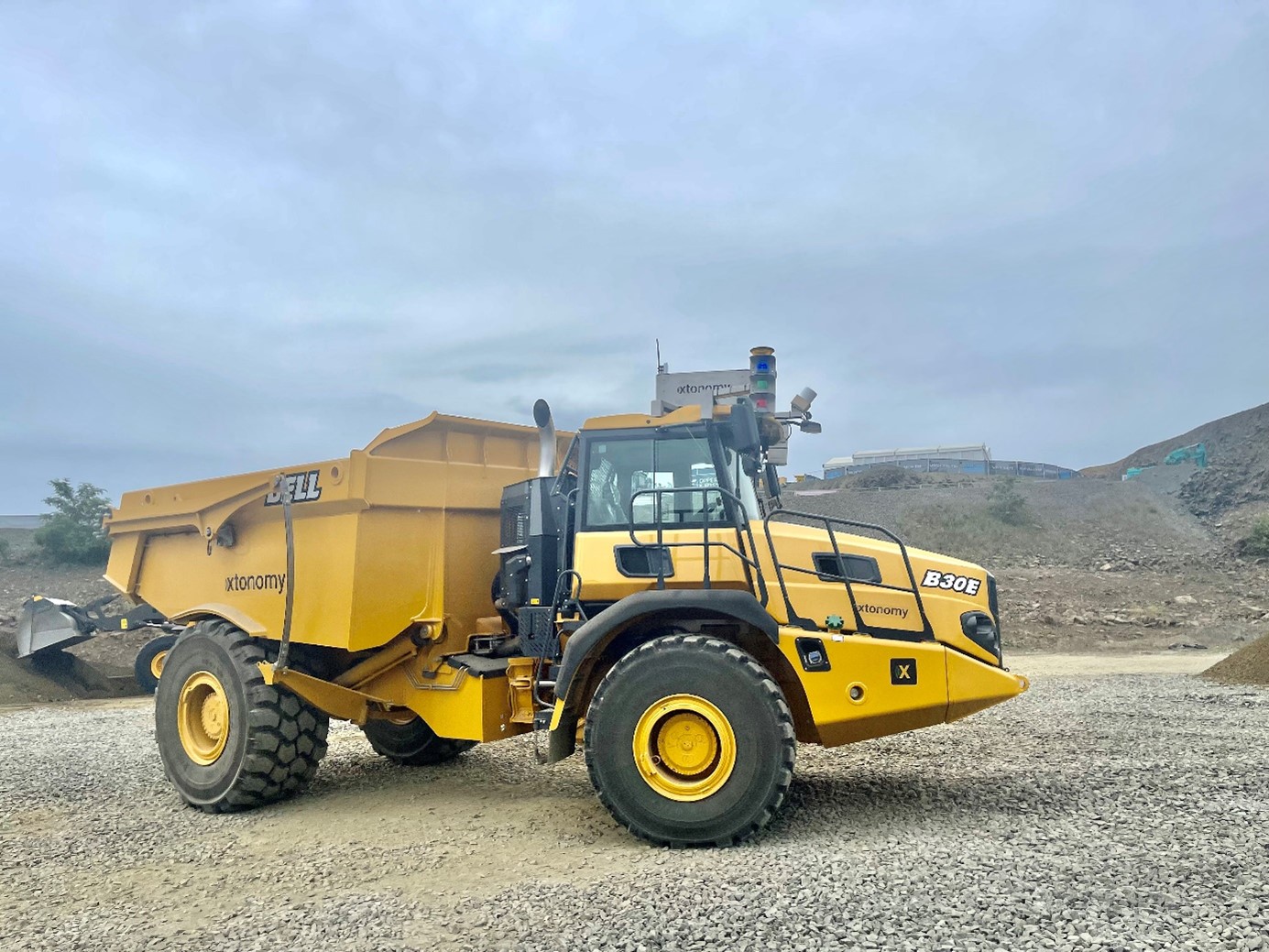
US-based technology company xtonomy says it provides the most advanced next-gen autonomous solution for mining and quarrying. In collaboration with Germany's Bell Equipment distributor, Kiesel, the firm recently illustrated its claim by demonstrating its fully operational autonomous haulage system (AHS) on a Bell B40E articulated dump truck (ADT) at steinexpo 2023, staged in Europe's largest basalt quarry in Homberg/Nieder-Ofleiden in the central Germany state of Hesse. Attendees at the five-day event (24-28 August) watched the articulated hauler making driverless cycles around the Quarry Vision area.
