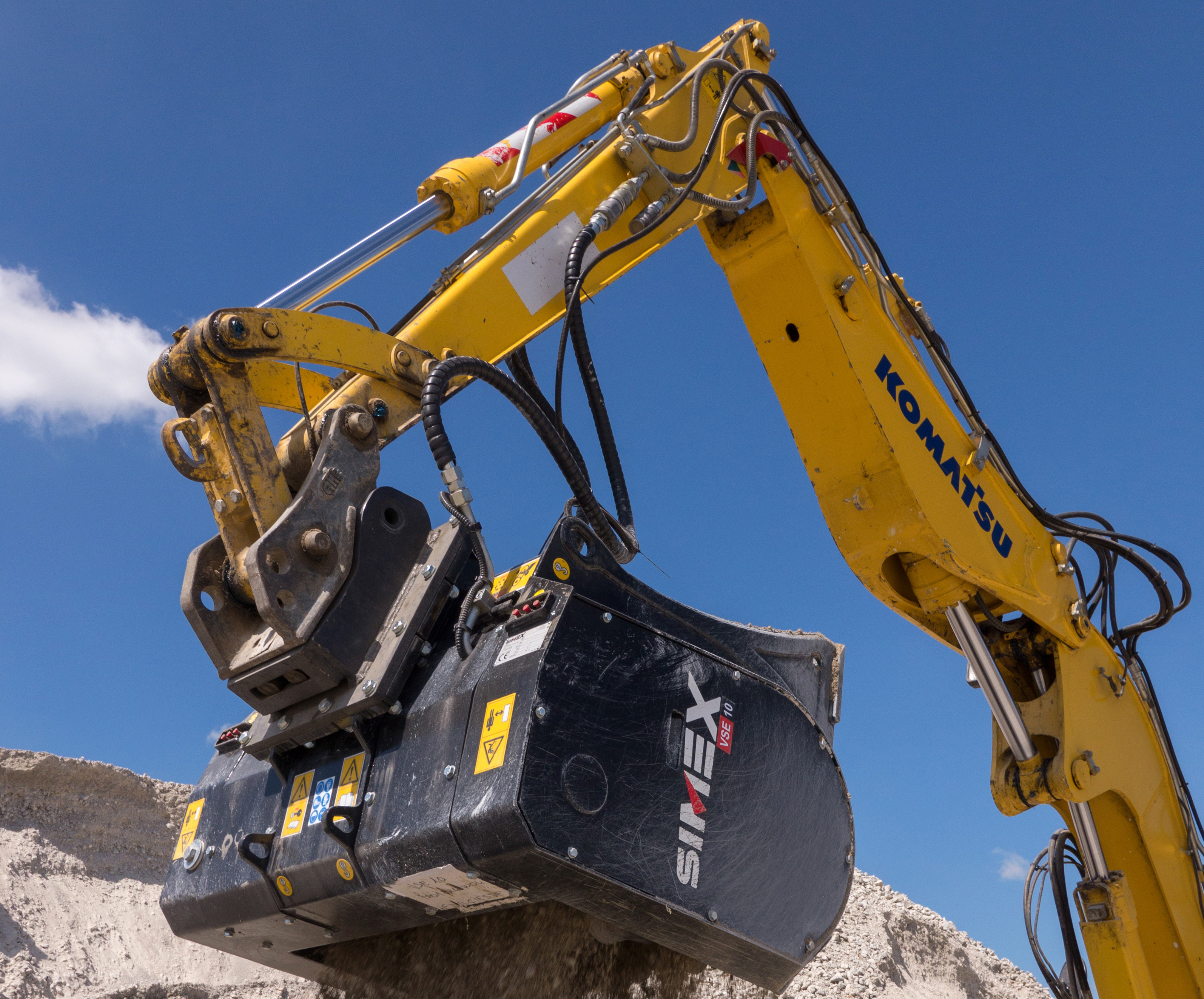
Breakers and screening buckets are another part of the materials production process, helping to make a variety of materials. Patrick Smith reports.
A centuries-old German company is using modern technology to help with slate production at its site.Epiroc’s hydraulic breaker
SB 202 is said to have proved itself many times over by providing excellent service for Rathscheck Schiefer in Mayen,in the Eifel region, south of Cologne.
Since it was founded in 1793, Rathscheck Schiefer has been a leading producer of premium quality slate, and it has partnered with Epiroc, which develops and produces innovative attachments for excavators used in rock mining, demolition and recycling.
At the start of the year the Hydraulic Attachment Tools division within
The division manufactures excavator attachment tools such as hydraulic breakers, cutters, pulverisers, bucket crushers, shears, grapples and magnets, and from 1 January 2018, all the division’s current products are being delivered with Epiroc product branding.
Moselschiefer (Mosella slate) mined at the Katzenberg mine in the Mayen region, is the premium product of Rathscheck Schiefer, and the current main shaft was commissioned in 1959 and reaches a depth of 220m on the seventh level. The latest level, level 11, opened in 2016 and reaches depths of 400m.
