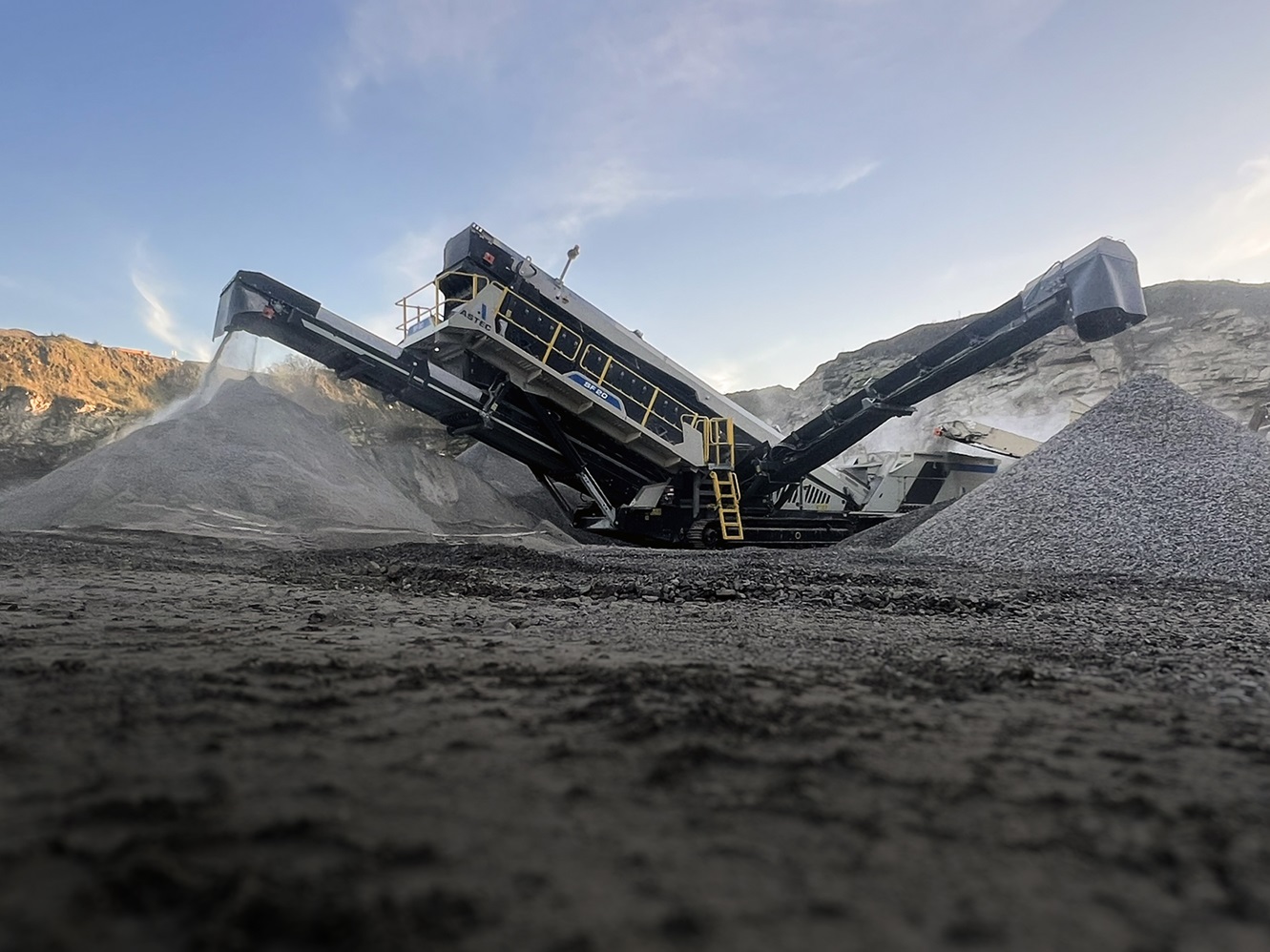
While many factors have contributed to the depressed global quarrying equipment market, the savviest original equipment manufacturers (OEMs) have continued investing in machine R&D, production capabilities, and international distribution networks. US quarrying and road construction giant Astec and its dry bulk material handling solution specialist, Telestack, are among the OEMs whose future-proofing endeavours leave them poised to prosper from renewed customer demand buoyancy. Aggregates Business reports
It is a very rainy day in late September 2024, and Aggregates Business is facing Damian Power, Astec’s managing director for Europe, and Malachy Gribben, Telestack’s commercial director, across the meeting room table at Telestack HQ in Omagh, County Tyrone, Northern Ireland. Their stark assessment of the state of the present off-highway equipment market mirrors the grim early autumn weather.
