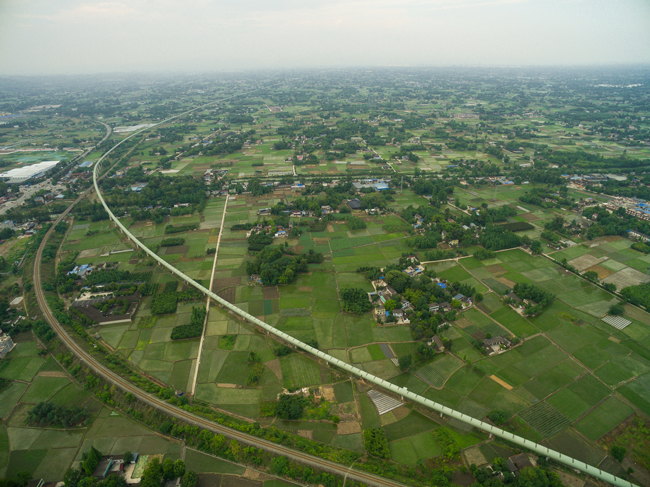
A leading conveyor system company has been talking about two giant conveyor belt projects for a Chinese cement firm. Meanwhile, another top sector player is launching new aggregates processing conveyors and components, while two other manufacturers are opening new state-of-the-art production facilities. Guy Woodford reports.
For nearly a decade, Sichuan Yadong Cement, in Pengzhou, China, has been relying on a 12.5-kilometre overland conveyor from
A traditional Chinese proverb says that the roads in Sichuan are hard, harder than climbing to heaven. Depending on the destination, there are rivers and valleys to be crossed and mountains to overcome. The southwestern Chinese province of Sichuan is the source of the majority of different ores in the country, such as titanium, lithium and silver and plays a major role economically. The electronics, mechanical engineering, metallurgical, chemical, medical, food and building material industries are all pillars of the economy. Located near Chengdu, the capital of Sichuan province, Sichuan Yadong Cement is a well-established regional cement manufacturer. The company is a member of the
In 2004 Sichuan Yadong Cement decided to build a new cement plant in its home province. During the development phase, Asia Cement received approval from the Chinese government to use an abandoned railway to transport the limestone. Halfway through finishing the plant however, the government decided to build a new dam. The area intended for the transport was to be flooded, which would have changed the project conditions considerably: roads would be flooded, and the trucks would have to take significant detours. Asia Cement was also planning on building two additional kiln lines at this location. It was determined, as a time- and cost-efficient alternative, to install a troughed belt conveyor able to navigate horizontal and vertical curves. For this, the company turned to BEUMER. For many years now, Asia Cement has been relying on the system supplier’s expertise and is currently operating several of its bucket elevators.
BEUMER’s Chinese subsidiary, BEUMER Machinery Shanghai, took over the mechanical and electrical engineering, supplying the core components for the overland conveyor and monitoring and commissioning its installation. “Our colleagues were able to work closely with the customer. They know the specific local customs, speak the language and are familiar with the particular market and customer requirements,” said Dr. Andreas Echelmeyer, director of Conveying and Loading Systems at BEUMER.
In May 2006 Asia Cement awarded the contract for the 12.5km-long system. The overland conveyor can reach a mass flow of 1,360tonnes/hour and a conveying speed of four metres/second. “Compared to other conveying solutions, the open troughed belt conveyors are suitable for higher throughputs. Horizontal as well as vertical curve radii are possible,” explains Dr. Echelmeyer. The belt conveyors can be adapted to a specific task and topography. Using its calculation programs, BEUMER could precisely calculate the static and dynamic tractive forces of the belt during the development phase of the system. This is a prerequisite for the safe dimensioning of horizontal curves. The type of drive technology and conveyor belts needed are based on these calculations. This would ensure longevity of the entire system for Sichuan Yadong Cement.
The terrain for the overland conveyor project was hilly and covered with dense bamboo forest, parts of which are listed as a nature reserve. For this reason, the government did not approve a service route nor deforestation. The ground also presented a major challenge for BEUMER engineers. “The ground is unstable due to previous coal mining. In other areas the ground consists mostly of granite that could only be partially removed,” explains Dr. Echelmeyer. Another 1.5km overland conveyor section had to be guided across a river. These framework conditions contributed to the fact that 90 per cent of the system was installed manually on site. As it was impossible for trucks to transport the components, they were carried by mules, one part at a time, to the place of installation.
