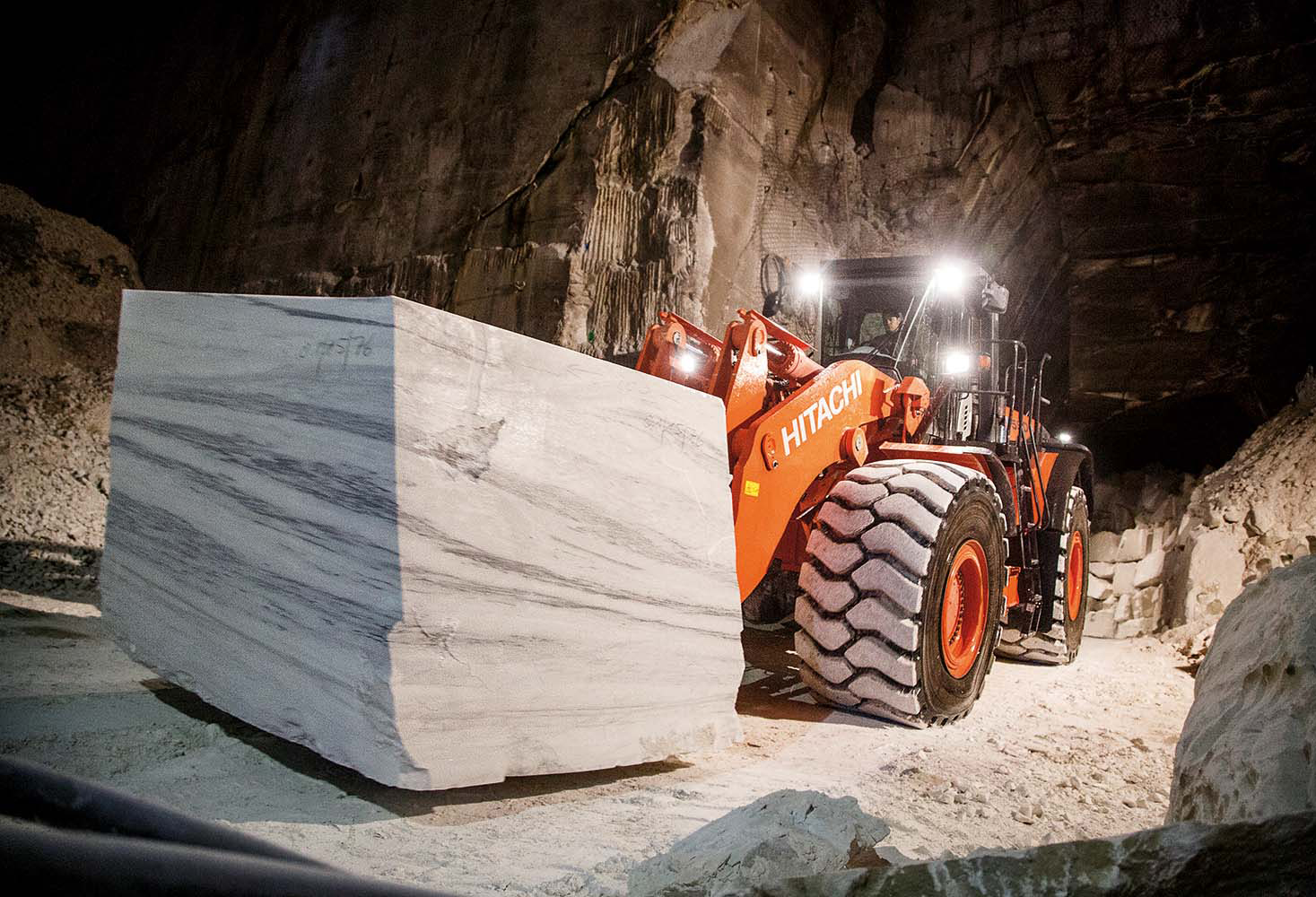
Major OEMs have new seen their new leading loaders take centre stage at a variety of successful quarrying and aggregate material supply businesses. Guy Woodford reports.
The ZW550-5 was delivered by Comac, a sub-dealer of the Italian Hitachi dealer for construction machinery, SCAI. The model’s fuel consumption is described as “brilliant” – on average eight litres/hour better than the previous machine – by Erich Tscholl, Lasa Marmo’s operations manager. It was supplied in December 2014 with a bucket and fork attachment, which is utilised through 80% of the machine’s operations.
Lasa Marmo’s decision-making process for the purchase of the wheeled loader was made by comparing three machines across five important criteria: the purchase price; aftersales service; performance and lifting power; agility and manoeuvrability; and size of the machine.
