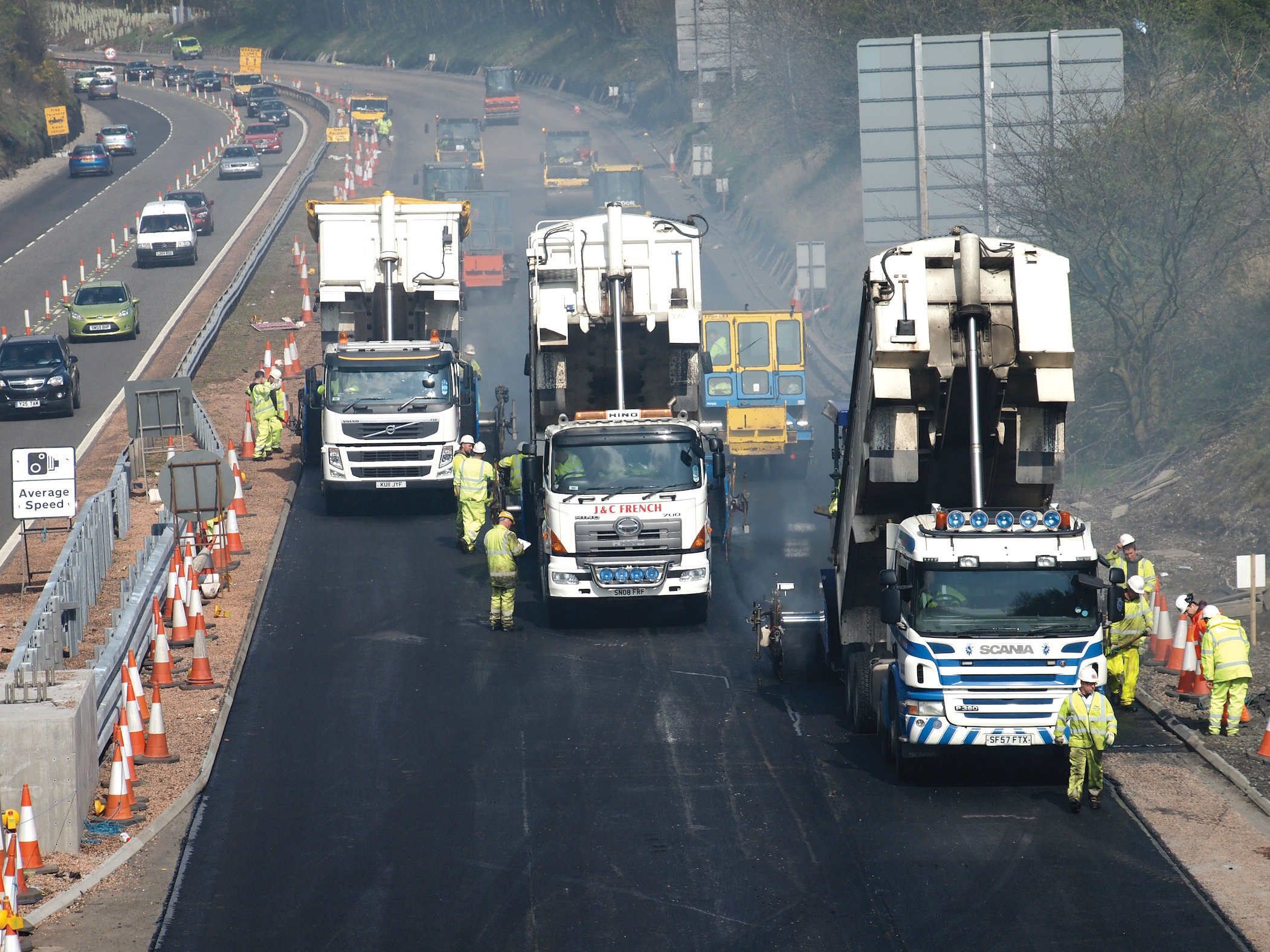
Advances in asphalt technology are leading to new mixes, such as one being trialled in Scotland. Patrick Smith reports
Developments in asphalt technology are helping to reduce emissions and make products cheaper to manufacture.
New additives and the increasing use of warm mix asphalts are all playing their part in the advances.
One example of this technology can be found in the UK.
A 3.8km section of the M90 motorway, north of the Forth Road Bridge, near Edinburgh, Scotland, has become the first stretch of motorway to benefit from a new specification aimed to improve the durability of SMA (stone mastic asphalt) thin surfacing.
The specification, TS2010, involves a four-stage approval process, the final one coming two years into a road’s service life.
TS2010 was developed from German standards, and requires gap graded aggregates, very high performance polymer modified bitumen (PMB) and gritting of the final surface.
For the
“This material is a highly polymer modified elastomeric binder with exceptional resistance to permanent deformation and cracking,” says Nigel Hardy, Nynas’ Scottish area sales manager.
“These characteristics mean it is well suited to the kind of durable asphalt that TS2010 is intended to produce.”
The specification’s four-stage type approval installation trial starts with the design phase, followed by a plant trial where the material is laid, and where destructive and non-destructive tests are carried out.
Stage three sees the design mix laid on the carriageway of a live road, and the final stage sees a final phase of testing after two years of live testing.
Nynas also supplied the binder, Nypave FX 20 to go into the EME2 (Enrobé à Module Élevé) asphalt for the contract. Nynas developed Nypave FX 20 for use in high modulus asphalts such as EME2, which is a high strength, long-life asphalt, used for the base and binder courses.
Echelon paving was used, with three pavers operating together to ensure hot-to-hot joint and further ensure long surface life.
The contract is one of three which makes up the Forth Replacement Crossing project, and involved upgrading the southbound M90 hard shoulder to a bus lane and associated pavement works, including total resurfacing of the carriageway.
Other elements of the Forth Replacement Crossing are the £790 million (€941.7 million) new Forth Road Bridge and connecting roads which joint venture contractor Forth Crossing Bridge Constructors (
According to AkzoNobel, Rediset LQ-1102CE is especially suitable for this type of paving as it improves mix workability during manual handling and reduces fumes and emissions.
“When talking to the paving crews I got a lot of positive feedback,” says Tomas Svensson, account manager for AkzoNobel Asphalt Applications.
The crews indicated that the mix was easier to work with compared to a standard mix produced at 165°C; it took compaction well; showed no signs of cracking and is less sticky to asphalt rakes and other equipment.
AkzoNobel says that by using Rediset LQ products as a warm mix additive when paving asphalt, this can be done at significantly lower temperatures than with regular hot mixes.
“The temperature reduction means less fuel consumption, saving energy and money,” says the company.
The Rediset LQ-1102CE-mix used at the National Arena is produced at 150-155°C in PEAB Asfalt’s plant close to Arlanda Airport, and then transported to the arena using two trucks.
On site it is unloaded into an open container with a plastic cover. The mix temperature measured with a probe is around 140°C inside the container. The mix is then transported with five small excavators up to the second and third floor where it is unloaded and paved manually with asphalt rakes at a temperature around 120°C.
The final step is compaction using a 1.5tonne roller without vibration, although a small vibrating plate compactor is used occasionally.
PEAB Asfalt started a trial with Rediset LQ-1102CE in July, 2012, and the first tests showing promising results for compaction and adhesion led to a decision to start using the product on a regular basis at one of its production plants.