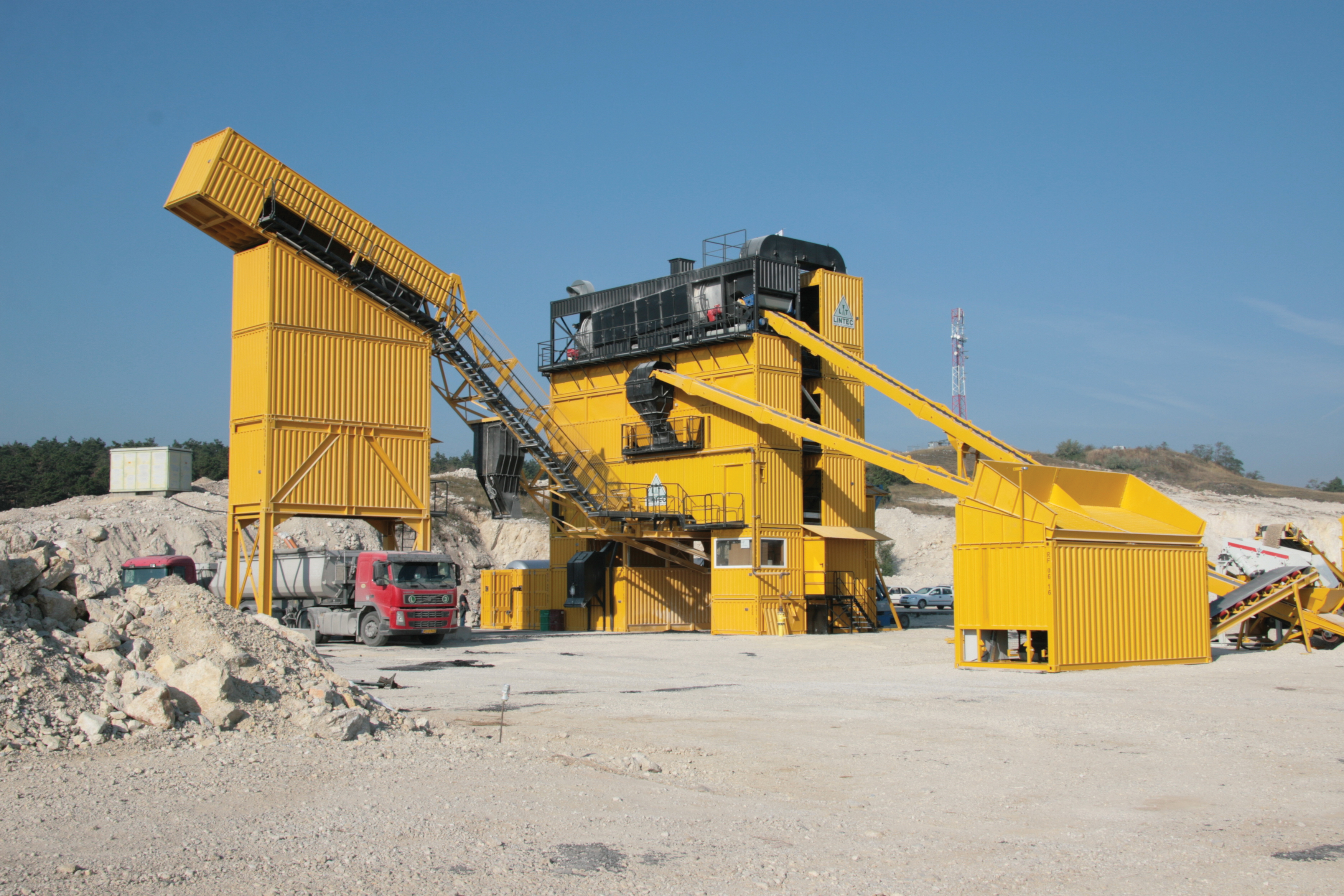
Many leading companies have been improving their asphalt recycling systems and putting them to good use in eco-conscious projects. Guy Woodford reports
The reuse of old asphalt is an absolute must in this day and age The reuse and the recycling of reclaimed asphalt pavements (RAP) started over 30 years ago, and in many European countries the use of RAP is common practice, says the
“Asphalt is 100% reusable/recyclable and for sustainable development its reuse/recycling should therefore be encouraged. RAP can be reused to produce new asphalt (in plant and in-situ) and it can be recycled by using emulsions, foamed bitumen and by adding cement (in plant and in-situ),” says EAPA.
Each year some 50 million tonnes of RAP is produced in Europe and a large amount of this is reused and recycled. The goal should be to achieve 100%, EAPA says in a position paper published some years ago.
Director at EAPA, Egbert Beuving, says recycling offers the same function as in the original application (adding the reclaimed asphalt to new asphalt mixes) while reuse is the utilisation of a lesser function than in the original application (reclaimed asphalt as foundation, fill or base course material).
The Swiss company’s parallel drum is said to be best suited for adding larger quantities, up to 60%, of hot asphalt to a mix. In addition, the reclaimed asphalt drum RAH 100 is said by Ammann to be made for adding close to 100% to a mix. This is done using adapted blades and process air with no direct flame contact.
