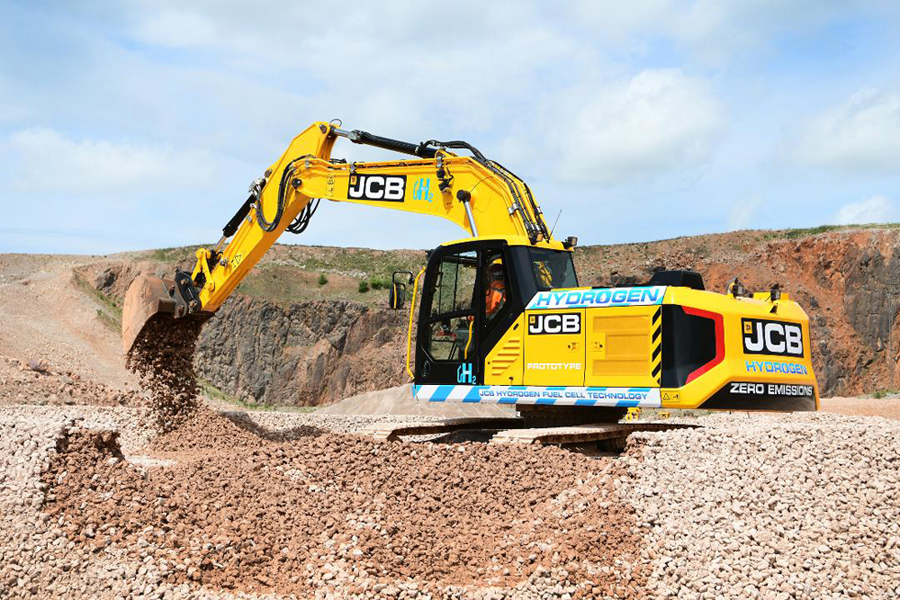
British construction and quarrying equipment giant JCB has created the world’s first hydrogen-powered digger.
Company chairman Lord Bamford and his son Jo, who runs Ryse Hydrogen and Wrightbus, have spent two years working on the construction of what is claimed to be the industry’s first-ever hydrogen-powered excavator, and a further year testing the prototype.
JCB says the new machine will maintain its position among the leaders in the sector on zero- and low-carbon technologies and will continue Ryse Hydrogen’s push to kickstart the UK’s hydrogen economy.
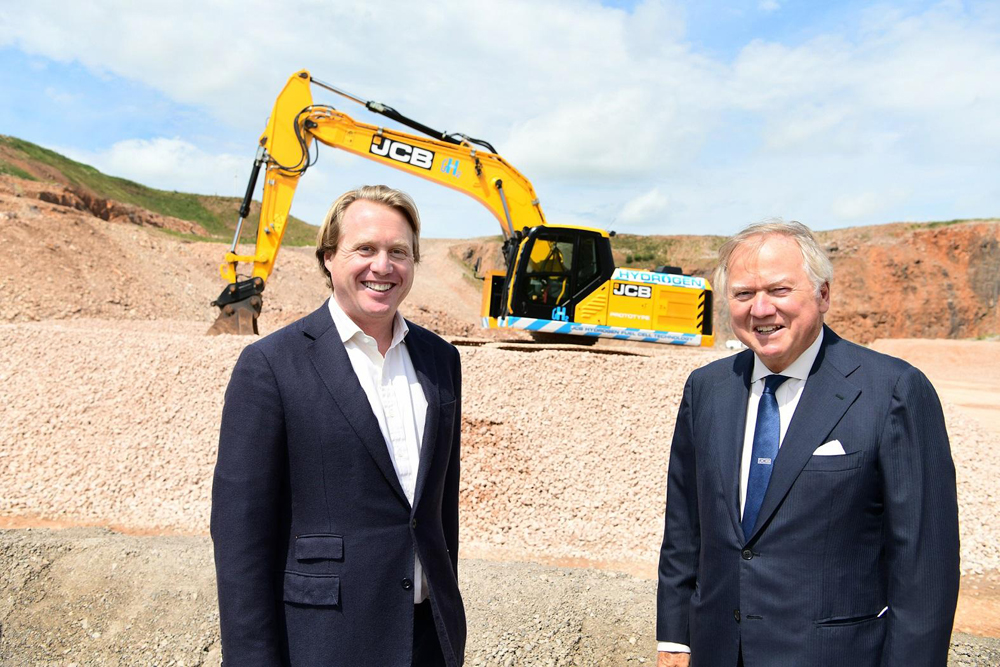
The 20-tonne 220X excavator powered by a hydrogen fuel cell has been undergoing rigorous testing at JCB’s quarry proving grounds. JCB says it is the first construction equipment company in the world to unveil a working prototype of an excavator powered by hydrogen.
