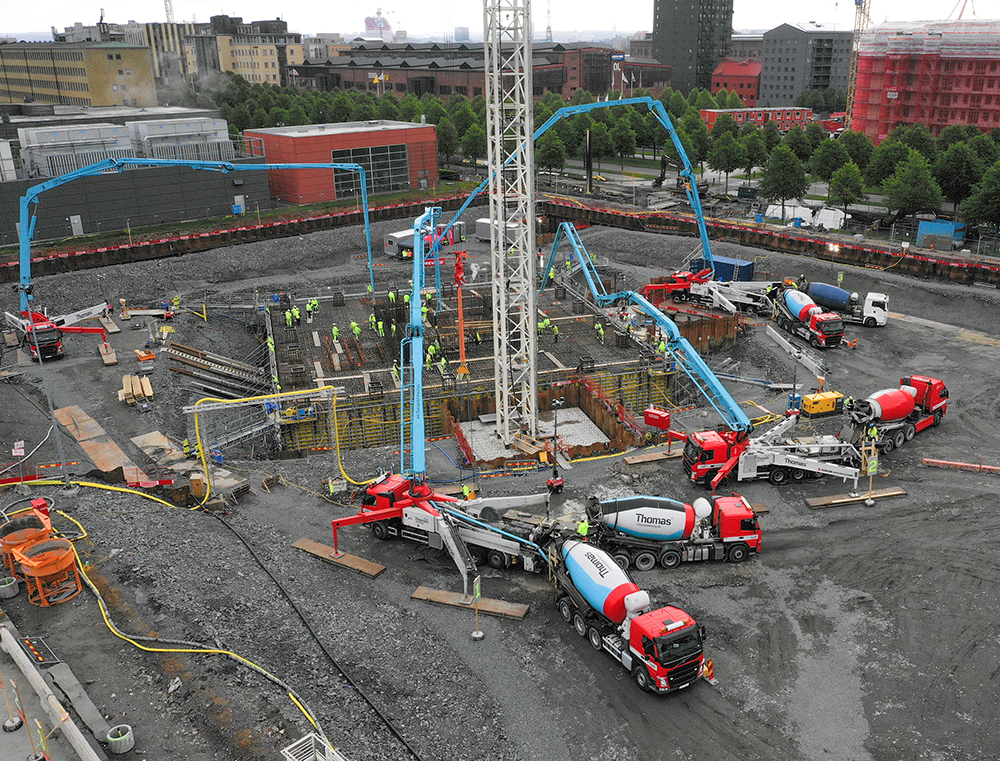
The Nordic region has always been a hotbed for aggregates production, with a thirst for production innovation and environmentally friendly quarrying practices.
However, like any other world region, the Nordic countries of Sweden, Norway, Denmark, Finland and Iceland and their building material suppliers and quarrying and construction equipment manufacturers cannot be totally immune from the impact of a contracting global economy.
On a positive note, Jonas Staaf, business director Hub North, Volvo CE, says healthy investment by Nordic national governments in major new infrastructure projects has left the region well placed to withstand current and forecasted future volatility in the global economy.
