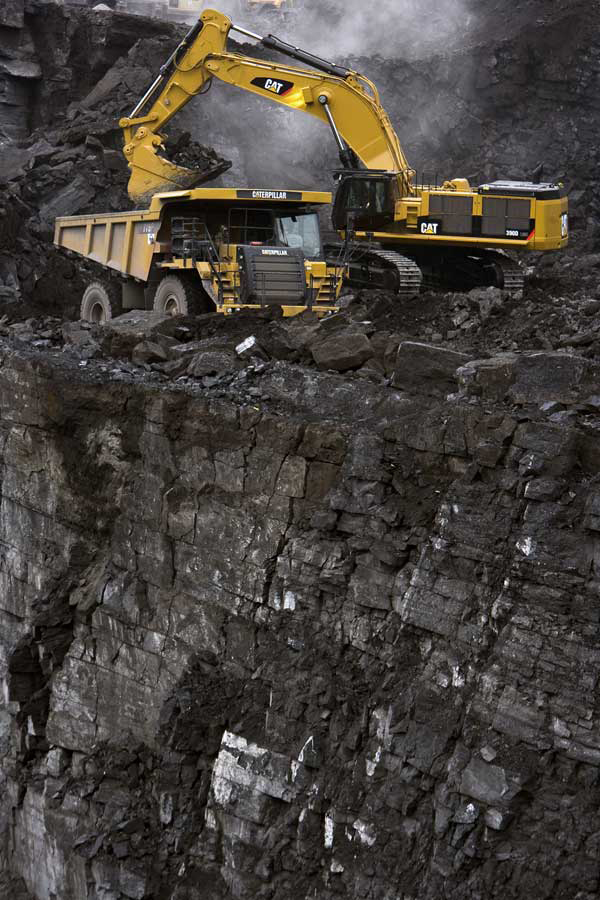
Design enhancements in the 390D L's implement hydraulic system allow the new model to deliver significantly greater digging and lifting forces than its 385C predecessor.
Main relief pressure in the new model's implement circuits has been increased to 35,000kPa, up nearly 10% from that of the 385C. This increase in operating pressure results in 9% more digging force, while the increased breakout force promotes faster and loading cycles plus stronger performance at the quarry face, according to Cat.
Also new in the 390D L's implement hydraulic circuits are electrically controlled regeneration valves, which assure rapid, positive response from the boom and digging arm cylinders while also significantly improving overall hydraulic efficiency.
The new machine is powered by a 18.1litre Cat C18 ACERT engine which is Stage IIIA 390kW engine. The engine's torque characteristics allow full power at maximum rpm, resulting in efficient hydraulic pump operation and positive hydraulic response. Refinements in the crankcase, cylinder heads and proprietary MEUI (Mechanical Electronic Unit Injector) fuel system provide enhanced performance and durability for the C18.
An improved undercarriage for the 390D L features redesigned links that operate with lower stress, forged idlers for improved durability and heavy-duty track rollers and carrier rollers. In addition, the recoil spring has been lengthened, giving the recoil mechanism greater impact-absorbing capability to protect the undercarriage system from shock loads.
To accommodate the higher digging and lifting forces generated by the 390D L, the carbody (the structure mounting the machine upper to the track assemblies) is fabricated with thicker reinforcing plates at critical locations. Complementing this change are thicker plates at the boom-foot mounting in the upper frame as well as thicker reinforcing plates in the rails and bottom pan to accommodate the heavier counterweight.
Booms and digging arms also are stronger - the result of thicker material used in their fabrication and an improved welding process. To assure continuous welds, with no craters at the start and stop of the weld pass that can induce stress, Cat has first tacked at each end of the runoff tabs of the seam between plates being joined. The company has said that when the weld is made, it begins on the first runoff tab, continues across the seam, and ends on the second runoff tab. The runoff tabs are then removed, leaving a consistent weld bead across the seam. When completely fabricated, booms and digging arms are placed in a heat-treat oven to relieve any welding-induced stress.
Specification
Manufacturer: Caterpillar
Model: 390D L excavator Operating weight: 88tonnes Power: 390kW
Lift capacity: 28.25tonnes
Special features: Improved servicing; More comfortable cab with improved displays; Advanced construction techniquesThe 390D L's operator's station is spacious, quiet and comfortable with commanding visibility.
The cab is pressurised to keep out dust, and the filtered ventilation system combines with automatic climate control to maintain a constant, comfortable environment. The monitor provides full-colour graphic displays with comprehensive machine information presented in either an English or
The monitor provides fluid level checks when the engine is started, can list approaching service intervals and display real-time fuel consumption information numerically. Flexible power modes - high power or economy - allow the operator to adjust machine performance to the task. Both modes provide the same digging forces, but the economy mode allows the machine to work with fuel-saving efficiency when production requirements are less critical.
Cat has also made a number of improvements to the service and maintenance operations on the new excavator. The new design features an electric fuel priming pump to simplify filter changes and a dual-element air cleaner with a double radial seal is also now standard. Service safety features include a 24-volt service light receptacle and wider, 500-mm walkways that provide sure-footed access to maintenance points.
To facilitate easier, environmentally sound routine maintenance, the 390D L is equipped with protected, valve-controlled fluid-drain ports and self-contained hoses for fuel, coolant and lubricant systems. Easy-to-change spinon filters are used in the fuel and lubricant systems, and pressurized fluid sampling ports (in all pressurized fluid circuits) assure reliable fluid samples. An electronic warning system alerts the operator if the air filter or hydraulic filter is approaching restriction limits.