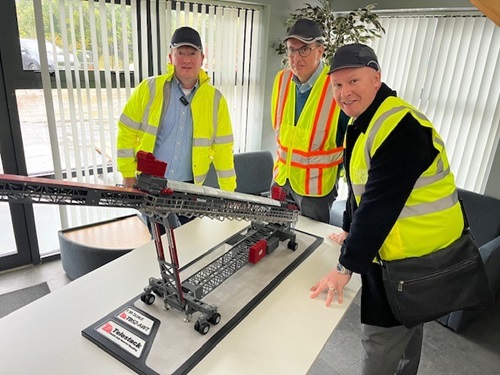
“I think the equipment market is 15% down year on year,” said Power. “On the Telestack side, we’ve not had big dealer inventories, as they would never carry big [mobile dry bulk material handling] rental fleets. We’ve been fairly judicious in managing that side of our SIOP [sales inventory and operational planning] process.”
Astec expanded into Northern Ireland in 2014 after acquiring Telestack. In 2023, the company finished the US$6.5 million 44,000ft² expansion of its Telestack-site-neighbouring Astec Doogary facility, bringing the total Astec Omagh footprint to 100,000ft². The extension took Astec’s total investment since its acquisition of Telestack to over $10 million, with the off-highway equipment manufacturer now employing over 230 people in Northern Ireland.
More than half of the global market supply for mobile crushing and screening equipment originates in Northern Ireland. As such, Astec’s enlarged manufacturing presence in Omagh will enable it to grow its international market business and better serve its customers and partners.
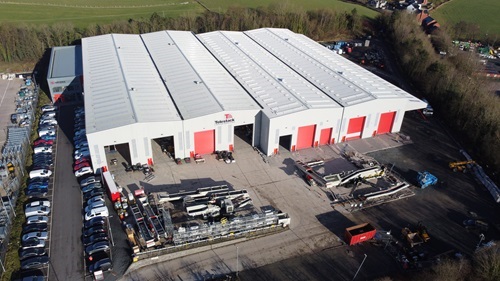
“We’ve only been getting out of the blocks in terms of building up our production capability at Doogary, so while we have had the same [depressed market] problem as others, it has not felt as big for us [Astec Europe]. We weren’t running the same [machine] build rates as some other manufacturers,” said Power.
“It’s tough, but we started planning for this market slowdown 20 months ago,” said Gribben. “With longer lead time items post-pandemic, it has taken our supply chain team time to adjust to our reduction in machine builds. We have a strong enough pipeline of work to think that the project side of our business will hold up next year. We appear to be in a better position than many of our peers.
“Astec’s tracked crushing and screening business will be bigger next year than this year, as we’re coming from a very low base,” said Gribben. “Let’s assume the global tracked crushing and screening market is not getting any smaller. The light switch will flick on again in our industry, probably in the second quarter of next year. Astec is already a proven supplier, so can we get our fair share of the market? Astec has not just started designing crushing chambers; we pioneered much of the technology that helped introduce chambers to the industry!”