After many years of development, xtonomy AHS for trucks is now transitioning to full production. It is designed for smaller truck fleets that the excavator or loader operator may fully operate. Although the autonomous trucks automatically follow the excavator position on the bench and adapt the queuing position, cusp point and loading position automatically, the operator can adapt all points to assist the process further.
No additional personnel are required to supervise the fleet, as all underlying processes are fully automated. Robust radar onboard mapping and object detection continuously monitor the environment. At the same time, motion planners freely plan the best routes and dynamically react to changes instead of driving from one fixed point to another on virtual rails. Furthermore, xtonomy AHS handles the interaction of multiple trucks in such unstructured environments. This is only possible, the company says, through high autonomy at the highest system levels.

Several safety layers guarantee a safe operation with safe radio communications, high-precision GPS, radar and ultra-wideband (UWB) localisation. Manned machines may be integrated into the ecosystem for safe interaction in complex scenarios.
Furthermore, the xtonomy autonomy system does not require uninterrupted coverage of high-bandwidth comms throughout the mine site. This dramatically reduces the system implementation effort.
Properly watered haul roads directly impact fleet cycle times and the ability to meet production targets. As haul-road dust affects safety and productivity at mines and quarries, the water truck is one of the site's most important support equipment. The new Cat 777 (05) Water Solutions Truck provides an integrated solution to help reduce haul-road dust by solving overwatering and underwatering issues.
The new 777 (05) is built on the Cat 777E truck platform, proven at mine, quarry and construction sites globally. An innovative truck that uses less water for controlling haul-road dust, the design integrates the truck, tank, and water delivery system, connected with technology. Its Cat Water Delivery System (WDS) combines with Cat MineStar Edge connectivity to help operations manage the site more safely and productively with flexible levels of technology to meet site needs.
Boasting a 75,700-litre Cat-branded water tank, the 777 (05) has a spray system, splash guards, fill chute and rock ejectors. It is powered by the 765kW Cat C32B engine that meets China Nonroad Stage III emission standards, equivalent to U.S. EPA Tier 2.
The new water truck's exclusive Cat WDS features a self-contained hydraulic system that controls spray patterns independent of engine RPM for consistent watering. Based on the truck's speed, variable water flow automatically starts and stops when the truck slows or comes to a halt, preventing overwatering and subsequent poor traction at road intersections. The pump features soft startups and automatically shuts off when the tank is empty to prevent system damage.
WDS components include a water cannon, oil cooler, variable displacement pump, hydraulic oil tank, electronic control boxes and hydraulic motor/water pump. Covering up to a 24-metre wide road in a single pass, the system sprays at rates reaching 0.8 l/m² at speeds from 4 to 40kph (3 to 25mph). With its maximum 61-metre-spray distance, the truck's water cannon offers a maximum flow rate reaching 4732l/min.
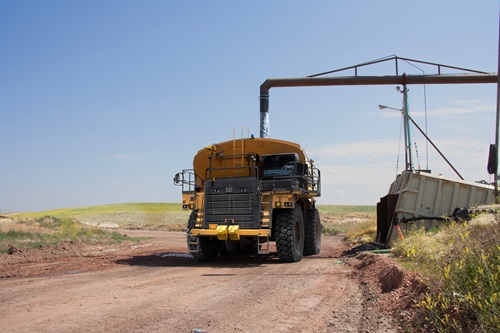
Factory-installed, ergonomic water controls are integrated into the truck's design for convenient operation. Its innovative automated water delivery feature enables the operator to focus on driving and site traffic to enhance safety. Complete with auto shut-off to prevent overfilling, the water tank is filled remotely, allowing the operator to remain inside the cab during the cycle to reduce potential operator slips and falls.
Flexible levels of the cloud-based MineStar Edge technology are integrated with the Cat WDS to collect and communicate machine data, allowing site supervisors to monitor the water truck to know where and when it's spraying water. Asset management options include productivity, water usage, fuel and water tank levels, when and where to apply water, geofencing, asset location, and remote management of water distribution.
