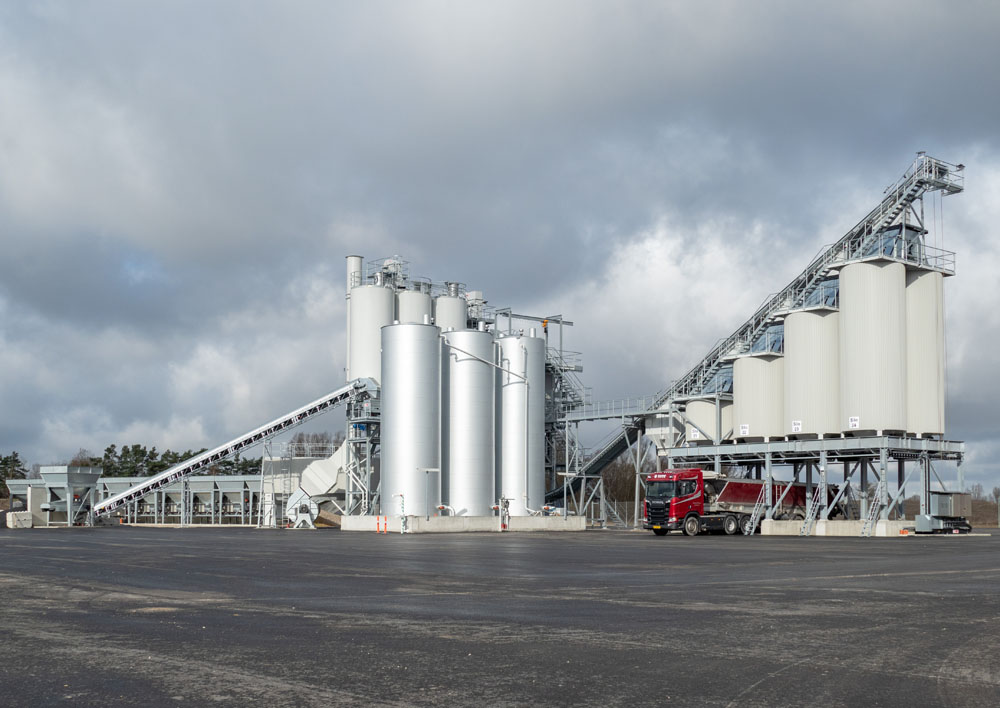
Pankas, a leading Danish asphalt producer, has reinforced its strong green credentials following the recent installation of one of Denmark’s most environmentally friendly asphalt plant supplied by KVM International.
The Freja 3500S will produce up to 100,000 tonnes of asphalt a year at Pankas’s new site in Allerød, north Copenhagen.
KVM International was said to be Pankas’s natural choice to supply its new state-of-the-art eco-friendly asphalt plant due to a reputation for producing premium solutions featuring highly insulated bitumen tanks and hot storage silos, together with a fully automated drying and filtration process bound together with KVM’s advanced Asphalt Management Control (AMC) system.
