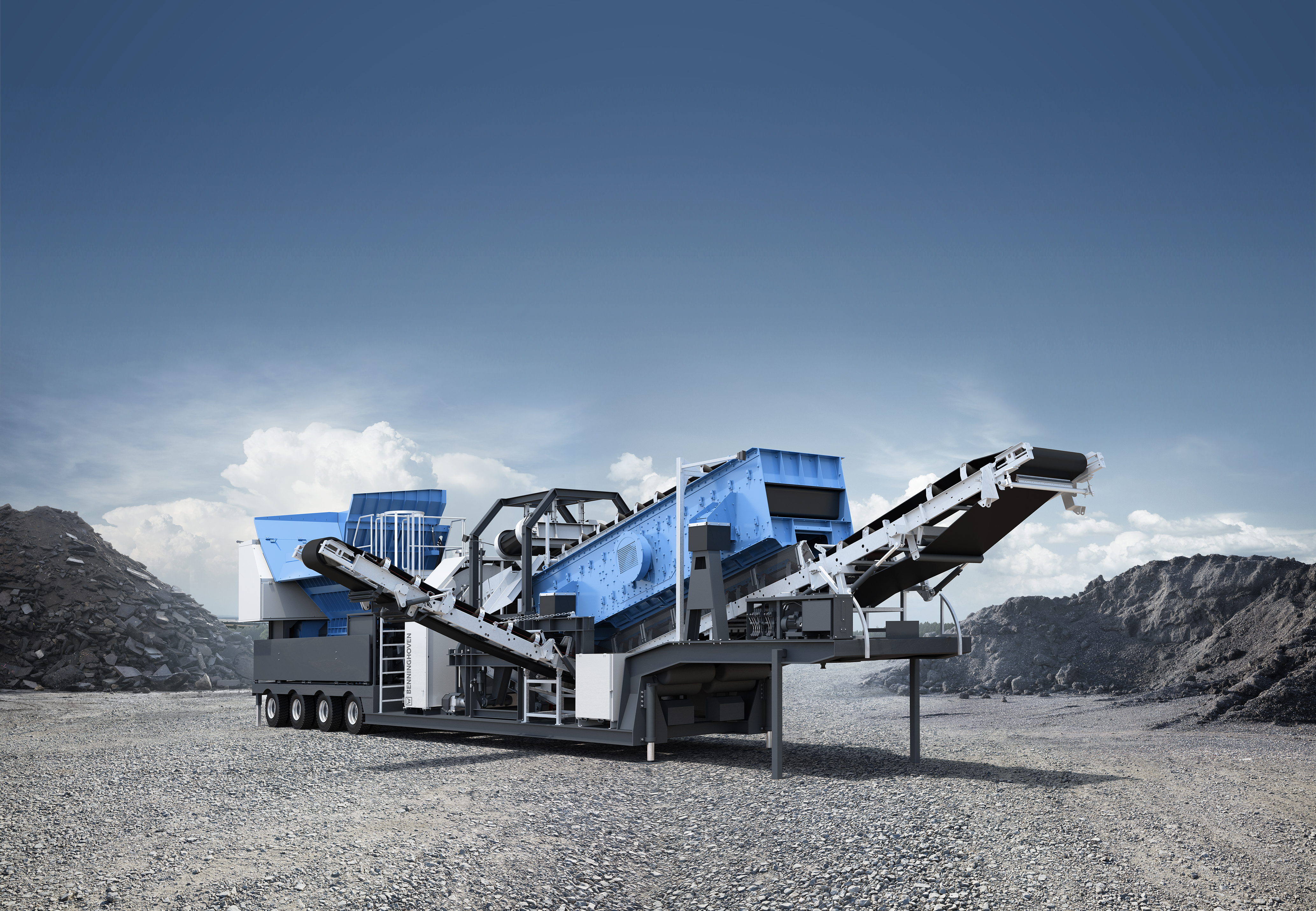
There’s much that is new this year from global asphalt plant manufacturers and bitumen product specialists, including a major asphalt supply contract at a leading international airport. Guy Woodford reports.
The bitumen sector giant’s facility is situated within the new Shell Technology Centre Bangalore (STCB), a 52-acre, custom-built technology centre that can house up to 1,500 experts, representing a broad cross section of products and services within the Shell group.
The location of the entire India-based Shell Bitumen team within the facility is designed to accelerate innovation in new product development and drive the continual improvement of premium bitumen products within the portfolio.
“We have made a major investment in new and upgraded technology, infrastructure and talent at Bangalore. The move means that Shell Bitumen’s customers will benefit from increased collaboration between the group’s technology innovators in multi-products and sectors.
“We have bold ambitions: ultimately, we want to continue to deliver on the needs of our customers by producing high-quality bitumen regardless of our refineries’ strategic choice over processing conditions and crude selection. The opening of the new facility at the STCB represents a key part in our long-term strategy,” said Professor John Read, general manager Technology (Bitumen and Sulphur) at Shell.
Scientists and researchers from the bitumen and lubricants’ operations are already working together with experts from Shell’s computer modelling, statistical modelling and advanced analytical groups on innovative molecular and rheological techniques, which will lead to greater understanding of bitumen at the atomic level.
Shell Bitumen’s team has also selected the new facility to develop the next generations of Shell Mexphalte C and Shell Tixophalte products, which form part of the company’s on-going R&D programme, focused on the continual improvement of products for customer applications.
With the move to Bangalore, Shell Bitumen has also expanded the research and analyst team by hiring three new bitumen technologists. They will work under Girish Rao, Shell Bitumen’s resource manager at the centre, who reports to Professor Read.
