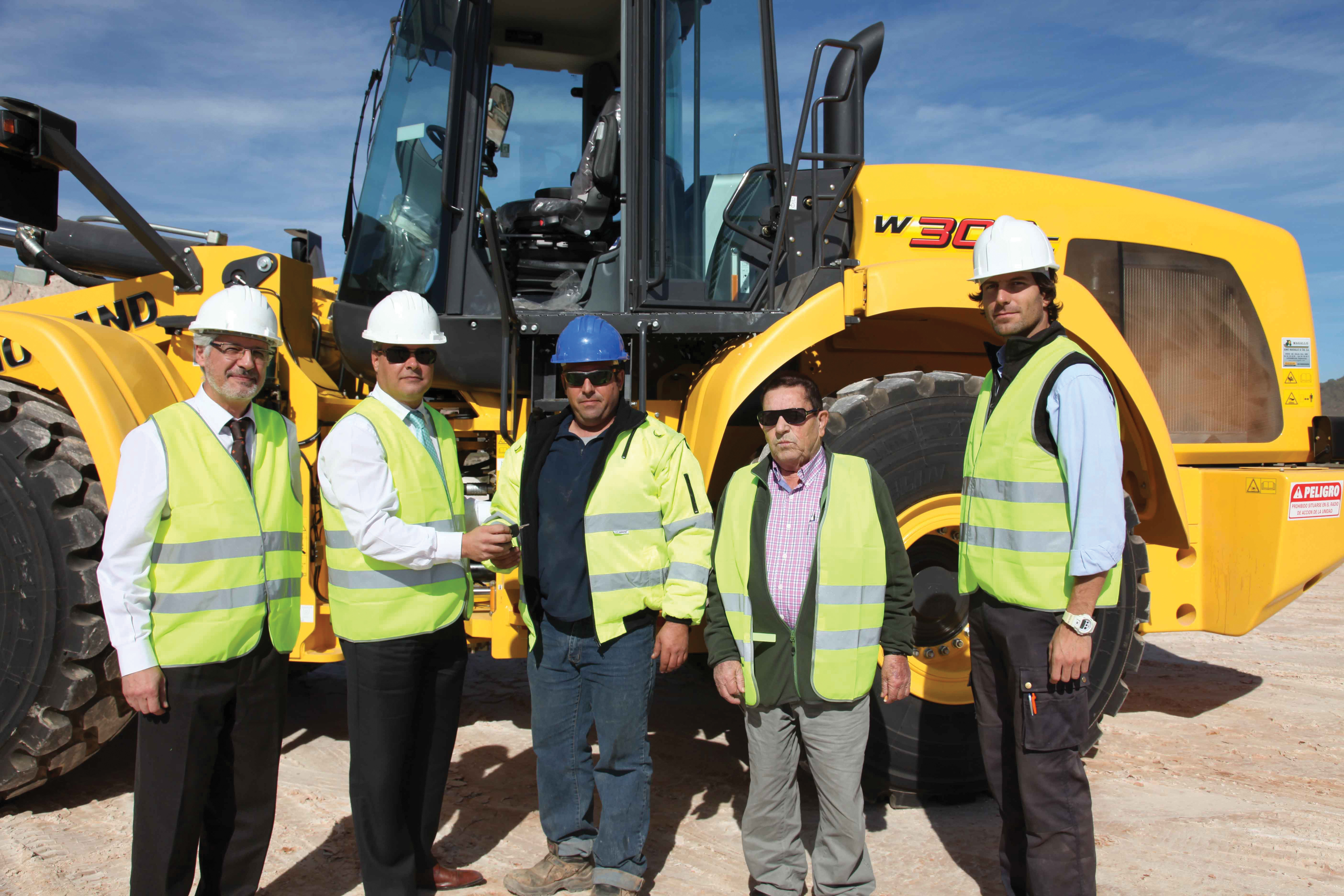
Loading is a vital part of a quarry operation and essential for good productivity. Patrick Smith reports
In a quarry, crusher capacity dictates the choice of all other machines in the process. The loader must be matched to the truck, with the right bucket size to optimise loading cycles, says
“In a chain process such as quarry ripping, loading and hauling, you can’t afford even one weak link,” says the company, pointing out that the number of trucks used will depend on the volume needed to keep the crusher fully loaded as well as the distance from the working face to the hopper.
Whether end-loading or drive-by loading on the bench, or open-pit loading, optimal loading procedures and cycle times are essential.
