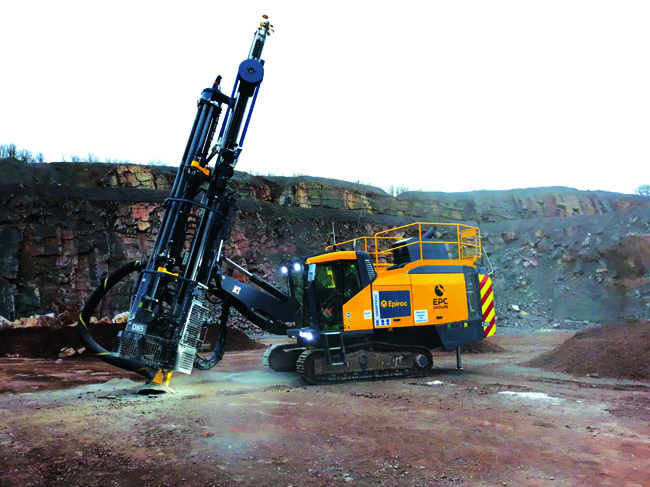
Quality drill rigs, hammers and breakers are an essential part of any efficient aggregates processing operation. Guy Woodford reports on new models from four leading global market manufacturers.
In order to keep at the forefront of drilling technology,
Incorporating cutting-edge automation and GPS technology, the SmartROC D65 is said to have the intelligence and power to consistently drill accurately located, high-quality blast holes. The accurate drilling of blast holes, combined with fully digital blast design and analysis via EPC-UK’s in-house software Expertir, means the blast process can be managed with precision from beginning to end, delivering the desired outcome for the customer.
The rig’s hole navigation system (HNS) enables faster setup at each hole location, whilst the automated drilling process ensures consistent contact with the rock, which controls the compressor and air flow to maximise fuel efficiency. The HNS in conjunction with the built-in GPS removes the need to manually mark and survey hole positions, greatly improving both efficiency and safety.
“EPC-UK is continually investing in the future to ensure its technologies and engineering expertise are industry-leading,” explains Ben Coppock, national operations manager at EPC-UK, “which demonstrates our continued commitment to providing customers with the most up-to-the-minute drilling and blasting technology.
“The Epiroc SmartROC D65 will help us to further optimise the blasting process to produce the best possible fragmentation, as well as reduce fuel consumption due to its intelligent control of compressor load and engine rpm.”
Paul Warren, SED sales manager at Epiroc, explains the importance of EPC-UK’s inaugural UK investment: “The SmartROC D65 is our first ‘down-the-hole’ smart rig to be deployed in the UK. This is a significant step for Epiroc in terms of product development and we are delighted that EPC-UK has decided to introduce this new technology to the industry.
“We have worked with EPC-UK for a number of years and understand its business ethos of constant development and improvement, as it mirrors our own.”
Coppock concludes: “The addition of the new SmartROC D65 drill rig to our portfolio will put EPC-UK at the forefront of drilling and blasting technology and when combined with our other technologies - drone surveys, fragmentation analysis, digital blast design - and our engineering expertise, will enable us to provide our customers with the next level of blasting services.”
In conjunction with these technological developments, EPC-UK is also in the process of constructing a new bulk emulsion facility at its Rough Close Works facility in Derbyshire, England. It will enable the company’s ammonium nitrate blasting intermediate (ANBI) manufacturing process to incorporate some of the latest, safety-enhancing technologies. The plant will provide a safer and more ergonomic working environment for both operations and maintenance personnel and will be the first emulsion plant to comply with BS EN 61511 standard (Functional Safety for the Process Industry). The facility’s construction and installation will meet or exceed a wide variety of British and international standards and provide enhanced protection above the already high EPC Groupe standards.
The new Cat GC S Series top-mount, hydraulic, silenced hammers from Caterpillar Work Tools—models H115 GC S, H120 GC S, H130 GC S, and H140 GC S - are specifically designed for hydraulic excavators with 13-40 tonne operating weights.
