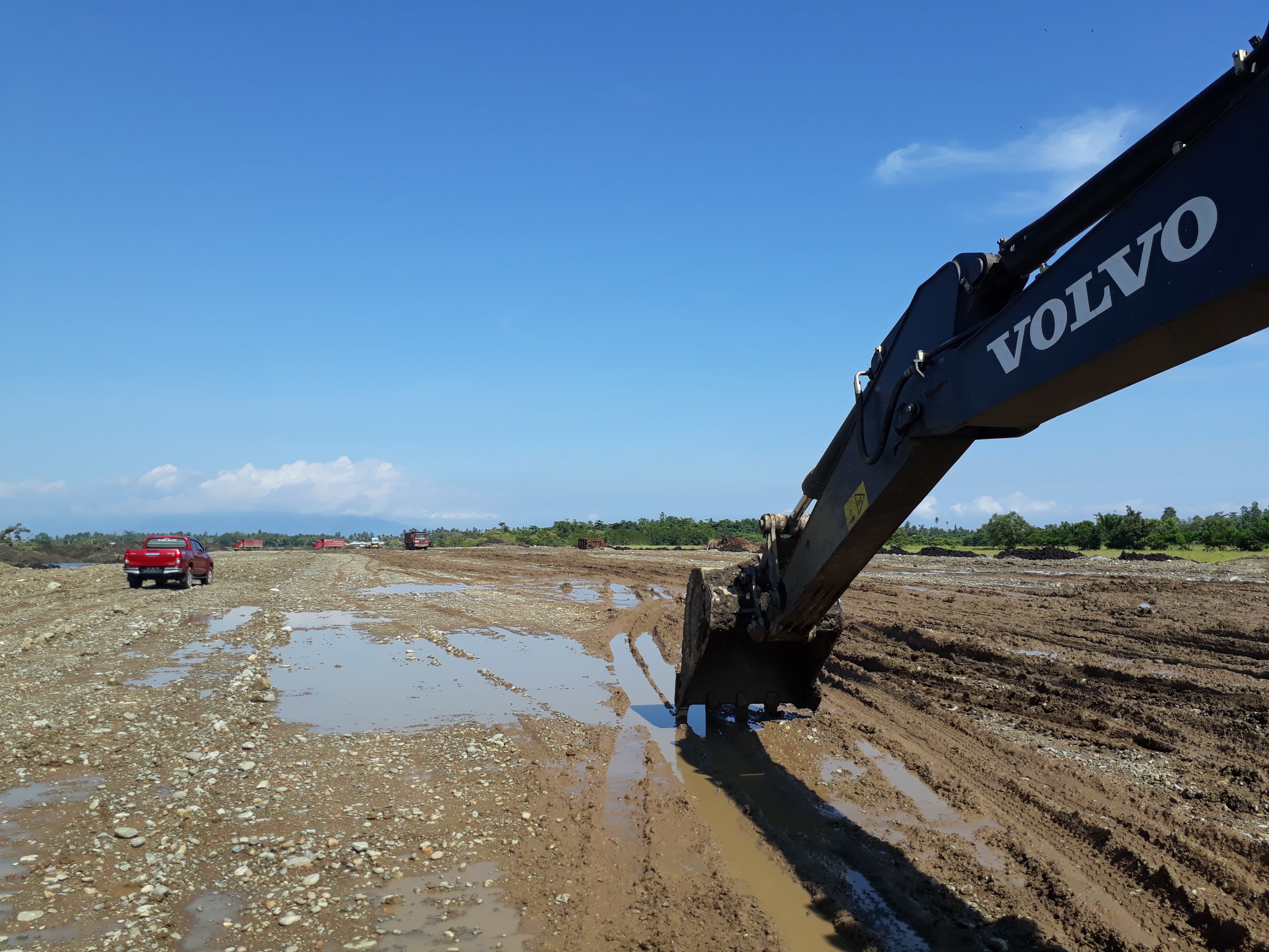
Loading models are making a major contribution to a key South East Asia-based infrastructure project while also proving their worth in a Dutch ‘urban mining’ operation. Guy Woodford reports.
Torowali Regency in Central Sulawesi, Indonesia, was only accessible via land or sea until March 2017, when its first airport was completed. Now, to accommodate larger aircrafts, a fleet of
“We are working under a tight five-month deadline to complete the runway extension, so we need durable machines with high efficiency—that’s why we selected the EC210D excavator,” said Ahmad Hakim Abdul Rauf, director and owner of PT Putra Morowali Sejahtera. “The Volvo excavators consume less fuel and provide superior performance. Plus, the aftermarket support from our dealer gives us the peace of mind we need.”
Four EC210D crawler excavators are helping to expand the Morowali Airport runway from 1.3km to 1.8km. This will not only accommodate larger capacity planes but is also in anticipation of greater future flight demand.
Designed to increase productivity and reduce fuel consumption, the robust EC210D crawler excavator features a maximum bucket capacity of 1.22m³, a maximum slew speed of 12.3r/min and a maximum slew torque of 76.7kNm. The model is equipped with a four-cylinder Volvo D5E engine. PT Putra Morowali Sejahtera purchased the EC210D excavators from PT Intraco Penta Prima Servis (IPPS), Volvo CE´s distribution partner for the Sulawesi region.