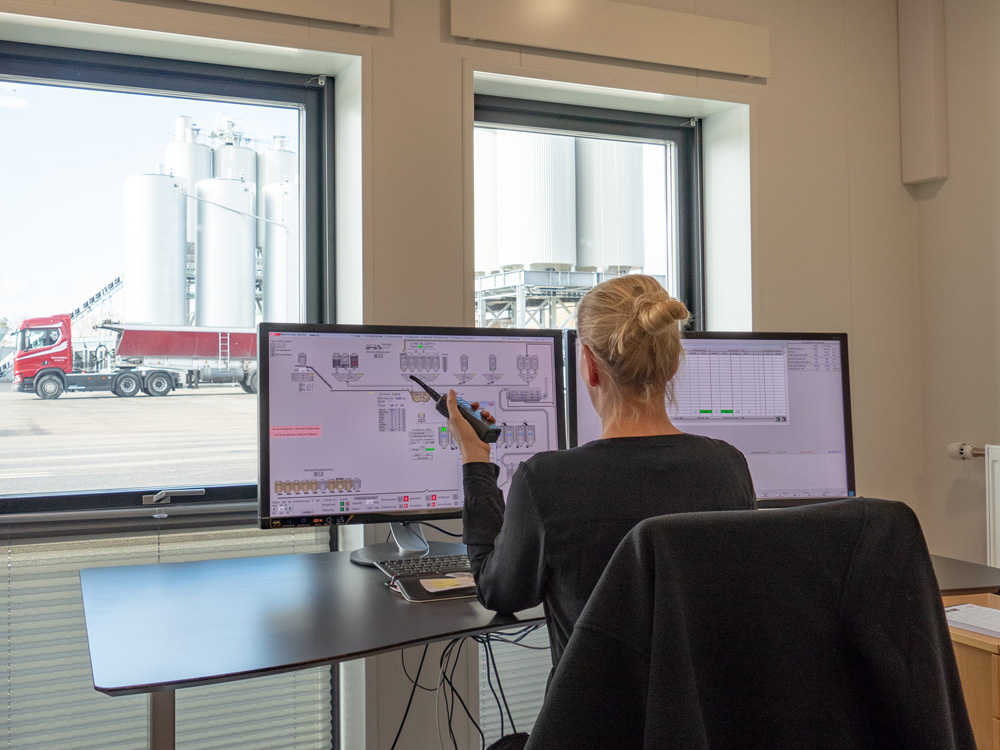
Pankas’s technical manager, David Bredahl, who has been in charge of the Freja 3500S plant installation, received the green light to start operating the new cutting-edge plant on 14 February 2020.
“It turned out to be just what we wanted. The plant does not interfere with the surroundings, from a dust, noise or rainwater perspective. We have used the best technology available, and everything is specially designed to protect nature and the environment – from the height of the chimney to laboratory-tested cleaning of surface water, advanced sound muffling and unloading of trucks without obnoxious smells,” says Bredahl.
The Allerød-based plant’s anticipated up to six-figure output is based on 150 days of four-hours-a-day operation. Throughout Denmark, 3.5 million tonnes of asphalt is produced each year at approximately 35 asphalt factories nationally.
Pankas’s new KVM International plant operates near vulnerable natural areas, so all water discharged from the factory must comply with the highest standards. As no water is included in asphalt production, there is no process wastewater from an asphalt plant. Therefore, Pankas has focused on the surface rainwater that runs off from surrounding paved areas, such as aprons and roads.
A safety layer of 23 centimetres, consisting of several layers of asphalt and adhesive, ensures that, for example, oil drips from cars and trucks do not seep into the groundwater. All surface water is collected and purified in a huge underground biological rainwater system covering 1100m², the first and largest of its kind in Denmark.
The quality of the purified water is tested at least four times a year by a Danak-accredited laboratory. Andy Hoang, a cloudburst and rainwater drainage expert from the consultancy Dines Jørgensen & Co, selected the water treatment plant. Hoang said there is no better and more environmentally friendly solution in the world market for Pankas’s needs.
“The water is cleaned so well in the plant that it meets the requirements of the EU-protected Natura 2000 sites,” he explained.
Most factories in Denmark are the result of expansions over the years. However, Bredahl said there had been massive environmental benefits from being able to plan out the entire factory before it was built. Besides the extensive cleaning of surface rainwater, he points out that the foundation and steel structure for the asphalt plant have been made extra strong, so additional sound-reduction enclosures can be added in the future if required. Additionally, the plant layout was made very compact, and the area with stable gravel and other clean raw materials has been designed so that clean surface rainwater is isolated and can seep into the ground naturally.
“As an experienced asphalt man, I am proud of the finished plant. All motors are frequency controlled, the burner runs on the latest natural gas technology, the plant lighting is low-voltage LED, we do not refuel machines on the site, and we only salt on walking areas. Even the rainwater from the roof is cleaned before it seeps out,” says Pankas’s regional manager Kenneth Dencker, a 31-year company veteran who is responsible for the factory’s daily operations.
