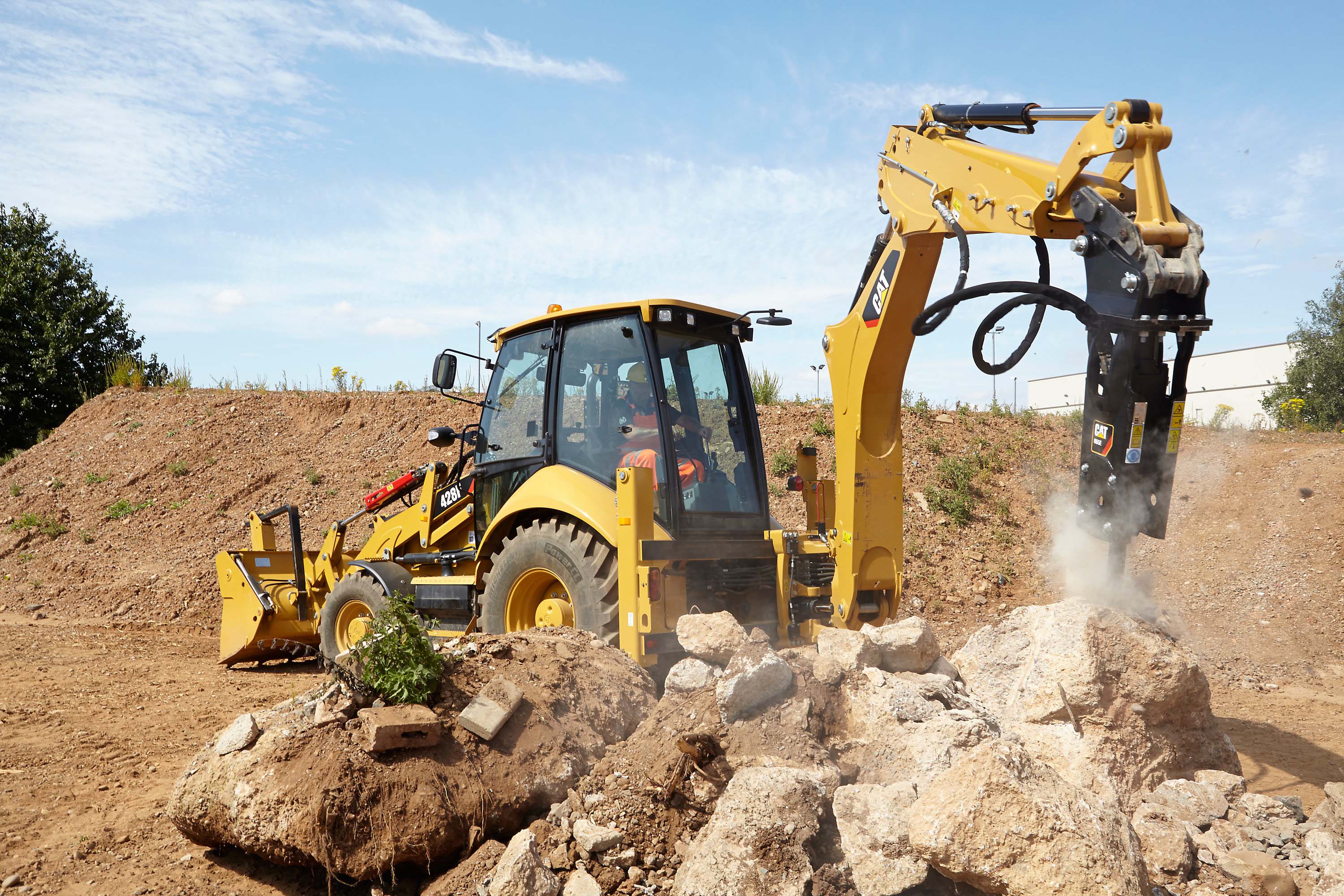
It is a critical primary stage of the rock processing operation, which has considerable significance for all later processes, says the University of Leicester, Department of Geology, central England.
“The degree of fragmentation and the shape of the muck-pile affect the loading and hauling operation, while the fragmentation itself has an effect on the primary crushing operation itself as well as the wastage in oversize and fines material,” says the university, which is running a course on drilling and blasting spread over four weeks between 11 May and 5 June, 2015.
“Precision in the blasting operation can control fragmentation and muck-pile shape as well as reducing oversize material and producing a controlled bench surface, and of course increasing safety. This requires precision in surveying the detailed shape of the rock face, estimating the strength of the rock, design of specific drilling patterns and explosive loading, and then correct implementation of the detailed blast design.”
Special breakers can also be used to further reduce the size of stone or indeed increasingly (used on large-sized excavators) for primary winning in quarries, particularly when blasting is not a viable option.
At the Fedorovskoye sandstone quarry, Rostov region, Russia,
Donskoy Kamen, familiar with the performance of the DP1500i after a successful demonstration on granite, had experienced problems with its existing fleet of drill rigs on the sandstone at the quarry. Its abrasiveness places greater demands on rock tools and uses more rig power, resulting in excessive use of fuel.
The quarried rock, used as aggregates, is particularly sought after as it provides frost resistance up to temperatures in the F300 grade, one of the highest.
When the drilling tests began the DP1500i was equipped with 102mm bits, and after 20 hours of intensive operation drilled a total distance of 822m, double the performance Donskoy Kamen had previously experienced. Using 127mm bits the DP1500i had a penetration rate of 1-1.1m/ minute, and with 140mm drill bits it achieved a penetration rate of 0.7-0.8m/minute.