Turning the slate into high-quality end products is a long process, and production of the local Mosella slate has been comprehensively modernised over the past 15 years.
In the past, the process was extremely involved and time-consuming, and at the Katzenberg mine six specially-developed SB 202 hydraulic breakers are in daily use, for between 3-4 hours/shift. Epiroc says these offer efficient mining, reducing costs and enabling slate to be offered at much lower prices today than a few years ago.
Four of the breakers are mounted on the
The breakers loosen the workable slate, which was previously cut with a diamond saw in a grid corresponding to the geological properties, and then break it out of the wall. Wheeled loaders put the slate onto the wagons of the underground mine train, which transports it to the hoisting shaft, which then takes it above ground into the production halls.
The work is carried out in damp, restricted conditions, and Epiroc says the simplicity of changing the working tool and the good visibility of the working area ensure precise and user-friendly handling.
The company also points to the SB series’ solid-body concept, which offers high reliability, versatility, high efficiency and performance, while the construction combines the striking mechanism and guide system in a single block of special cast iron, thus reducing the total number of components considerably.
“This results in an extremely slim and compact form that makes handling easier, says the company.
“The recoil force of the piston is automatically used to increase the power, without additional hydraulic energy. Consequently, the stress from vibrations is extremely low. The ventilation of the breaker’s percussion chamber, that protects the breaker from wear, and the integrated water spraying system are further advantages.”
Epiroc says that the SB 202 includes the floating bushing for easy replacement on-site with a normal hand tool; installed pressure relief valve; integrated dust wiper, which prolongs the service life of the bushing and supporting bars, and the AutoStart function, which makes handling the tool much easier.
Meanwhile, Italian company
Since Simex screening buckets were introduced with the VSE 40, they have been used in harsh environments, from the scorching climate of the Middle East to the sub-freezing temperatures of Siberia.
The Simex line of attachments has a designed and patented mechanism that allows the screening bucket drums to be distanced or closed via a hydraulic system, enabling the output size to be varied in seconds by activating a simple command from the operator’s seat.
After introduction of the VSE 30 and VSE 20, Simex launched the VSE 10, a model that is said to maintain the ratio between capacity and weight, while offering the possibility to screen any material when coupled with 8-13tonne excavators. This class of machines also enables the VSE to be used in situations where space restrictions exclude the use of large machines and screening buckets.
The VSE 10 is said to offer excellent levels of production, thanks to the rhomboid-shaped elements with different-sized disks that compose the shaft. This shape is said to produce an intense whirling of the material to be screened, an advantage to the hourly production.
Finnish manufacturer
As the Transformer is essentially designed to fit excavators and wheeled loaders of up to 160tonnes, this has made the equipment ideal for large-scale surface mining operations, where transportability and productivity are essential requirements of material handling equipment, says ALLU.
The M-Series attachment is a high capacity mobile material processor that can crush soft and brittle material and separate hard unwanted impurities in the rock mass, while loading a dump truck or conveyor system.
“This makes it ideal for processing of soft rock and other minerals in often hard to get to areas, with the M-Series delivering simultaneous mobile crushing, separating, enrichment and loading,” says ALLU.
Different drum configurations of 50mm and 75mm mean differing fragment sizes may be processed with high productivity in one step, and the process is fully mobile.
In New Hampshire, USA, the geology includes a heavy presence of metamorphic, especially igneous, rock formations, which yield different types of granite.
The many quarries producing this material used in construction earned the state its nickname of the ‘Granite State’, and given the occurrence and hardness of the rock masses blasting was long considered the only valid method for excavating.
However, over the last decade the hammer has become more commonly used for trenching, laying utilities, excavating small and medium-sized lots, and profiling slopes.
Parker Mullins believed in the capabilities of hammers, and nine years ago started his own company, New Hampshire Rock Reduction.
Aware of the increasing difficulties using explosives due to environmental impact and a constant rise in costs, he realised that in certain situations the hammer could offer solid advantages and be a more efficient and less costly alternative.
This led him to buying an
“Prioritising the use of the hammer was definitely the decision that gave our company a future as it allowed us to take on a whole set of projects that we would otherwise be excluded from,” says Mullins.
“While blasting certainly offers advantages when the job is to excavate large areas containing formations with little fracturing and certain types of very hard gray granite, in other situations it is not the best solution, especially when working in residential areas where the lots include very fractured rock masses.”
Newry, Northern Ireland-based attachment manufacturer
“The Tefra Tilt represents a very strong middle ground,” says Oliver Phelan, Hill Engineering sales and marketing manager.
“The product itself has really taken off. We are selling more and more as the months go by. We have seen a 60% growth in sales of the tilt over the last year and it’s still growing.”
The Hill Tefra Tilt hitch was born from the innovation of the Tefra, which was brought to market in 2011. The tilt system is said to allow operators greater flexibility in the way they use their machines and turns attachments into ones that can be used at up to 180º.
Hill engineering has used the award-winning Tefra system as the core of the product and introduced the tilt motor from HKS of Germany to achieve the 180º tilt function.