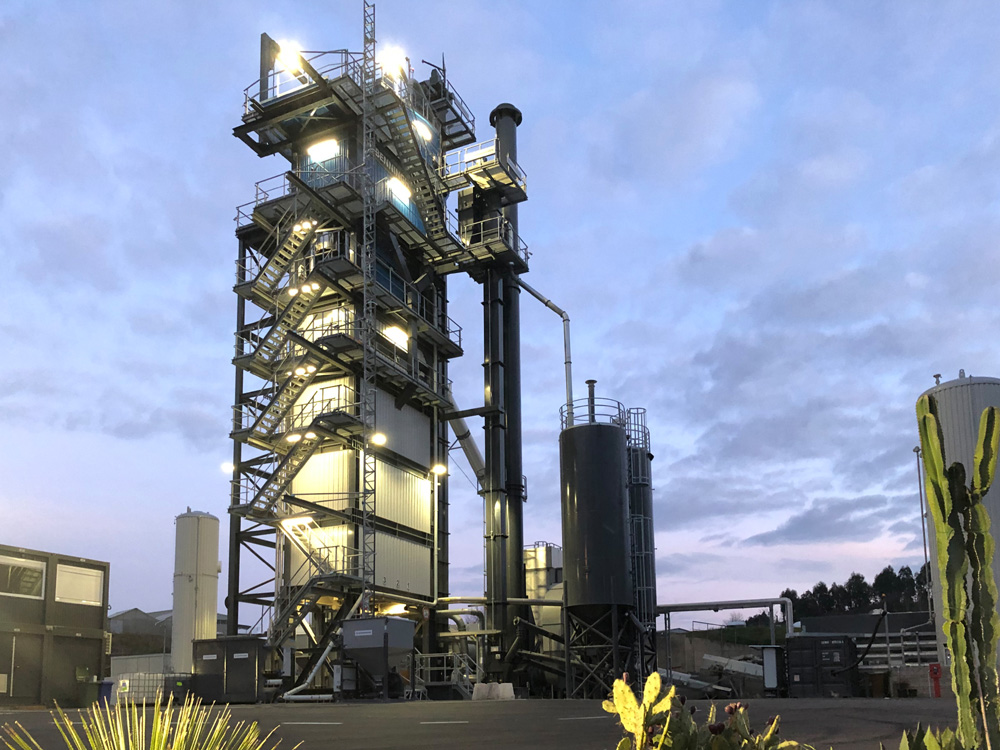
The factory is run daily by five employees, and in order not to impact the neighbours in Allerød, Pankas has taken a number of extra measures. The plant is surrounded by noise barriers and attenuators have been put on the factory’s noisiest features such as the burner, exhauster and the skip winch hoist.
“We also avoid obnoxious smells when the tankers deliver bitumen. All the air that is purged from the silos is pumped with help from special pipework directly back into the tankers,” says Dencker.
The 20-metre-tall chimney is also fitted with an alarm that goes off if dust emissions exceed their limit.
“We have now produced more than 30,000 tonnes of asphalt with our new KVM Freja 3500S asphalt plant, and we are convinced that our decision to go with KVM International was the right choice. We have experienced excellent professional project work and competence from the company throughout this project, and we are confident that we will receive first-class support and help in the future,” concludes Bredahl.
Cicchetti has been an active supplier of asphalt products to customers in the Rome and surrounding Lazio region of Italy for many years. The continuously increasing requirements for the quality of the end product are and always have been an important factor that has to be achieved and explored.
It was the necessity to produce ever more innovative asphaltic mixtures using different additives while continuously increasing the quality of the end product that finally convinced the company owner to invest in a new asphalt mixing plant – one which can be a central sourcing point for road construction in Rome and is capable of meeting these high requirements and demands now and in the future.
