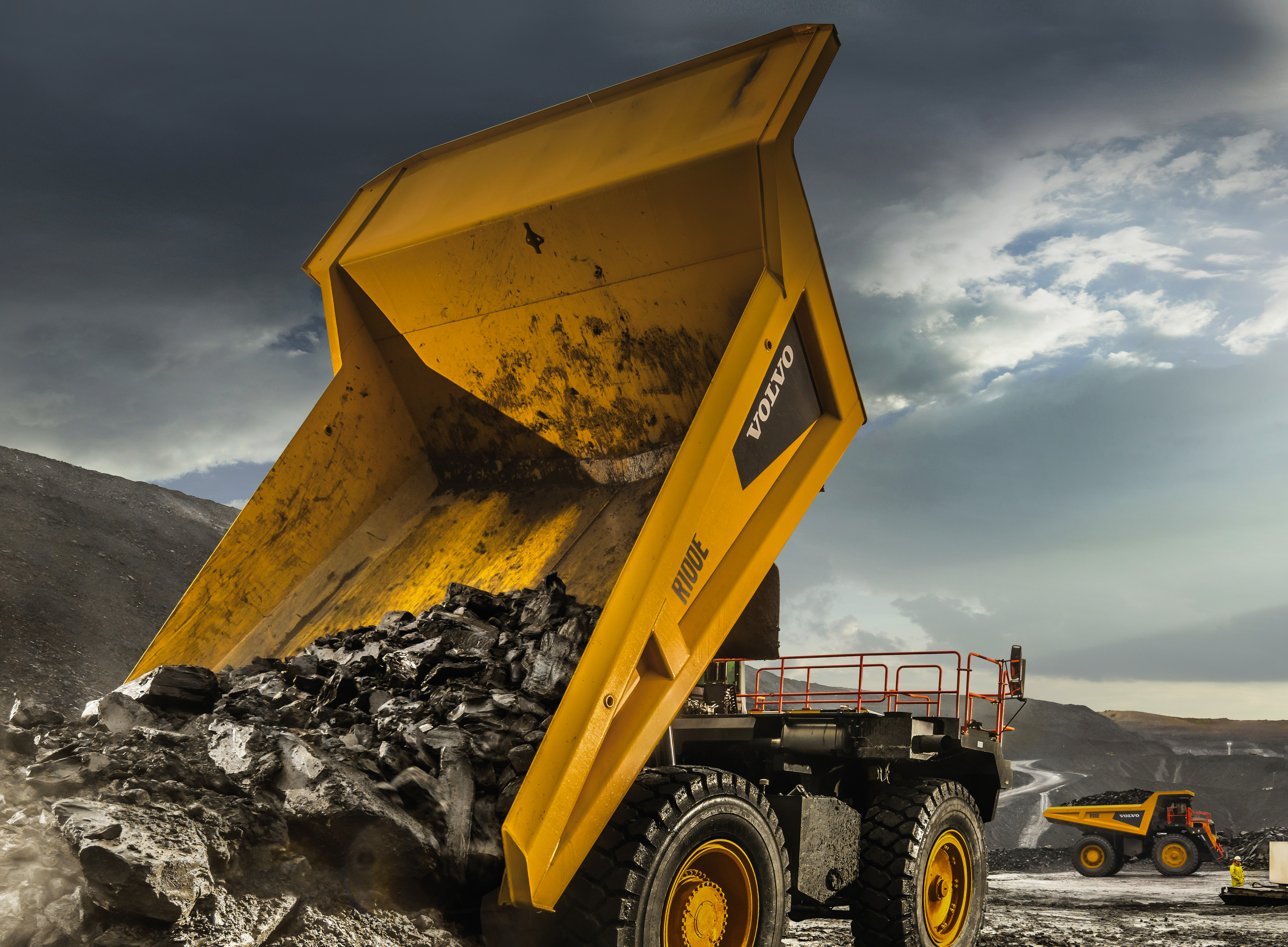
The global hauling market is going through a highly newsworthy period, with a major new player entering the rigid market, and an established articulated hauler OEM launching a highly productive and mobile four-wheel drive model. Guy Woodford reports.