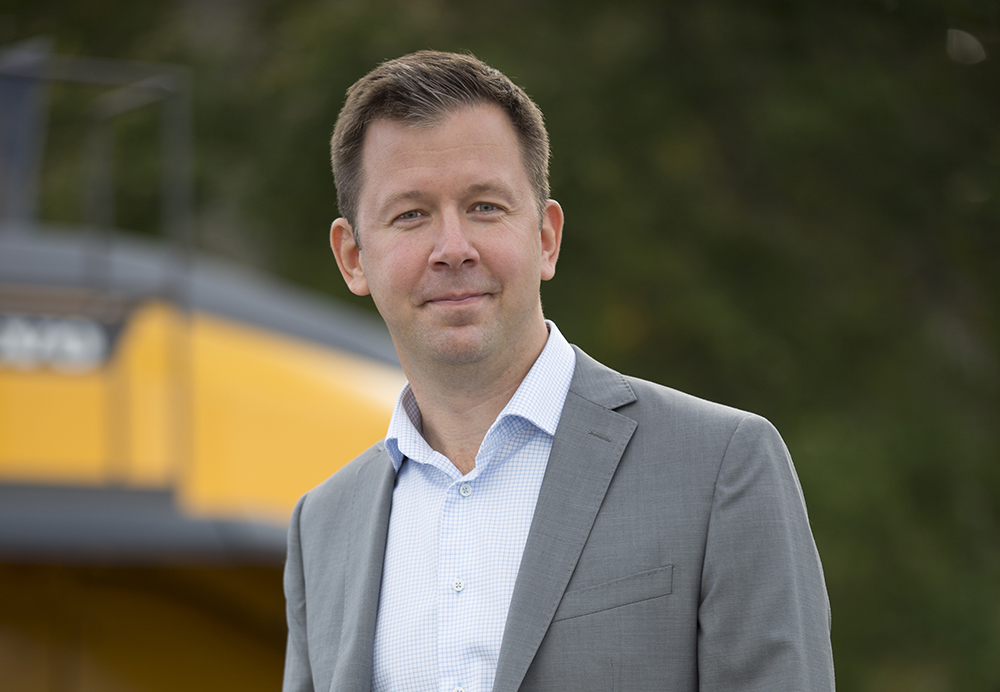
“New infrastructure and housebuilding are always the drivers of aggregates demand. Housebuilding is not as strong as it was due to prices levelling out,” Staaf told Aggregates Business Europe during a recent visit to Volvo Construction Equipment’s (Volvo CE) key Eskilstuna facility.
Staaf says Volvo CE is among original equipment manufacturers (OEMs) that have been supplying machines for several major new infrastructure works in the Nordics, including the Stockholm bypass project. Due to open in 2025, the new 21km-link, which includes just over 18kms of road tunnel, will connect the southern and northern parts of the Stockholm county, relieve the arterial roads and the inner city of traffic and reduce the vulnerability of the Stockholm traffic system. When the link opens for traffic it will be one of the longest road tunnels in the world. By 2035, the Swedish Transport Administration (Trafikverket) estimates that the Stockholm bypass will be used by around 140,000 vehicles every day.
Staaf continues: “Another big infrastructure project in Sweden that we are supplying equipment to is the West Link project, which is modernising the railroad connection in Gothenburg, making it double-track. There are also plans to build a high-speed rail connection between Stockholm and Gothenburg. These kinds of projects require a lot of ballast, concrete and asphalt, which is good business for quarries. We sell a lot of wheeled loaders, such as L180s, to quarry customers.
“Norway’s infrastructure project pipeline is also absolutely massive. They tend to divide their projects into SEK 3-5bn- (€275mn-€460mn) sized works which can be handled by medium-sized construction companies. This kind of ongoing and pipeline projects is why we feel that there can be something of a soft landing in this region which can help it cope with any changes in the global economy.”
In November 2018, Volvo Construction Equipment and its customer Skanska revealed groundbreaking results at the end of the first stage of their Electric Quarry Site research project. The 10-week study at Skanska’s Vikan Kross quarry, near Gothenburg, which incorporated the use of electric and autonomous prototype Volvo CE loading and hauling units, showed a 98% reduction in carbon emissions, a 70% reduction in energy cost and a 40% reduction in operator cost. As reported elsewhere in this issue of Aggregates Business Europe, the second stage of the Electric Quarry Site research project is due to take place in 2020.
Staaf thinks that Nordic quarry operators are becoming more aware of the need to reduce their carbon footprint due to the volume of new regulations in other areas of the building materials supply and deployment chain, as well as high-profile projects such as the Electric Quarry Site.
“I think there is a positive knock-on effect. For example, the Norwegian government board that looks after new roadbuilding has set a new target to reduce CO₂ emissions by 40-50% by 2030. There are also more local things that quarry operators can look at for the long term like having the right engines in their machines. Sometimes regional government departments or quarry customers will want to only buy engine emissions-standard compliant machines.