After viewing various plants abroad, this decision had already been made several years ago. Due to delays in the required permits, however, it had to be postponed numerous times. The owner’s primary objective – to keep the in-house asphalt mixing plant state-of-the-art at all times – was finally achieved last year with the new Benninghoven TBA 4000 asphalt mixing plant with a four-tonne mixer and a nominal mixing capacity of 320 tonnes per hour.
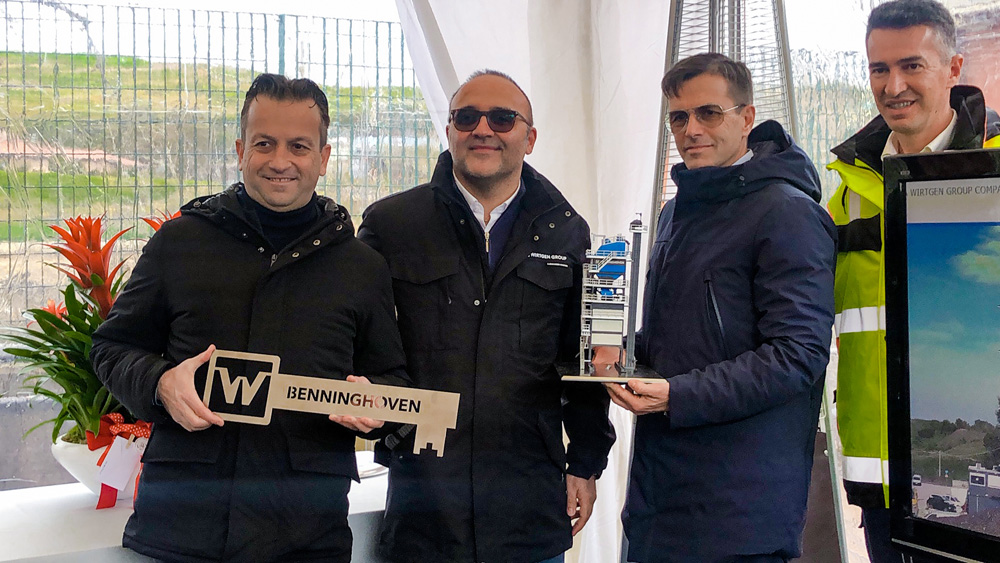
The new asphalt mixing plant was commissioned on 18 January 2020 in the presence of numerous customers, the administrative authority and the purchaser Cicchetti. The guests were informed about the various benefits of the new asphalt mixing plant, the easy operation of the software and the wholly revised control station. Guests with a particular interest in the plant were offered a tour which highlighted the special technical features of the plant.
Before the plant was planned, a lot of time and detailed work were invested in the precise layout of the construction site. This meticulous preliminary work allowed the new asphalt mixing plant to be safely installed while the old plant was still running, continuing to product asphaltic mixture while the TBA 4000 was being assembled. Other parts of this concept included optimising the positioning of the storage locations for the minerals, the processing of the recycling material and the manoeuvring of lorries for loading.
As the central control unit for the asphalt mixing plant, the command station was updated with the Benninghoven BLS 3000 control system. Examining the recycling material to be reused and in particular, the accurate rendering of the recipes and the quality of the asphaltic mixture delivered to the customer are crucial aspects for a plant which produces exclusively for third parties. Material samples are extracted daily to guarantee the correct composition of the product for road construction.
In the context of reusing recycling material, a new screen unit was also purchased for screening the delivered recycling material into different fractions. This is the best way to ensure that the material can be added to the mixing process with the correct grain size. The screened recycling material is stored in the covered internal area to minimise dust at the construction site and to protect the processed material against rain. Without this protection, the material could re-absorb moisture which would have to be removed again during the drying process, requiring additional energy and costs. This measure substantially reduces fuel consumption for drying the mineral and increases the hourly output of the plant.
