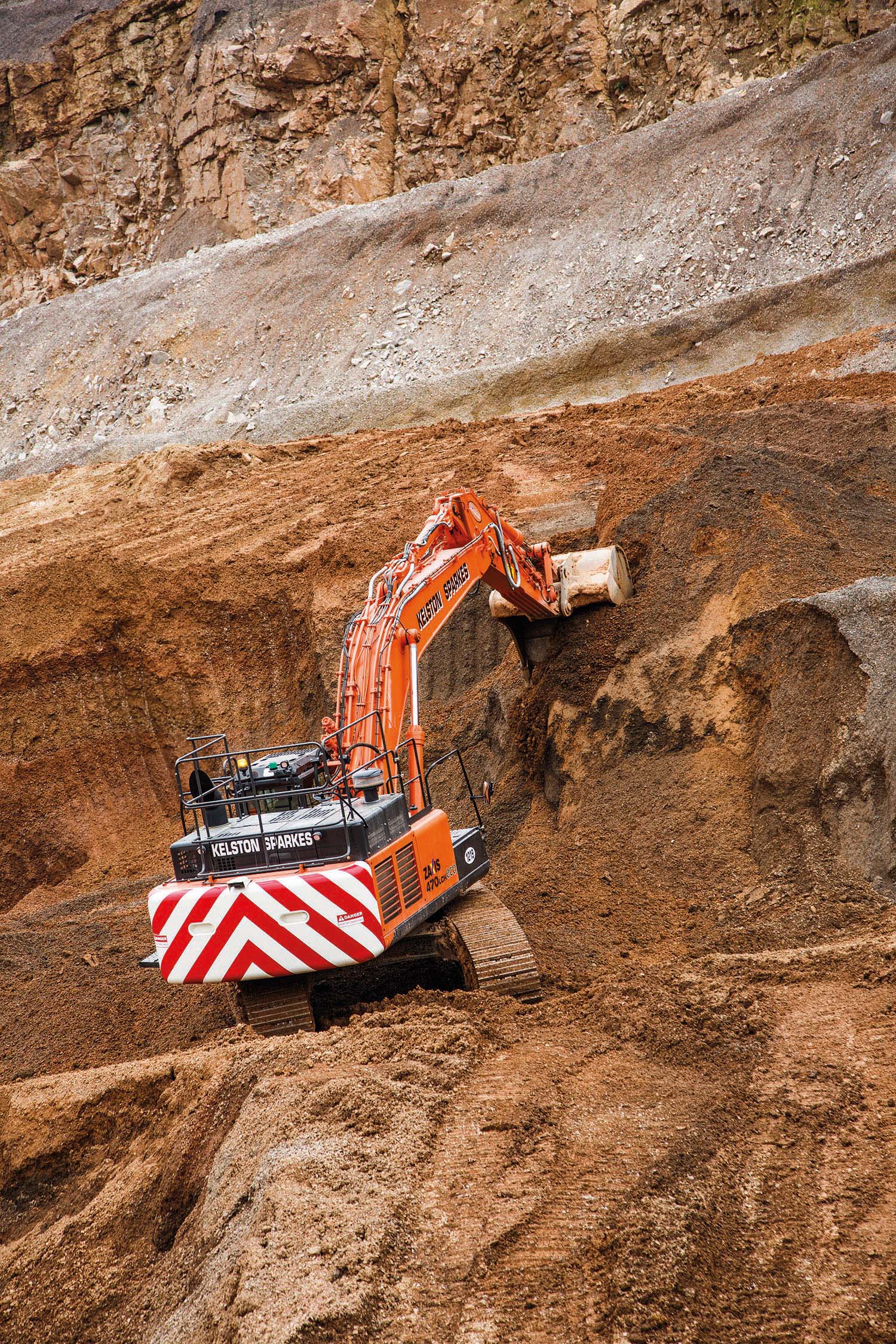
A leading global manufacturer has unveiled what it claims is a world crawler excavator first, while increased demands from leading European cement and aggregate companies for local firms to load and haul their materials is encouraging new UK loader model sales. Guy Woodford reports.
