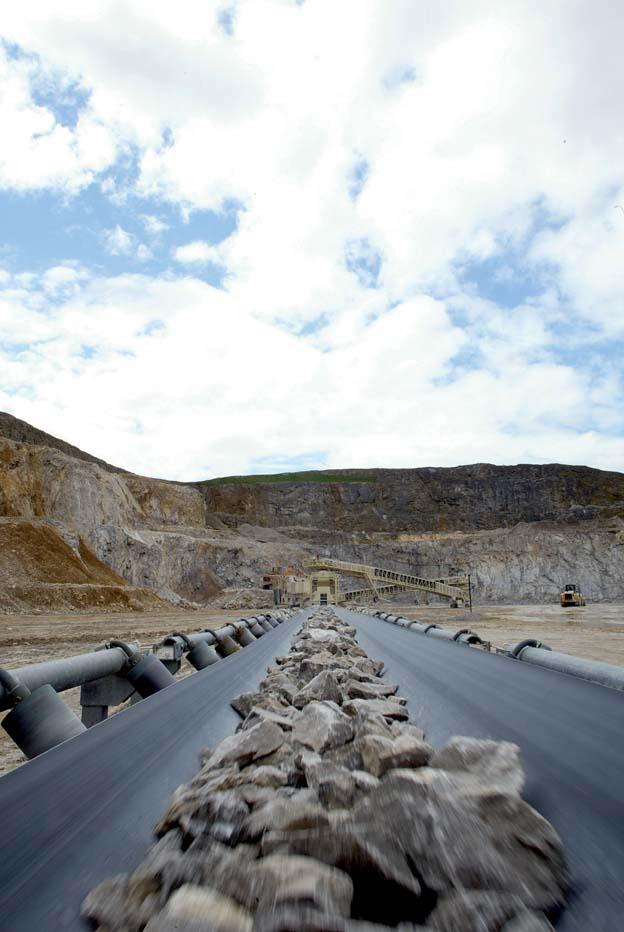
In just eight years Tarmac has turned its Swinden Quarry operation around and gained full public support that has recently helped it gain approval for expansion. Claire Symes visited the Yorkshire quarry to find out more
Gaining permission to extend a quarry is the Holy Grail for many quarry operators but to achieve that inside a national park is almost impossible. Nonetheless,
The site has recently gained planning approval to extract a further 24million tonnes from the site, which guarantees its future until 2030 along with 110 local jobs. But reaching this landmark decision has not been an easy task and it is one that has been taken on at a personal level by the quarry's employees.
Speaking to Swinden unit manager Brian Lockey and zone manager Phil Dukes, who is also responsible for two other quarries in the area, it is clear that they are passionate about improving things at the quarry.
Lockey has worked almost continuously at the quarry for over 30 years during which time he has worked in almost every aspect of the quarry and understands the site's geology and the demands it places on the equipment. Dukes is a more recent recruit to the Swinden site and is not only involved in the day to day running of the quarry but has also taken his role with the community very seriously and is a governor at the local school.
They have every right to be proud of the way the quarry has been turned around since it came under the Tarmac brand too. Before
Long heritage
At the time of ABE's visit to Swinden, maintenance operative Sean Milward was preparing a presentation for Skipton Naturalist Society on the need for quarrying in North Yorkshire, development of Swinden and improvement of the site. Milward's father also worked in the quarrying business which has helped give him a good insight into the development and need for the industry.
According to Milward, the Dales landscape shaped by quarrying and agriculture - the field systems are surrounded by dry stone walls formed from rock that has been quarried locally. sWithout the impact of quarrying and agriculture, it is likely that the area would have more marshland and forest than it does today. The area is also littered with old lime kilns that were used to make lime for the farmers.
The history of quarrying at Swinden dates back to 1793 with work carried out by hand using iron splitting tools and hammers to break the rock and there are still marks from drill steels in some rock outcrops. Later the rock was blasted and then broken to 'foot long' pieces by hand and thrown straight into the kiln before the quarry was mechanised in 1948 with mechanical crushers.