Lord Bamford said: “The development of the first hydrogen-fuelled excavator is very exciting as we strive towards a zero-carbon world. In the coming months, JCB will continue to develop and refine this technology with advanced testing of our prototype machine, and we will continue to be at the forefront of technologies designed to build a zero-carbon future.”
Jo Bamford said it was a game-changing addition to JCB’s fleet and a strong message for Britain’s green economy.
“I grew up on the shop floor at JCB and have spent many years working on a prototype to help take our companies into the future,” he said.
“I truly believe hydrogen is the UK’s best opportunity to build a world-leading industry which creates UK jobs, cuts emissions and is the envy of the globe.”
Power for the prototype excavator is generated by reacting hydrogen with oxygen in a fuel cell to create the energy needed to run electric motors. The only emission from the exhaust is water.
The development comes after JCB last year went into full production with one of the construction industry’s first fully electric mini excavators, the 19C-1E. JCB has also extended electric technology to its innovative Teletruk telescopic forklift range with the launch of an electric model, the JCB 30-19E.
JCB says it has also developed clean diesel technology to meet Stage V EU emissions regulations that has almost eradicated the most harmful emissions from its latest range of diesel engines. Nitrous oxide (NOx) is down 97%, soot particulates down by 98% and carbon dioxide (CO2) emissions down by almost half.
Komatsu Europe is launching the new PC210LCi‐11, PC290LCi‐11 and PC290NLCi‐11 excavators.
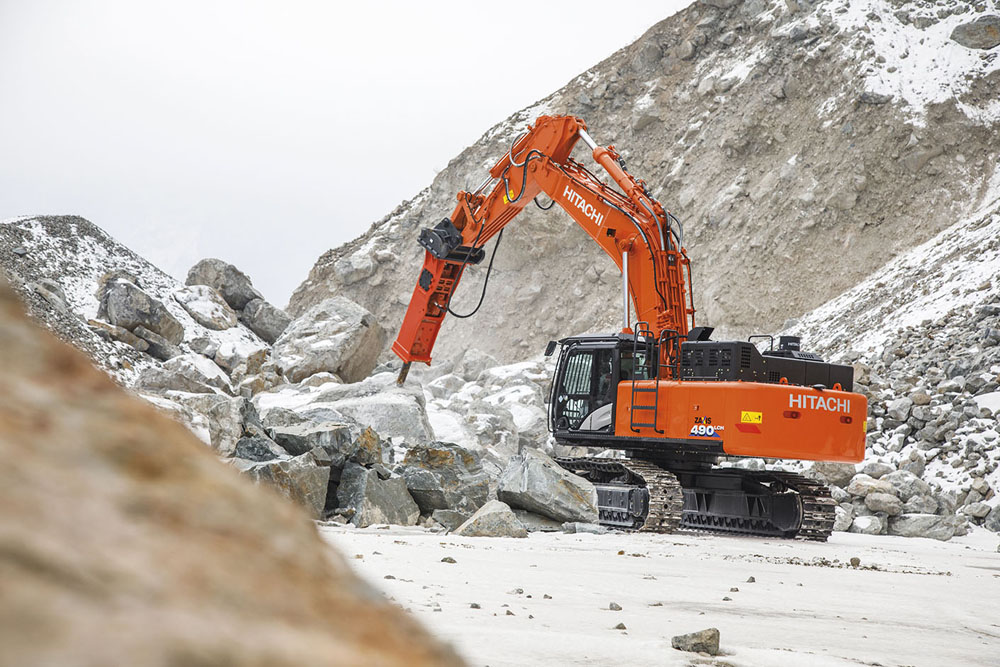
The excavators incorporate Komatsu’s fully factory‐integrated intelligent Machine Control 2.0 (iMC 2.0), which Komatsu says will deliver higher productivity, efficiency and cost savings.