Wheeled loaders, hydraulic excavators, front shovel machines, work tools and quarry trucks are all designed to work productively together, but idle equipment means underutilisation of loaders or haulers due to wait time and inefficiency, which means lost productivity, says Larry C. Tate, segment manager Cat Hauling Systems.
In a presentation prior to MINExpo in Las Vegas, USA, last year, he suggested that in a loader to hauler pass match, the load time should be 1-2 minutes while there should be 4-6 loading cycles for hydraulic excavators and 3-5 for wheeled loaders.
Included in Caterpillar’s offerings for loading is the 966K XE wheeled loader, which utilises an integrated Cat continuously variable transmission system. It was tested at various sites in Europe in 2012, including
A hydraulic pump and motor (variator unit) on the model allows for smooth and continuous gear ratio change between engine speed and machine speed. The variator provides the ratio flexibility while reducing the heat load generated by the drive train when the machine is digging, pushing and climbing under heavy load.
The continuously variable gear ratio of the variator also enables the engine to run at a more efficient operating range independent of machine ground speed.
Power is transmitted through the variator unit (versatile gear ratio) as well as a parallel mechanical gear path (highest efficiency). Power is combined through a series of planetary gear sets in order to maximise the transmission efficiency over a wide range of operating conditions.
Developed especially for production loading for both 966K and 966K XE, Performance Series buckets are standard.
Volvo flagship
Meanwhile, Kelston Sparkes Group has taken delivery of
The company, which is normally associated with Volvo articulated haulers, loading shovels and medium-sized excavators, has its first EC700C working on primary extraction on a long-standing contract for
“To be honest we tended to look elsewhere for our large prime mover requirements, but with our existing 65tonne excavator approaching 15,000 hours and some significant track repair work required, we took an objective look at the market,” says managing director Alan Sparkes.
“With the long-standing relationship with Volvo’s product support people, their outstanding back-up and cooperation it was an easy decision for Steve Marsh, our workshop manager and his team.”
The new EC700C takes over as prime mover joining a Volvo EC480D and four Volvo 40tonne articulated haulers. Both excavators load the trucks with blasted limestone which is then hauled a short distance to the giant O&K mobile crusher.
“The areas for blasting and processing over the current phase of operations called for approximately 1.5 million tonnes of rock to be hauled to the crusher, which is at its maximum distance from the processing plant,” says George Stanley, Kelston Sparkes’ foreman in charge of the primary extraction team.
“We are shifting upwards of 15,000 tonnes of material a day on a 7am-5.30pm shift between the two excavators and four trucks.”
Equipped in mass excavation configuration as delivered to Kelston Sparkes Group, the machine is fitted with a bespoke 4.4m³ rock bucket supplied by MST.
At the heart of the EC700C is a 16litre Stage III V-ACT engine, and the specification of the new excavator also has a Lincoln automatic greasing system and the CareTrack advanced telemetric monitoring system.
Supplying equipment to feed the primary crusher at only one of several contracts Kelston Sparkes is currently engaged in at Torr Quarry, which includes the relocation of the quarry’s waste tip and crushing specific pockets of the quarry for Type I material which has seen a significant increase in demand.
Hitachi for hire
In Germany, one of the first new
Supporting two Hitachi ZX870H-3 loading shovels (the first of their kind in Germany) at the Calcitwerk Heidenheim limestone quarry, it loads overburden onto the company’s two
As the ZX670LCH-5 digs down through the overburden, the final destination for the materials is determined by the grade of rock, which contains a large proportion of high-quality calcium carbonate.
There are two production lines on the site: one produces building materials; and another grinds the rock down finely to one micro for varied industrial applications.
The ZX870H-3s were specified with loading shovels for this application so that the operators can select the type of material better for each process. They have completed between 6,000-7,000 hours working in temperatures as low as -20°C.
“This is a challenging working environment for construction machinery, but the Hitachis are helping us to meet our production targets,” says Christian Wogenstein, Calcitwerk Heidenheim’s technical manager.
“The ZX870H-3s have worked well in conjunction with the EH750s. We also enjoy a strong working relationship with Kiesel and we were happy to rent the new ZX670LCH-5 to test it alongside our existing fleet.”
Operator Robert Hahn says: “Productivity is so important in a quarry and that’s why I think the speed of the swing mechanism is the best thing about the ZX670LCH-5. It only takes four passes to fill one of the trucks and the loading cycle is fast, even when emptying the bucket.”
Meanwhile,
At a time when the Spanish mining industry is in great difficulty, the company is investing in updating its fleet to ensure it has the high productivity equipment it needs to run its operation efficiently.
“Arcigrés has had the foresight to act quickly and to invest in new equipment, and as a result it has not only maintained, but improved its position in the market,” says Ximo Magalló, general manager of NHC’s dealership.
