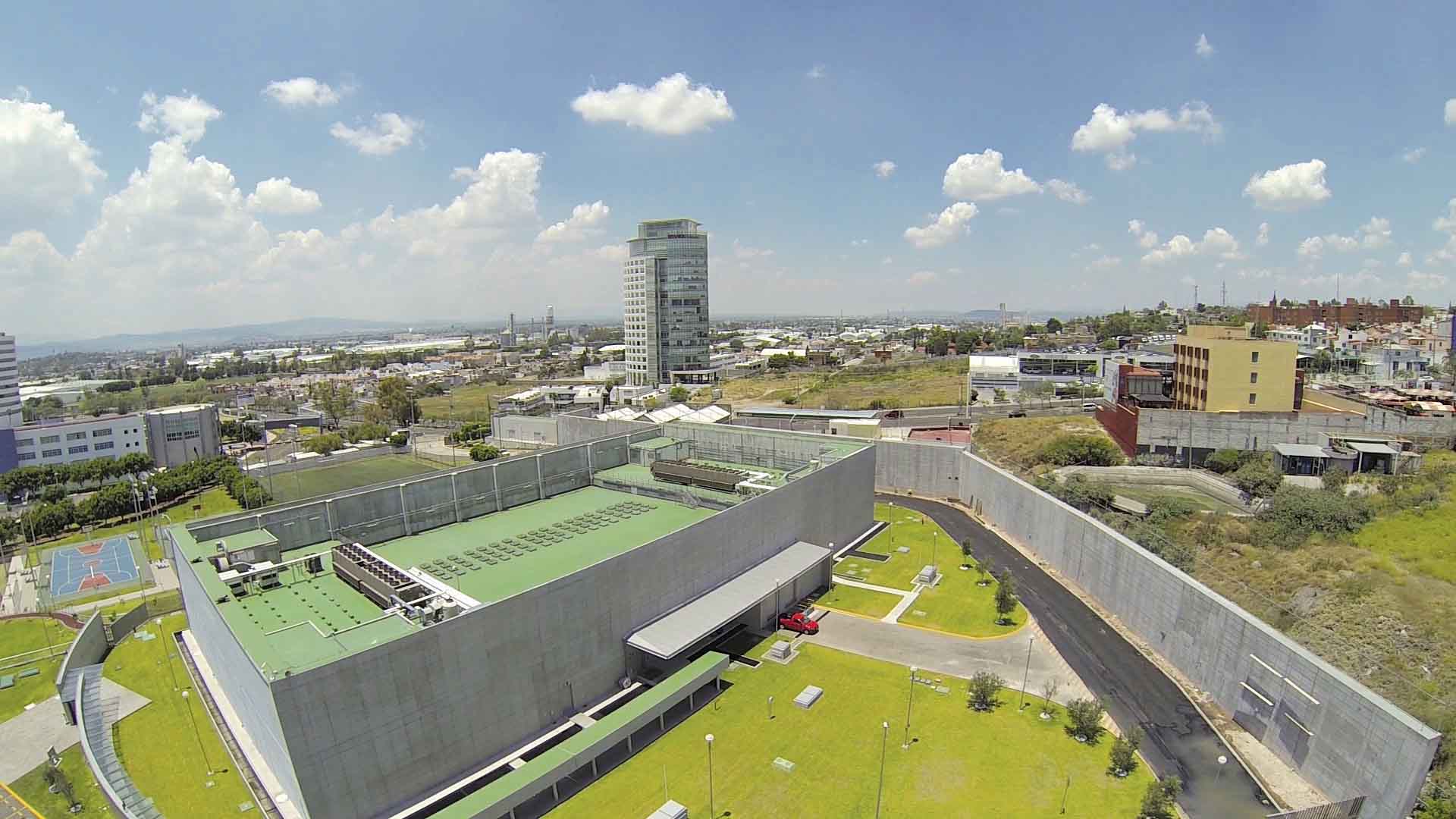
While concrete has been in use for thousands of years, companies worldwide are still finding new speciality mixes to meet specific requirements.
Major players in the industry have state-of-the-art research and development facilities that are able to quickly come up with solutions.
For example, global building materials company
In its home country, Cemex Mexico developed a fire and explosion-resistant concrete, specifically designed to safeguard the Data Processing Centre, Proyecto Q, of the Santander Group, while the company also developed a speciality concrete for a Polish project.
Located in Queretaro, Mexico, Proyecto Q is the Santander Group’s most technologically intensive and energy-efficient data processing centre in the world. When a fuel station was built 20m away from Proyecto Q’s facade, the Santander Group carried out a risk analysis and concluded that its facilities were vulnerable to the effects of potential thermal radiation (fire) and over-pressure (explosion). The group says it turned to Cemex for the design and construction of a perimeter wall capable of withstanding both scenarios.
“Only Cemex, through its Global Center for Technology and Innovation, was able to provide us with the perfect solution for this significant challenge,” says David Romero, real estate director in Queretaro for the Santander Group in Mexico.
The result developed for the Santander Group is a 204m-long and 1.1m-thick perimeter barrier with a maximum height of 10.3m. The design is comprised of two 50cm and 20cm-thick walls, separated by a 40cm-wide air chamber.
Cemex in Mexico supplied 3,000m3 of a high-strength structural concrete with special raw materials that increases its fire resistance. Additionally, the company says its durable and curable auto-compacting specifications facilitate the ecological and economic viability of the project.
In order to certify Cemex’s speciality concrete for the project, a full-scale prototype of the wall was built at the Efectis and TNO research centres in the Netherlands. The wall was subjected to physical fire tests, withstanding a temperature of 1,150°C for more than 60 minutes, and to impact tests of a direct over-pressure wave of 1.1 bars for 80 milliseconds. It is said that the success of these experiments met the demands stipulated in preliminary studies, and the performance of the wall was awarded certification from the Bureau Veritas rating company.
In Poland, Cemex participated in the construction of the Jordanki Cultural and Congress Center, a multifunctional building located in the green ring of the Medieval town of Torun, a United Nations Educational, Scientific and Cultural Organisation (UNESCO) World Heritage Site.
Cemex supplied over 30,000m3 of concrete for this project, designed by the Spanish architect Fernando Menis.
To blend perfectly with the historic character of Torun’s gothic architecture, the Jordanki Center was made of partially immersed raw brick and concrete. This mix of crushed brick and concrete, known as Pikado, was used to fill the 1cm spaces between the bricks, providing an unusual visual effect.
Based on the architect’s model, Cemex’s laboratory also developed a special architectural concrete containing aggregates that matched the specific texture and colour required by Menis for the facade, walls, polished floors and pathway surfaces of the building.
As the new home of the Torun Symphony Orchestra, the Jordanki Center has a rehearsal room for which Cemex developed a concrete solution with special diffusers for the spread of sound. Cemex delivered a singlepiece casting solution of walls, 10m high, from 5-6m wide, and 10-20cm thick, with impressions of boards and diffusers.
“The Jordanki Cultural and Congress Center is a prestigious project for us. We were the only ones to successfully pass the tests performed before the project’s implementation. During deliveries, we developed a lot of concrete mix applications that were both interesting and demanding,” says said Sławomir Dobrowolski, director of mobile concrete plant division for Cemex in Poland.
“The most spectacular one was Pikado, which was a challenging but positive lesson for us.
“Collaboration with our customers is our priority. As exemplified by this project, we analyse the best possible solutions with our customer in the areas of technology or logistics that benefit both parties, so they produce additional projects for us to work on together in the future.”
Cemex’s cement and readymix technology centres are part of the R&D collaboration network, headed by Cemex Research Group, based in Switzerland.