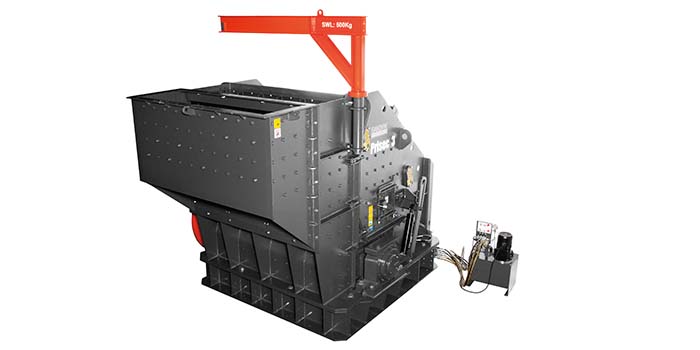
Many new crushers and screens have been launched onto the global market in the last few months, as Guy Woodford reports.
More than 300 international dealers and customers from over 90 countries travelled to London, England recently for
A full programme of events included the unveiling of new products, a business conference, live product demonstrations and an end-user open day.
The onsite demonstrations featured 20 recent product launches and prototypes of Terex Finlay models due to be released during 2015.
The three official new product launches at the event were the J-1175 dual power jaw crusher; the C-1540 dual power cone crusher; and the 693+ inclined screen incorporating innovative Spaleck screen box. The new trio join the 694+ dual powered inclined screen launched in 2013.
Built with significant energy savings in mind, the new products added to the 694+ screen allow Terex Finlay to offer operators a full mobile crushing and screening train that can be powered from mains electric, in addition to their self-powered option. In applications where a full train is powered by the onboard gen-set configuration, the crushers generate sufficient energy to enable the operator to run the 694+ dual power inclined screen for ‘free’ when used in conjunction with the J-1175 dual power jaw crusher.
The new 693+ inclined screen features a novel flip-flow top and bottom deck said to guarantee first class screening of wet, moist, and dry materials, and mixed materials including recycling and skip waste, fines material, compost, waste wood, timber, aggregates and ores.
Terex Finlay says the official launch of the new machines follows a stringent and strenuous development cycle which has seen them tested and proven in challenging and diverse product applications across Western Europe. In addition to these new product launches, the large number of prototype machines previewed included the J-1170AS Jaw Crusher.
The J-1170AS provides the flexibility of a crushing and screening plant on one machine. This ‘aggressive’ machine features a detachable onboard sizing screen that gives operators the capability of producing two spec sized products. The model was demonstrated working in a concrete recycling application and will be launched in Q1, 2015.
Nigel Irvine, Terex Finlay’s Sales & Marketing Director, said: “This event provided an ideal platform to showcase the significant level of investment in new product development across our entire range. During the conference, we outlined our aggressive new product road map, shared a clear vision of where we and our business partners should be positioned in the coming years, and reinforced our commitment to provide world-class products, supported by exceptional levels of customer service.”
Rowan Dallimore, Sandvik’s product line manager for Impact Crushers, Stationary Crushing & Screening Systems, said the Prisec 3 HSI’s offer numerous advantages, including impressive cubical shape; low operating cost per tonne; the ability to work with great efficiency as a primary or secondary crusher; the possibility of single stage crushing with the ability to recirculate material to the primary versions of the models; easy and safe crusher blockage removal; and impressive reduction rations through a new design crushing chamber and use of two innovatively designed curtains.
The CI531 can process up to 700tonnes/hour of material and has a maximum feed size of 1,000mm. The CI532 can process up to 400tonnes/hour of material.
The modularised style of the Prisec 3 range also means wear parts can be configured to offer longer life and deployed across the whole crusher range.
The Prisec 3 (larger) models come after the successful launch around two years ago of the Prisec 1 (smaller – CI511 and CI512 – up to 600mm feed) and Prisec 2 (medium-sized – CI521 and CI522 – up to 900mm feed) stationary crusher models.
As of mid-October 2014, 17 Prisec 1 and 2 models had been sold worldwide, with a CI512 improving crushing operational efficiency at the famous Koelga Marble quarry in Russia (as reported on in ABISep-Oct 2014). Dallimore says other Prisec 1 and 2 sales have included those to customers in Germany, Mexico, Oman and Egypt. The four models sold in Egypt were all to the Egyptian army, who are likely to take up an option to buy more.