A 1.2-metre difference in altitude at the construction site was created between the storage area for aggregates/recycling material and the area where the plant was installed. This omits the need for a feed ramp on the site.
Even though the previously used plant was not wholly outdated, some weak points had become evident over the years which had to be addressed: the hourly output was increased to offer customers shorter wait times; the market requirement for offering ever more progressive products; the readiness to use recycling material and the continuously growing necessity for reducing the environmental impact (odours, emissions, etc.).
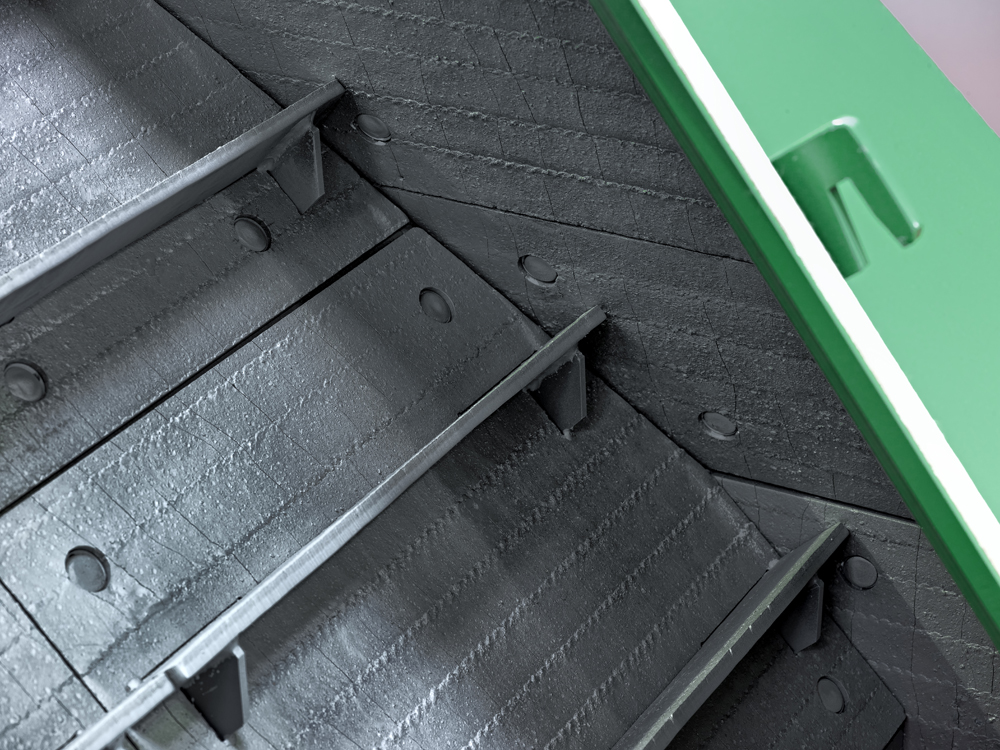
With respect to emissions, the burner is now run with liquid gas instead of heating oil. Another standout feature of the new burner is the afterburner unit, i.e. extracted bituminous vapours generated during the internal asphalt transfer from the mixer into the skip or the loading silo are transferred to the burner and burnt there. This not only drastically reduces contamination of the plant, but also allows the odours generated during specific processes to be eliminated as much as possible.
A particular focus was also placed on stocking the raw materials for the final asphalt: a total of nine feed hoppers for virgin mineral allow easy processing of mineral containing lime as well as basalt. Four bitumen tanks allow the use of different bitumen types, depending on the recipe and on which is more suitable for the mixture to be produced, as well as two tanks for storing emulsions.
In addition to this, an increased focus was on the type and quality of bitumen heating and storage and the protection of all essential components. Bitumen pumps, for example, were specially encapsulated to reduce noise and to protect them against the weather.