Tscholl summarises the company’s conclusions: “The Hitachi’s hydraulics were better and the traction power was stronger – even when travelling up the steepest hill. We spoke to the operator of the previous ZW550 model and carried out some tests with the machine, such as travelling fully loaded uphill. Overall, the Hitachi performed better than the other two brands.
“The height and width of the machine were among the most important parts of the required specification. The DPF filter is another essential feature – with less emissions and noise in such a confined space, we were aiming for a better and safer working environment within the site.”
Operator Roland Spechtenhauser has found the machine to be incredibly user-friendly: “It was easy to learn how to operate the ZW550-5 and it already felt like it was part of me after only a few days. The sensitivity of the levers is one of the machine’s strengths – it does exactly what you want it to do, even to the nearest centimetre.
“It is really amazing, especially with the hydraulic system and its lifting capacity. I’ve not yet had the need to push the machine, but so far it doesn’t flinch when lifting even the heaviest loads. In fact, it can lift anything on minimum throttle and there is also no difficulty in moving the blocks through narrow spaces or up the steep slopes in the cave. The automatic gearshift is incredible and could be one of the main reasons for the low fuel consumption.”
Whitewater quarry is the area’s main source of the 400 million-year-old metamorphic rock – an exceptionally hard and durable material, which is resistant to harsh and adverse weather conditions. With an estimated 30million m³ of marble remaining to be quarried over the next 500 years, it is one of the largest natural resources of its kind on the planet.
Lasa Marmo currently has a 30-year lease for Whitewater and two other historic quarries up until 2033. Between 2,000 and 4,500m³ of marble are quarried each year, and the company places a strong emphasis on processing the raw materials in Laas. This helps it to contribute to local industry and the region’s artistic traditions, as well as work as a partner with the local authorities for the protection of the area’s natural beauty.
In quarries worked by Schiewe in Ostwestfalen-Lippe, northwest Germany, Liebherr mining excavators are extracting shell limestone from the Triassic period 200-230 million years ago. In order to be able to cope with the enormous quantities of between 600,000 and 700,000tonnes/year, the company examines the machines in terms of their efficiency and sustainability prior to purchase. Together with the Liebherr dealership, Grotemeier in Bünde, the R 984 mining excavator with 7.5m³ capacity bottom-dump bucket was found to be the most effective equipment for direct excavation. Since this excavator was able to impress with its high level of performance, Schiewe invested in an additional R 9150 with an 8m³ bottom-dump bucket.
“Our latest acquisitions, the Liebherr R 9150, as well as the R 984, have proved to be equally well-suited to the extraction process in the quarry. Both the Liebherr excavators have the right operating weight and more than sufficient hydraulic power for the direct excavation method. A feature of both machines is also their tremendous efficiency,” says director Rolf Schiewe, emphasising his satisfaction with the Liebherr machines. Schiewe values the models’ low fuel consumption, but not only for reasons of efficiency.
“Environmental protection is important for us. We make a real effort to ensure we control the impact of our business activities on the environment. Fuel savings are an important step in this direction.”
For tough tear-out operations or for moving heavy material, quarrying and mining industry businesses mainly use larger crawler dozer models such as the Liebherr PR 756 and PR 764, said by Liebherr to be ideally suited for such applications due to their 40 and 50tonne operating weights. Both models’ hydrostatic drive lines are said to transfer the engine output with no loss of traction and without slippage to both drive chains. As such, material can be steadily loosened and removed efficiently.
In addition to various Liebherr wheeled loaders and mobile excavators, a Liebherr PR 734 crawler dozer is used in quarry operations at Holemans. The company, which has been quarrying gravel and sand between the Ruhr district and the Netherlands for many years, also trialled a PR 736 crawler dozer over a six-month period as part of its product development.
The PR 736 has an electronic drive control with integrated Eco function and proactive power adaptation. Contractors can choose between high performance capability and maximum possible efficiency. “The most important thing for us is pushing with force. This is 90 per cent of our operation,” explains Thomas Derksen, technical manager of Holemans. “The performance of the PR 736 is really impressive compared to the preceding models. And this is achieved with fuel consumption still at a similar level.”
Optimised structures throughout and an exceptionally strong undercarriage are said to ensure long-term durability, and field-proven components guarantee day-to-day reliability. A range of work tools extends versatility, and a spacious cab enhances operator comfort, convenience, and safety. Available Cat Connect technologies enhance overall machine efficiency and job site safety.
The 336D2 GC uses the fuel-efficient Cat C9 ACERT engine, rated at 208kW (ISO14396) and designed to meet U.S. EPA Tier 2 and EU Stage II equivalent emission standards. Electronic control of fuel and air systems ensures optimum power, and the engine’s constant speed contributes to fuel economy and reduced sound levels, Engine speed is reduced automatically during light-load conditions for further fuel savings. A new three-stage fuel-filtration system effectively removes contaminants from potentially low-quality fuel, resulting in minimal downtime and optimum protection of the engine and fuel system components.