“With machine control being an ever‐growing trend in the construction industry, the introduction of these new iMC 2.0 machines re‐affirms Komatsu’s lead in this space,” said Rob Macintyre, product manager at Komatsu Europe.
Operating weights of the PC210LCi‐11 range from 22.12 to 23.58 tonnes, and it has a maximum recommended bucket capacity of 1.65m³. The EU Stage V Komatsu engine has a power output of 123kW @ 2000rpm.
The PC290LCi/NLCi‐11 operating weights range from 28.95 to 30.95 tonnes, with a bucket capacity of 2.02m3, and their EU Stage V Komatsu engines have a power output of 159kW/196HP @ 2050rpm.
The machines also feature the latest KOMTRAX telematics, and the Komatsu Care maintenance programme for customers.
Komatsu says the European market introduction of the new PC210LCi‐11, PC290LCi‐11 and PC290NLCi‐11, brings along with it several new intelligent features that further boost machine and jobsite productivity and efficiency.
These include the new Komatsu Auto Tilt Control for tilting buckets which is designed to make operations on slope and ditch work easier, and automatically limits under‐digging and increases bucket fill. The bucket automatically tilts to design surface with no need for the operator to manually intervene.
With the new Bucket Angle Hold the operator no longer needs to use the lever to maintain the bucket angle through grading pass. Once the desired angle is selected, this feature automatically maintains it as the arm moves in.
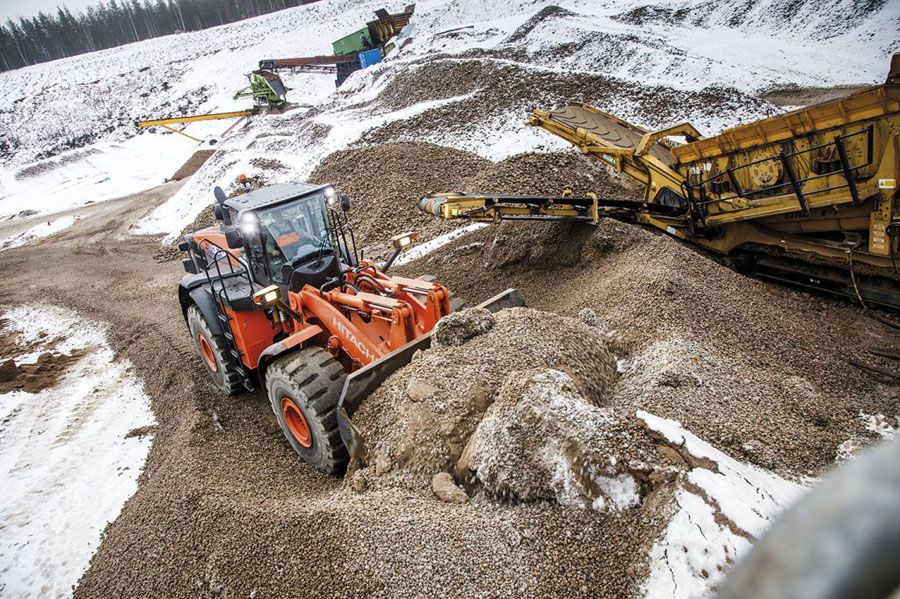
A new iMC 2.0 monitor is claimed to provide unrivalled ergonomics and intuitive smart-phone-like screen navigation features. Slimmer, lighter and more compact, it has increased memory capacity and fast processing speed.
Komatsu intelligent Machine Control 2.0 now features a new IMU sensor for tilt buckets. Easily mounted and calibrated, it increases attachment and machine utilisation, allowing different tilting buckets to be fully integrated into the excavator’s control system.