In line with the overall concept, the dust collection system was equipped with a larger filter area (over 1100m²) and fully insulated to reduce heat loss and the resulting fuel consumption as much as possible. In addition to this, the fan in the mixing tower extraction system, as well as many of the main motors in the system, were equipped with a frequency converter (for reducing power consumption and noise generation).
The requirements for the technology for using recycled material were carefully evaluated and coordinated after several visits to sites in Italy and abroad. The “multivariable” system was the most convincing: it allows the production of the asphaltic mixture from screened recycling material (mandatory on the Italian market today) which is added to the mixing process cold.
The Benninghoven control system allows the use of a high ratio of recycling material. At the same time, this concept eliminates the risk of mistakes with respect to the grading curve of the recipe, any process oils (rejuvenators) to be used or the production temperature of the mixture.
To ensure production of a new high-quality asphalt, the system allows the user to adapt the quantities of the different aggregates, the rejuvenator, filler and bitumen – which are required for the best possible grading curve – depending on the quality and ratio of the recycling material used.
To meet the customer’s requirements, a large-capacity loading silo (with two 76-tonne chambers) was selected to keep waiting times during loading of lorries at the site as short as possible.
Other important features are the screen unit with six-fold screening and a screen surface of over 46m² and a hot bin section with a total capacity of 80 tonnes for storing the hot screened material. This ensures unparalleled flexibility when handling a variety of different recipes. Also, it helps to minimise plant starts/stops not connected to planned production and to provide optimum service to customers arriving without registering beforehand.
All asphalt production businesses want to minimise the cost of ownership. The lower those expenses, the more competitive asphalt prices can be – and the higher profits can go.
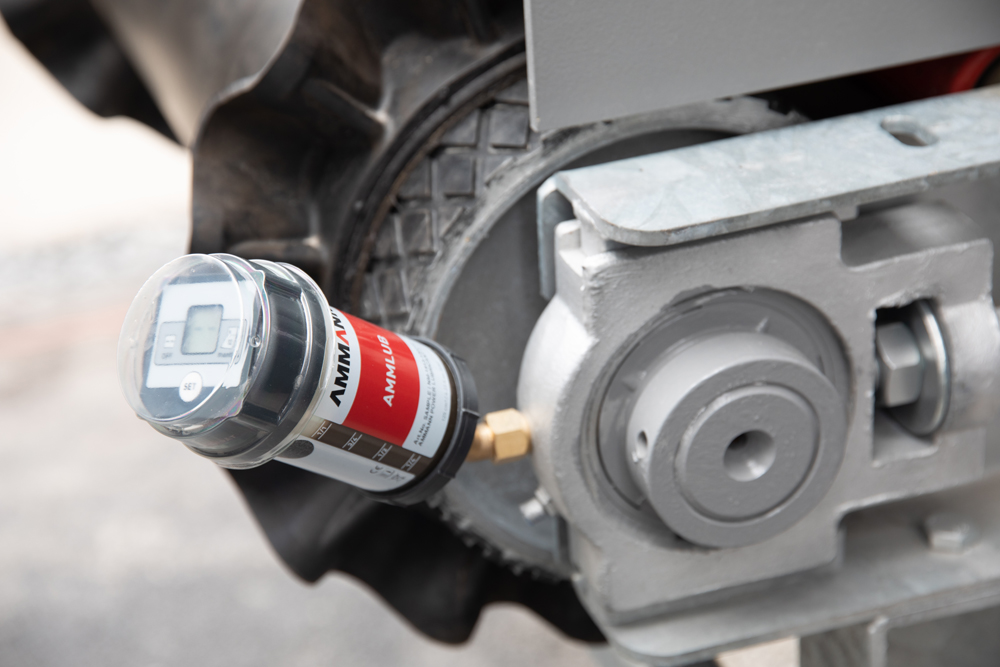
Ammann’s efforts to reduce asphalt-operating expenses include two key products that protect plant: Ammlub and Amdurit.
Ammann’s automatic lubrication system is said to provide three key benefits: longer plant life, reduced fuel costs and improved safety.
