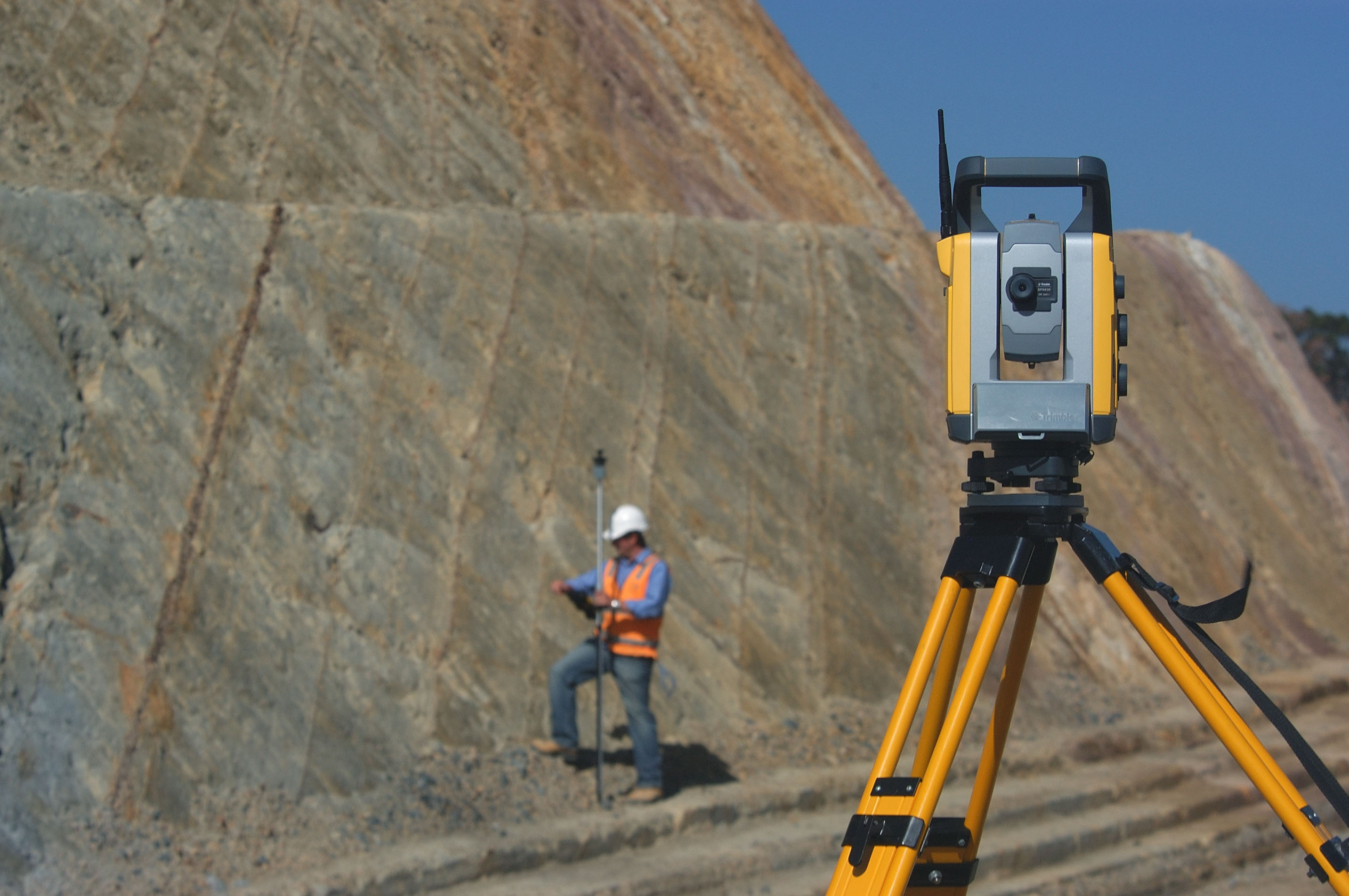
Modern surveying techniques mean that quarry operators can collect more usable information in less time than ever before
Surveying a quarry used to mean calling in a specialist company several times a year to trek round on foot with a tripod and manually collecting data before taking it back to the office to process. Today it is possible for a quarry manager to collect a greater level of information on an almost daily basis in a format that can be more easily used than ever before.
The equipment that is bringing about this step change is vehicle mounted scanning systems that are linked to GPS positioning which can collect millions of points of information in a short space of time.