Guests got their first glimpse of the new machines – which consist of the 41tonne (45ton) R45D, 54tonne (60ton) R60D, 65tonne (72ton) R70D and the flagship 95tonne (105ton) R100E – on Tuesday 10 April 2018 as part of a three-day Volvo rigid trucks launch event. The star of the show was the R100E, a completely new rigid hauler said to combine a wealth of market and customer knowledge with proven components, new technologies and a striking new design – all providing a cost-effective and productive solution to fulfil the needs of today’s mining and quarrying customers. The new four-model range is initially available in less regulated markets, with the R70 and R100E also available for sale in the
With a focus on helping customers achieve production targets faster – and using less fuel in the process, Volvo Construction Equipment’s (
As well as having the chance to inspect the new machines, guests at the 9-11 April landmark event also got the opportunity to test drive the all-new flagship R100E, see how the rigid haulers are designed and made and watch them in action at Hillhouse Quarry in Troon, South Ayrshire.
The E-Series R100E is a completely new machine that delivers stability, a long service life, high profitability, durability and comfort. With its high capacity and hauling speeds, new V-shaped body, efficient hydraulics, intelligent monitoring systems and operator environment, Volvo CE demonstrated at Motherwell how the rigid hauler will help customers in the mining and quarrying segments move more material in less time. With this in mind, the R100E is said to have a fastest-in-class tipping time of 24 seconds, 11 seconds in the up cycle, and 13 in the down cycle. Furthermore, the R100E is also said to be quick and simple to operate and maintain.
Based on the existing and well-proven
“It was great to invite customers and dealers to the site where the new Volvo-branded rigid haulers are being manufactured,” says Thomas Bitter, senior vice president of the marketing and product portfolio (MaPP) function at Volvo CE. “We’ve been working on the new range since Volvo CE acquired Terex Trucks in 2014. The development of these machines has relied heavily on the long-standing rigid hauler expertise of Terex Trucks as well as customer input and the technological strength of the Volvo Group.”
A key part of the extensive customer input in the development of the new range of rigid haulers has been their extensive field testing – with very positive results. One such customer is Trollope Mining Services, a contract mining company based in Johannesburg, South Africa, which have tested the R100E for more than 1,000 hours over the past year.
“The Volvo R100E is an impressive design that offers a good balance between productivity, fuel efficiency, comfort, ease of maintenance and safety,” says Sagrys De Villiers, site manager at the Manungu Colliery. “We are sure that this truck will be a strong competitor in the rigid truck market in the future.”
“The R100E is capable of carrying an extra bucket pass compared to other 100 tonne trucks being used on the site,” agrees workshop manager Danie van Niekerk. “This means extra productivity for the mine, which is very valuable. Speed and acceleration of the hauler on inclines compares favourably against competitor machines, even when fully loaded and carrying more material.”
Speaking in a Q&A session with mining and quarrying trade media, Paul Douglas, Volvo CE’s vice president rigid haulers and managing director of Terex Trucks, gave more details of how the R100E is a truly customer-focused truck. “We spent thousands of hours talking to customers and talking to dealers to really understand what they wanted. For example, they wanted to make sure the truck was still relatively simple to maintain and operate. They wanted it to be efficient and productive, but they didn’t want it to have all the bells and whistles that in many of the markets they don’t actually use. The four key messages were low total cost of ownership, operator well-being, productivity, and easy maintenance. The R100E offers all this and represents a total package that differentiates it from others.”
Commenting on the rigorous bench testing of the R100E at Volvo’s Jinan, China, technology centre prior to its launch, Douglas said: “We took the frame, body and all of the suspension cylinders of the truck, overloaded it and put it on a huge vibration test ride machine for 60,000 hours. We used to say with previous trucks that the frame life was 50,000 hours, but it’s now tested to higher payload and overload conditions, and for 10,000 more hours.”