The route of the overland conveyor was coordinated between BEUMER and the cement manufacturer. The system supplier calculated the tractive forces of the belt considering the eight horizontal curves with radii of 1,000-5,000 metres. The routing was checked for its feasibility on site. The complete route was checked by employees on foot, passing through rough terrain, in order to reliably check the predefined positions for the 460 supports for their suitability directly on site. Whenever technically possible, the routing of the conveyor was adapted to the topography. Height differences of up to 100 metres had to be overcome within the shortest distances, so several sections were equipped with bridges of up to 55 metres. One section was realised with a 130-metre long tunnel.
Since February 2009 the overland conveyor has been transporting bulk material from the quarry to the bulk loading system. Since commissioning of the first section, the mass flow of the conveyor has increased in two steps. Today, the system conveys a mass flow of 2,000tonnes/ hour at a conveying speed of 4.5 metres/second.
In July 2013 Asia Cement contracted BEUMER again for an additional, efficient overland conveyor to replace the trucks transporting the limestone from the bulk loading system to the cement plant. A mass flow of 1,995 tonnes of limestone per hour was necessary to meet the plant’s requirements. For this project, the first conveyor was to be customised to these requirements. “We were planning a second troughed belt conveyor with an overall length of 13.7 kilometres,” says Dr. Echelmeyer. This was agreed on, making it the longest system in BEUMER’s history.
Projects of that size are often unpredictable, so flexibility was needed from the engineers. During the planning phase, Asia Cement acquired another plant in Lanfeng, approximately ten kilometres away. “Now we had to design the system so that both plants could be supplied with limestone,” explains Dr. Echelmeyer. The team had to divide the overland conveyor in two parts. After 5.4 kilometres, an additional conveyor can be added to be fed to Lanfeng in the future. In February 2015 the system supplier started with the installation of the conveyor frame.
Both overland conveyors have four horizontal curves with radii of 1,200, 1,500 and 1,800 metres. “We provided the engineering and the individual parts such as pulleys, motors, drive and control technology and the entire automation,” describes Dr. Echelmeyer. The installation was monitored by a BEUMER supervisor and the wiring of the system was supported by a BEUMER electrical engineer. The system supplier was also in charge of the commissioning in May 2016. The troughed belt conveyor is now supplying three kiln lines, and a fourth line is planned.
The requirements were different for the two Sichuan Yadong Cement/Asia Cement Group projects: the challenges for the first project were the hilly terrain, unstable grounds and crossing through conservation areas and over waterways; for the second project the system had to be built crossing through populated areas. The Chinese government has set out exact regulations on the noise emission levels so that the residents would not be impacted. “We had to minimise the noise to an extremely low level,” says Dr. Echelmeyer. The system supplier took several constructive measures in order to reduce the noise emissions. “We used noise-reducing idlers and customised protective covers on the drive stations,” Dr. Echelmeyer adds. In collaboration with the operator, BEUMER optimised the conveyor frame and the completely enclosed conveyor bridge.
Across both projects, BEUMER was able to ensure that the limestone is transported safely and quietly, without disturbing the residents or disrupting the surrounding natural environment.
Superior Industries (Superior), an American-based manufacturer and global supplier of bulk material processing and handling systems, has launched two new tracked conveyor models.
Joining the manufacturer’s top-selling line of portable conveying solutions are a 23-metre tracked stacker and a 2.4m x 4.9m tracked feed hopper.
Following Superior’s reputation for heavy-duty designs, the tracked stacker will be one of the heaviest models available in its class at 15.42tonnes. Each stacker is capable of handling up to 907tonnes/hour, while hydraulic power controls the tracks, folds, and discharge height. Using a cross-bracing design built into the undercarriage of the tracked stacker ensures structural rigidity and stable track travel.