Traditional lubrication methods can be a struggle. They often require that technicians stretch and strain to reach extremely tight spaces – and that they fight dust, dirt and heat in the process. There also is the question of when to grease – and how much grease to apply. Was it too much? Not enough?
Ammlub ends these battles, says Ammann. The labour-saving, smart system is mounted directly on the plant’s lubrication points. It automatically applies lubricants at scheduled intervals, ensuring that the process is done on time – every time.
Also, Ammlub is said to eliminate downtime. The lubricant applications can occur while the plant is running, enabling the completion of routine maintenance without a drop in productivity.
An immediate benefit is fuel savings, which Ammann says can be reduced by as much as 10% when all parts and components are working harmoniously.
With appropriate lubrication, those parts and components will also last longer, providing further savings. Additionally, because this system locks out contaminants, plant life is extended.
Finally, workplace safety is also improved. Technicians no longer need to lug tools and fluids with them to access difficult-to-reach service points. These service points typically include all components along the process flow, starting with the cold feeder and ending with the discharge shoot.
Amdurit, Ammann’s proprietary wear-protection system, is said to provide up to three times the service life of wear-resistant steel and protects valuable parts and components. It makes maintenance easy, too. Instead of replacing the component, simply swap out the Amdurit covering.
The wear-protection system is said to result in savings as components last longer, which translates to fewer replacements and therefore, lower costs. Plant owners also avoid the labour costs associated with replacing parts.
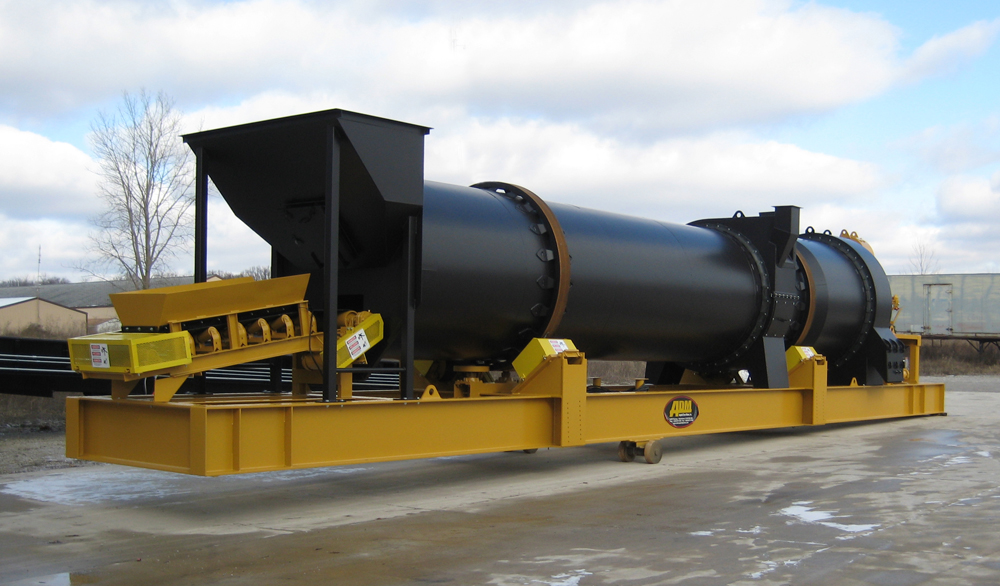
Component replacements are also quick and easy to install when necessary, so overall plant uptime is improved.
There are many potential areas of use, including drum inserts; transition and discharge locations; feeders, both reclaimed asphalt pavement (RAP) and traditional; and silos.
The preferred areas of use concerning components for RAP feed are RAP elevator feed and discharge; drum pipe infeed, cone and scales in the drum pipe; intermediate container and chute in the mixer; and RAP feed, worm screw and screw trough.
A range of fastening methods, such as welding, clamping and bolting, make it easy to replace the original part with Amdurit wear protection.