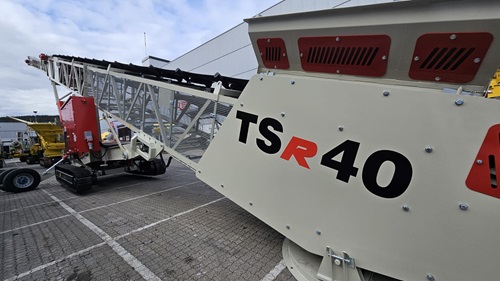
Attendees at this year’s Hillhead exhibition (25-27 June 2024) saw live demonstrations of Astec’s FT4250 HSI (horizontal shaft impactor), a popular US market crusher, and GT205 screener. Many exhibition goers also visited the manufacturer’s large show stand, where Astec showcased an extensive product range from its Rock to Road solutions portfolio.
Telestack was also at Hillhead 2024 with its highly mobile and versatile TSR 40 radial telescopic stacker. The only ‘Roll On – Roll Off’ (Ro-Ro) radial telescopic unit on the market, the TSR 40 utilises its radial, telescopic and luffing features to allow the operator full control and flexibility when stockpiling a range of materials. The addition of an integrated PLC stockpiling system eliminates segregation, degradation, contamination, and compaction of material. This is critical for maintaining the quality of your material during the stacking process. Telestack says the TSR40 offers up to 30% larger stockpile capacity than conventional fixed-length conveyor systems, with greater site mobility.
During the key quarrying equipment industry showcase, Aggregates Business spoke to Power and Michael Norris, president of Astec’s Materials Solutions division.
“All the machines you see here at Hillhead were manufactured in Omagh,” said Power. “The SF20 is our new 20” x 5” triple-deck screen, and the one we have here at Hillhead is fitted as a Rinser. The SF20 can be quickly converted from a dry screening to a rinsing configuration. It’s the first tracked mobile plant fully designed and built by our Omagh-based team. We also think there will be a good international market demand for the FT4250 tracked impactor given its success in North America today.”
“We have a stronger focus on Europe, and Damian was recently appointed our European managing director,” said Norris. “The machines we are designing and building in Omagh are specifically for the international market.”
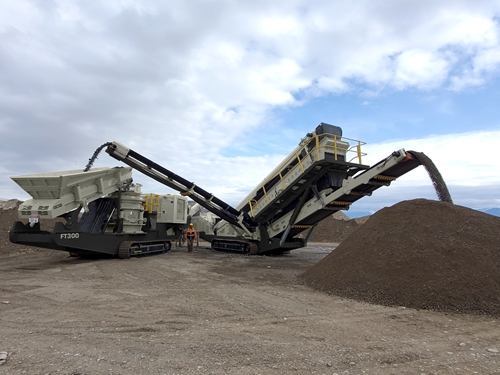
Asked about Astec and Telestack-branded machine production volumes at the Omagh facility, Power said: “The industry accelerated out of COVID but has cooled off. We are in a multi-election year across the world. We expect that the current [market] slowdown is temporary. We have invested in Omagh to grow manufacturing volumes there significantly over the next three to five years.”
“We want to increase production out of Omagh seven to ten-fold,” said Norris.
Has Astec found it hard to recruit engineers, welders, and other skilled workers to work at its Omagh facility due to the number of competitor OEMs [original equipment manufacturers] with a strong presence in Northern Ireland? “We have an employee-focused culture, and whilst recruitment is challenging for the industry, we are on a growth trajectory, and people can see that,” Norris replied.
“We are a unique proposition to employees in that we are high growth with a strong record in the [global] aggregates industry, in crushing and screening specifically,” said Power. “We are not just some start-up. We have substance behind us.”
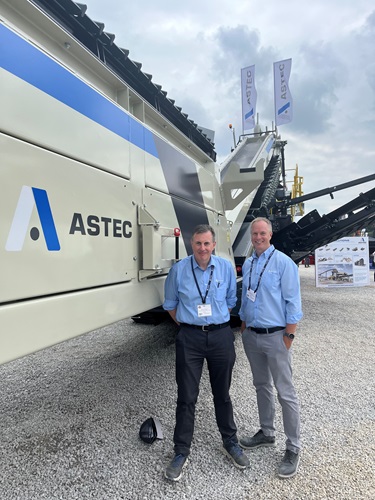
“We are an over 100-year-old company when it comes to crushing and screening. We have that expertise,” said Norris.