JW Spencer and Son is the earliest company name linked to the site and was bought out in 1965 by the Lime Sand Mortar Group. Later Swinden was owned by Tilling Construction which became Tilcon in 1970.
Today the quarry produces 2.2million tonnes per year of very good quality Carboniferous limestone but the deposit varies through the quarry - soft sections are hard, others soft and abrasive. Material from the quarry is taken away by a combination of customer's on-highway trucks and by the dedicated rail line and is used in concrete manufacture, steel making and road construction.
Redevelopment
"There are 28 people directly employed by the quarry, plus we use contractors for some maintenance and earthmoving work," explained Dukes. "While the workforce may be smaller than in years gone by, the quarry has beneficial impact for thousands of people through the need for landscaping, provision of PPE, the hauliers, and business rates into the local community. We also put something back with funding of local sports clubs and school events.
"There have been some big changes at the site since 2000 - the main one as far as production is concerned was installation of the new crushing and screening plant in 2001. But in terms of visual improvement, the main changes were the removal of the old processing plant and block making facility from the road side location and the entrance to quarry was restored using a mix of quarry waste and paper pulp to create a screening bund that has been planted with 10,000 trees, grassed and landscaped.
"The total value of the investment here was around £16million (€12.7million)." According to Lockey, before the change, the quarry and surrounding area was covered with a layer of white dust and the operation was not supported by the local community. "A nearby caravan site was closed during 2001 during the Foot & Mouth outbreak in the UK and coincided with when the work was being carried out and when the site re-opened a number of previous guests asked if the quarry had closed because of the difference," he said.
The interest and level of support from the local community for the site today is underlined by the arrival of 1500 visitors at the quarry during the last open day in 2007. The change in support has been achieved partly through the investment in change but also through involvement with the community. Today there is a liaison committee to provide a clear communication route, the quarry supports local clubs and host visits by school children from all over the country - children have travelled from as far as Surrey and Scotland to view the site and get an understanding for the quarrying sector. Tarmac has constructed a special viewing platform that allows children to see the operation and remain safe.
Visitors to the site not only learn about the quarrying processes, but are also introduced to the variety of wildlife that exists at Swinden. Like all Tarmac's UK quarries, the site has a biodiversity action plan and any flora or fauna in the quarry is recorded and monitored by the employees. The quarry is home to a number of rare species of birds and Lapwings regularly nest in the restored area of the quarry.
Extraction
Drill and blast is carried out under contract by Ritchies - usually once or twice a week. Blast holes are drilled using an
The quarry is worked on 20m benches that are dictated by the machine fleet at Swinden. The extraction work is currently working at taking the quarry floor from 155m AOD to 135m AOD and it will eventually sink to 120m.
Monitoring of noise and vibration is carried out during blasting but is well within limits, according to Lockey.
Swinden uses a Cat 5130B as its primary mover and the machine is used to load up to 2000tonnes per hour (average of 1200tonnes per hour) directly into the hopper of the mobile crusher. The 240tonne Metso Minerals Norberg LT160 jaw crusher discharges onto field conveyors that are moved as blasting progresses and connect onto fixed conveyors that feed a surge pile. The crusher produces materials from 300mm downwards at a rate of 1200tonnes per hour.
"Use of mobile crusher avoids 1000 dumper movements per day and is much safer as well as significantly reducing fuel and manpower costs," said Lockey. "The quarry used to run 10 40tonne dump trucks with two loading machines. It used to get through 4000litres of fuel per day and produce 8000tonnes of rock. Now the quarry fleet uses 1800 to 2000litres of fuel each day to produce 50% more rock." The main field conveyor is 360m long, formed from a
Swinden has a general policy of enclosing conveyors where ever possible to avoid problems with dust and loss of fines. Floculant is also sprayed onto the surge pile to prevent wind blown dust.
From surge pile the material is conveyed into three feeders - two operate at a time at 500tonnes per hour each to scalp off the 40mm down aggregates. These feed into a Pennsylvania rotary impact crusher and can also feed into a Pennsylvania tertiary crusher depending on current customer orders.
Once in the screen house, material is screened using two triple deck, two double deck and two single deck Don Valley screens into six different grades of material which is dry stored in silos.
