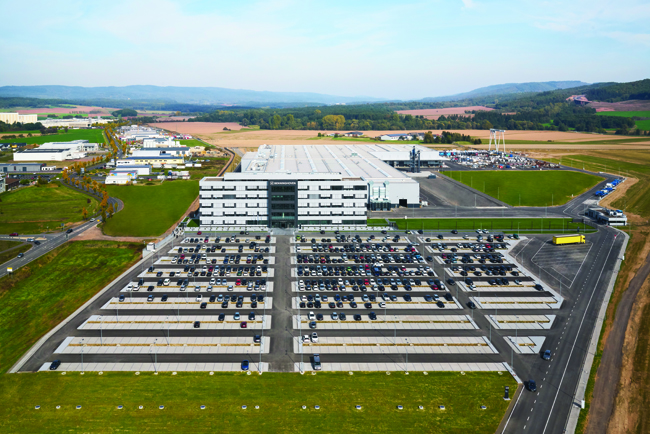
Following a €130 million
Benninghoven’s production facility at the Wirtgen Group company’s ultra-modern 313,000m², 800-employee headquarters in Wittlich, south-west Germany, is as cavernous as it is well resourced. A tour of the 46,000m², LED-lit facility takes in a raw material storage area, a large laser steel cutting, plasma drilling, component manufacturing and pre-fabrication area, a generously proportioned surface treatment-powder coating hanger, a sizeable final assembly area, a spacious and well-equipped electric production room, and a giant central asphalt plant parts warehouse. All of this is managed via the latest SAP (Systems Applications Product) business management software.
Step outside the central warehouse and you cannot miss a fully assembled asphalt plant used by the company’s senior field engineers, sales teams and apprentices from the Benninghoven training academy, which takes in aspiring engineers from local schools and colleges. Apprentices also have onsite their own large indoor metalworking and electrical engineering training workshops.
Benninghoven says the health and safety of all employees was a primary concern when designing its new headquarters, which also features an attractive and 12,000m² five floor administration building. This is apparent in the site’s ergonomic, air-conditioned offices and the production facility’s use of powder coating rather than wet paint. This has meant that previously used solvents have been largely eliminated from the production floor. Another big environment-minded advance has been the installation of a system that extracts hot air from the production facility, which is then purified in a filter unit, while the energy generated from the exhaust air is returned to the air circulation.
The new headquarters, which took just over two years to build after groundbreaking in late August 2016, is said by Benninghoven to demonstrate the company’s clear commitment to Germany as a production location. With its emphasis on lean management and the use of Industry 4.0 technologies, the firm, acquired by the Wirtgen Group in 2014, also stresses how the new production plant, which will eventually rise to a 150 plant/year production, makes it more competitive and able to meet increasing market demand for its asphalt plant and associated products. Overall, you are left with the lasting impression that a lot of thought as well as money has gone into maximising the return on this eye-catching capital project.
Benninghoven produces mobile, transportable and stationary 100-400tonnes/hour rolled and mastic asphalt mixing plant, capable of handling up to 90% recycled asphalt pavement (RAP). Benninghoven plant is known for its innovative modular system and intelligent connection technology, making assembly easier. The company also produces high-quality, maintenance-friendly components for all its plant.
Benninghoven manufactures four types of asphalt plant – MBA, ECO, TBA, BA (BA RPP), all featuring the company’s BLS 3000 control systems. The company also produces its own asphalt plant combustion (burner) technology, with burners available in five sizes, and carries out full asphalt plant retrofits. During my tour I am told the heat generated by a burner running for just one hour is enough to heat the average family home for a whole year.
MBA 1250, 2000 or 3000 plant are said to offer high flexibility, easy transport, and short assembly and dismantling times. A gravelled and compacted area is also said to be sufficient for an installation location.
The new concept 1250, 2000, 3000 and 4000 ECO series plant, being showcased at
Benninghoven TBA 200, 3000 or 4000 plant offer huge hot and ready-mixed asphalt storage capacity. They can handle a cold RAP addition of up to 40%, and a hot RAP addition of 70-90%. An intelligent building block approach is said to allow for quick plant assembly and installation. Like the ECO plant, modular extension is possible with the TBA, which can work off either a transportable or stationary foundation.
Finally, BA 3000, BA/ BA RPP 4000, and BA/ BA RPP 5000 plant have the advantages of highest capacities and short project realisation phase and quick assembly and installation. The BA and BA/ BA RPP models are said to offer very good accessibility in all areas, and multiple configurations. BA/ BA RPP plant can handle up to 90% RAP. Their emissions and energy consumption are both said to be low.