Providing tracking capabilities without infrastructure investment, Edge Equipment Tracking delivers basic connectivity without interfering with existing fleet management systems. Helping to achieve a lower total cost of ownership, Equipment Tracking provides insights to help mines better manage their assets. It features service meter readings, fuelling and recording data, location accuracy and replay, time utilisation tracking with downtime and operator tracking, automatic stoppage measurement, and health event recording.
Paired with Equipment Tracking, MineStar Edge Production Recording delivers premium connectivity with an accurate and automated near-real-time measurement solution that reports on every aspect of the watering cycle without requiring operator input. Giving visibility to the entire operation helps to discover opportunities for improving productivity. This premium package also includes water usage by truck/fill station, volume and rate of water put down over time and area covered, water delivery system setting by location, truck, and conditions, activity breakdown with time and distance – watering, not watering, stopped, etc.
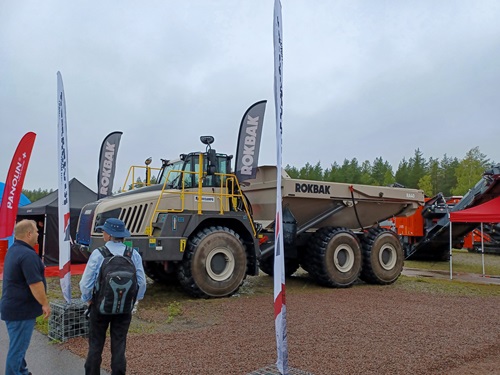
The Cat dealer and parts network fully supports this integrated system with Cat-branded tank options. Covered by the Caterpillar factory standard warranty, the water truck, including the tank and components, is eligible for Cat equipment protection plans (EPP) and customer value agreements (CVAs). Cat dealer installation of the integrated system is available, and retrofit kits for existing Cat 777E truck platforms in the field have planned availability in the future.
Rokbak's RA40 articulated hauler was showcased at this year's Maxpo (31 August – 2 September), Finland's largest exhibition of land construction and environmental maintenance machinery. Visitors got a close-up look at the RA40, courtesy of Kivisampo, Rokbak's trusted dealer in the Nordic nation.
As a biennial global exhibition, Maxpo presents 'the biggest and greatest machines' to almost 10,000 visitors at Hyvinkää Airfield, approximately 40 miles (60km) north of the Finnish capital Helsinki.
Kivisampo has been attending Maxpo for two decades. This is the first time a Rokbak hauler has been exhibited at the event since the rebrand in September 2021. The rebrand followed huge investments and improvements after the Volvo Group's 2014 acquisition.
"For us, Maxpo is a big deal," explains Kivisampo sales director Sakari Rantanen. "It's the time of the year when the customers come to you instead of the other way around. We're delighted to present the truck to the masses. Rokbak is still a relatively new brand, but, especially in the Nordic countries, Volvo is a name on everyone's lips, and the truck's Scania engine is very well-liked."
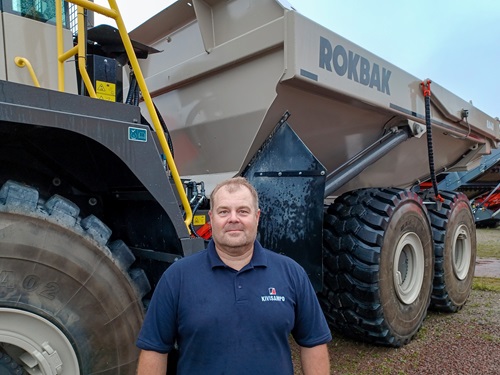
In the first half of 2023, the Nordics accounted for 16% of the European market for ADTs. This is a 52% increase in share compared with 2022. In the Finnish market, the over 35-tonne class is the largest sector.
The RA40 has been on demonstration in Finland and was introduced to the wider market at Maxpo. Arriving in a straight-to-the-point sand-coloured palette, the 38-tonne RA40 is a heavy-duty articulated dump truck that makes light work of large-scale quarry, mine and construction jobs. Offering reliability and performance, the RA40 delivers cost-effective productivity in the toughest conditions and roughest sites, from quarries and infrastructure developments to commercial construction projects.