Among other Astec machines exhibited at Hillhead 2024 were the 3,000 tonnes per hour HF24 hopper feeder and the versatile, custom-built 220 tonnes per hour Kolberg 9225S sand plant.
“Part of our offer out of Omagh is going to be our washing product line,” said Power. “Astec has been in washing for many years, and there has been good collaboration between the US and Omagh teams to quickly bring the new [Kolberg 9225S] sand plant to the market. There’s a real opportunity to internationalise much of our washing product range, tweaking the proven designs of some of the washing modules to best suit European and international customers that tend to work in a tighter footprint than in the US.”
“Over the last couple of years, we’ve been delivering our strategic business plan focused on our employees and working culture and ensuring we are taking care of our customers and getting their feedback about our new products,” said Norris. “The innovation side and coming up with new products is the DNA of our company.”
Power told Aggregates Business that Astec is also reviewing how its existing European dealer network fits into its international growth plans.
Back at the meeting room table at Telestack in late September 2024, Power gives more details about how Astec and Telestack have adapted their global growth strategy to meet prolonged market challenges. “Eighteen months ago, we’d have said we need X amount of people on the [Astec Doogary] shop floor, but they’ve not been required, so we’ve not added employees. On the Telestack side, we’ve let natural attrition do its thing. However, we are still hiring the right people, and in the past six months, we have recruited industry-leading and proven leaders from the industry.”
“Hillhead was a real eye-opener for our potential recruits, from the shop floor worker to management roles and all in between,” said Gribben. “Attendees from local industry suppliers who may not have been as familiar with Astec saw us and recognised the opportunity to partner with us. It’s not because we had a lot of equipment there. It’s the good story we have behind it. They saw our latest crushers and know we’ve been in that game for 120 years, and we’ve been in washing since 1965.”
Asked to give more details on Astec’s approach to developing its European dealer network, Gribben said: “The channel network is always a fluid process. You need to supply it with a product range. That doesn’t get built in a day. We’ll have fewer traditional routes to market in the first couple of years until we build up the range. We’ll have a combination of dealer-led and direct sales and support. It will depend on the national market.”
Power said: “We have pockets of strength in Europe today, such as in the asphalt solutions and roadbuilding space with Roadtec’s Shuttlebuggy. I was recently with a Roadtec European distributor and a significant customer who both loved the Shuttlebuggy solution. There is some work to do with other products against some major competitors. I sense there is a hankering for a proven alternative or something new that our road technology or crushing and screening range could cater for. There could be quick wins with our modular machines and around parts and service.”
Gribben emphasised how a small number of producers dominate European aggregate production. “We think we can position ourselves so that if we’re sitting in a board room with one of them and talking to them about the solutions we offer, including bulk material handling, asphalt, concrete, crushing and screening, and washing solutions, they’d be thinking, ‘Well so-and-so can’t do this or that’. With the right support, we can give them everything they need now that Astec is expanding further within Europe.”
Gribben said: “If you look at Astec’s well-publicised growth aspirations, most of that growth is outside America. The company’s asphalt business market share in North America is +60%. It’s more about protecting and sustaining it. For the concrete plant business, it’s a +30% market share. On the other hand, Astec has a small portion of the asphalt and concrete market share globally, so those businesses must look internationally. You can’t only do that by building equipment in North America and shipping machines worldwide. You often need a production and aftermarket support presence in Europe and other big regional markets.”
Power believes Astec now has an even greater mindset. “Jaco van der Merwe [CEO] and Ben Snyman [group president – Infrastructure] have South African roots. Both have highly successful backgrounds in the global mining equipment and linked technology industry.
“Working in this part of the world [Northern Ireland], you can’t just have a domestic focus. If you don’t export, you don’t sell anything. It’s export or die.”
Power and Gribben stressed that the difficult off-highway equipment trading environment has not affected Astec and Telestack’s ambitious R&D programme. “Absolutely, yes,” said Power. “We’re committed to accelerating it,” emphasises Gribben. “On the Telestack project business, 50 to 60% of it is based on our product innovation.”