From the silos the material is either directly transferred to the rail siding via a conveyor, into the auto wagon loading system that can load a 30tonne truck in around 90seconds or into the 'toast rack' storage from which a wheeled loader can directly load customers wagons. Used for excess material and specialist products - one for extra white fines for fair faced concrete.
Dispatch of the material into the 'toast rack'- which stores up to 1400tonnes of material, road load out unit or the rail sidings is all computer controlled and can be carried out simultaneously.
The road load out unit can process four trucks at time - one loading, one waiting in the bay and the other two preparing for loading. The unit uses RFID tags to ensure trucks are loaded with the correct quantity and type of material. All the trucks are weighed on the way in and way out.
Also in the weigh bridge office is the control unit for the crushing and screening operation along with CCTV to visually check operations in the quarry. The control also checks the power consumption and actual production capacity of the processing plant.
Around 50% of the material is transported by rail to Tarmac's depots at Cross Green in Leeds, Hull, or Dewsbury and also to a Corus steel making plant.
Loading of the rail wagons is all automated and material is taken from the storage ares and over to the rail sidings by another set of covered conveyors. Site has the heaviest shunting locomotives in the country and had to be brought to site in pieces by road and built on site. The train was named Cracoe after the local village by school children at the village school.
The train has 66tonne wagons that can each transport 1800tonnes of aggregate which is the equivalent of 66 road lorries. The have covered top doors.
The quarry usually serves two trains per day but the new plant has capacity to serve four trains per day. The old plant used to take 7 hours to convey a single train, now it takes just two hours so capacity has been significantly increased.
The Cross Green depot was specially designed to receive material from Swinden and can unload a train in just 60 to 75 minutes.
The quarry used to run 24 hours a day because of the cost of shutting down the processing plant but now the site operates 5 days a week. The crushing and screening generally operates 6am to 7pm in the summer and no lorries are allowed to collect material from the site before 6am or after 5pm.
The site has a very good safety record and at the time of ABE's visit to the quarry stood at 8 years and 116 days, so extends back to before the new plant was installed. As well as focusing on safety around the machines, great care is paid to the stability of the rock faces with netting and fencing to prevent rock falls reaching the quarry floor.
Restoration and Expansion
Tarmac received full support for the planning extension at Swinden which will give the quarry access to an additional 24million tonnes of material and extend the life of the quarry to 2030. The extension does not extend the quarry outside of its existing boundary but allows the site to go deeper than previously consented.
Achieving such consent is noteworthy, not just because no public objection was made to the plan, but also because the site lies within the Yorkshire Dales National Park and quarry operations in other similar park areas in the UK has been a contentious issue.
As part of the deal, Tarmac will surrender and restore the nearby Threshfield quarry over the next two years, well ahead of the 2042 permitted end date.
It is planned for the quarry to be restored as a lake once extraction is complete - most of the site is below the water table and relies on a sloped quarry floor and sump pumping to keep it free from standing water.
Water collected by the sump pumping is filtered using stone filters and straw bales along with settlement ponds to remove solids and is the put through reed beds.
Currently the normal pump is broken, so the standby one is being used and another backup unit has been rented just in case the second one fails. Swinden has an automatic system that sends a text message to Lockey's mobile phone if the pump fails, to ensure the secondary unit can be primed and put into action promptly to protect the equipment in the quarry floor, which is valued at around £3million (€3.2million).
As the depth of the quarry increases, Lockey has said that stage pumping will be used to keep the quarry dry. The need for pumping is illustrated by the high flow of water in excavations in the existing quarry floor that have been made as preliminary access to the next bench level. "Work in the quarry is currently focused on extraction that will allow us to reach the extension area," said Lockey. "Further work will also be needed to move old tip areas that were created during the early days of extraction."
Investment
Swinden has already seen significant investment in recent years but Lockey said that some more machines may be needed for the extension and also to move the old quarry tip to access the resources underneath. But currently spare units from other Tarmac quarries and contractors' equipment is being drafted in. Other quarries are suffering from reduced demand but activity at Swinden means that these operators and machines have alternative employment. Swinden has noticed an impact but the efficiency of the quarry means the effect is lessened.