In addition to helping improve air access in Morowali, seven EC210D heavy-duty excavators are working as utility machines at a smelter plant. Three EC210B, the predecessor to the EC210D, are helping to produce an average of 7,500tonnes of stones daily at a river quarry. On both the smelter plant and the river quarry, the excavators work a minimum of 10 hours in challenging and demanding conditions.
The EC210D can be equipped with either a top or side mounted Volvo hydraulic breaker built to break even the most demanding materials, delivering consistent power and high breaking force. The Volvo-designed hydraulic breaker/shear piping and quick coupler piping option provide optimum flow to the hydraulic attachments. State-of-the-art auxiliary lines allow the correct flow and pressure for special attachments.
“At both the smelter plant and the river quarry, machines work with abrasive material, which quickly reduces bucket teeth and affects the undercarriage. But with the EC210D excavators we’ve experienced fewer breakdowns—they truly are higher performers,” said Rauf.
A fleet of
During its ‘urban mining’ process, Heros extracts ferrous materials such as iron, and non-ferrous metals such as aluminium and copper, from incinerated bottom ash. The remaining material forms the basis for the production of high-quality secondary aggregates, used, for example, in road construction or concrete products.
On the challenging 45-hectare site, the Hitachi machines are used to carry out a variety of tasks. The ZX350LC-6 medium excavator is used to open up the stockpiles of incinerated bottom ash, which can be stored on site for three to six weeks. One of the ZW310 wheeled loaders takes material from the pile and transports it to the feeder of the separation and processing equipment.
A ZW250-6 works in another section, where scrap metal is separated, while the company’s largest wheeled loader, a ZW370-6, is used to unload material from ships that dock in the adjacent canal. The smallest Hitachi wheeled loader on site, the ZW180-6, works for 16 hours a day in the 2,700m² non-ferrous upgrading facility.
“We chose the Hitachi ZW180-6 to work inside the plant, as it’s easy to manoeuvre and able to reach the height of the feeder,” said Peter David, head of machines and planning at Heros. “It’s also versatile for tidying the stockpiles, loading the machine and cleaning the floor.”
To ensure the highest level of support, the machines are provided with full maintenance and service contracts, and extended warranty from Hitachi’s local dealer Pladdet (a sub-dealer of Hitachi Construction Machinery Nederland), which is conveniently located 20km away. “Reliability and service nearby are the most important things for us,” said David.
Such demanding conditions require a fleet of the most robust and durable equipment. “It’s a very corrosive environment,” added David. “The bottom ash can stick to machines like concrete or cement. In fact, the reliability of the Hitachi machines in combination with the maintenance programme ensures we don’t incur any unexpected costs.”
The Doosan D-ECOPOWER system is said to provide a perfect illustration of Doosan’s commitment to combine new engine technology with advanced features and innovations that significantly increase performance and lower the total cost of ownership for customers.
In all of the latest ‘LC-5‘ generation excavators from Doosan, the combination of high pressure common rail fuel injection engines and the company’s Electronic Control Unit has served to optimise the performance of the diesel engine to achieve the maximum fuel efficiency.
The D-ECOPOWER technology builds on this by focusing on the role of the hydraulics system and demonstrates Doosan’s continuous iteration of all the processes and components utilised in the company’s new generation products to achieve claimed unprecedented levels of diesel energy efficiency.
Doosan’s D-ECOPOWER technology utilises an electronic pressure-controlled pump within a closed centre hydraulic system to accomplish claimed increases of up to 26% in productivity and up to 12% in fuel consumption improvements, depending on the mode selected. A closed central main control valve minimises pressure loss, while the electric pressure-controlled pump manages and optimises engine power more effectively.
The D-ECOPOWER system uses nine sensors to detect the amount of hydraulic oil necessary to accomplish a specific task and precisely meter the amount of oil required rather than continuously forcing a fixed amount of oil through the system, thereby improving efficiency. Software is utilised to electronically reproduce the full benefits of an open centre hydraulic system with very little energy loss. The hydraulic system and engine horsepower are said to be fully optimised and synchronised, further reducing losses within the system.
Improved feedback to the operator through the joystick results in better machine control and less operator fatigue. The acceleration and deceleration of the excavator workgroup functions are smoother, allowing operators to perform repetitive swinging and digging motions with less jerking movements.
The DX490LC-5 and DX530LC-5 are Doosan’s largest Stage IV compliant crawler excavators, providing significantly improved performance compared to the previous ‘LC-3’ Stage IIIB models.
The benefits of the D-ECOPOWER technology complement those already available on these two models. The DX490LC-5 and DX530LC-5 are both powered by the
Renowned for their excellent fuel efficiency, reliability and long service life, Scania engines combine exceptional power output with high torque at low revolutions. The Scania engine in the DX490LC-5 and DX530LC-5 operates at a much lower engine speed of 1800rpm, down from 2000rpm in the Stage IIIB models, leading to significant reductions in fuel consumption.
As well as the fuel-efficient Scania engine, new innovative and exclusive features have been introduced that together lead to huge reductions in fuel consumption amounting to an average of 6% to 13% compared to the Stage IIIB machines.