“We have a couple of PhD researchers based here in Europe that work within the Astec Digital Group,” said Power. “They are developing ideas around crushing chambers and material flows that our engineers and R&D teams are now looking at. I’ve got a regular touch point with them and was amazed at what they were doing. They are talking at some very high-level industry conferences. It doesn’t translate into today’s machines, but it’s shaping what we can do in the future.”
Power said that Astec’s machine presence at bauma Munich 2025 (7-13 April), the world’s biggest construction, quarrying, mining and recycling equipment exhibition, will be “limited” as the company focuses on building its Omagh-based operation. Telestack will be represented by its German dealers, C. Christophel and Kölsch Baumaschinen.
After a lively and insightful hour with Gribben, Power, and Mairead McCrory, Astec’s senior customer acquisition manager and Aggregates Business walked over the road to the Astec Doogary site. Elaine Mallaghan, Telestack's operations director, met us there and gave me a factory tour.
“We have our standard product production areas and NPI teams with dedicated engineering and supply chain specialists. We also have manufacturing engineers dedicated to fabrication sourcing, working out what we make and buy,” said Mallaghan.
On our way to a viewing platform offering a great view over the Astec Doogary factory floor, Mallaghan pointed out various production and training rooms. “We have 50 production staff here working on product assembly. Then there’s the office staff, stores, and materials people.”
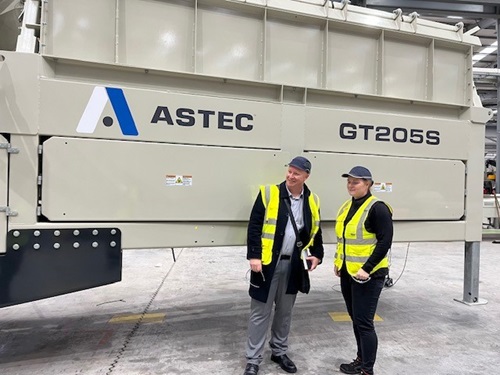
After reaching the viewing platform, Mallaghan highlighted various working areas. “That’s our tracked conveyor line, and next to it is sub-assembly. Then, we have a packing area at the bottom, handling containerisation. It’s mainly for Telestack products.
“The next production line is for crushers. Five different footprints are working at a time. Then we have the screeners and scalpers production line, with a sub-assembly and a testing area. We have our new stores area on the far side of the factory. We use Caterpillar engines in the crushers and screeners and some Deutz engines on the tracked conveyors. We have good relationships with both those suppliers.”
The Astec Doogary production team work either 7am to 4pm or 8am to 5pm shifts Monday to Friday. Mallaghan, who joined Telestack two years ago after a decade, mainly in operations, at Terex, said Friday afternoons and Saturdays can offer overtime work depending on product shipping demand.
After we pass a Telestack LF 523 tracked conveyor being assembled, we look at some crushing jaws and chambers that have arrived from the Astec plant in South Africa, where they are manufactured. “That chamber there is for a [GT] 440 [HSI - horizontal shaft impactor],” said Mallaghan, pointing at the chamber in question. “That other one there is for a [FT] 4250 [Fast Trax impact crusher.].”
With the rain still pouring down, we visit the outside machine testing area, where another Astec FT4250 HSI—the first Omagh-built units were demonstrated at Hillhead 2024—is waiting to be put through its paces.
“We do a full day's pre-delivery inspection [PDI] testing on every machine by our quality team. We look at functional running, production speeds and performance. The machine then returns to production if snags need to be smoothed out. New test units undergo wet testing onsite [before being prepared for customer dispatch].”
Before Mallaghan and Aggregates Business ended the tour with a picture in front of a nearly fully assembled Astec GT205S screener, she said: “The final parts of our recent investment have just been completed with an expansion of our entrance and completion of the surfacing of our external areas. After our 2023 and 2024 investments, we now have a large production footprint with significant capacity to increase our machine build run rates for multiple products in the future.”