“Nowadays we have to look beyond the sale of a machine and guarantee a full service. Technical support is a key activity in our business. We always try to support our customers in every way we can, from loaning a machine in case of break down to payment plans that fit their business’s needs. Our customers greatly value these attentions.”
An NHC customer since the 1970s, Arcigrés opted for the W300C, which features New Holland’s Tier 4 interim AdBlue technology, “for its powerful performance,” required for the china clay extraction applications.
Working in a quarry with a daily production of around 7,000m3 and where about 2,000tonnes are loaded every day, the machine’s bucket can carry up to 10tonnes of china clay.
“We load up a truck with just three buckets full of clay,” says Jorge Gabarda Cortés of Arcigrés.
It is claimed that the new W300C uses 70litres less fuel a day than the W270 wheeled loader it replaces.
“Considering ten hours work a day, five-days a week, we will save 16,800litres of fuel and at a price around €1.19/litre, we can save as much as €20,000 in the next 12 months,” claims Jorge Gabarda.
In another first, Castle Hill Quarry, Cannington, near Bridgwater in County Somerset, south-west England has bought the UK’s first
With a bucket capacity of 4.2m3, the wheeled loader, powered by the 13litre
“Since we purchased our first Daewoo 180LC excavator in 1991 and subsequent to the takeover by Doosan in 2005, the machines have come a long way,” says Stephen Ford, managing director of Castle Hill Quarry.
“The main things that have impressed me about the latest Doosan Stage IIIB wheeled loader are its power and fuel efficiency, which are big factors in the current climate,” says Ford, who oversaw the purchase of the first Daewoo 180LC tracked excavator from Kellands, a machine that is still used around the quarry, which also runs a Doosan DX480LC excavator purchased together with a DL400 from Kellands in 2008, which works mainly at the quarry face as a primary cutter.
Quarrying started on the site at Castle Hill in 1903, supplying the local area with aggregates, and it is still delivering aggregates throughout Somerset using the company’s own fleet of trucks. It can supply anything from rock armour down to 0mm-4mm fine.
Doosan Infracore Construction Equipment has also launched the new Stage IIIB compliant DX380LC-3 large crawler excavator in the 34-42tonne market segment, which is aimed at applications including large-scale material handling. It is powered by the Doosan DL08K common rail six-cylinder turbocharged diesel engine meeting Stage IIIB engine emission regulations.
Complimentary KOMTRAX
In late 2012,
Weighing in at 17,910kg, Komatsu says it offers improved efficiency, lower fuel consumption, improved operator comfort, and enhanced serviceability.
Powered by a Komatsu SAA6D107E-2 engine producing and EU Stage IIIB/ EPA Tier 4 Interim emission certified (S3B), it is supported by Komatsu CARE, a complimentary maintenance programme for Komatsu customers that comes as standard with every new Komatsu S3B construction machine.
The latest KOMTRAX technology gathers data, such as operating hours, fuel consumption, location, cautions and maintenance, with alerts relayed to a web application for analysis.
Among other new features is SmartLoader Logic, which Komatsu says provides optimal engine torque for the job required.
“Komatsu SmartLoader Logic helps to save fuel by automatically decreasing engine torque when the loader isn’t working hard, such as when it is driving with an empty bucket. It functions automatically and doesn’t interfere with operation, saving fuel without decreasing production,” says Komatsu.
For loading operations on a major contract, Beton & Recycling from Bad Düben in Germany opted for latest generation
Site manager Torsten Hankel ordered one of the first CX350C excavators to be used in Germany for extraction operations in a sand pit.
The contract for work on the B6N highway involved raising an embankment to take a steel arched bridge over the future Halle-Leipzig railway near Köthen.
Beton & Recycling had to deposit some 200,000tonnes of material either side of the bridge. This was transported by the company’s fleet of
Beton & Recycling opted for three latest-generation Case machines to fill key positions within the production chain.
The new C series crawler excavator is said to be ideally suited to demanding digging and excavation applications. It soon became clear that the load capacity of the CX350C was not the most critical factor in the calculation: the available carrying capacity was more important, so more dumpers were called in on a short-term basis. The incoming material was spread and mounted by a new LGP (large grouser pads) 1650L bulldozer, the first Case dozer of this type to be used in Germany.
With heavy traffic, and in order to transport the required quantity of material to the site, an intermediate depot was set up material was temporarily stored in a skip trailer and several dumpers.
Then Beton & Recycling’s third new machine, a new type 1021F wheeled loader, took over.