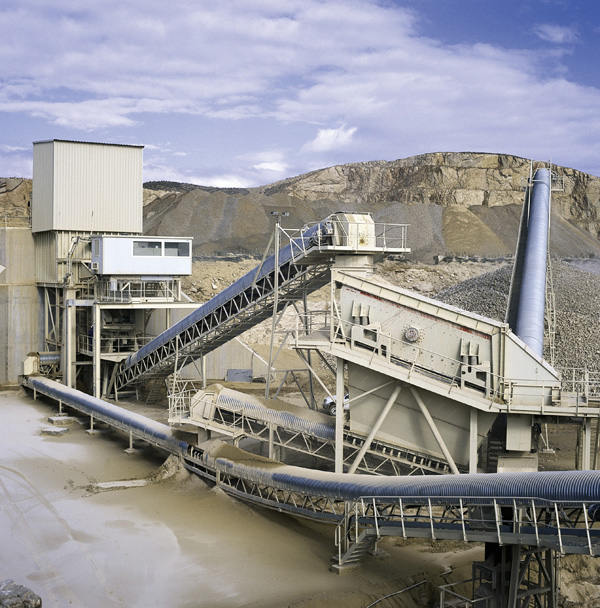
With the price of fuel continuing to rise across Europe, quarry operators are turning to conveyors as a more cost effective hauling option. Claire Symes reports
When
"Our overall aim was to reduce our fuel and electricity bills by 10% between 2006 and 2009," said Heloise Chardigny who has responsibility for Cemex France's energy efficiency programme. "We used four quarries as pilot studies to look at the benefits of different techniques and compared them on the basis of the kilowatt hours saved per tonne." Swapping trucks for conveyors was one of the techniques which Cemex studied at the pilot sites. "The distance between the extraction site and processing site can be several kilometres or more and conveyors have been shown to offer a much more efficient way of transporting aggregates," explained Chardigny. "The saving does vary from site to site, but in general conveyors are around three times more cost effective than trucks for haulage.
"As part of the energy efficiency programme, each of our quarries has developed a specific action plan but we have a policy to introduce conveyors in place of trucks across France." According to Chardigny, Cemex discovered that conveyors offered other advantages in addition to the cost benefits. "Conveyors offered a safer solution for haulage and also helped to reduce noise," she said. "They also reduced reliance on sub-contractors, which helped to minimise overall operational costs." It is these benefits which are helping the €400million conveyor market in Europe to grow at a faster rate than any other quarrying equipment sector, according to
Specifications Renewing conveyors is a long term investment and there is no such thing as an 'off the shelf' conveyor, so specifying the right equipment for the site is essential in order to achieve the maximum available cost and efficiency benefits.
Most conveyors are specified on the basis of delivering a certain tonnage per hour but the product size and material type also need to be considered. However, according to Santos, the two other key criteria are price and safety.
"Conveyors are one of the major causes of accidents and injuries in quarries," said Santos. "The risk of pinches or falls is high, so a lot of innovation in the sector has concentrated on improving the safety aspects. Modern conveyors used in Europe now feature walkways, gang switches, stop switches and mechanical and electrical protection as standard."
Innovation While there has not been much significant development of the actual belts and driving motors in recent years
- although there is always some fine tuning with new models - the main area for advances in conveying technology has been in the way long distance belts are supported.
"Installing a new conveyor used to require a significant amount of civils works to install the supports. Careful planning of the quarry layout for the next phases of extraction to ensure the belt was in the optimum position was also essential," explained Santos. "Now we can create pre-cast concrete supports that do not need to be permanently fixed to the ground. These can not only be moved but also allow the belt to be positioned close to ground level to allow for easier, safer maintenance, and can also be repositioned relatively easily." Modern conveyors often feature sensors to check that the belt is running smoothly and measure the capacity and type of product being conveyed. Some hi-tech conveyors also feature cameras to analyse the product gradation.
A common problem with conveyors, particularly when transporting wet material, is carrying back material on the return belt. This means that production capacity is reduced but can also result in additional dust as material drops off and causes wear to the conveyor motors and bearings.
"We developed a system which turns the belt for the return, so any material still on the belt is retained," said Santos. "We introduced the system a couple of years ago specifically for the crushing and screening market and it has proved to be very popular." Another environmental protection feature that is becoming common on conveyors used in European quarries is the adoption of covers to prevent dust contamination and meet the demands of planning consents. Many new conveyors are specified with covers but there is also a market for retrofitting them on sites where dust has proved to be a problem.
Mobile growth The rising demand for mobile crushing and screening equipment in the European quarrying sector has also triggered an increase in sales of mobile conveyors.
Unlike fixed conveyors, mobile units can be quickly moved from site to site which allows mobile crushing units to be managed by a single operator, by removing the need for a wheeled loader to transfer material from the crusher or screen to the stockpile
"There are two main segments to the mobile conveyor market," explained
"The second market segment for mobile conveyors is for transfer conveyors, which could be used to transfer material from a mobile crusher to a fixed conveyor, or to connect several items of mobile crushing and/or screening plant together." According to Wardell, although mobile conveyors may represent a higher initial outlay than a wheeled loader, the long term effect on the cost per tonne of moving material can be as much as 60% less than it would be with a wheeled loader. "Conveyors are the most cost effective and environmentally friendly method of moving material within a quarry," he said.
"Growth in demand for mobile conveyors can be directly linked to the trend towards use of mobile crushing and screening equipment in Europe. Mobile conveyors give quarry operators more flexibility and are also gaining popularity with contractors too." According to Wardell, one of the strongest markets for mobile conveyors is the Middle East. "There is a real scarcity of skilled operators in the region, so use of mobile conveyors can either cut labour costs or frees up operators for other tasks," he said.
Wardell added that, like fixed conveyors, the needs of the customer have to be carefully matched to the specification of the mobile conveyor. However, mobile conveyors can compete on capacity with fixed units. "We generally sell units with a 350 to 500tonnes/hour capacity into the quarrying market but mobile conveyors can be designed to offer capacities of between 250 to 2500tonnes/hour."
Future development Rising fuel costs means that using conveyors for haulage is likely to become an increasingly financially viable option for European quarries. But Santos believes that the efficiency of conveyors will further improve over the next five years. "New materials now available will enable the belts used to convey aggregates to be advanced," he said. "The next generation of belts will be stronger and lighter, which will reduce energy consumption, adding to the efficiency benefits of conveyors."