“The Prisec crushers can be converted from a primary to secondary crusher, and vice versa, in just a few hours. They are very flexible and this has given us a good lead on the competition,” said Dallimore. “We are looking at the next generation of Prisec models, which will offer even more modularisation, so wear parts can be used over and over again. This will give us a huge advantage in meeting customer [wear parts] demand.”
Crush Ltd had been putting the 1150 Maxtrak cone crusher through its paces with extensive testing prior to its launch. At its quarry in Wales, Crush Ltd has been primarily using the 1150 Maxtrak unit for the crushing of gritstone to produce 6mm, 10mm, and 14mm chips on final products
“Typically, we had been using a crushing and screening train consisting of a jaw, two 1000 Maxtrak cone crushers and a Chieftain 2100X screen. When the 1150 Maxtrak cone crusher was substituted for the first 1000 Maxtrak unit, the plant’s output surged by an additional 30%,” said Crush “With the 1000 Maxtrak unit in this application, we had been producing around 1200-1300 tonnes per day. With the 1150 model, we are now at 2100 tonnes per day.”
Targeted at quarry operators and contractors alike, the 1150 Maxtrak model builds upon the success of the 1000 Maxtrak and 1300 Maxtrak models. It is said by Powerscreen to offer unrivalled performance, production and versatility.
The crushing action of the 1150 Maxtrak model is also said to deliver the same high quality product shaping synonymous with other Powerscreen cones. The machine will be offered in two configurations: a direct feed model and a pre-screen version which enables customers to handle dirty feed material and achieve higher production rates. With a choice of strokes and four liner options, all compatible with a single upper frame, the 1150 Maxtrak cone crusher can be easily configured for all applications. Feed sizes of up to 205mm are possible with the 225kW cone chamber, which is driven directly by a fuel-efficient 331kW Scania DC 13 engine that complies to the latest Stage IV emissions regulations.
Powerscreen says that one of the most impressive features of the pre-screen model is the patented hydraulic folding system, which converts the machine into a direct feed layout in minutes, delivering what the firm describes as unparalleled flexibility to the end-user.
The 1150 Maxtrak cone crusher is also designed with transport in mind, boasting a highly compact transport envelope which translates to savings on shipping costs and times. It weighs approximately 43.77tonnes, excluding options, and features two-speed tracking for excellent mobility.
The introduction of the Nordberg C130 jaw crusher continues the renewal of Metso’s proven, mid-size and large jaw crushers. Prior to the launch of Nordberg C130, Metso launched the Nordberg C120 and C150 jaw crushers.
The new C130 is a 40tonne operating weight jaw crusher which features the famous pinned and bolted design for reliability, long life and easy service. Metso says that reliability, crushing efficiency in stationary and mobile applications, and uncompromising
safety and ease of use have been the key parameters while designing this jaw novelty.
“Our C130 really stands out of the crowd with its bigger cavity volume. In fact, the cavity is larger in all three dimensions: deeper, wider and longer,” said Ilkka Somero, Metso’s Product Manager for jaw crushers.
The large, 1300 x 1000mm feed opening of the C130 jaw crusher is said to be able to process even the coarsest feed and maintain a trouble-free material flow through the crusher. This results in savings in blasting costs and allows the processing of coarser feed at the primary stage.
“This new design combined with a 160kW power range, a small nip angle and excellent kinematics ensures aggressive crushing along the whole length of the crusher cavity,” added Somero.
Thanks to the compact design, Metso says older crusher models can be easily replaced with the C130. The pinned and bolted design also makes it possible to disassemble the C130 and transport it even to the deepest underground mines.
Safety is one of the key focus areas for Metso when designing a new crusher. The C130 features optional, easy-to-open composite flywheel guards that allow quick and safe access to all service points. The standard delivery includes lifting tools for jaw dies, cheek plates and a toggle plate, all contributing to operational safety.
The Nordberg C130’s operating speed is 220rpm and the closed side setting between 100-250mm. The operational weight is 40.1tonnes, excluding options.
In addition to the composite guards, the new C130 can be customised to any application with options such as a wear-protected feed chute, an integrated motor bed with electric drive, a hydraulic setting adjustment, a rock breaker and a boom combination, and an IC1000 process automation package.