According to Ammann, adding near 100% of reclaimed asphalt to a mix can lead to significant project cost savings on building materials. Utilising the company’s counterflow technology is said to realise further savings due to reduced fuel costs.
Meanwhile, claimed lower emissions due to the RAH 100’s asphalt recycling solution is said to allow better augmentation during the approval process. Gentle heating of the binding agent contained in reclaimed asphalt is also said by Ammann to retain quality.
Reclaimed asphalt recycling recipes are said by the company to be more flexible, preventing the need to overheat the minerals, while making work simpler for the mixing engineer.
Ammann claims its as1 plant control system’s new Dynamic RAP addition option makes it easy to modify the RAP ratio according to need, even during production.
The as1 is said to achieve quantitative compensation, as the correction of virgin material is carried out in relation to the quantity and composition of the RAP material. In addition, as1 is also said to provide qualitative compensation, as the correction of virgin material is based on the quantity and composition of the RAP material to ring and ball testing standard (based on the formulae detailed in EN13108). The system’s integrated wizard is said to guide operators through the recipe input process, with one recipe said to be sufficient for numerous RAP ratios.
Wirtgen’s offers a variety of recycling equipment, and its cold asphalt recycling technology was used during a major upgrade of Interstate 81 in the US state of Virginia.
The works led to the upgrade’s managing authority, the Virigina Department of Transport (VDOT), winning the US Cold Recycling Award 2012, awarded by Roads and Bridges magazine and the Asphalt Recycling & Reclaiming Association (ARRA).
“Using the cold recycling method has the potential to revolutionise how we rehabilitate our ageing roads, both in Virginia and nationally,” says the Governor of Virginia, Robert F. McDonnell. “We expect to continue using these processes, where appropriate, to save money and materials as we rebuild older roads throughout the commonwealth.”
One of the major north-south routes in the eastern US running through Virginia with two lanes in each direction, Interstate 81’s increasing traffic volumes and loads imposed by heavy vehicle traffic left its pavement surface covered with alligator cracks, wheel ruts and patches where minor repairs had been carried out.
On a 6km stretch near the city of Staunton the right-hand truck lane required complete rehabilitation due to structural damage and an inadequate load-bearing capacity. The left-hand passenger car lane, which was subject to lower loads, was repaired by cold recycling to a 12cm depth.
The construction project involved the use of as many as three different recycling methods, “a ground-breaking project for the rehabilitation of a US interstate.”
VDOT used Wirtgen’s high-performance W210 and W2100 cold milling machines; WR2400 cold recyclers; a 3800 CR cold recycler equipped with a 3.8m wide integrated paving screed and a KM220 mobile cold recycling mixing plant, and an entire fleet of
VDOT Commissioner, Greg Whirley, said: “Savings on the Interstate 81 in-place pavement recycling project go beyond time, money and materials. The reduced transports for old and new material saved fuel. Safety for drivers and road workers on the project was also increased, because work zone congestion was reduced. This section of rebuilt pavement will also be stronger from bottom to top, extending its service life and reducing the need for such complex maintenance for many years to come.”
Cold mix road repair material containing 100% recycled asphalt was laid on rural routes in north Wales, UK, by the contractor Hogan Construction (part of Hogan Group).
The work was carried out to demonstrate that structural integrity can be restored to a failing carriageway without making use of primary aggregates or hot bitumen.
Over 500tonnes of recycled material featuring a Nymuls CP50 emulsion, supplied by
The cold mix material was laid and compacted at an ambient temperature before being overlaid with a surface dressing.
“We wanted to lay an asphalt made up of 100% recycled material because we saw the potential to reduce the use of primary aggregates in the highway maintenance process. The clients are perfectly happy with how the material has performed so far,” says Hogan’s director of business development David Morris.
German company
The recycling drum works with parallel flow system, and the modular concept and built-in 100% ISO containers are said by Lintec to allow for quick and economical transport after test erection at the company’s production facilities, and short erection and dismantling times at the jobsite.
Lintec also offers a new cold recycling system with a maximum of 25% recycled material. The standard system includes a cold feeder with two chambers, the conveyor belt and the RC hopper.
The weighing of the recycled material is executed automatically and is said to be fully integrated into the control system.
The RAP solutions from Lintec are said to be useable for the whole Lintec asphalt mixing plant range from 80–400tonnes/hour.
US-based Asphalt Drum Mixers (ADM) offers four new models of portable and stationary recycling systems said to enhance the cost-efficiency of asphalt plants. These allow plants to use milled material in hot mix asphalt (HMA), and since “RAP is much cheaper than virgin aggregate the result is a less expensive finished product that maintains the high quality of a pure virgin aggregate mix.”
ADM’s recycle bins feature a 13.6tonne capacity, and to transfer RAP from the bin the recycle system includes a heavy-duty weigh conveyor that is 60cm wide and, depending on the model, between 13.7m-19.8m long. It introduces RAP to the dried aggregate mix after the heating process. Based on conditions and type of plant, ADM says up to 50% of the HMA can contain recycled pavement.RSS