Operating at a main-relief pressure of 35000kPa and producing optimised fluid flows from each of two large pumps, the 336D2 GC’s hydraulic system develops ample power to handle a range of buckets and work tools. For added efficiency and fuel savings, an electric pressure sensor reduces pump flow during light-load conditions, and regeneration valves in the boom and stick circuits efficiently recycle hydraulic fluid to lessen loads on the pumps. An optional auxiliary-hydraulic system adds versatility with its ability to handle powered work tools.
The 336D2 GC’s optimised mainframe is reinforced in high-stress areas, such as the boom foot, and its massive carbody is designed for strength and durability. Exceptionally heavy track frames form the undercarriage’s foundation which uses premium steel components in conjunction with grease-lubricated track chains that reduce undercarriage noise and internal wear.
The optimised front linkage, a 6.5m reach boom and 2.8m stick, features structures fabricated of high-strength-steel in a box-section, multiplate construction with internal baffles for added durability in severe applications. The linkage also uses castings and forgings in high-stress areas and is fitted with high-strength, large-diameter, abrasion-resistant pivot pins that can easily be serviced.
The versatile 336D2 GC can use a wide range of pin-on or coupler-type buckets and work tools to fit the machine for optimum performance and durability in its working environment. Buckets feature precise geometry for easy loading, which speeds digging cycles, increases production, and conserves fuel. Work tools options include hammers, grapples, shears, multiprocessors, compactors, and rippers. Cat couplers allow the operator to quickly change work tools and move from task to task for optimum machine utilisation.
The 336D2 GC model’s integrated Cat Connect technologies are designed to assist in improving three key areas: fleet management; productivity; and safety. LINK technologies include Product Link, which provides access to management information such as machine location, hours, fuel usage, idle time, and event codes via the online VisionLink user interface.
Loads of history
Hitachi’s new ZW550-5’swheeled loader could be said to be carrying a rich weight in history as well as each Lasa marble block at Lasa Marmo’s Whitewater marble quarry in northern Italy.
Lasa marble is still an important feature of certain architectural styles – especially from the neoclassical period – in cities such as Vienna, Munich and Berlin.
The most famous works constructed in the marble from Laas include: the Helmuth von Moltke statue in Berlin; the Pallas Athena fountain in Vienna; the Queen Victoria monument (outside Buckingham Palace) in London; and the Heinrich Heine monument in New York. In addition, around 96,000 white marble crosses are located in 15 cemeteries across Italy, France, The Netherlands, Belgium, Tunisia, England and The Philippines to commemorate the fallen soldiers in World War II.
Other more recent examples have seen 40,000m² of Lasa marble used in the new World Trade Center Transportation Hub in New York and 2,000m² in Italy’s tallest building, the Torre Isozaki in Milan.Volvo’s prime mover
Hampshire, county England-based New Milton Sand & Ballast Ltd’s recent decision to purchase a new
The family-run business has been producing sands and gravels in South Hampshire and East Dorset since 1936, and has had a long association with Volvo, operating various Volvo loading shovels at its facilities since the early 1980’s. The 38tonne EC380E has become the prime mover at the company’s Hurn Court Farm Quarry.
“We needed to replace the existing machine with a larger capacity excavator to assist in reducing cycle times as the extraction area gets further from the plant here at Hurn Court,” explains Drayton. “We had tried the smaller EC220D on loan to us from one of our associate companies for a short period and were impressed with its performance and production capabilities, as well as our operator’s positive feedback. All of this together with a competitive package on offer including a service contract for the larger EC380E meant we were buying a quality product and getting value for money at the same time,” he continues.
Equipped with a Stage IV Final 13litre engine, the EC380E is ideally matched to its automatic sensing mode hydraulic system. The machine’s hydraulics are said to perfectly complement the engine and are controlled by an advanced system which provides on-demand flow and reduces power losses within the circuit. Volvo’s innovative ECO mode is said to contribute to significant fuel savings without any loss of performance in most operating conditions. As well as improving fuel efficiency, this increases controllability for more precise performance.
Besides fast cycle times, the EC380E offers exceptional digging geometry with a forward reach of 11m, a generous dig depth of 7.3m and a load over height of 7.2m. The machine supplied to New Milton Sand & Ballast has been supplied with a hydraulic quick fit, a general purpose bucket and a heavy duty grading bucket.
“So far we’ve not been disappointed with our purchasing decision,” says Drayton. “The machine is certainly ticking all of the boxes.”