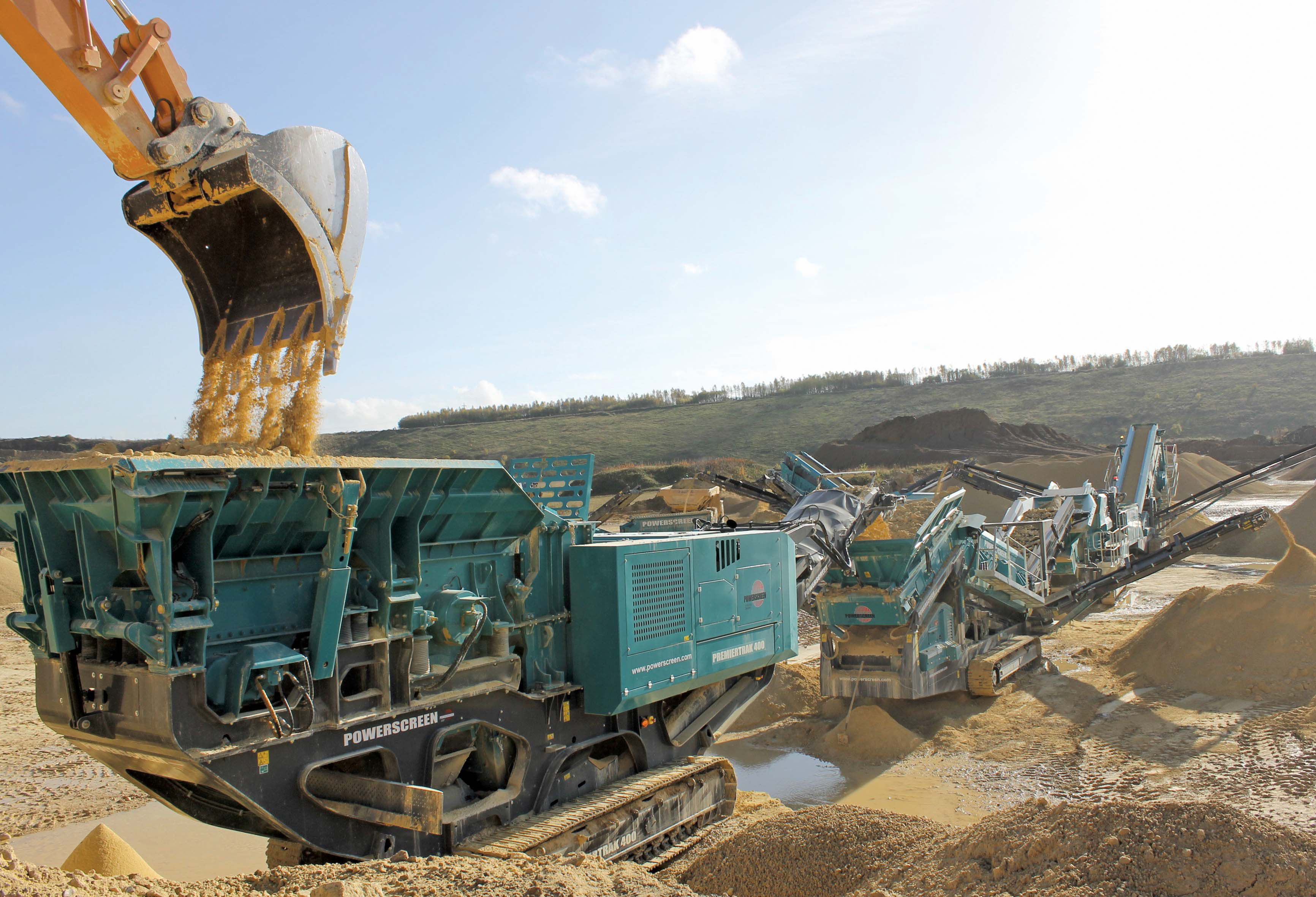
Crushing and screening equipment manufacturers have been overseeing the global launches of products as well as introducing new models and prototypes writes Patrick Smith.
The recent
“The Sandvik product offering now provides Chinese and Asian focused solutions for virtually any application, enabling such businesses as surface rock quarrying, excavation, tunnelling, demolition, recycling and civil engineering to improve their performance,” says the company.
Its global launches in the crushing and screening sector included the SK2462 screen while Chinese product launches were given to the CI532 impact crusher and the QI441 mobile Prisec impactor.
The SK2462 is the latest in the SK&SC range (available in sizes ranging from 1.5m-3m wide, 4m-8m in length, and in two, three or four-deck versions). A modular approach in the range allows flexibility for aggregate producers and quarries, offering accurate and efficient screening in the secondary and tertiary stages.
The new circular motion screen is 2.4m by 6m and weighs in at 7.3tonnes, and is powered by a 22kW motor, allowing rotation speeds of between 780-900pm. Dust encapsulation is incorporated to satisfy clean air regulations.
It can be deployed at incline rates of between 15° and 22° and the maximum feed size is 200mm with separation of between 1-30mm.
Maintenance was a key point in developing Sandvik’s new screens to minimise operational downtime, and the number of parts has been reduced and bearing lubrication improved. The vibration mechanism can be removed and installed as a fully assembled module.