In the same Q&A session, Tomas Kuta, senior vice president of sales at Volvo CE, stressed how the popularity of the R100E rigid truck among customers in lesser regulated markets would be key to the model’s overall global sales. “Traditionally, around 70-80% of sales of 100tonne class rigid dump trucks are to customers in lesser regulated markets. If you look now at, for example, Indonesia, Latin America, Africa and Russia, you will see huge demand for this type of truck.”
Articulated dump truck (ADT) specialist
According to Bell Equipment product marketing manager Tristan du Pisanie, the Bell B30E 4x4 – launched at
While not possessing the extreme off-road capabilities of a 6x6, the B30E 4x4 still offers sound all-weather characteristics on undulating haulage roads and light terrain, and provides better manoeuvrability in confined material handling areas or stock yards. Having one less axle means no tyre scuffing - which results in significantly reduced tyre wear compared to 6x6 applications on hard ground.
The front tyres are typical 23.5R25 tyres whereas the heavier loaded rear axle uses 29.5R25 tyres, commonly found on 40tonne ADTs. With its oscillation joint providing permanent contact of all wheels, and a well-balanced load distribution (empty: 50/50; laden: 33/66), the 21.5tonne Bell B30E 4x4 proves itself far superior to rigid tippers or tractor-trailers at load and dump areas, or in wet conditions.
The new two-axle truck is based on the 6x6 model Bell B30E and shares the front chassis and oscillation/articulation joint. This means that Bell Equipment customers benefit from the 246kW Mercedes-Benz engine, six-gear
With an identical payload to the B30E 6x6 of 28tonnes, the major differences are the shorter rear chassis with a solidly mounted Bell 36tonne axle and the newly designed 18.6m³ bin. Compared to the three-axle ADT, the B30E 4x4’s outer turning circle diameter is 1.3m smaller (14.6m), which makes manoeuvring in narrow loading or tipping spaces easier and faster. The short bin allows optimal loading times for silo discharge or with wheeled loaders, and is also compatible with the more typical excavator loading method.
The most important development is in the suspension of the DA30 which is being upgraded to a hydro-gas self-levelling system to provide outstanding performance and superior shock absorption for better driving comfort, especially when the truck is being driven when it is empty. To complement this, the operator will now benefit from a Grammer Actimo XXL seat in the cab as standard with its own independent low-frequency pneumatic and wide scissors-type suspension.
The Grammer seat is not the only change in the new state-of-the-art operator’s cab on the DA30 which has been redesigned to provide better ergonomics and more operator comfort. The dashboard has a completely new layout and soft-touch material composition that is easier to clean and features a new display as well as a high-quality finish and appearance.
The cab also offers new safety and performance functions with a more comfortable control panel with a power cut-off switch and an LED indication lamp which indicates when it is safe to switch off the power cut-off.
On the outside of the cab, a new all-round hand grip rail has been installed for improved safety for moving round the outside of the machine for cleaning and other tasks. Doosan has also introduced a new position and solution for the power cut-off switch.
Doosan says the new version of the DA30 offers lower running costs than its predecessor. There are a reduced number of service points with fewer different oil types in the driveline and increased intervals for transmission oil change. In addition, the new cab tilting system enables the service technician to lift and close the cab in just a few minutes.
Like all Doosan ADTs, the DA30 features an articulation hinge positioned behind the turning ring to provide equal weight distribution to the front axle even during maximum steer articulation. This together with a free-swinging rear tandem bogie ensures equal distribution of weight to each wheel and guarantees permanent 6-wheel contact and drive for equal power distribution and excellent performance on difficult terrain.
Collectively, the forward turning point, the unique tandem bogie and the sloping rear frame results in claimed best-in-class rough and soft terrain capabilities. This also avoids the need for electronic aids such as traction control.
The claimed best-in-class fuel consumption of Doosan ADTs is down to a combination of features including the
The Doosan DA30 is powered by the Scania DC9 276kW diesel engine, meeting the Stage IV/Tier 4 Final emission regulations through the use of both selective catalytic reduction (SCR) and exhaust gas recirculation (EGR) technologies, with an electronic engine brake system, one of four brake systems on the trucks. Doosan’s Stage IV/Tier 4 Final ADTs do not need a diesel particulate filter (DPF) to meet the emission regulations.