A recent development saw Benninghoven install its BA RPP asphalt plant’s proven recycling drum using counterflow action with a hot-gas generator on the firm’s 160-320tonnes/hour semi-mobile and stationary TBA plant range.
Benninghoven’s hot-gas generator is said to be a solution that is environmentally friendly, future-proof and a secure investment. With it, the recycling material – in addition to the virgin mineral – is heated by an EVO JET burner. However, this takes place indirectly in a recycling drum using counterflow action. Depending on the quality of the recycled material used, feed quantities of over 90% are possible.
Unlike conventional parallel drums used for recycling, these recycling drums use counterflow action for heating the gas indirectly. Here, the material is conveyed in the opposite direction to the heat source. As a result, the discharge temperature of 160 °C is the same as the application temperature, with the exhaust gas temperature approximately 100 °C (though above the dew point). This procedure leads to key advantages for the operators of asphalt mixing plants. In classic recycling systems using the parallel flow principle, the temperature is limited to 130 °C by the resulting exhaust gas emissions. However, the exhaust gas temperatures physically exceed this, which leads to increased energy consumption and a greater load on the dust collection system. To enable the asphalt mixture to reach a temperature of 160 °C, overheated virgin mineral must be conveyed.
The EVO JET burner can be supplied with different fuels as normal and supplies the thermal energy required for drying and heating the recycling materials. The generated hot air is mixed intensively with the circulating air, also using counterflow action. In doing so, the hydrocarbons in the exhaust air are almost eliminated.
After my tour of Benninghoven’s HQ in January this year, I sat down with three senior Benninghoven figures, Marcio Cavalcanti-Happle, head of sales, Albert Czerny, sales manager, and Lars Henrich, head of marketing, along with Paul Holmes, managing director of Wirtgen Group UK & Ireland, to discuss how Benninghoven plans to capitalise on its new production facility and headquarters.
Speaking about Benninghoven’s current global market reach and likely growth areas, Lars Henrich says: “We are well established in Europe through our subsidiaries, with a particularly big market in Russia and in Turkey. We are not yet selling into Latin America and Asia, but both offer good growth potential for Benninghoven.”
“The European market is a batch mix plant market. It’s a much more mature market which tends to run asphalt distribution from fixed location plants,” explains Paul Holmes. “In America and developing market countries, they tend to favour continuous mix plant. Wirtgen Group has
“Benninghoven has gone through a big change: two factories to one, a revised product range focusing on the modularity of plant, such as the ECO range, and then bringing everything we do on to SAP business management software. Looking at SAP from an engineering perspective, it means every component on an asphalt plant needs to have its own number, to ensure production line consistency. We now also use Siemens NX software, which is a three-dimensional building block, in our engineering. That’s another big change. The factory is very much the start of our growth strategy. Within the Wirtgen Group, Benninghoven and Kleemann [mobile crusher and screener plant manufacturer] offer two of the biggest growth opportunities.”
Marcio Cavalcanti-Happle adds: “Our focus after this big change period is to concentrate on our long-time markets while firmly integrating Benninghoven within the Wirtgen Group, in terms of sales network and expertise, to gain the trust of customers. I use the example of one asphalt mixing plant having the same complexity as 19 different paving machines, all with their own options.”
Holmes says there is a growing trend in mature markets such as northern and western Europe to use more RAP in each asphalt mix. This is partly due to increased strict legislation on carbon emissions but also down to other factors such as the rising cost of bitumen, greater knowledge of how to process RAP, and a desire for companies to be ‘seen to be green’. This, he says, creates exciting sales opportunities for Benninghoven.
Cavalcanti-Happle says he has just returned from visiting customers in Finland, Norway and the Netherlands. “They talked about the market now wanting to achieve a standard target of 100% use of RAP with zero CO₂ emissions in asphalt mixes by 2030.”
“I think what will happen in the future is that asphalt production will be more automated, as technology continues to develop,” says Albert Czerny.
“I think off the back of increased automation will be how customers can manage data that our sophisticated [BLS 3000] machine control software and telematics is generating,” says Holmes. “Giving customers the ability to benchmark plants, so they can find out why one of their four plants, say, is performing more efficiently than the others. Why is one plant producing asphalt for £2 a tonne, while the others produce it for £2.05? We want our customers to be able to access all this innovation and, ultimately, make more money.”