Shell Technology Centre Bangalore is one of the three main technology hubs in the company’s global network of R&D centres, with the other two located in the Netherlands and the USA. More than 4,000 staff work at these hubs and smaller technical centres on a broad range of projects, such as turning natural gas into more efficient and cleaner fuels, developing affordable technologies to unlock energy thousands of metres below the sea surface, and R&D projects on low carbon technologies.
Singapore Changi Airport is one of the busiest transportation hubs in South East Asia – and the world. A flight lands at or departs from the airport every 90 seconds, with 58.7 million passengers passing through Changi in 2016.
Changi has a reputation for quality as well. It has been named the world’s best airport by a number of organisations, including highly regarded Skytrax – which has awarded Changi with its top honour for the past five years – and counting.
Remaining at the top is always a challenge. Passenger traffic continues to increase annually, and the airport is also one of the world’s busiest cargo hubs. That volume creates pressure that could take away from the passenger experience. But Changi officials are taking steps to meet the increased demands while maintaining quality.
The construction of Terminal 4 will be completed in 2017. An expansion of Terminal 1 will follow in 2019, enabling that facility to handle 28 million passengers per year. Terminal 5 will open in the mid-2020s. That terminal alone will be able to accommodate 50 million travellers annually.
The first project is the completion of Terminal 4, which consists of adding a third runway. It is demanding work with tight time constraints and no margin for error when it comes to quality.
Providing the mix for the terminal is an
The ABA UniBatch was a natural fit for the expansion. Most importantly, it provides productivity with its capacity of 300 tonnes/hour.
“It’s an advanced plant, and it has a very small footprint, which is perfect for the location,” said Michal Dvorak of Ammann Singapore PTE Ltd. “It also has a very low height, important near an airport. It’s very simple to operate and easy to learn the as1 control system. The plant is also easy to maintain.”
The base course consisted of 1.6 million tonnes of cold mix, a number that will increase before completion, said Terry Isedale, project manager for United E & P. The plant will also produce binding materials of 650,000 tonnes and 850,000 tonnes for the surface lift.
That surface material was a mix that had previously not been used in Singapore, Isedale said. But the plant’s capabilities and the operating system enabled the production.
“It’s performing well,” Isedale said. “We did originally program the plant to run just 10 hours a day, six days per week. That will probably change to 24 hours a day, seven days a week, for a three-month period. We’re sure the plant can keep up with that pace.”
Ammann AV 110X Articulated Tandem Rollers handled compaction of the runway. The roller has two frames connected by a double joint that enable crab steering on each side. That steering provides increased compaction output and responsiveness.
“The manoeuvring is great, according to the operators,” said Low Cheng Hwee, operations manager at United E & P. “The operators like the machines a lot. It’s important that the machines leave behind a smooth surface. We don’t want to leave any bumps behind.”
That goal is being met, as the runway is reaching all targets for compaction density and smoothness.
The Ammann rollers and plant are helping United E & P deliver on its promises. As a result, Changi is well positioned to continue its run of “best airport” awards.
Asphalt Drum Mixers (ADM) says the company’s new EX120 asphalt plant is a solution for producers who need a portable counterflow plant that can process high percentages of RAP. Featuring single-drum counterflow technology, the compact 120-tph EX Series plant meets all US federal and state emission regulations.
ADM featured its EX120 asphalt plant during CONEXPO-CON/AGG 2017 in Las Vegas, USA.
“The EX120 combines the innovative counterflow technology of our EX Series with the compactness and portability of our SPL Series,” said Mike Devine, Asphalt Drum Mixers president. “The result is a dependable asphalt plant that goes wherever you need it to go while producing material at a low cost per tonne and delivering a high ROI.”
The EX120 boasts the longest aggregate drying and mixing times in the industry, resulting in a low cost per tonne. The unit consistently produces quality asphalt to help protect plant owners against out-of-spec damages. In addition, the plant is capable of processing as much as 50 percent RAP.
Counterflow technology with separate drying and mixing zones allows the EX120 to achieve maximum heat transfer and fuel efficiency. The system virtually eliminates unsafe carbon emissions that are a common problem with other drum mix plants. ADM further reduces emissions by designing the counterflow system to reintroduce gases back to the drum’s combustion zone.
Similar to ADM’s SPL Series asphalt plants, engineers designed the EX Series for smaller output and optimal transport. The entire EX120 plant sits on one chassis for easy movement from site to site. This makes it ideal for remote and demanding locations worldwide. In addition, the portable plant’s compact size and easy manoeuvrability greatly simplify the process of obtaining an operating permit when compared to stationary plants. This is because the Environmental Protection Agency (EPA) considers portable plants to be temporary and stationary plants to be permanent.
Plant capabilities are highly sophisticated, yet controls are simple to operate. One plant operator and one loader operator can control the EX120. ADM constructs each plant with durability and low maintenance in mind, so on-site staff are easily able to troubleshoot. In addition, the manufacturer builds the EX120 primarily with readily available parts for easy and cost-effective repair.
Customers choose from a full range of components to customise the plant for their operation. ADM offers cold feed bins, hot oil asphalt cement tanks (both horizontal and vertical), direct-fired horizontal cement tanks, portable and stationary baghouses, mineral filler systems, RAP systems, self-erect and stationary silos, weigh and drag conveyors, weigh batchers and fuel oil tanks.
In addition to the EX Series, ADM also offers its RoadBuilder, SPL and MileMaker Series. Each ADM plant can be custom-designed to meet individual site and production requirements.
The new MBGR 2000 mobile granulator from