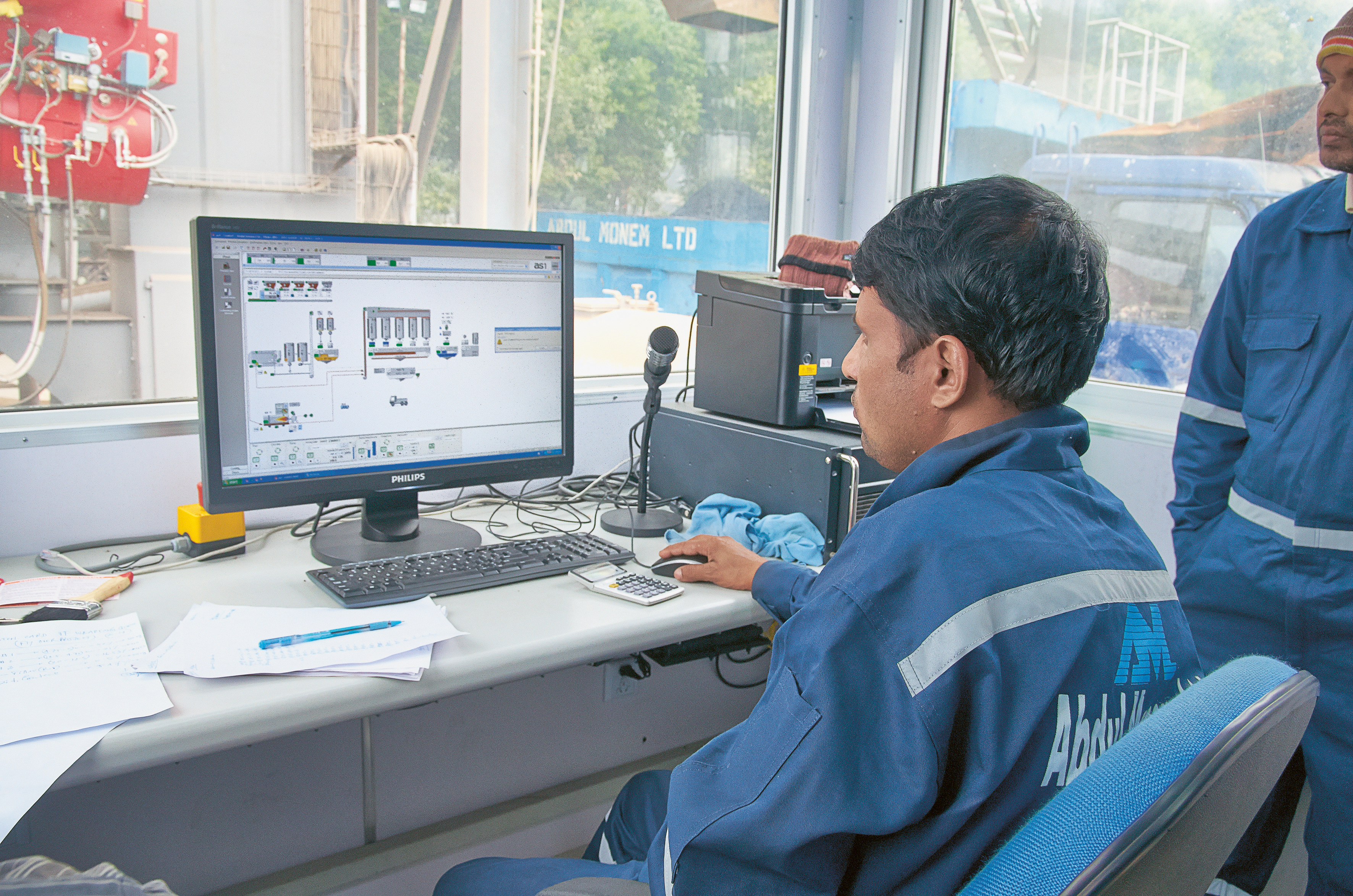
Leading asphalt plant manufacturers have been busy increasing their market share in key emerging markets of Africa and Asia. Guy Woodford reports
The plants, which have an almost identical mixing tower, with the drum and filter slightly larger on the 160 model, were bought by AML to help fulfil its contract to refurbish the runway at Hazrat Shahjalal International Airport just outside Bangladesh’s capital, Dhaka. The paving was last renewed in 1996 and had aged over the years due to heavy use.
As it’s the airport’s only runway, air traffic can only be interrupted for a few hours during the night. AML cannot start work until 11pm and has to clear the runway at 5am to allow flight operations to resume. Ammann says this has shown the importance of having reliable asphalt mixing plant systems, such as the Amman JustBlack 160 and 150 models.
