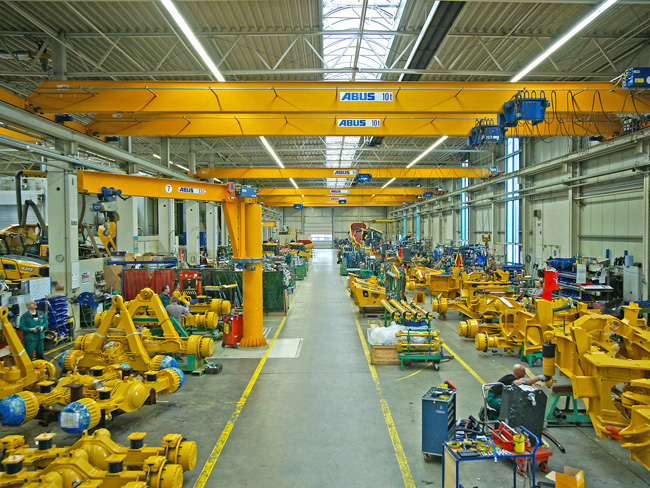
A leading global hauler manufacturer is increasing its European assembly capability, while other leading sector names are bringing new models to key global markets. Guy Woodford & Munesu Shoko report.
Scheduled for completion in mid-2019, the Phase II extension will add two new halls totalling 12,000m² which will treble the available floor space and provide capacity for bin fabrication and future expansion.
The Eisenach factory opened in 2003 as the company’s first production facility outside of South Africa. Bell says the factory offers the best access to its existing established markets in Western Europe and has also proved to be an ideal base from which to provide for the emerging Eastern European markets.
The company adds that the close proximity to its European technology partners and suppliers of drive and control components minimises lead times, improves cost structures and optimises flexibility in terms of production planning.
The original 6,000m² assembly plant was purposefully designed to assemble all Bell Equipment ADT models from the smaller trucks to the giant 50tonne vehicle. It was intended for a maximum output of 20 units per week in a three-shift operation. However, the introduction of the Bell E-series trucks in 2013 led to an increase in demand and a need to escalate production. The result is the current extension of the existing facility, which on completion will provide an 18,000m² structure for production and storage.
The long-term plan for the new factory is the incorporation of more componentry fabrication. Bell says the selection of components to be introduced will be driven by lead times, flexibility and, ultimately, how best to fulfil customer expectations. Bin fabrication will be the first service to be relocated to the site, as most of the high-quality steel used for the bin structures is sourced from European suppliers.
The Cat 740 GC ADT re-introduces the 40ton (36.3tonne)-size class to the Cat articulated hauler range. The new model is designed to incorporate the proven features and performance of models currently in the ADT line-up, including new controls, transmission-protection features, hoist-assist system, advanced traction-control system, stability-assist system, and a fuel-saving ECO mode.
In addition, the 740 GC also incorporates the latest automatic retarder-control system, which requires no input from the operator, resulting in greater operating efficiency. For added control and convenience, the new model also features a “wait brake,” which temporarily applies the service brakes during pauses in the work cycle, reducing operator effort and fatigue. Also, a hill-start system automatically holds the machine on grades, allowing the operator to move from the service brake to the throttle with no roll-back on slopes.
The 740 GC cab features the new ‘external spinal-ROPS’, which is found on other Cat ADTs in the range. This cab incorporates a rear quarter glass that eliminates a structural pillar, resulting in enhanced rear visibility. Also, a ‘wake-up’ feature initiates machine displays when the door is opened. The door itself is lighter and stronger than previous designs and more effectively seals against dust infiltration. The overall cab design results in interior sound levels of 72dB.
Optional infrared glass reduces solar heating inside the cab, and left- and right-hand sliding windows increase ventilation, while also facilitating communication with workers and the loader operator. An automatic climate-control (HVAC) system positions more vents above and behind the operator for increased heating and cooling efficiency. An optional heated/cooled seat provides added adjustments that allow operators to ‘dial in’ personal comfort settings, and the second seat with added cushioning now uses a flip-up/flip-down design to provide additional cab storage.
