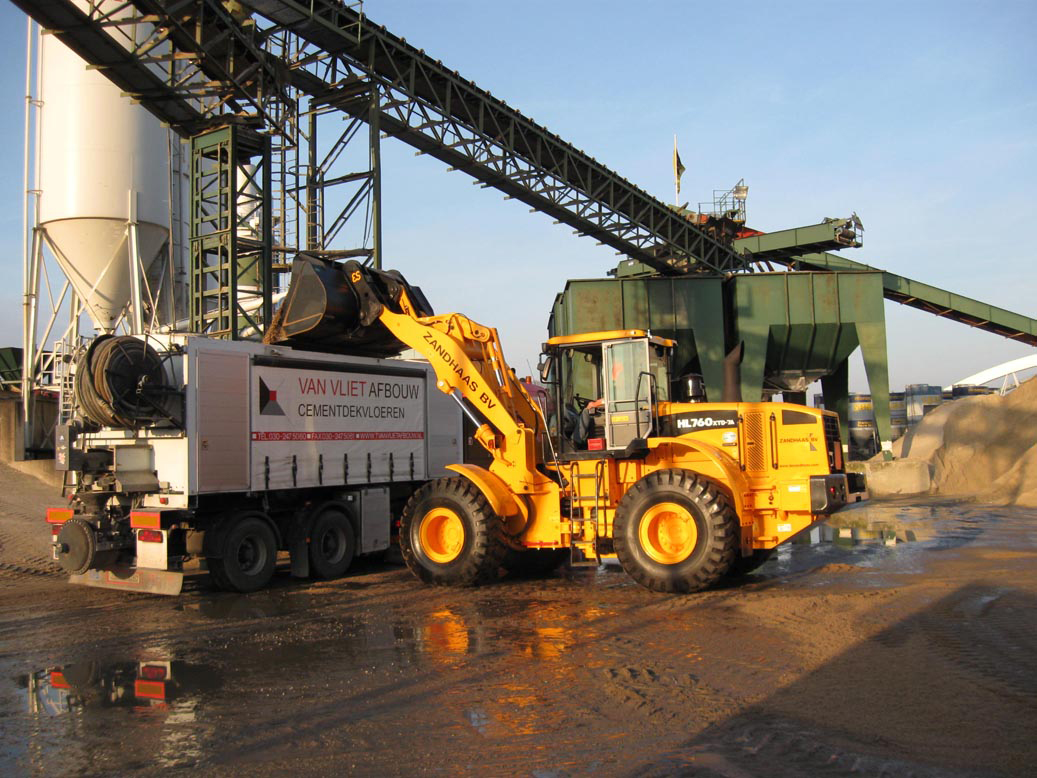
Wheeled loaders provide an efficient loading solution both at the quarry face and in the loading yard. ABE takes a look at the changing technology
The wheeled loader is a true quarry workhorse - it can provide productive truck loading at the quarry face or directly feed a mobile crusher hopper, as well as work in the loading yard. The addition of parallel linkage options on many models opens up a range of attachments that means the wheeled loader can also prove to be an effective house keeping tool.
While their benefits are widely known, the latest developments are helping to further improve productivity and reduce operating costs. "There is an ongoing quest to be more productive and efficient," said
"This is focusing on fuel economy, owning/operating costs and the cost
per tonne of aggregate moved." According to Rainey, many of the latest models demonstrate the significant improvements in efficiency that have been achieved. "They feature load sensing hydraulics that allow for a smarter use of power that reduces the draw on the fuel economy by minimising the 'parasitic' load from the hydraulics system," he said. "It allows for better on-demand power with systems able to quickly deliver rim pull and hydraulic power.
"Fuel management systems have also been introduced that can automatically sense where the machine is in the dig cycle and if power is not needed then engine revs are automatically dropped.
"Idle management allows machines to have a waiting phase that automatically lowers the rpm and then shut off the engine if it is idle for a pre-determined length of time."
Safety advances
"Safety has also been improved," added Rainey. "We are working on technology to warn the operator if the machine is close to an object. Vision cameras are also becoming standard. There has been a lot of focus on access and egress of wheeled loaders as we have identified that many injuries occur at this stage in machine use. Such steps have included improvements to hand rails and more ergonomic step designs." Wheeled loaders are seen as such a cornerstone of an equipment manufacturer's quarry offering that many more companies are entering this key market. In recent years
But the next significant move into the market looks set to come from
"These machines will be badged as Kawasaki but the agreement includes joint development of the next generation of machines - expected by 2011 - which will be badged as Hitachi models. The Kawasaki models we can currently offer will be the 28tonne ZW330, 33tonne ZX370 and 35tonne ZW550.
"The machines all have joy stick control available as an option and the majority of quarries do prefer this as it reduces operator strain and improves productivity."
Lean and green
Sustainability has also influenced the design of wheeled loaders and this is a concept that is gaining momentum. Such features include extending maintenance intervals, greener oils, lower engine emissions and recycling of wear parts and old machines.
"The latest engines have significantly improved emissions in terms of NOx and particulates and the next stage will tackle CO2," explained Rainey.
"The issue of new engines affects most equipment types, not just wheeled loaders and presents a big challenge to research and development having to introduce the new systems in one move. However, the next stage will deliver further improvements in fuel economy.
"Generally there are three different approaches - after treatment, in-cylinder and reburn systems. The approach for the quarry sector will be selected with the need for durable design with maximum up time in mind.
"Quality and reliability has to be a focus for this application. We have improved this in recent years with factory quality checks and assurance processes. The design is initiated with a virtual product development to check for motor failure, load, environmental issues and hours. This enables us to design to mitigate the risks and plan scheduled maintenance to prevent risks that cannot be designed out "The manufacturing process has to ensure that we get it right the first time. Quality comes next after safety and customers have high expectations, particularly those in the quarry sector." According to Rainey, operator optimisation is very important. "What the driver thinks of the machine may be make or break in terms of how the machine is used and the productivity achieved," he said.
"Designs make the best of skills with joystick control, modulating clutches and a general focus on finger-tip control to reduce fatigue. Cab designs have also been revised to reduce fatigue and iso-mount technology has been introduced to minimise transfer of vibration to the cab. Sound isolation and fresh air with filtration and air conditioning has further improved the operator environment.
"There is also a move to automate functions with auto-dig but there is more to come in this area."RSS