Built at Komatsu UK’s excavator plant in Birtley, north-east England, the PC210LCi-10 features Komatsu’s exclusive machine control and guidance system, said to be fully integrated with all other qualities and benefits of a standard Komatsu PC210LC-10 excavator.
From rough digging to finish grading, Komatsu says the PC210LCi-10 excavator can dramatically improve efficiency, precision and safety on the work site.
“This latest Komatsu technology is a revolution in how hydraulic excavators will be used in the coming years” says Mal McCoy, product manager for Hydraulic Excavators and intelligent Machine Control Products. “The ability of the PC210LCi-10 to achieve and maintain grade with minimum effort from the operator is awesome.”
The 21tonne PC210LCi-10’s latest KOMTRAX technology sends machine operating information to a secure website via wireless technology. Data such as operating hours, fuel consumption, location, cautions and maintenance alerts are relayed to the web application for analysis.
Komatsu claims the KOMTRAX fleet monitoring system increases machine availability, reduces the risk of machine theft, allows for remote diagnosis by the distributor, and provides a wealth of other information to drive business efficiency and productivity.
The PC210LCi-10 is supported by Komatsu CARE, a free maintenance program for Komatsu customers that comes as standard with every new Komatsu EU Stage IIIB construction machine. For the first three years or 2,000 hours it covers factory-scheduled maintenance, performed by Komatsu-trained technicians with Komatsu genuine parts. Komatsu CARE offers up to two complimentary Komatsu Diesel Particulate Filter (KDPF) exchanges and a KDPF warranty for the first five years or 9,000 hours.
The bucket on the PC210LCi-10 is, says Komatsu, is automatically limited from digging beyond the target surface. The control function maintains grade automatically, with real-time bucket edge positioning in relation to the machine and the job surface. Status is instantly displayed on the full colour, multi-function 30.7cm control box monitor, eliminating the wait time associated with conventional sensors.
Factory installed, Komatsu’s fully integrated intelligent machine control system includes stroke sensing hydraulic cylinders for the boom, arm and bucket, newly developed by the Japanese firm for highly accurate real-time bucket edge positioning. The IMU (Inertial Measuring Unit) is said to give precise machine orientation and determines machine angle from gyro and accelerometer data. High performance antennae send satellite signals to a GNSS receiver that processes them and provides real-time position of the machine.
The touch-screen control box monitor on the PC210LCi-10 is said to make grading easy and accurate with a facing angle compass, a light bar and audio guidance. Information such as real-time ‘as-built’ status, a magnified fine grading view or a 3D bird view can be displayed simultaneously.
By setting 3D design data on the control box monitor, Komatsu says staking can be reduced or eliminated, along with surveying and final inspection. Safety is also said to be greatly improved, with less people needed on the job site and near the machine.
Customers have complete access to the machine through client support and KOMTRAX, both of which can be integrated to some extent with other proprietary site management systems to deliver daily work tasks to the machine. However for those looking to take the system further, Topcon offers its Sitelink 3D Enterprise site management tool as an option.
Sitelink 3D provides complete access to machine data, with a two-way transfer of information to provide engineers on-site with as-built data from the machine, reducing the need for final engineer checking of grades on-site. The system can be used to report daily volumes and for various task management functions.
This system will only work with Topcon IMC controlled equipment, however Topcon is also working in partnership with Ammann and Bomag, along with several haul truck systems, to provide complete road construction site management compatibility.
Scottish quarrying expert William Thompson & Son is the first British firm to invest in the new
Of the landmark deal with Cat, Andrew Thompson, director at William Thompson & Son, says: “We strive to be at the cutting-edge of new technologies enabling us to maximise productivity, minimise cost, whilst reducing our carbon footprint. The new Cat machines are leading the way in our industry, therefore it was a simple business decision to integrate them into our fleet and benefit from the value they will add to our operation.”
Thompson says that efficiency is just one of the reasons for purchasing Caterpillar equipment, adding: “Making sure our operators know we’re providing the best equipment possible is important to us. Operator comfort and machine functionality is a big factor in deciding to invest in the Cat machines. We’ve already seen a decrease in minor denting and uplift in productivity since using the Cat 336 Excavator on-site this year.”