For added safety, a lighting system, controlled via a ground-level switch, illuminates the cab’s entry steps and hitch area as part of the ‘wake-up’ feature, and optional long-range LED work lights improve overall visibility at night. Optional integrated payload lights provide an external indication of payload levels for the loader operator or site supervisor, helping to ensure proper loading. Exterior features include a redesigned, flexible lower fender and a low-profile exhaust stack that need not be removed for transport.
The optional Cat Connect PAYLOAD technology calculates payload via sensors on the walking-beam suspension and includes load-status lights at all four corners of the cab roof to ensure visibility to the loader operator from any angle. In addition, the standard Cat Detect/Stability-Assist system monitors the working angle of the tractor and body, as well as the grade, and cautions the operator if the machine is approaching a set threshold angle, stopping the dump process if continued action might potentially result in tipping.
Further enhancing safe operation is the Cat Advanced Automatic Traction Control (AATC) system, which features refined technology for proactively applying differential locks to avoid wheel spin.
Following the completion of field operation trials in Austria, the first
While it is ideally suited to the mining sector, Liebherr Africa is also targeting large-scale quarrying operations with the new 100tonne truck. Tom Munch, director mining, says the new rigid hauler arrives at an opportune time for Liebherr Africa. “We are working in a contract mining market. If you look at the type of equipment this group of customers requires currently, it’s mainly 100tonne excavators and 100tonne dump trucks. This is due to the mobility they require, given that their contracts are limited to 3-5 years at most,” says Munch.
Munch adds that Liebherr also urgently needed a truck to complement its excavator range. Designed to carry up to 100tonnes of payload, the T236 can be ideally paired with Liebherr’s R 9100, R 9150, R 9200 or R 9250 mining excavators.
Munch reasons that the T236 is ideally suited for the contract mining market because it speaks directly to lower cost per tonne, increased productivity and safety, three key parameters of sheer significance to contractors, especially in light of the current tight operating conditions.
Mining and quarrying companies have spent many years ruthlessly seeking ways to reduce their operating costs. One of the measures they have implemented is supply chain optimisation. In a bid to control their costs, many have tightened their contractor service level agreements. For example, many mines and quarries have put a fuel cap on each and every contractor’s machine. If a machine exceeds its fuel cap, the extra fuel consumption will be deducted off the mining contractor’s certificate.
Donald Hewitt, national service manager – mining at Liebherr Africa, says probably 60-70% of mining contracts awarded today have a fuel cap. Previously, “wet contracts” had no limit on fuel and contractors were not so concerned by the fuel efficiency of their machines. Today, mining contractors are being forced to rank fuel consumption high up on their buying checklists. With a range of fuel-saving innovations, the T236 will surely address these concerns.
Abie Kriel, technical manager – mining at Liebherr Africa, says the T236 sets a new era by becoming the first truck in the 100tonne segment to utilise a diesel-electric drive system.
Major road infrastructure work is underway in Horokiwi, New Zealand, and Bryce O’Sullivan Contracting (BOSCO) is busy sourcing rock for asphalt at the Horokiwi Quarry with the help of two
Located in the North Island of New Zealand, Wellington is marketed as the ‘coolest little capital in the world’. Millions of tourists travel there every year to enjoy its art galleries, craft beers and night markets. Set back from the hustle and bustle of the city centre is the suburb of Horokiwi. It’s semi-rural, with no schools and only one access road, which comes off the Petone-Wellington motorway.
BOSCO has been based in Horokiwi for some time, helping to renovate the city’s transport infrastructure. It is involved in two of the biggest construction projects in the region – building the Kapiti Expressway and the 27km, four-lane Transmission Gully motorway. With the help of two TA400s, BOSCO is shifting blue rock in Horokiwi Quarry, which is being used as base course and asphalt. Since August 2017, the pair of Terex Trucks articulated haulers has removed 200,000m³ of aggregate and clocked up around 700 hours.
“We’ve got the machines working in tough conditions – but they’re delivering on every level,” says Suds O’Sullivan, who is an employee as well as the company owner’s father. “They’re robust, reliable and our operators say they are simple to operate, too.”