“We are also finding that more of our quarry and other sector customers are taking out not only machine service and repair agreements, but also more packages where we look at helping the customer become more efficient. This might be through, for instance, analysing fleet fuel efficiency and ECO-mode machine operation. Optimising machine uptime is also, obviously, a key consideration for customers.”
According to UEPG (European Aggregates Association) latest available figures, Norway producers (companies) produced 122 million tonnes of aggregates in 2017 – up an eye-catching 32.7% from 82 million tonnes in 2013; Sweden’s producers produced 98 million tonnes (+22.4%); Finland’s 80 million tonnes (-6%); Denmark’s 52 million tonnes (+33%); and Iceland’s 3 million tonnes (same as 2013).
Headquartered in Gothenburg, Thomas Concrete Group is an SEK 6.5 billion (€635mn) annual turnover business with a footprint of 154 ready-mixed concrete plants in five trading countries – 79 across Sweden, Norway, Germany and Poland, and 75 in the USA.
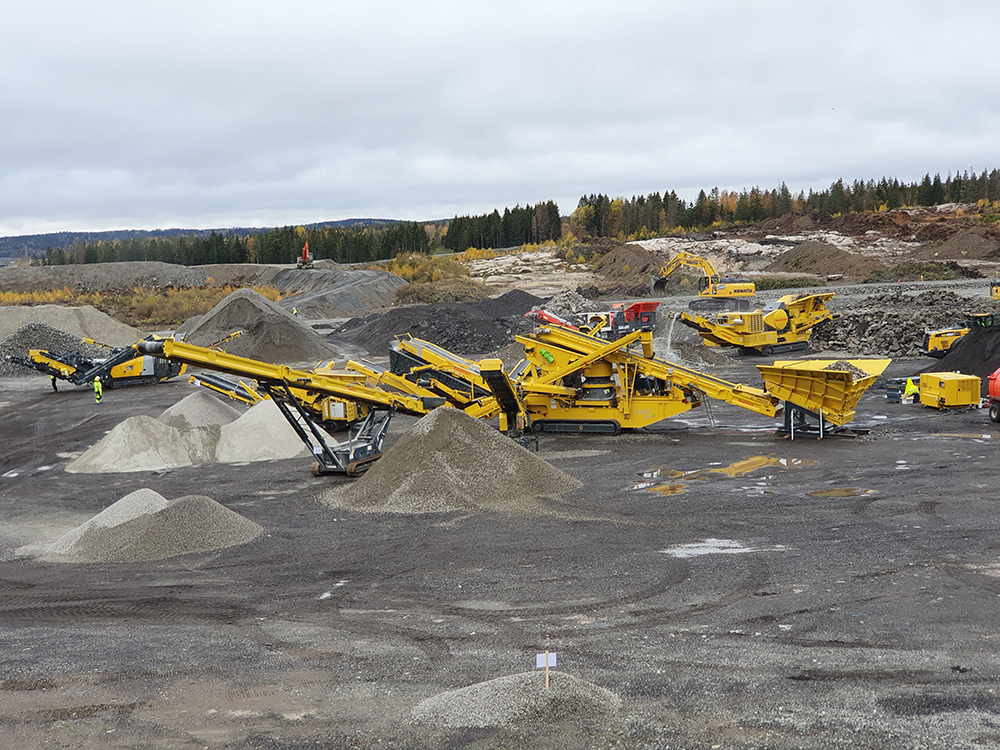
“When you look at Sweden, the residential construction side of building materials demand has declined quite a lot in the last two years,” says Hans Karlander, CEO and president of Thomas Concrete Group, which operates the Thomas Betong AB subsidiary in Sweden. “The residential property market is down 30-50% in the Stockholm area, down an average of 20% in Sweden, but actually stable in the Gothenburg area. Generally, the apartments which have been built in the big cities are relatively expensive. There is a high demand in Sweden for apartments but, mainly, at a lower price level. I think property developers are pursuing slightly higher [profit] margins associated with more expensive city apartments and are waiting for the economy to stabilise, before building more lower-priced properties.”
