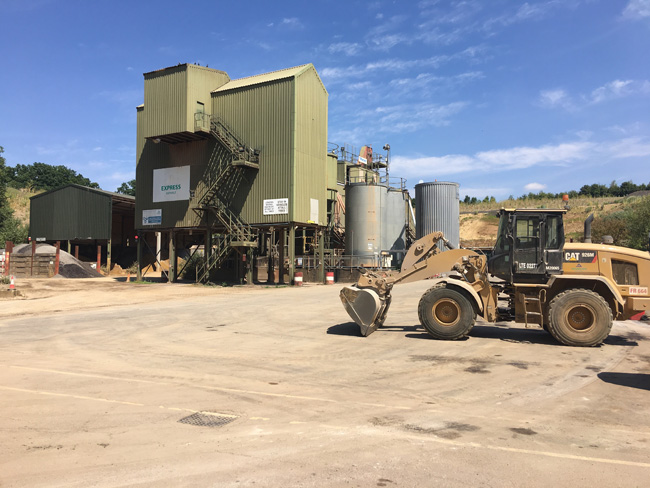
Major global projects such as the UAE’s Ras Al Khaimah Road and the third airport in Istanbul require the supply of high-quality asphalt, and lots of it. Liam McLoughlin reports.
We need to produce quality asphalt, and high volumes of it,” according to Adnan Elmasri, operations manager for Top Link Contracting & General Transportation, based in Dubai.
Top Link, an established contractor in Abu Dhabi and Dubai, is providing mix for a new highway that will greatly alleviate the traffic on the major thoroughfare, the Ras Al Khaimah Road. The new construction will create a bypass around Ras Al Khaimah and connect to roads going south of United Arab Emirates (UAE).
The new project is a 40km highway with three lanes in each direction. Construction began in 2016 and will be completed later this year.
Top Link opted for the ABA 260 UniBatch asphalt-mixing plant from
The ABA UniBatch will create more than 400,000tonnes of asphalt mix by the project’s completion.
Efficient production is essential on a large-scale construction project like this, according to Elmasri. “The plant can produce 260 tonnes per hour,” he said. “The mix is a good quality and a good quantity.”
Top Link is also using the proprietary Ammann as1 Control System on the project. “The system is flexible and simple to use,” said Elmasri. “Everyone can use it. After a little time, it makes everyone look like a genius.”
Top Link plans to make further purchases of Ammann asphalt-mixing plants in future. The company recently took delivery of an Ammann EmulTEK plant, which is capable of producing high volumes of bitumen emulsion.
There is a growing demand for the use of recycled asphalt (RAP) in India. The ability to use RAP in place of fresh aggregates is a key cost saver, according to Ammann.
RKC Infrabuilt, an Ahmadabad company involved in large-scale roadbuilding projects in India, is using the Ammann ABA UniBatch asphalt-mixing plant for the repurposing of RAP.
“It’s very economical compared to all other plants,” said Siddharth Shah, a director at RKC Infrabuilt. “We have been saving great amounts.”
He adds that the plant provides excellent asphalt mix. “The baghouse is amazing,” says Shah. “The drum is good for recycled asphalt as well.”
He adds that a significant factor in RKC choosing the ABA UniBatch was the plant’s ability to add hot and cold recycling material.
The plant was built in India for that particular market, but utilises European technology. It can access a foam generator that produces asphalt at a reduced temperature. This low-temperature asphalt (called ‘warm asphalt’ in India) has the same quality as a traditional mix but requires less fuel to produce. Emissions are lower, and the lower temperature mix makes it more comfortable for the paving crew to work with.
Shah said the intuitive nature of Ammann’s proprietary as1 Control System makes production of all the mixes possible. He commented on the as1 software: “It gives you a total description of the entire plant.”
RKC has needed high production on some recent large-scale roadbuilding projects and the ABA UniBatch plant has produced 130,000tonnes in fewer than 100 days. It can develop mix that utilises up to 40% hot RAP and 25% cold RAP. It also offers a foam mix option and solid additives.
The RKC plant has an uptime of close to 100%. Research and development has led to green technology efforts, including an efficient burner and baghouse that ensure less than 20 mg/Nm3. This also provides customers with additional carbon credits.
Martinho Fernandes, the commercial manager for Ammann and Apollo plants in India, says the Ahmadabad plant is ready for the next round of challenges. “The ABA UniBatch is also ‘future ready’, meaning customers can easily incorporate new technology as it becomes available,” he said.
The building of Istanbul’s third airport, officially named Istanbul Yeni Havalimanı, is among standout elements of Tukey’s current multi-billion euro infrastructure spending programme. The
After three years of construction, the world’s biggest airport in passenger number terms is set to go into operation before the end of 2018, initially with two runways, expanding to three by 2019, and to six by the end of the project in 2028.
The high-quality asphalt mix for the runway construction is being produced by six Benninghoven mixing plants: one TBA 3000, a TBA 4000, two ECO 3000 and two ECO 4000 models, with mixing capacities of 240tonnes/hour and 320tonnes/hour. This corresponds to up to 1,680tonnes/hour, depending on the type of asphalt to be produced. The mix for the surface course consists of a stone mastic asphalt with polymer-modified bitumen. The material is used for surfaces which are subjected to heavy stresses and consists of a mix with a high proportion of stone, polymer-modified bitumen and stabilising additives for the bitumen. The composition is balanced so as to ensure lasting resistance to deformation, producing surface courses which are robust, safe for traffic and have a long service life.
Responding to rising demand for coloured asphalt across south-east England,
The introduction of the SuperColour collection of distinctly coloured asphalts at the Hertford Express site comes after the range’s deployment at Aggregate Industries’ Doncaster and Bristol plants.
The British building materials supplier heavyweight says the move is part of its ongoing plans to expand SuperColour supply across the UK. Coloured asphalt is increasingly popular in the south-east of England, where it is in demand for private drives, bus lanes, cycle lanes, sports landscaping and parks and natural areas.
The expansion has seen Aggregate Industries invest heavily in kitting out its Hertford Express asphalt plant, upgrading the site with seven new high-tech aggregate bays and a state-of-the-art specialist bitumen tank. The major revamp, which took four months to complete, has transformed the small collect-only depot into a multi-functional asphalt plant capable of supplying both black and coloured asphalts, acting as a dedicated SuperColour site when required.
Duncan Reaney, general manager of Express Asphalt at Aggregate Industries, said: “Since its inception, our SuperColour range of distinctly coloured asphalts has proven to be ground-breaking when it comes to any application requiring colour differentiation. In the south-east of England in particular, we’ve seen demand for this high-performance product grow rapidly in recent years, driven by its clear safety benefits and aesthetic appeal.
“As such, in order to make it easier for our busy customers to access asphalt materials quickly and efficiently, we’ve invested heavily in expanding our popular Hertford Express asphalt so that it can now offer SuperColour alongside our pioneering Express Asphalt service. The result is the ultimate one-stop shop in the South East for all things asphalt-related.”
Aggregate Industries’ Express Asphalt service includes a ‘click and collect’ service with a guaranteed turnaround of 30 minutes for single loads of standard products, which enables customers to order asphalt, or tools and equipment, and pick it up from any one of the business’s 40 Express Asphalt depots nationwide, including the one serving the Hertford Express plant.