Caterpillar claims the Cat 972M XE wheeled loader is the class leader in fuel efficiency, with XE advanced powertrain technologies enabling a claimed 25% fuel saving for William Thompson & Son.
The Cat XE range is said to have been designed to deliver superior efficiency by utilising an integrated Cat continuously variable transmission (CVT) system, rather than a standard torque converter. A hydraulic pump and motor (variator unit) is said to allow for a smooth and continuous gear ratio change between engine speed and machine speed. This variator unit allows the machine to run at a much lower rpm, meaning that the functioning rpm of the XE model runs at 500rpm less than the standard Cat 972M. This will save William Thompson & Son an average of four litres of fuel for every hour the Cat 972M XE model is deployed.
There is an increased level of demand from leading European cement and aggregate companies, who own sites and sell aggregates in the UK, for local companies to load and haul their materials.
This has led to Bristol, England-based Kelston Sparkes Group buying seven new
The company has purchased two ZX210LC-5s, two ZX470LCH-5s, a ZX520LCH-5 and a ZX670LCR-5 in 2014. In addition, over the past 12 months it has also added a ZX290LC-5 excavator and a ZW310 wheeled loader to its fleet of Hitachi construction machinery, which includes a ZX70, two ZX350LC-3s and a ZX470LCH-3.
“Our replacement cycle for excavators was 6,000 hours before the economic crisis,” says Alan Sparkes, whose father Kelston established the company in 1952. “We’re getting back to this level, as the future is looking positive with several large construction projects due to start soon in this region.”
Sparkes is the co-owner of the privately owned company with his brother-in-law, Robert Stark. Kelston Sparkes has had a long and successful history, from the early days as an agricultural contractor to its first steps into plant hire and its current status as a national contractor, with 167 employees and a fleet of 60 trucks, 40 excavators, 30 bulldozers, 12 mobile crushers and 20 wheeled loaders.
Kelston Sparkes’ core business is quarrying, supported by other projects including gravel pit, waste disposal, flood and sea defence sites. Quarrying now accounts for more than half of the company’s €25.38 million turnover and it estimates that it moves over eight million tonnes of materials/year.
The biggest current operation is in the Mendip Hills, Somerset, where the quarry owner relies on Kelston Sparkes for 90% of the movement of its materials (3.5million tonnes/year). It has between 30 and 36 machines on the site at any one time, all supplied with operators.
“Our strategy has been to stick to what we do best, i.e. bulk earthmoving,” adds Sparkes. “We’ve never had so much long-term work thanks to the excellent working relationships we have with our customers. One of our biggest strengths is flexibility – we can make quick decisions – and this helps us to build upon the strength of our partnerships. Our customers need suppliers who they can rely upon and the big priority is health and safety.”
The most important criterion that Kelston Sparkes considers when buying a new machine is after-sales support. The workshop manager is influential in purchase decisions and the back-up he gets from the manufacturers is vital to the company’s entire operation.
“Reliability is the number one reason for buying Hitachi excavators,” says Stark. “Our customers have no patience for downtime – they need an immediate response from us and our suppliers. It’s not just about technical support and genuine parts though, it’s about the whole Hitachi Support Chain package, including Global e-Service and Hitachi Extended Life Program [HELP].
“The information from Global e-Service is very useful for analysing fuel consumption and actual machine usage. It is company policy to take out HELP for a minimum of three years/6,000 hours. We focus on the total cost of ownership of each machine, with a full record of everything from the running costs to the resale value of each model.”
Brian Smyth, who has worked as an operator with Kelston Sparkes since 1978, says: “I’ve been working with Hitachi excavators for over 30 years. I started with a UH063, before moving on to an EX120 and the more recent Zaxis machines. The overall operation of the new ZX470LCH-5 is very good and it helps me to efficiently load our fleet of articulated dump trucks.
“The ZX470LCH-5 is powerful, smooth and an excellent all-round package.”