The 8mx16m tracked portable feed hopper processes up to 725tonnes/hour from a 6.1m³ reinforced hopper. A bi-directionally dumping grizzly is equipped with adjustable grizzly bars and can be tilted at one of five pre-set angles. The hopper’s drive and backstop are hydraulically controlled in addition to the discharge conveyor’s fold and raise features.
Both the stacker and the feed hopper are equipped with Superior brand conveyor components like off-the-shelf idlers, pulleys and Exterra Primary Belt Cleaners. Several units are now in stock and available for immediate delivery from Superior or one of its many conveying equipment dealers.
From its humble beginnings in a garden shed in 1979,
The family-owned company has risen to its fair share of challenges - not least several recessions and the 2008 global economic downturn - by continually adapting, innovating and remaining true to its core values of staying ‘Close to Our Customers’ and being ‘Problem Solvers’. Having broken sales records in 2018, now Smiley Monroe has entered its landmark 40th anniversary year.
As this issue of Aggregates Business goes to press, Smiley Monroe Inc is finalising the location of its first USA production centre. Set to open its doors in 2019, the facility will be based on its successful production models in Lisburn and India. The US production centre will have a key focus on just-in-time supply of ZIP CLIP Belts to the North American market.
“Demand for our ZIP CLIP Replacement Conveyor Belts has grown exponentially in the States, so the time is right to invest in a facility close to our US customers, so we can reduce lead times and ensure the fastest turnaround” said Ryan Wright, North America sales manager. “This product is unique in the market place and with a growing industry focus on maximising opportunities for aftermarket sales, ZIP CLIP fits perfectly into this Spares and Wear Parts strategy. Some OEMs even specify ZIP CLIP on new machines, as it suits their existing manufacturing process and it’s both easy to factory fit and fast to replace in the field.”
Unlike the alternatives, ZIP CLIP Belts are produced using industry leading, stainless steel mechanical fastener technology for superior splice strength, durability and belt straightness. Like a spare wheel for your car, Zip Clip is supplied ready-to-fit – to suit the conveyor’s exact Endless belt length, width and specification – so there’s no need for specialist training or waiting on an external vulcanising team and once tensioned the belt can be run immediately. Having Zip Clip belts in stock, close to your most critical conveyors, which can be fitted in as little as 30 minutes, can really help maximise uptime in the event of an otherwise costly breakdown, particularly in operations such as contract crushing, where time is money.
“Having a base stateside opens the door for new business. Smiley Monroe has been exporting to North America since the mid-nineties, but the interest in our products and growth potential across the Atlantic is something we want to maximise. As a supplier, we believe our success is built on partnerships and a ‘go see’ culture that begins with how we support our customers to be successful,” said Chris Monroe, global sales director. “Opening our first USA facility during our 40th year in business is about deepening those relationships, so it makes this an extra special milestone.”
Meanwhile, closer to home, Smiley Monroe is gearing up for bauma Munich, the world’s largest construction machinery trade fair. “We’ll certainly have a lot to talk about this year” says Tim Monroe, the firm’s marketing director. “We’ll be launching our ‘Made for Mobile’ conveyor belt handbook which is intended to help support our engineering customers to design and adapt conveyors for mobile equipment, not just static or fixed plant; and to comprehensively address some of those frequently asked technical questions we have encountered over many years in the industry. Our content is very visual and has been created as an easy-to-use guide to meet the specific needs of our engineering customers.
“We’re also keen to educate visitors to our stand on the economic and environmental benefits of energy-saving products such as our polymer King Roller, something we’ve seen take on greater importance for our OEM customers as they seek to reduce the overall weight of their machines to reduce shipping costs and meet transport restrictions. It’s always great to catch up with our customers at bauma and with the industry so buoyant, the atmosphere this year promises to be something to look forward to.”
On the other side of the world, Smiley Monroe India has significantly increased the capacity of its Hosur production facility, near Bangalore in southern India, by increasing its footprint to 2,320m². Investment in a new CNC cutting machine and a new automated vulcanising press will enable the company to ramp-up production of Custom Cut Parts and Endless Conveyor Belts for customers in the region such as Terex, CDE Asia and Keestrack.