Both Ammann plants are located at the airport and are said by the firm to deliver a reliable supply of asphalt every day. Ammann’s sales team involved in the AML purchase negotiations and subsequent installation of the JustBlack 160 and 150 plants at Hazrat Shahjalal International Airport noted, “Bitumen in Bangladesh is not available in a hot, liquid form but is sold cold in barrels. Every barrel has to be cracked open and the bitumen heated prior to use. All day long, one employee sits on the barrels and opens them with a hammer and chisel to ensure a ready supply of the bitumen required for the project.”
During the commissioning phase, Ammann agreed to rent AML with one of its asphalt plant mixing engineers. Since then, an Ammann mixing engineer has monitored the customer’s asphalt production process.
Through using Ammann’s JustBlack 160 and 150 plants, AML is said by Ammann to have finished the airport runway project four weeks earlier than scheduled.
In addition to its construction business, family-owned AML, headed by Abdul Monem, is also a general importer for Coca-Cola and Igloo ice cream.
Meanwhile, Ammann hopes its new and highly mobile Prime 140 asphalt mixing plant, showcased at this year’s
Capable of producing 140tonnes/hour at 3% rH, Ammann says the plant has been made specifically for markets where high mobility is in demand.
Like all continuous asphalt mixing plants from Ammann, the Prime 140 is equipped with a continuously running two-shaft paddle mixer and T 1860 drier drum. Among a number of its special features is its controllable outlet gate, enabling the filling height and therefore the mixing time to be set depending on recipe and output. The outlet gate is also said to dramatically reduce losses during plant relocation and commissioning/decommissioning.
The Prime 140 is controlled by Ammann’s new fully automatic as1 Push system. An operator can manually control the plant using ‘Soft Push Buttons’, with corresponding ‘Wizards’ said to provide fast plant calibration. Automatic daily production figures are generated by as1 Push.
With the design of its new mobile drum mix asphalt model, the CDM-70/80, Çesan says it has managed to create a valuable addition to its product line. Having already sold one to Cyprus and one to Cameroon, Çesan is aiming to increase its stronghold in the North African territories with its new model.
Having the ability to transport a 60-80 tonnes/hour drum mix asphalt plant with one chassis over great distances has been a crucial consideration for constructors in areas with limited infrastructure and bad road connections. Çesan says the single chassis CDM-70/80 covers the filter, aggregate silos mixer and control cabin all in on one.
“Our aim was to enter this niche market, where constructors prefer to buy small capacity plants to perform road work and projects which are not accessible via large capacity plants,” said Tahir Aydodu, the Turkish firm’s general manager.
“We have listened to the request of our customers and designed a plant that will fit the small-medium size companies which have vast amount of projects spread around a country where mobility is very difficult for them,” added Aydodu, who said Çesan were “finalising deals” with two other North African clients interested in buying the CDM-70/80.
Çesan has also created the King Batch - a new design asphalt plant. The new plant, with a 280tonnes/hour capacity, was shipped to bauma 2013 with only eight trucks. The King Batch’s transport and erection time is said to be drastically reduced due to its compact design.
With the CDM-70/80 and King Batch, Çesan is aiming to increase their sales numbers this year especially in the African, Middle East and CIS areas. The firm says its latest plant models are the result of listening to the needs and requests of its customers, who have stressed that compact and easily transportable plants cut vital costs.
Offered in both stationary and portable designs, cold feed bins from Asphalt Drum Mixers (ADM) are engineered and constructed for maximum durability. The bins are manufactured with all welded painted steel, industrial strength columns and end bracing said by ADM to outlast other similar systems – making them ideal for often tough emergent market climates and working conditions.
ADM cold feed bins are equipped with tapered sidewalls and a specially designed belt feeder to virtually eliminate plugging and bridging problems, whether the bin is heaped or low. Material flow is further enhanced by a fully adjustable radial gate system with self-relieving tapered discharge opening. These features all work together to simplify operation and ensure high quality asphalt production.
The bins provide more capacity and better accuracy for Superpave and other high specification mixes. Available in single bin and multi-bin configurations, ADM cold feed bins are compatible with any control system and can be retrofitted to add extra tonnage capacity to existing cold feed systems, regardless of brand. The bins are offered with bolt-on or hinged extensions, and minimal on-site assembly is required.
E-MAK for key Turkish tourist highway
Cemil Ozgur is one of the pioneers of construction business in Turkey. During the firm’s 58 years in the construction business, it has built many highways, dams, tunnels and buildings. One of its latest projects is helping to extend the Antalya-Burdur highway in southern Turkey to Istanbul.
Antalya is one of the most important tourism centres in Turkey, and the Antalya-Burdur highway is an essential tourist travel route. Extending the highway to Istanbul will make tourist access to Antalya quicker and easier. The construction project, which began in 2012, is set to be completed in 2014.
Cemil Ozgur is responsible for building a 15km stretch of the extended highway. As well as carrying out ground and utility works, the company is generating 600,000tonnes of hot mix asphalt for the project using the
E-MAK says that Cemil Ozgur has been impressed with the plant and is working to schedule on its part of the Antalya-Burdur highway extension project.