"Extensive use of surveying in quarries started in the 1980s with laser scanning to profile the bench shape, which over the last 25 years has enabled the industry to blast with more safety," said MDL chairman Steve Ball. "The technique is very popular now - particularly in the UK - and people are still investing in the technology although there are new alternatives available.
"Video stereo photography systems are available on the market to quarry operators but there are limitations with such technology as it requires good contrast to work effectively.
"The biggest breakthrough is the latest vehicle mounted scanning systems which are much faster than laser profilers and open up the data to wider use than just planning blasts. The systems, like our Dynascan, are formed by a pod mounted on the roof of a vehicle to scan in three dimensions using GPS to position the vehicle and motion sensors to remove the effects of pitch and roll of the car "Instead of collecting a number of points per hour to produce a face profile as laser scanning does, the Dynascan can scan hundreds of hectares in the same period. The system can scan 150m from both sides of the vehicle at a speed of 10km/h." MDL has been developing the Dynascan system for several years and already sold several to surveying companies but in July, Ball made the first sale directly to a quarry operator and he said this demonstrates the difference between this and laser scanning.
"US-based quarry group Mulzer has bought the system to allow it to carry out regular inventory checks for stock control and royalty payments for its quarries in Indiana," he said. "Normally such checks would call for a survey crew to be commissioned once a quarter and the work would take a few weeks to complete with crude results. With Dynascan the ability to collect this information changes to just hours.
"The resulting image is not just a pretty picture with sections clearly mapped for blasting - it allows for much better planning too as it log everything in detail including the roadways and even the potholes with those roads." According to Ball, delivering the data to the customer via the web opens up other new possibilities. The company is currently developing a web server to help with this. "We recognise that most quarries do not have the computer systems to handle this volume of data so the server will allow us to process the data offline for them and hand back the data in a ready to use format.
"Effectively the data will allow authorised users to 'fly' into the quarry using
IP-S2 data can be viewed in Spatial Factory on a background map, in 3D or in a panoramic view of images overlaying point cloud data. Control point registration can be achieved to increase the accuracy of collected data over long distances. The software is designed so distances between features can easily be measured and features and attributes can be extracted and exported into shapefile or ASCII formats in various coordinate systems.
Topcon Europe Positioning business development manager for mobile mapping Sander Jongeleen said, "The new software really simplifies the IP-S2 datasets and makes the complex combination of high-tech sensor information easy to use and understand. Viewing colourful 3D point clouds overlaid with images makes the data easy for anyone to interpret, manage and export for use in many popular GIS and mapping programs. This development makes a very complex system simple for the user." Ball also believes that the new systems are simple to use and thinks that within a couple of years the technology will have developed to allow such systems to be easily integrated into the quarry manager's truck with automatic download to the web.
"It is revolutionary and relatively cheap too," he said. "A conventional tripod surveying system might cost around £20,000 but it requires specialist skills to use it and is time consuming. Dynascan costs around £60,000 but the productivity is unbelievable.
"A typical survey crew with a tripod scanner would take one to three days, depending on the size of the quarry, to collect and process the data at a cost of £1000 to £2000 per day. This new technology cuts the time to one hour with an unskilled operator.
"As the information is collected it is plotted in real time on a pc within the cab and a screen displays a visual guide to show which areas have already been mapped and which still need to be covered." Ball explained that processing is not currently automatic but there is back office software available for auto-recognition of basic features such as edges, crests and toes. He added that MDL is working on a video system that would enable identification of aggregate sizes within the stock piles.
"In a high workload quarry, such a system could give shift reporting," he said.
Ball believes that the scanning technology is likely to spread much faster than lasers have. "Lasers are widely used in the UK but are not so common elsewhere in Europe," he said. "They are used by maybe 10 to 15% of the sector in the US. However, this new generation of scanning will gazump lasers and I think the industry will now go straight to investing in mobile mapping.
"The consolidation of the industry in Europe means that there is a larger market for auditing and control. Back in the 1980s the industry was more dominated by family-owned enterprises where people knew what stock they had and where but now with more multi-national operators, there is a real need to monitor assets and have greater information control for financial applications." Nonetheless, further scanning technology developments are being made and
While the choice between vehicle mounted scanning or tripod based scanning systems may come down to initial cost, it is clear that surveying can now be carried out more simply and offers huge potential to improve planning in quarries.