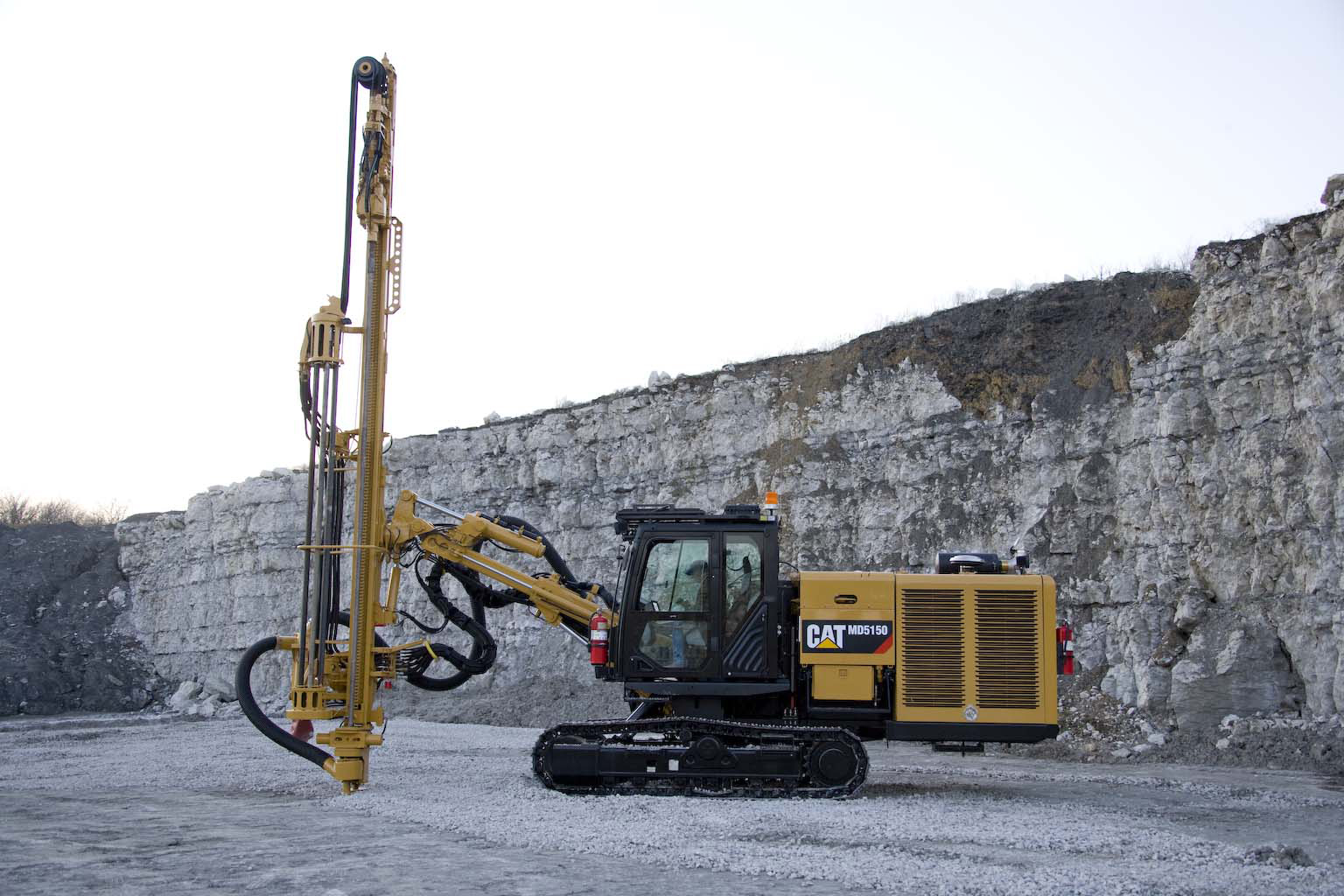
“Benefiting from more than 50 years of track drill design, the MD5150 incorporates a proven rock drill, patented carousel rod changer, new cab and many other features that boost productivity and reduce operating costs,” says Caterpillar.
The MD5150, introduced at the recent MINExpo in Las Vegas, USA, is said to dramatically reduce set-up time, thanks to its innovative carousel rod changer. The Cat design holds six rods and accommodates multiple lengths and diameters of drill steel, while powerful dual-rod grippers and a special gate design let the rod and gate move simultaneously, reducing cycle time.
The rod changer is supported by a feed and heavy-duty 2.4m boom that extends to 3.3m for larger pattern coverage with fewer set-ups. Because the carousel rod changer weighs less and holds more rods than linear models, the boom extension can reach farther and drill deeper while maintaining stability, says Caterpillar. Holes can be drilled within 610mm of the highwall, which is “50% closer than with a linear rod changer.”
Caterpillar says that owners can service the rock drill themselves to reduce downtime and control costs, and that a new automated lube system keeps the drill working productively, eliminating the need to stop the machine for manual greasing every two hours.
The heart of the power group is the Cat C11 Engine rated at 287kW at 1,800rpm. Designed for high performance and excellent fuel efficiency, the engine meets US Tier 3 and EU Stage IIIA emissions standards.
The cab on the MD5150 is designed to enhance safety and productivity. It is ROPS/FOPS-certified and incorporates numerous shutdown methods accessible from the cab or at ground level. Large windows, streamlined front structures and a skylight enhance visibility, as do well-placed mirrors and high-resolution cameras. The front window provides a secondary emergency exit.
To boost operator comfort and productivity, the cab features automatic climate control, excellent ventilation, a fully adjustable seat, ergonomic controls and switches, and low sound levels (less than 80dB), while a smart drill monitoring system tracks changes in rock formation and automatically adjusts impact and feed pressure based on hardness of the rock. The system’s anti-jam, anti-plunge and anti-plug capabilities keep the track drill working efficiently and extend drill string life.
Maintenance and service technicians appreciate the MD5150’s simple component layout and convenient service access. A walk-in service station provides easy access to major service points for the engine, compressor, air conditioner, hydraulic valves and more. A boom-mounted camera allows constant visibility to the front of the drill while working inside the service center.
“Caterpillar Electronic Technician (Cat ET) speeds the troubleshooting process, improving repair accuracy and reducing downtime. Cat Product Link allows remote monitoring of machine location, service meter hours, fuel usage and other critical factors, providing owners the information they need to optimise utilsation and reduce owning and operating costs,” says Caterpillar.