Asphalt producers worldwide understand the importance of aggregates drying for producing high-quality, hot-mix asphalt. Not as readily understood may be the principle of counterflow technology in hot-mix asphalt plants. What is counterflow technology, and how does it work to impact aggregates drying times to produce highest quality asphalt?
ADM Asphalt Drum Mixers’ EX Series of asphalt plants (120–425 tonnes per hour) with single-drum, counterflow systems, are designed to meet high-capacity production demands and strict environmental regulations. These plants handle up to 50% RAP and virtually eliminate blue-smoke and hydrocarbon emissions, combining high volume, high efficiency, and environmental friendliness in a compact package.
A hallmark of the EX Series plants for high-quality asphalt production is their counterflow design, an innovative technology based on the process and movement of the material through the drum in the opposite direction of the heated air flow and combustion gases. Here’s how it works.
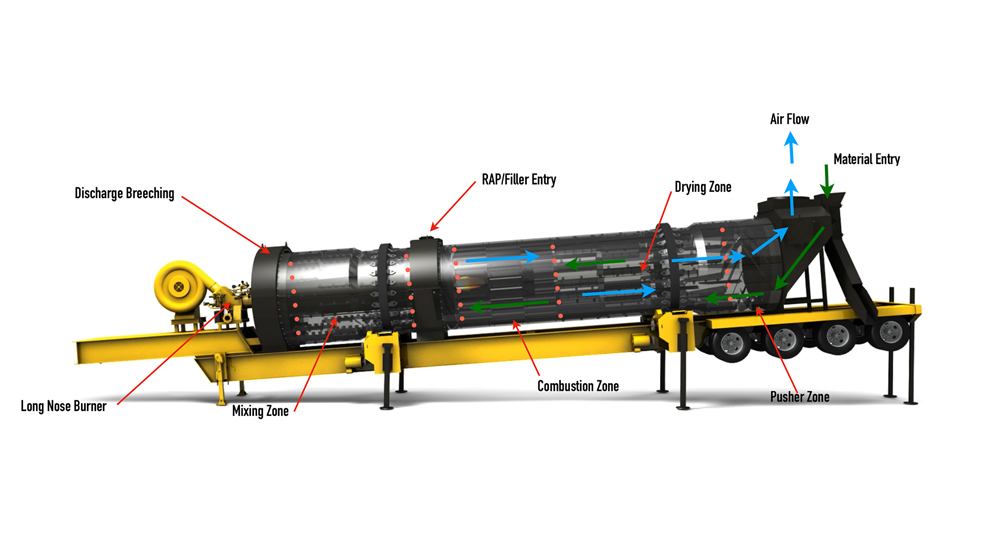
Aggregate flows through the slinger conveyor or optional inlet chute, into the drum, which has six different zones. The material first enters the pusher zone. Here, the steep spiral design helps push the material into the drying zone, where the combination of J-type, saw tooth, and basket style flights, set in a herringbone pattern, lift and move the material forward through the drum. The lifting creates a vale or curtain of material through which the hot air travels. This allows for heat transfer onto the material.
Following the drying zone is the combustion zone. The combustion zone has specially designed T-type flights, which keep the material against the shell of the drum. This serves two purposes. First, it keeps material from falling through the flame, and second, it helps insulate the drum shell from the heat. The nozzle of the long nose burner is located about 1/3 of the way into the drum, which allows for a separation of the drying and mixing zones.
Past the combustion zone and behind the flame, the material passes through the RAP and additive introduction zone. Here, the now dry virgin aggregate mixes with the baghouse fines being reintroduced into the process and any RAP or dry fillers being added into the mix.
The next zone is the mixing zone where the liquid asphalt is introduced and the previous materials are further mixed. Once mixed, the now hot-mix asphalt (HMA) is moved into the discharge area, where it is lifted and pushed out through the material discharge chute, into the drag conveyor. From here the material moves up the drag into the storage silos.