A leading global bulk material handling systems manufacturer serving, among others, quarrying and mining sector customers, Telestack supplies some of the largest blue-chip companies in the world. Designed, manufactured and exported from its current 9,755m² manufacturing facility in Omagh, Telestack plans to extend their manufacturing capacity by initially building a phase one 4,180m² factory on a greenfield site next to the current Fane Valley factory. The new factory will incorporate state-of-the-art manufacturing premises, a dedicated research and innovation development centre and modern office suite, all of which is central to the firm’s continued growth strategy.
The engineering acumen within Co.Tyrone is renowned globally, and the expertise within Telestack has grown and developed significantly over its 34-year history. In addition to its Aggregate and Mining Group, Telestack has matured within another material handling niche in the ports and inland terminals sector, designing and manufacturing equipment to load and unload dry bulk onto vessels up to Panamax (80,000tonnes size limits for ships travelling through the Panama Canal). The company’s equipment is involved in some of the most ground-breaking, exciting and forward-thinking projects across the globe, with Telestack gaining serious traction in other industries such as the rail, power, cement and steel plants.
Employing almost 160 local people, Telestack has demonstrated enviable year-on-year sales growth, with sales more than doubling in the last three years. In the last two years alone, the Northern Irish firm has invested almost £4million (€4.6mn) in its current Bankmore site within Doogary Industrial Estate. This has included the installation of a state-of-the-art shot-blast, two paint booths and additional manufacturing facilities, all contributing to the business’s impressive sales and operational performance.
Martin Dummigan, Telestack managing director, said: “Telestack has grown rapidly over the last number of years and we have firm plans to double our revenue again in the next three-and-a-half years. We have outgrown our current facility and we need to extend our footprint to meet the international demand for our products. We have made a conscious decision, even in the face of Brexit uncertainty, to invest locally. We have a unique skills base in Omagh and we need to protect Telestack’s engineering acumen. The marketplace has become somewhat flooded with companies who try to copy our designs, but you simply can’t buy experience. For want of a better cliché, you have to earn your stripes. We have the experience, the commitment and the enthusiasm to continue forging ahead and continue leading the market, hence the purpose-built research and innovation development centre. We have an aggressive strategy to continue growing our sales and we are committed to Omagh, to the people that we employ and to the local suppliers and businesses that will continue to benefit from the Telestack success story.”
Telestack recently designed and manufactured what is thought to be the largest international mobile bulk reception feeder in the world. The unit is currently loading aggregates onto barges for a large American multi-national corporation at loading rates in excess of 14,000 tonnes/day.
Telestack has also recently installed a unit as part of the multi-billion pound Thames Tideway Tunnel in London. Tideway is building a major new sewer under the River Thames, nicknamed the ‘super-sewer’, which is urgently needed to stop millions of tonnes of sewage overflowing into the river. At 15 miles long, seven metres wide and up to 65 metres deep, the Thames Tideway Tunnel is the biggest infrastructure project ever undertaken by the UK water industry. The Telestack unit is at the end of the tunnelling process, loading the tunnel clay onto barges fed from a fixed conveyor.
Meanwhile, Telestack is currently completing the installation of a £5 million (€5.74mn) system in Oman for the Port of Salalah. The equipment will be another global first in terms of innovation, providing a novel shiploading system to handle the additional capacity needed by the port. The four-unit installation comprises two shiploading systems, both featuring a TB60 All Wheel Travel Shiploader fed by a Titan dual-feed All Wheel Travel 800-6 Bulk Reception Feeder. Telestack says this represents the new generation of mobile shiploading, offering all of the performance of traditional systems but with the added benefits of mobility, flexibility and, ultimately, a lower cost per tonne achieved by increased production rates, reduced cycle times and reduced labour costs. The equipment is designed to load limestone, gypsum and cement clinker at average rates up to 1,200 tonnes/hour to Handymax, Panamax/Post Panamax vessels. Telestack began discussions in 2013 with the Port of Salalah technical and operational teams to design a customised shiploading system as part of an ongoing $15 billion infrastructure investment to cater for the export requirements of its local mining, quarrying and cement industries.
Telestack opens 2019 with its largest order book ever as it builds on the successes of 2018. This includes projects for Africa, USA, South America, Europe, Russia and Asia.