The new PC210LCi‐11, PC290LCi‐11 and PC290NLCi‐11 also carry over the original Komatsu intelligent Machine Control features of Auto Stop Control, Auto Grade Assist & Minimum Distance Control which Komatsu says have assisted operators to move material safely, quickly and easily over many hours of operation and without having to worry about digging too deep.
Hitachi says one of its ZW370-6 wheeled loaders is offering a Finnish contractor high levels of productivity at a demanding quarry in the south of the country. Niemisen Sora’s (Niemisen) decision to utilise Hitachi’s second-largest wheeled loader was based on the successful introduction of the equivalent ZW-5 model in 2016.
Niemisen is using both wheeled loaders to move materials at a busy eight-hectare quarry in the municipality of Hausjärvi. From its headquarters in Hauho, Niemisen supplies around 40 types of gravel and stone. The Hausjärvi quarry produces approximately 800,000 tonnes of sand, gravel, chippings and stone ash per year for the family-owned company.
Niemisen’s chief operator at the quarry is Henri Petman, who has spent 15 years with the company. “Hitachi wheeled loaders are particularly suited to the work we do here, because of their excellent carrying capacity and grip,” said Petman. “The traction control means there is no wheel spin in slippery conditions. I’m currently working with the ZW370-5 and it performs to a high standard.”
The ZW370-5 was delivered in February 2016 by the authorised Hitachi dealer in Finland, Rotator, and has worked reliably for over 2,000 hours – even at temperatures as low as -15°C.
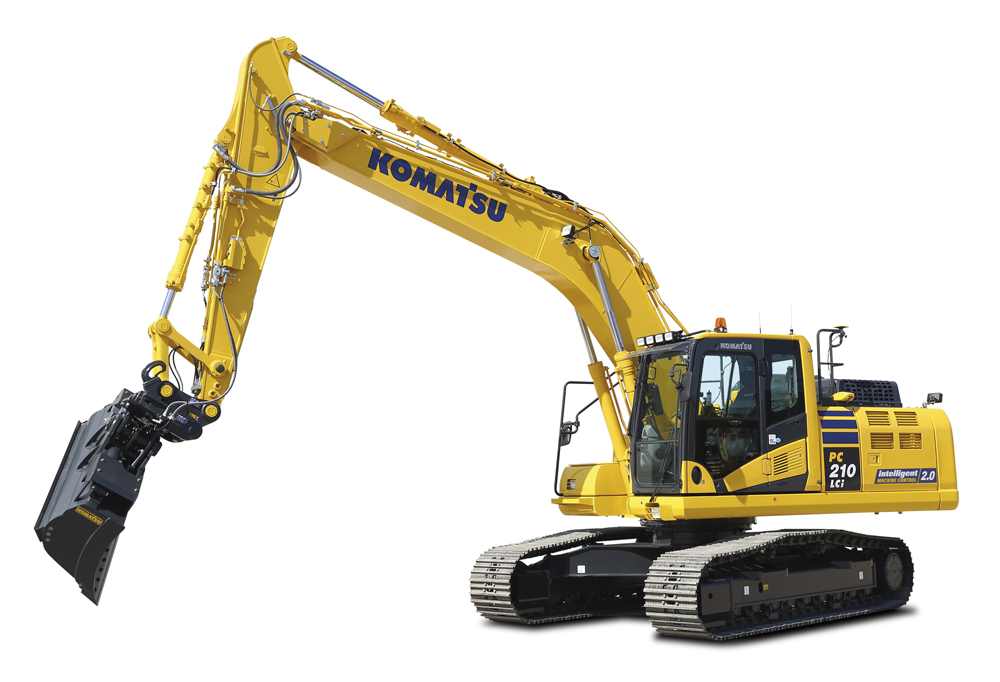
Hitachi machines are also being effectively employed by Réné Apprin & Cie for its quarry near Saint Jean de Maurienne in the Auvergne-Rhône-Alpes region of France. Local dealer Teramat supplied a new ZX470LCH-5 excavator in 2015 and the latest ZX490LCH-6 model with a three-year/5,000-hour extended warranty a year later to Carriére du Rocheray, which dates back to 1880.
