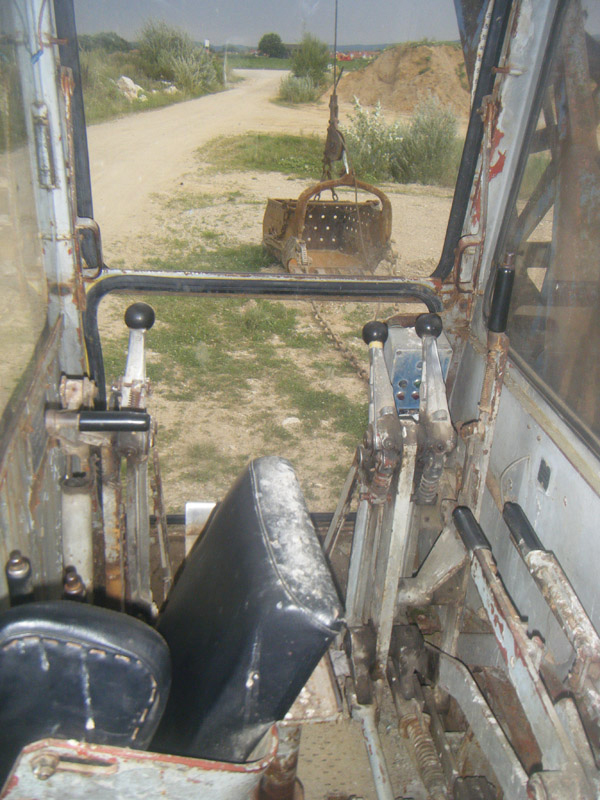
Improving operator comfort is now a common theme on new quarry machines, but that wasn't always the case as Mike Woof explains
Cab design and operator comfort seen on present day machines is being continually improved but it is worth appreciating by just how much the working environment has improved, particularly in the last 20 years.
Sitting in the cab of a piece of heavy equipment built in the 1950s, for example, gives an insight into how much tougher was the job of the older generation of equipment operators. Safety features were unheard of and comforts were basic, where they existed at all. Compared with modern machines that feature air conditioning, power assisted controls and ergonomically-designed cab layouts, older pieces of equipment seem harsh and uncomfortable and sometimes, downright dangerous.
Using old machines was hard work too. Operating a mechanical dragline required the use of various pedals and levers that needed considerable effort to push and pull. Even the early hydraulic excavators of the 1950s and 1960s featured lever type controls that needed a degree of muscle to use, as well as considerable skill (and 'feathering') to ensure accurate operation.
The old generation graders were notorious and nicknamed 'knucklebreakers' by many. This was because the hydraulic control levers had a habit of springing back, cracking the knuckles of any operator unwary enough to leave a hand in the way. Meanwhile the winch and cable-raised blade systems used on many older bulldozers, while effective, could lead to serious injuries in the event of an overstressed cable snapping.
In the early days of mechanised minerals extraction, haul truck drivers had to be content with wooden bench seats and open cabs for the most part. On a cold day, truck drivers made do with a blanket stretched across the knees and a thick overcoat, hat and gloves for warmth and to provide the most basic protection against the elements. Cab heating was unknown at first. Operators had to contend with trucks that featured crude suspension and minimal damping. What these were like to drive for a working day across bumpy and unmade surfaces, while sitting on a hard wooden bench, is hard to imagine.
The Mack AC 'bulldog', one of the most popular trucks used in the extraction industries during the early part of the 20th century featured further hazards for the operator. With its cooling system mounted between the cab and the engine, a cracked radiator could result in the driver being enveloped in a cloud of scalding steam.
Only in recent times have trucks been fitted with power steering. To be able to drive an older machine through a full working shift, an operator needed to have arms like a weightlifter. Hitting a pothole could result in the steering wheel spinning round, possibly breaking the driver's thumb or wrist in the process.
Meanwhile engine vibration transmitted through the steering wheel and gearstick could also result in serious discomfort after a full working day. Quite possibly after a few years of repeated exposure, this would cause painful and crippling long term nerve and capillary damage from vibration white finger.
In terms of safety, braking systems were crude and could be relied upon to just about slow a vehicle down when it was unladen. With a full load, the only thing that could be guaranteed to stop a truck in a hurry was a collision with something large, heavy and solid. As for roll over protection (ROPS) or falling object protection (FOPS), there was none for many years.
In the past, operators were often lucky to finish a shift with a full complement of working digits and limbs, not to mention avoiding more serious injuries. These days, machines are designed to be comfortable, with low-effort joystick controls that are ergonomically designed, plenty of leg room, multi-adjustable air-conditioning, suspended seats, and even a plethora of cup holders and stowage areas for personal items and food. Considering the equipment of the past, present day machine operators have never had it so good.