In the case of the sandstone drilled at the Fedorovskoye quarry the 33kW delivered by the Sandvik DP1500i was enough to extend the service life of bits by up to 2.5 times longer, says Sandvik, which also unveils the two latest models from its C-Series Bretec hydraulic breaker brand, the M17C (1.6tonnes) and L20C (1.65tonnes), which are designed for carriers in the 15-23tonnes and 20-29tonnes operating weight class.
Chinese manufacturer Xuzhou Construction Machinery Group (
The company says it applies a self-adaption, all-terrain off-road chassis in the truckmounted drilling rig field for the first time, and is integrated with multiple proprietary technologies of XCMG such as oil and gas suspension, independent axle lifting and intelligent multi-axle turning control.
“With a small turning diameter, the drilling rig is flexible and can adapt to transition construction under various severe road conditions and can be put in place quickly and accurately. The drift diameter of the mandrel of the top-drive power head is increased to 105mm, providing a stronger slagging capacity. There is a telescopic drill tower and the travel of the power head is 15m,” says XCMG.
Meanwhile,
As a T series design feature, the ROK 600T accepts the industry-established bit shank model QL60, but with the blow tube/foot valve removed. Rockmore says the elimination of this plastic part associated with the drill bit “offers various technical and economic advantages.”
A further development from
“The BenchREMOTE can handle up to three SmartROC D65 rigs in parallel. This multiplies the operator efficiency and was made possible by the full drill cycle automation, says Mattias Hjerpe, product manager. Up to ten rigs can be preprogrammed in the operator station, which facilitates the planning process, and the BenchREMOTE operator station can be installed in a vehicle, trailer or container with all controls and screens the same as in the real cabin on the rig.
Finnish company Robit is claiming to be the first company in the world to develop a patented measuring system that can measure the straightness of a hole during the percussive drilling process. When drilling holes in rock, they can often turn away from the desired direction, and in long holes the deviation may even be several metres, which “results in inefficient operations on a site and in the worst case may create hazards.”
Robit’s new measuring technology system, the result of a seven-year R & D programme, is in operation at selected customers, and it can measure the actual straightness of drill holes immediately, so the information can be utilised in optimising and charging a rock face thus raising efficiency.
Meanwhile, another European manufacturer, Italian company
FDT, specialised in the use of explosives for excavation works, has a fleet of machinery and equipment including Indeco breakers, which it uses for all excavations and works to reduce the volume of rock either as a complementary method or as an alternative to blasting.
The HP 16000 (North American designation for the HP 12000) and an HP 25000 (corresponding to the HP 18000) are being utilised to construct the new campground resort. While the initial phase of excavation used blasting, the breakers perform the actual excavation and reduction of the rock into transportable pieces.
The rock, made up of grey limestone and schist with a presence of quartzite, was especially hard and abrasive in some areas. Some 150,000m³ is being utilised in situ for the construction of road embankments and parking areas and some material is being traded by the owner in exchange for other building materials such as wood, cement and asphalt needed to complete the works.
“The service provided by Indeco dealer SMS in Canada is another important consideration because we know that any need, whether related to service or simply to the optimisation of the excavator-breaker set-up, will be met with a quick and professional response,” says Philippe Paradis, owner of FDT.
“Today Indeco is the only producer that puts out a breaker with 25,000 joules that maintains the versatility and agility of breakers of a lower class. With a speed of up to 460bpm (blows per minute) and a 216mm diameter tool, the HP 18000/25000 boasts spectacular productivity considering the quantity of rock that is fractured and demolished.”
Silenced hammers, identified with ‘s’ in the model designation, use a fully enclosed housing to suppress noise, said to be a valuable feature in sensitive work environments and in small machine applications in which the hammer is in close proximity to the operator. Non-silenced, side-plate models are available for all four sizes.
Flat-top models allow versatility for installation on Caterpillar and equipment made by other manufacturers, and pin-on models are available for the H55E and H65E in applications that require a dedicated, hammer-equipped Cat machine.
The new E-Series hammers include 47% fewer parts than the D-Series predecessors, and this allows for quicker and easier servicing.
“When it comes to daily maintenance, a single grease point is conveniently located and easily accessed. Tool changes are accomplished with common hand tools,” says Caterpillar. Volvo Construction Equipment (Volvo CE) has been highlighting its full line of 18 hydraulic breakers for all applicable machines, ranging from 1.5tonne compact excavators, skid steer loaders and backhoe loaders up to the 70tonne EC700 excavators.
“At Volvo we have focused on building a productive and reliable beaker with good uptime that can also be considered cost-effective globally,” says Jonas Staaf, director of attachments for Volvo CE, sales region EMEA. The company says that since the range was launched, the Volvo hydraulic breakers have proved especially popular in Africa, China and South-East Asia, with a significant number of orders in Europe for the compact breaker range in particular.
Basalt rock is known for being hard and extremely abrasive, and all the machines used in its extraction such as hydraulic hammers, excavators, loaders and crushing plants, face critical conditions due to the very high wear caused by friction and impact with it.
In 2002, when
The company says that after the positive result of the test, another two units arrived in the quarry to increase the production in the peak years 2005–2006, and today a brand new Promove XP4500 mounted on a
The company says the blank-firing prevention system on XP hammers proved to be “highly reliable in secondary demolition as well as in tunnelling construction.”
Other features such as impact energy versus frequency adjustment “allow these breakers to be successfully utilised both on hard rock and in light applications such as road maintenance or municipal works.”
The XP4500 is also said to offer low noise and vibration levels, with the nitrogen chamber over the head of the piston absorbing excess vibrations and returning energy to the percussion. The power unit is also insulated from the outside casing via a series of heavy-duty polyurethane dumping elements.
With a service weight of 4,380kg and a tool diameter of 180mm, the XP4500 offers a blow frequency of 290-590bpm and impact energy of 15,250 joules.