The two excavators are used for breaking (the ZX490LCH-6 with a hammer attachment) and loading the materials (ZX470LCH-5) respectively. Réné Apprin & Cie expects that each machine will be operated for less than 1,000 hours per annum.
“The biggest benefit that the large Hitachi excavators bring to the business is undoubtedly their reliability,” said company owner Pierre-Olivier Apprin. “This is very important to us, as well as how fast and smooth they operate in the quarry. The Hitachi machines are strong and durable and have the capacity to handle large rocks.”
Réné Apprin & Cie extracts up to 250,000 tonnes of granite-based materials each year, with a licence that currently runs until 2034.
The first new Doosan DX350LC-7 36-tonne crawler excavator to operate in Italy has helped to secure the bed of the But creek, a tributary of the Tagliamento river in the province of Udine in Northern Italy.
Part of a fleet of Doosan equipment, including two further crawler excavators, two articulated dump trucks (ADTs) and a wheeled loader, the DX350LC-7 is involved in cleaning and safety operations along 4km of the riverbed, to repair damage caused by the catastrophic Vaia Storm at the end of 2018.
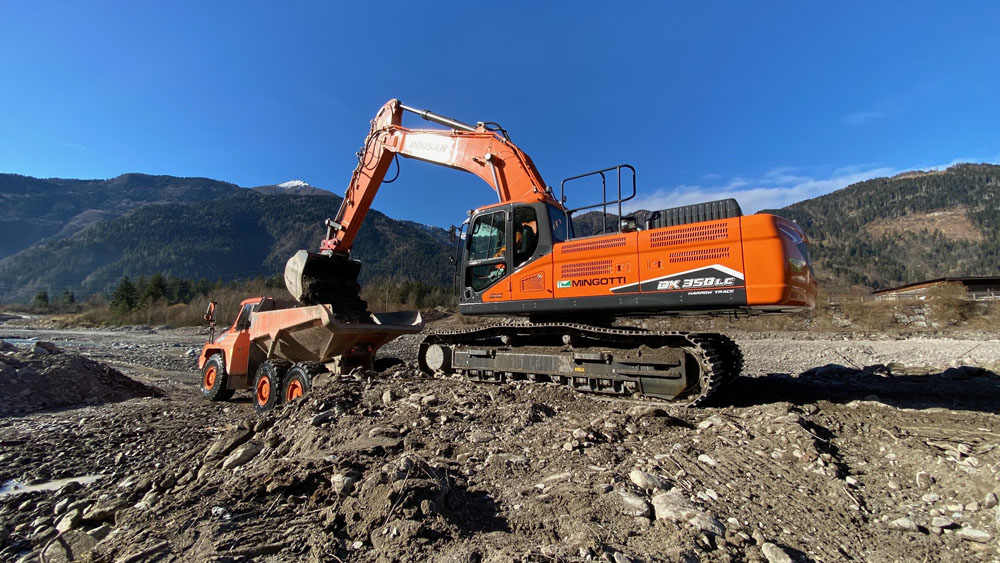
The new DX350LC-7 has been purchased by Mingotti T., based in Tavagnacco in Udine, and supplied by DMO Spa, the authorised dealer for Doosan and Bobcat in the region. Mignotti T. was contracted to carry out work repairing damage from the Vaia storm by the authorities in the Friuli Venezia Giulia region.
Doosan has also launched a new line-up of general-purpose performance buckets covering capacities from 2 to 6.7m3 for the company’s wheeled loader range. The new range of buckets represents the first stage in an expansion of the choice of new wheeled-loader work tools from Doosan.
The key features of the new range include the wide configurability and larger capacities of the buckets available to customers, with new buckets able to be tailored for their applications. The buckets are manufactured using Hardox steel and are claimed to offer increased wear resistance compared to those made from hardened steel. All the parts in contact with the ground or materials are designed to facilitate optimum penetration into material mounds, thus reducing fuel consumption. New shock absorbers also provide additional comfort for operators and reduced stresses on both the wheeled loader and the bucket structures.