Like Staaf of Volvo CE, Karlander says building materials demand is much healthier when it comes to infrastructure works. “There is a high level of infrastructure projects in Stockholm and Gothenburg – Sweden’s two biggest cities. For most construction companies, this is good. However, when it comes to the suppliers of building materials to these companies, the margins are going down, simply because the pricing competition among suppliers in this market sector is much higher.”
In Gothenburg, Thomas Concrete Group is supplying ready-mixed concrete to the Marieholm Tunnel project. Due to be completed in 2020, the tunnel is located 5km north of Gothenburg city centre and will relieve the burden on the Tingstad tunnel, reduce the vulnerability of the road system and connect the Partihall junction, Marieholm junction and Tingstad junction to each other. Thomas Concrete Group is also supplying special low-carbon concrete to Gothenburg’s West Link project, which includes a new underground railway station.
Karlander says the Norwegian residential construction market is much more stable, with major national infrastructure projects in abundance. “The big infrastructure projects there are proceeding at a high pace, both along the coast and also in the metropolitan cities.”
Karlander says Thomas Concrete Group trading was “quite good” over the first eight months of 2019, mainly due to a significant increase in sales in the U.S. “This has been helped by much better weather there this year,” he explains.
Thomas Concrete Group has this year again introduced two new lower C0₂ footprint Thomas-branded concrete products. Karlander says the group will launch more in the next couple of years, given the demand among customers in Sweden, Norway and its other national trading markets.
“We’ve launched Thomacrystal in Poland and we’re just about to launch Thomagreen in Sweden. The Thomagreen product is more based on the use of alternative binder material to lower its C0₂ footprint.”
Looking at the mid- to long-term prospects for the Thomas Concrete Group and the wider building materials sector in the Nordic region, Karlander says: “The global economy has passed its peak. At the same time, it is very uncertain how market demand will shape up in 2020 and beyond. As a group, we have invested in more digital solutions and reshaped our internal business systems in order to become much more efficient going forward.”
Keestrack, the Belgium-headquartered global crushing and screening plant market manufacturer, notes that natural stone is Norway’s biggest export product in volume – with only oil a bigger export product in terms of value. As the global demand for aggregates is rising, Keestrack says the demand is also rising in the Nordic countries.
Fredheim Maskin sells and services Keestrack tracked-mobile crushing and screening equipment in Norway and Sweden and works closely with customers on their specific needs. The company recently staged a granite quarry demonstration of key Keestrack plant models during its 10th Demo Days event in Spydeberg, near Oslo (see this issue’s Aggregates Production feature for more details).
“The Norwegian government and the general public are very concerned about their environment,” says Marcel Kerkhofs, Keestrack marketing manager. “Ensuring a zero-carbon footprint and environmental protection has high priority, especially when operating aggregates material processing plants in and near an urban environment. This is one of the reasons why our hybrid and electric plug-in plant solutions are popular in Norway. The additional higher investment for the electric-drive systems is earned back very quickly.”
Keestrack says replacing hydraulic drives on conveyors, screen shafts and crusher drives with electric motors negates the need for long oil piping with leak-prone hose connections. Thermal problems during applications in extreme conditions are also eliminated.