Sandvik’s 29.65tonne Prisec CI532 horizontal shaft impact crusher has a throughput of 250-400tonnes/hour, while the company’s new QI441 mobile Prisec impactor works as a primary or secondary crusher. The QI440, said to be already proven for offering “superb” product shape, high productivity and ease of manoeuvrability, and the QI441 model is said to offer customers flexibility in primary and secondary applications through the use of the CI421 patented Prisec impactor box. Optional extras that allow the crusher to precisely match the demands of the customer’s specific application include a Doublescreen double-deck hanging screen with recirculation system.
Meanwhile, Metso has introduced its Nordberg GP7 secondary gyratory crusher, while LiuGong-Metso introduced the first prototypes of track-mounted mobile crushing and screening plants for China at bauma China.
The GP7 crusher includes a constant feed opening, steep cavity and seven strokes available as standard. The possibility to select a suitable combination from the strokes (25-50mm) is said to ensure perfect adaptability for any application.
Metso says that the 58tonne crusher can be fed with a large primary crusher such as the Nordberg C200 jaw crusher or Nordberg Superior primary gyratory crusher, and followed by a Nordberg HP6 cone crusher for tertiary crushing.
It features a feed opening of 450mm, which remains constant throughout the lifetime of the liners, said to be one of the most significant benefits of the new crusher.
“The steep cavity and easily changeable stroke ensures high performance when using a power rating as high as 550kW,” says Metso.
“Process control is based on an advanced Metso IC automation that provides easy, safe, and trouble-free operation.
“The Nordberg GP7 secondary gyratory crusher has exactly the same footprint as the Symons 7’ and similar crushers which makes replacement of an old crusher very easy.”
LiuGong Metso Construction Equipment (Shanghai), the joint venture funded by the LiuGong Group and Metso, has also introduced its first prototypes of track-mounted mobile crushing and screening equipment designed for the Chinese customer requirement.
The equipment is designed for crushing hard stones and recovering building materials with the main applications in project contracting, quarry, mine, cement, municipal road and bridge construction as well as construction waste recycling.
“Featuring high productivity, low fuel consumption, high reliability, high safety factor and easy operation, the new products can save energy and costs while protecting the environment and maximising the value created for customers,” says the joint venture.
In the north-east of England, six
Willowtree Site Services, a contract crushing and screening specialist, is in partnership at Coxhoe Quarry in county Durham with owners and operators
Willowtree, a Blue Machinery Scotland customer since the company bought its first Powerscreen rinser a couple of years ago, has made a major investment with Blue, buying the six Powerscreen crawler-mounted mobile machines which are now working the top bench at Coxhoe Quarry.
The Powerscreen set-up at Coxhoe comprises a Premiertrak 400 jaw and 1000
The high capacity Powerscreen Chieftain 2100X and Warrior 1800 screening plants have output potentials of up to 600 and 400 tonnes/hour respectively, depending on feed size, mesh size and material type, while the 1000 Maxtrak cone crusher can accept an all in feed, thereby eliminating the need for prescreening which would reduce the cubicity of the finished product. The Premiertrak 400 prescreen jaw crusher incorporates a fully independent high amplitude, hydraulically driven pre-screen with increased drop angle on the bottom deck to facilitate maximum throughput and capacity.
Chinese producer Shanbao has introduced a new track-mounted jaw crusher (designed and developed in the company’s factory close to Shanghai) that it will sell in both China and emergent markets.
Olivia Weng, international sales director explained that the crusher can be used in an array of applications in the cement, quarrying and asphalt sectors.
“We developed a mobile machine as it’s more versatile than a fixed plant,” she says.
The company is looking to expand its worldwide coverage, particularly in markets such as the CIS, Africa, the Middle East and Latin America.
Following Shanbao’s acquisition by Sandvik two years ago, the Chinese company has had more resources available for new model development, such as for the CT710J mobile crusher. This is one of three track-mounted crushers Shanbao now builds, with the range offering throughputs of 100-250tonnes/hour.
Power for the mid-sized CT170J comes from a
With the acceleration of urbanisation, abundant recyclable construction waste arises, which not only destroys the environment, but also wastes resources, says XCMG.
It is predicted that Chinese construction waste growth will increase in the next 20 years, thus aggravating the conflict between humans and land, environmental pollution and other problems during the urbanisation process.
According to XCMG, the sustainable development of concrete needs to be thought out seriously, and it is offering its new crawler crusher station PUF1214, which recently rolled off the production line.
The product marks XCMG concrete machinery’s next step in the environmental protection industry after releasing the ZSX150 and MS400K machine-made sand production lines and other green and environmental protection equipment.
The PUF1214 combines sand-making, stone-making and construction waste regeneration, and can transfer the original construction waste to renewable resources through receiving materials, crushing, sieving, deironing, transferring and other technologies.
In recent years, XCMG-Schwing says it has focussed on industry developing trend, enhancing the development of the green industry, being committed to the sustainable development of concrete and concrete machinery.
The company says it also is versatile enough for use across multiple industries and can process a variety of materials, including quarry rock, demolition debris, recycled concrete, recycled asphalt and base rock for oil fields.
The machine features a 1.5m x 4.87m double-deck screen, and has the ability to crush, screen and separate up to three different sizes of materials, two sized and one crusher run, at a rate of over 450tonnes/hour.
The crusher is powered by a