The new GC S Series models are said to combine optimum power-to-weight ratios with design simplicity to ensure reliable performance, versatility, ease of use, convenient maintenance, and cost-effectiveness in a range of applications—including quarrying, mining, municipal and general construction and demolition. As a package solution, Caterpillar-designed hydraulic kits are available to provide an exact hammer-to-machine fit for Cat models, ensuring optimum performance.
The Cat GC S Series hammers provide customers optimum impact power and reduced owning and operating costs. The gas-fired operating cycle delivers a constant reliable performance, maximising hammer efficiency.
The automatic shut-off feature provides blank-firing protection by stopping the piston from cycling internally when no material is under the tool. Eliminating blank firing protects the hammer by reducing internal stress and heat, which results in lower overall owning and operating costs. Additionally, the automatic shut-off helps protect rental-fleet hammers, which typically are used by operators with varied levels of expertise.
As a standard feature, GC S Series hammers feature a protective, enclosed housing, designed to lower the noise level for the operator, as well as for the overall job site. In addition, the GC S Series incorporates features that buffer the effect of pressure spikes in the carrier’s hydraulic system and reduced shock loads on the carrier’s front linkage also serve to attenuate noise levels.
The most critical maintenance requirement for hammers is adequate lubrication (hammer paste). To eliminate manual greasing, automatic lubrication systems are available for GC S Series hammers. Customers have the option of installing either a carrier-mounted or hammer-mounted system.
The top-mount design of GC S Series hammers increases impact power by ensuring that hammer force and stick force are consistently in line. The top-mount style also provides a larger work area and enhances visibility for the operator. A further benefit of the design results from the top-mounted bracket transferring considerably less force into the end of the stick, reducing both potential bending stress and overall impact on carrier structures.
A high-pressure accumulator is standard with GC S Series hammers, factory supplied and field serviceable. The accumulator helps protect the carrier hydraulic circuit by absorbing pressure spikes created during the firing stroke.
Caterpillar says that hammer speed/frequency can be easily adjusted to match specific applications and materials to provide optimum productivity.
The design, manufacturing practices, quality inspections, and testing of GC S Series hammers are said to ensure durability in tough applications.
GC S Series hammers are designed with mounting brackets specifically matched to Caterpillar linkages ensuring optimal compatibility with Cat machines.
Full-length side plates on these hammers provide ready access to service points. Also, field-maintenance capability for tools and bushings, plus field-replaceable lower-tool bushings added overall customer value in terms of daily operation and maintenance.
GC S Series hammers are fully supported by Cat dealers. Customers can order parts and service for machines and work tools from a single source. Every Cat work tool is supported with a comprehensive range of pre- and after-sales services, including advice about work-tool selection, operator training, equipment management, and a range of financial and insurance solutions.
As initially reported in the Equipment Update section of Aggregates Business magazine’s January-February 2019 issue, and in response to customer requests, Sandvik Mining and Rock Technology has added to its Ranger DX series of surface top hammer drill rigs with two non-cabin Ranger DXR models, the DX600R and DX800R. The new Ranger DX models are said to offer improved safety in the toughest quarry, open pit mine and construction applications.
Contractors active in urban areas are likely to find a particularly attractive option in Noise Guard, a simple and rugged cover structure offering a total noise reduction of more than 10dB. It could be a decisive advantage when competing for contracts with strict noise limits.
Like the other Ranger DX series models, the DXR600R and DX800R drill rigs are said to offer reliability and large drilling coverage area - from the standard 17.6m² to an optional 26.4m², the latter via a lighter and more mobile package – a superior solution for hazardous conditions where safe and productive drilling requires advanced radio remote-control capabilities.
At the bauma 2019 exhibition in Munich, Germany (8-14 April), Furukawa is introducing the FXJ1070 - a new model in its FXJ series of hammers. Replacing the F100XP, the new model will be half a tonne heavier and has much more impact energy than its predecessor. Furukawa says the FXJ1070 offers improved durability and lower lifetime cost. The Japanese company, whose FRD Europe subsidiary is based in the Netherlands, is exhibiting its full range of demolition tools and crawler drills during the week-long bauma showpiece event.