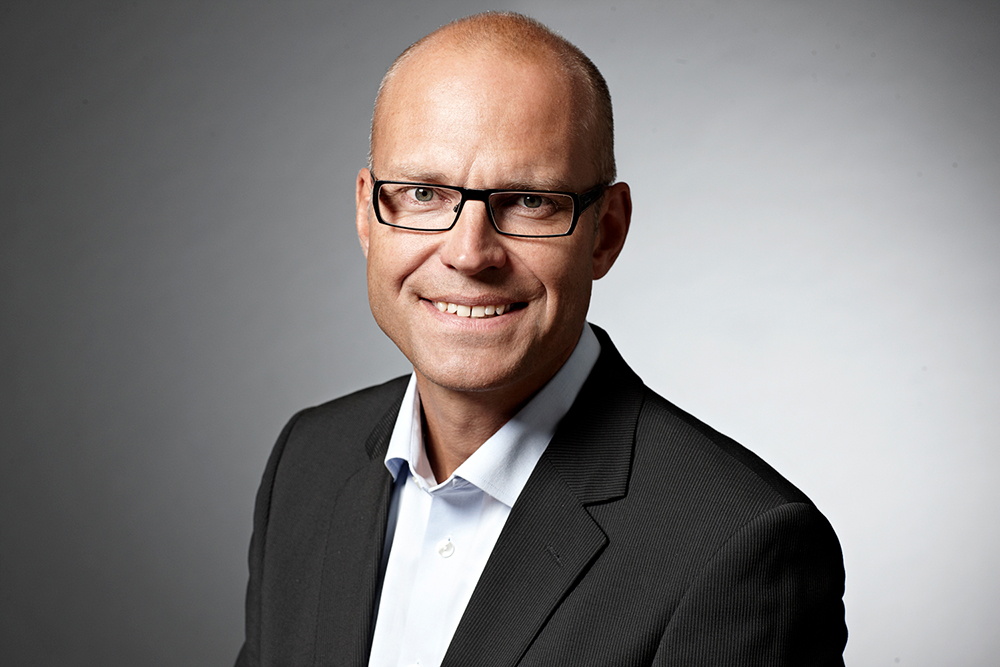
Kerkhofs continues: “With significantly lower oil quantities and extended change intervals, the smaller hydraulic systems of Keestrack’s ‘e’-versions not only save the environment but also real money. In full-electric operation, this also applies to lubricants, filters and other wear parts of the onboard diesel. Less engine hours mean less maintenance and downtime, which has a positive impact on total cost of ownership, as well as the higher value retention.”
Kerkhofs also stresses how engine problems on a diesel-hydraulic crusher can stop the whole production or job site. He concludes: “With a plug-in hybrid machine, a total breakdown can be avoided by providing an external gen-set to ensure the completion of a project without delay.”
Headquartered in Stockholm, Sweden, Epiroc produces innovative surface drill rigs, rock excavation and construction equipment for quarrying, mining, infrastructure and natural resources industry customers in more than 150 countries.
Commenting on Nordic region aggregates and quarrying equipment demand, a company spokesperson says: “The last three years have seen demand at a steady high level. The housing market is uncertain but government-related infrastructure projects are being rolled out. We see the market continuing steadily but not increasing.”
The spokesperson says that the driving force behind equipment sales in Sweden and Finland has been surface mines investing in Epiroc’s SmartROC D65 surface drill rig. “We have seen an increasing interest in automation technology, such as our BenchREMOTE system,” adds the spokesperson. “Swedish and Finnish quarry operators are also looking to be climate smart, locating their sites close to the consumer so that transportation is kept to a minimum, reducing the environmental impact. This increases the need for surface drill rigs with noise reduction.” The spokesperson says this, for example, has led to almost eight out of 10 deliveries of FlexiROC T35R surface drill rigs to Swedish and Finnish quarry operator customers featuring a noise reduction kit.
Epiroc equipment is also being deployed in Greenland, where Munch Engineering is building two airports covering an area of 9 million m³. Meanwhile, 2017 and 2018 were record years for Epiroc heavy equipment sales in Norway. “The main driver for that was national infrastructure projects,” says the company spokesperson. “This trend is continuing in Norway in 2019. Our FlexiROC T35R and SmartROC T35/40 surface drill rigs are being used on some of the infrastructure projects.
“Environmental protection and health and safety are high focus areas in Norway. Noise, dust and other emissions controls are a top priority. Tools for planning and documentation of completed works are also required in more and more projects.”